Home > Blow Molding > 3D Blow Molding
Booling’s 3D blow molding is mainly used in air ducts around automobile engines. It has the outstanding advantages of seamless welding and uniform wall thickness. It adopts advanced 3D hollow plastic molding processing technology to ensure aesthetics while having excellent high-temperature resistance, corrosion resistance, and high-strength characteristics. We provide a complete solution for 3D blow molding molds. The accuracy of 3D air ducts can reach the millimeter level, and we deliver molds for Volkswagen, Mercedes-Benz, Audi, Tesla, Toyota, and other cars.
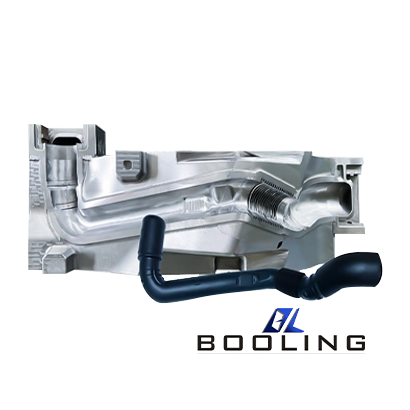
3D blow molding is an advanced manufacturing process that can realize the production of products with complex geometric shapes. Booling provides off-axis extrusion blow molding, robots or manipulators holding parisons, and sequential opening and closing of molds with vacuum assistance.
- Off-axis Extrusion Blow Molding
- Robot or Manipulator Holding the Parison
- Sequential Opening and Closing Mold with Vacuum Assist
3D Blow Molding Capabilities
3D blow molding can achieve one-piece molding, optimize part performance, and reduce costs, making it an ideal manufacturing process for complex integrated designs.
·
US
Metric
PP
27.6in. x 27.6 in. x 15.8 in.
700mm x 700mm x400mm
HDPE
27.6in. x 27.6 in. x 15.8 in.
700mm x 700mm x400mm
PVC
27.6in. x 27.6 in. x 15.8 in.
700mm x 700mm x400mm
PC
27.6in. x 27.6 in. x 15.8 in.
700mm x 700mm x400mm
*3D blow molding is ideal for manufacturing complex curved pipes, ducts, and other hollow components without parting lines or excessive flash.
3D Blow Molding Material
3D blow molding is a hollow plastic product molding technology. Booling provides a variety of molding material options, such as PP, HDPE, PVC, PC, ABS, etc. These materials have good processing characteristics.
Material
- PP
- HDPE
- PVC
- PC
The Advantage of 3D Blow Molding
Compared with traditional molding, 3D blow molding is suitable for the production of more precise blow molding parts
- Obtain high-quality blow molding products with no welds and uniform wall thickness
- Less waste and no flash, no trimming required
- 3D blow molding molds can be produced economically and efficiently, and the products are consistent
- Booling provides a wide range of material options to meet the needs of different product application scenarios
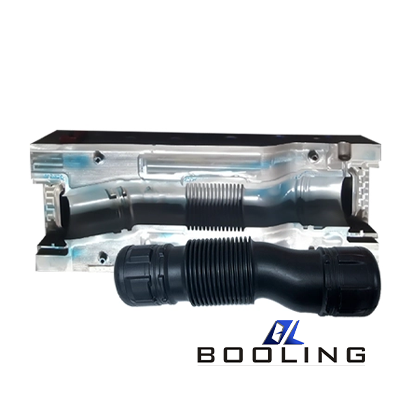
Application of 3D Blow Molding
3D blow molding technology has been widely used in the precision product production industry to meet the processing needs of various seamless pipes in the automotive, furniture, electrical appliances, construction, and other industries, such as turbocharged engine pipes, cooling system pipes, fuel lines, refueling pipes, natural gas pipelines, etc.
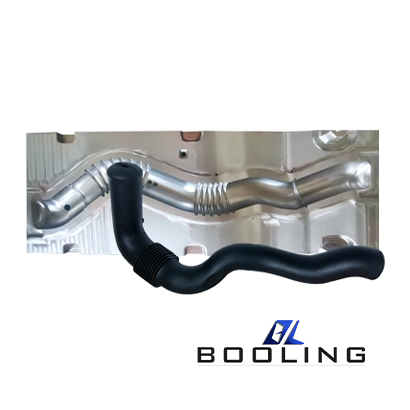
Guidelines for 3D Blow Molding
3D blow molding can realize the production of complex parts, reduce parting lines, improve wall thickness, obtain seamless products, and meet the processing requirements of precision products.
3D blow molding has technical advantages. The plastic raw materials are extruded and pre-blow molded, tightly adhered to one side wall of the mold, and the extruder or mold rotates the second or third axis according to the molding program preset by the Booling designer. After the intestine billet fills the mold cavity, the other side of the mold is closed and tightly fixed on the intestine billet segment, and separated from the subsequent billet segment. The entire billet is blown up and close to the mold cavity wall for cooling and solidification.
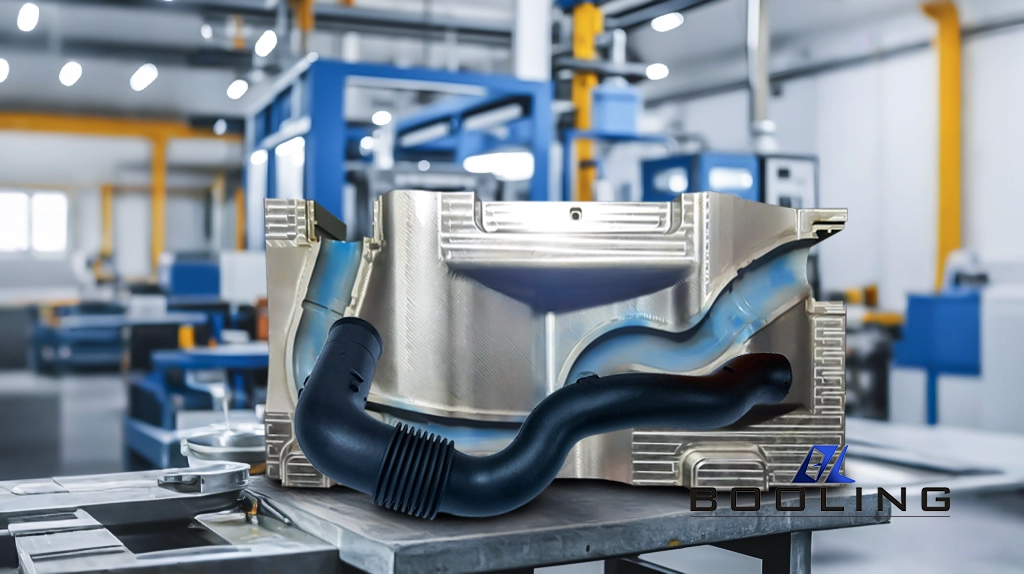
Types of 3D Blow Molding
Plastics are blown in the mold with the help of 3D movement to produce hollow products with complex structures, reduce surface burrs, reduce roughness, perform continuous extrusion, and eliminate the use of clamping devices.
- After the plastic blank is extruded, it is pre-blown and pressed against one side of the mold wall. The extruder head or mold rotates the second or third axis according to a pre-set program. When the intestinal blank fills the mold cavity, the other side of the mold is closed to separate the parison and the subsequent parts. After the mold is closed, compressed air is introduced, and the parison expands and presses against the inner surface of the mold. After solidification, a high-quality product is formed
- We provide negative pressure molding technology, making the upper and lower ends of the mold into sliders that can be opened and closed separately. By accurately controlling the injection volume and temperature, negative pressure is applied inside the mold to help the parison fit the inner wall of the mold more closely. This solution is more suitable for the molding of regular pipes
- Use a robot or manipulator to clamp and move the parison to enter the mold cavity more accurately. Booling processing has a high degree of automation and can be operated and clamped in a six-axis linkage mode to achieve more accurate parison position control
3D Blow Molding Molds
Booling provides the design and manufacture of extrusion, injection, stretching, and multi-layer blow molding molds to achieve the processing of products in different application scenarios.
- Extrusion Blow Molding Molds
During the 3D extrusion blow molding process, the parison can move in multiple dimensions. Booling provides 6-axis robots and manipulators for parison processing, which can improve accuracy and reduce flash. This method is suitable for the production of plastic bottles and other containers.
- Stretch Blow Molding Molds
Before the formal blow molding, the parison needs to be axially stretched to improve the mechanical properties of the final product, and then the stretched parison is blown.
- Injection Blow Molding Molds
Injection blow molding requires the use of an injection molding machine to inject molten plastic into the parison, and then blow it.
- Multi-layer Blow Molding Molds
Multi-layer blow molding molds can extrude plastic layers of multiple different materials at the same time, realizing the synchronous operation of multiple extruders, which is suitable for the production of large quantities of wide-mouth containers.