Home > Comparing Plastic and Metal Materials in 3D Printing
Plastic 3D Printing
The advantage of plastic 3D printing is to achieve integrated molding of products, saving a lot of labor and transportation time. Compared with traditional manufacturing techniques, plastic 3D printers produce relatively fewer raw materials, and this technology does not cause significant waste of raw materials.
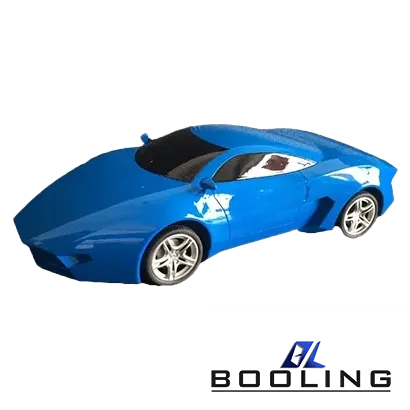
3D printing service, also known as additive manufacturing, and this technology allows for the creation of complex geometries, customized components, and intricate designs that were once considered impossible or prohibitively expensive to produce using traditional manufacturing methods. Although plastic 3D printing and metal 3D printing are widely used, they have unique advantages and limitations, making them suitable for different applications.
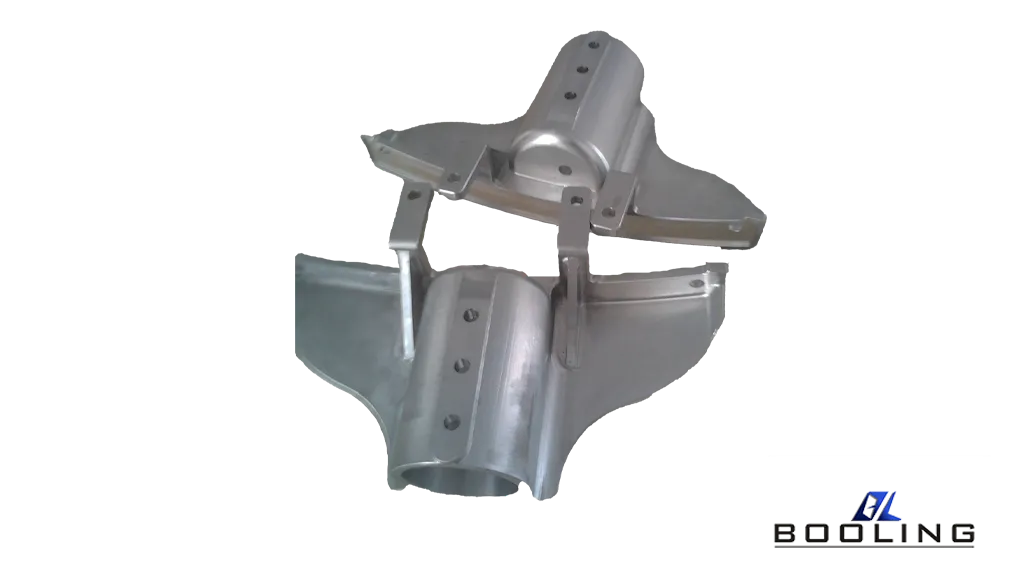
Overview of Plastic and Metal 3D Printing
Before diving into the detailed comparison, it is essential to understand the fundamental principles and technologies behind plastic and metal 3D printing.
- Plastic 3D printing
Plastic 3D printing encompasses a range of additive manufacturing processes that utilize thermoplastic materials to create three-dimensional objects. The most common plastic 3D printing technologies include:
– Fused Deposition Modeling (FDM) / Fused Filament Fabrication (FFF): This technology involves extruding thermoplastic filaments layer by layer to build the desired object. It is widely used for prototyping, low-volume production, and hobbyist applications due to its affordability and accessibility.
– Stereolithography (SLA): SLA uses a laser to cure liquid photopolymer resin layer by layer, creating highly detailed and accurate parts with excellent surface finish. It is commonly used for producing prototypes, dental models, and intricate designs.
– Selective Laser Sintering (SLS): SLS utilizes a high-powered laser to selectively fuse powdered thermoplastic materials, such as nylon, to create strong and durable parts. It is suitable for functional prototypes and end-use parts in various industries.
- Metal 3D Printing
Metal 3D printing, also known as additive metal manufacturing, involves the use of metal powders or wire feedstock to create fully dense metal parts. The most common metal 3D printing technologies include:
– Direct Metal Laser Sintering (DMLS) / Selective Laser Melting (SLM): These technologies use a high-powered laser to selectively melt and fuse metal powders, such as stainless steel, titanium, or aluminum alloys, layer by layer. They are widely used for producing high-performance and high-stress components in the aerospace, automotive, and medical industries.
– Electron Beam Melting (EBM): EBM utilizes a high-energy electron beam to selectively melt and fuse metal powders in a vacuum environment. It is known for producing parts with excellent mechanical properties and reduced residual stresses.
– Binder Jetting: This technology involves selectively depositing a liquid binder onto a bed of metal powder, layer by layer, to create a solid object. The “green” part is then cured and sintered to achieve full density and strength. Binder jetting is suitable for producing complex geometries and low-volume production.
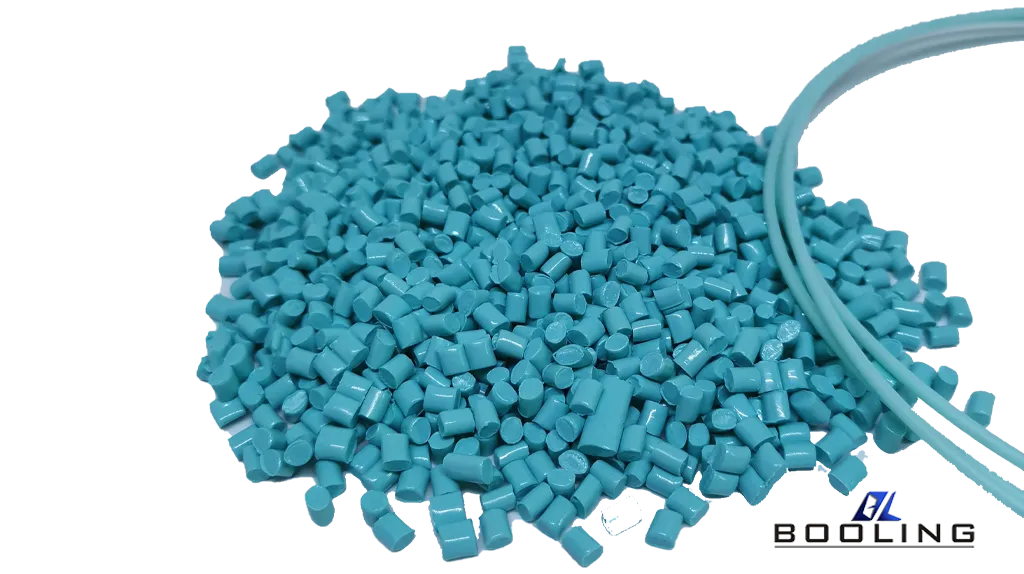
Properties and Characteristics of 3D Printing
The properties and characteristics of plastic and metal materials in 3D printing play a significant role in determining their suitability for different applications. Here, we compare the key properties of plastic and metal materials:
- Mechanical Properties
– Plastic: Thermoplastic materials used in 3D printing, such as PLA, ABS, and nylon, offer good flexibility, impact resistance, and tensile strength. However, they generally have lower mechanical properties compared to metals, making them suitable for low-stress and low-load applications.
– Metal: Metal materials, such as stainless steel, titanium, and aluminum alloys, exhibit exceptional strength, hardness, and durability. They are capable of withstanding high loads, stresses, and harsh environmental conditions, making them ideal for high-performance and high-stress applications.
- Thermal Properties
– Plastic: Thermoplastics have lower melting points and thermal conductivity compared to metals. They are suitable for applications with moderate temperature requirements but may deform or degrade at high temperatures.
– Metal: Metals have high melting points and excellent thermal conductivity, making them suitable for applications involving high temperatures and thermal cycling. They can maintain their mechanical properties and dimensional stability under extreme conditions.
- Chemical Resistance
– Plastic: The chemical resistance of thermoplastics varies depending on the material. For example, polypropylene (PP) and polyethylene (PE) offer excellent chemical resistance to acids, bases, and solvents, while other materials like ABS may be more susceptible to chemical attack.
– Metal: Metals generally offer superior chemical resistance compared to plastics. Stainless steel, for example, is highly resistant to corrosion and chemical attack, making it suitable for applications in harsh environments.
- Electrical Properties
– Plastic: Thermoplastics are excellent electrical insulators, making them suitable for applications requiring electrical insulation and dielectric properties.
– Metal: Metals are excellent conductors of electricity and heat, making them suitable for applications requiring electrical conductivity and thermal management.
- Surface Finish and Detail Resolution
– Plastic: SLA and SLS technologies can produce plastic parts with excellent surface finish and high detail resolution. FDM/FFF, while more affordable, may result in visible layer lines and require post-processing to achieve a smooth finish.
– Metal: Metal 3D printing technologies, such as DMLS/SLM and EBM, can produce parts with high detail resolution and good surface finish. However, post-processing steps, such as machining, polishing, or heat treatment, are often required to achieve the desired surface quality and mechanical properties.
Applications of 3D Printing
The unique properties and characteristics of plastic and metal materials make them suitable for different applications in various industries. Here, we compare the common applications of plastic and metal 3D printing:
- Plastic 3D Printing Applications
– Prototyping: Plastic 3D printing is widely used for creating prototypes and concept models due to its affordability, ease of use, and ability to produce complex geometries quickly.
– Consumer Goods: Thermoplastics are used to produce a wide range of consumer products, including toys, household items, and electronic housings, due to their versatility and cost-effectiveness.
– Medical Devices: SLA and SLS technologies are used to produce medical devices, surgical guides, and dental models with high precision and biocompatibility.
– Automotive: Plastic 3D printing is used to produce automotive components, such as interior trim, housings, and prototypes, due to its lightweight nature and design flexibility.
- Metal 3D Printing Applications
– Aerospace: Metal 3D printing is widely used in the aerospace industry to produce high-performance components, such as turbine blades, fuel nozzles, and structural parts, due to its ability to create complex geometries and lightweight structures.
– Automotive: Metal 3D printing is used to produce high-strength and durable automotive components, such as engine parts, exhaust systems, and suspension components, due to its superior mechanical properties.
– Medical Implants: Metal 3D printing is used to produce customized medical implants, such as orthopedic implants and dental prosthetics, due to its biocompatibility and ability to create patient-specific designs.
– Industrial Tooling: Metal 3D printing is used to produce industrial tooling, such as molds, dies, and jigs, due to its ability to create complex geometries and high-strength tools.
Processing Considerations of 3D Printing
The processing considerations for plastic and metal 3D printing differ significantly due to the unique properties and requirements of each material. Here, we compare the key processing considerations for plastic and metal 3D printing:
- Plastic 3D Printing
– Material Handling: Thermoplastic filaments and powders must be stored and handled properly to prevent moisture absorption and contamination. Proper drying and storage conditions are essential to maintain material quality.
– Printing Parameters: The printing parameters, such as temperature, speed, and layer height, must be carefully controlled to achieve optimal print quality and minimize defects. Each thermoplastic material has specific processing requirements that must be followed.
– Post-Processing: Post-processing steps, such as support removal, sanding, and painting, may be required to achieve the desired surface finish and mechanical properties. SLA and SLS parts may require additional steps, such as cleaning and curing, to ensure complete polymerization.
- Metal 3D Printing
– Material Handling: Metal powders must be handled with strict safety protocols to prevent contamination, oxidation, and health hazards. Proper storage and handling conditions are essential to maintain material quality and safety.
– Printing Parameters: The printing parameters, such as laser power, scan speed, and layer thickness, must be carefully controlled to achieve optimal print quality and mechanical properties. Each metal material has specific processing requirements that must be followed.
– Post-Processing: Post-processing steps, such as heat treatment, machining, and surface finishing, are often required to achieve the desired mechanical properties and surface quality. These steps can be time-consuming and add to the overall cost of production.
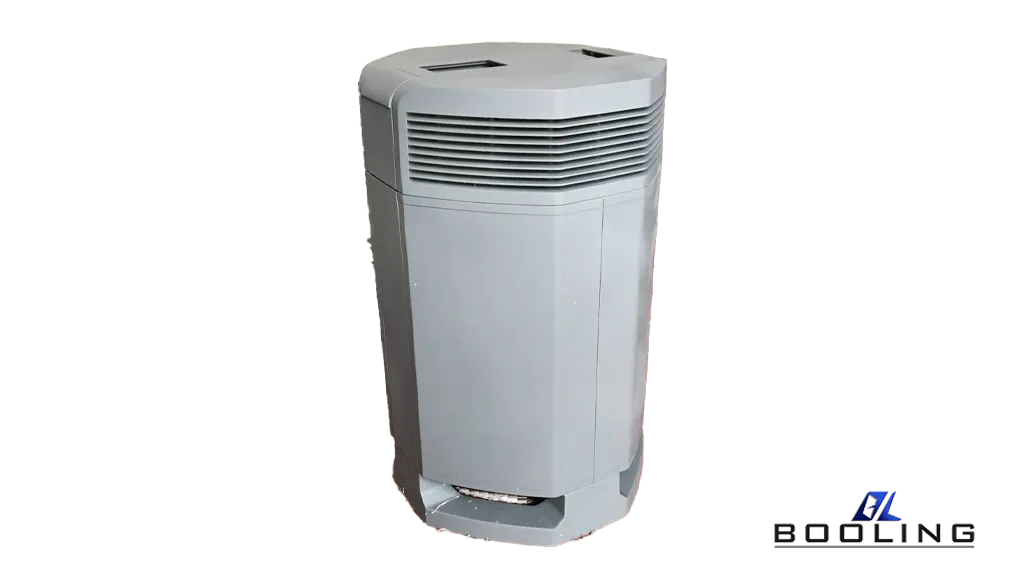
Cost Implications of 3D Printing
The cost implications of plastic and metal 3D printing vary significantly due to the differences in material costs, equipment requirements, and processing considerations. Here, we compare the key cost factors for plastic and metal 3D printing:
- Plastic 3D Printing
– Material Costs: Thermoplastic materials, such as PLA, ABS, and PETG, are generally more affordable compared to metal powders. The cost of photopolymer resins used in SLA printing can vary depending on the formulation and properties.
– Equipment Costs: Desktop and entry-level 3D printers for plastic materials are relatively affordable, making plastic 3D printing accessible to hobbyists, educators, and small businesses. Industrial-grade plastic 3D printers, such as SLS machines, can be more expensive but offer higher performance and capabilities.
– Processing Costs: The processing costs for plastic 3D printing are generally lower compared to metal 3D printing. However, post-processing steps, such as support removal and surface finishing, can add to the overall cost.
- Metal 3D Printing
– Material Costs: Metal powders, such as stainless steel, titanium, and aluminum alloys, are more expensive compared to thermoplastic materials. The cost of metal powders can vary depending on the material purity, particle size distribution, and specific alloy compositions.
– Equipment Costs: Metal 3D printers, such as DMLS/SLM and EBM machines, are significantly more expensive compared to plastic 3D printers. These machines require specialized equipment, such as high-powered lasers or electron beams, and advanced safety features.
– Processing Costs: The processing costs for metal 3D printing are higher due to the specialized equipment, strict safety protocols, and post-processing requirements. Post-processing steps, such as heat treatment, machining, and surface finishing, can add to the overall cost of production.
Environmental Considerations of 3D Printing
The environmental impact of plastic and metal 3D printing is an important consideration for sustainable manufacturing practices. Here, we compare the key environmental considerations for plastic and metal 3D printing:
- Plastic 3D Printing
– Material Sustainability: Thermoplastic materials, such as PLA, are biodegradable and derived from renewable sources, making them more environmentally friendly. However, other thermoplastics, such as ABS, are derived from petroleum and may have a higher environmental impact.
– Waste Generation: Plastic 3D printing can generate waste materials, such as support structures, failed prints, and excess material. Proper waste management practices, such as recycling or responsible disposal, are essential to minimize environmental impact.
– Energy Consumption: The energy consumption of plastic 3D printing varies depending on the technology and equipment used. Desktop 3D printers generally consume less energy compared to industrial-grade machines.
- Metal 3D Printing
– Material Sustainability: Metal powders used in 3D printing are derived from natural resources and can be recycled, making them more sustainable. However, the extraction and processing of metal powders can have a significant environmental impact.
– Waste Generation: Metal 3D printing can generate waste materials, such as unused powder, support structures, and failed prints. Proper waste management practices, such as recycling or responsible disposal, are essential to minimize environmental impact.
– Energy Consumption: The energy consumption of metal 3D printing is generally higher compared to plastic 3D printing due to the specialized equipment and high-powered lasers or electron beams required. Advanced energy-efficient technologies and practices can help reduce the overall energy consumption.
Plastic and metal 3D printing offers unique advantages and limitations that make them suitable for different applications across various industries. Plastic 3D printing is ideal for prototyping, consumer goods, medical devices, and automotive components due to its affordability, ease of use, and versatility. On the other hand, metal 3D printing is suitable for high-performance and high-stress applications in aerospace, automotive, medical implants, and industrial tooling due to its exceptional strength, durability, and thermal properties.
Related News
Applied’s expertise in modifying materials at atomic levels and on an ihdustrial scaleenables our customers to transform possibilities into reality.