Home > Booling Customized 3D Printing Technology Solution
Booling’s industrial-grade customized 3D printing solution adopts intelligent digital manufacturing technology, accurately analyzes 3D model data, and transforms design drawings into high-precision solid products through layer-by-layer stacking and forming processes, perfectly achieving personalized customized production of complex structures. After continuous innovation and verification by our technical team, this technology is particularly suitable for high-end manufacturing fields such as aerospace precision components and medical customized implants. In the manufacturing of key components for automotive engines, our 3D printing technology has successfully achieved a breakthrough in weight reduction of 35% and research and development cycle reduction of 60%, while maintaining excellent performance with a material utilization rate of over 95%.
Advantages of custom 3D printing processing:
- Flexible design
- Rapid prototyping
- High material utilization
- High product quality
Custom 3D printing technology, with its excellent manufacturing capabilities and additive manufacturing advantages, can realize the production of complex structural products that are difficult to process with traditional processes. Compared with traditional processes, it has significant advantages such as fast molding speed and high cost-effectiveness, effectively avoiding the high-cost defect problem in traditional manufacturing. At Booling, we have provided more than 300 successful cases of interior and exterior parts in the field of rapid prototyping in the automotive industry through 0.1mm precision layer-by-layer stacking technology, which fully verifies the reliability and excellent performance of our technology. Our custom 3D printing solutions provide strong technical support for new product development and product optimization for many companies.
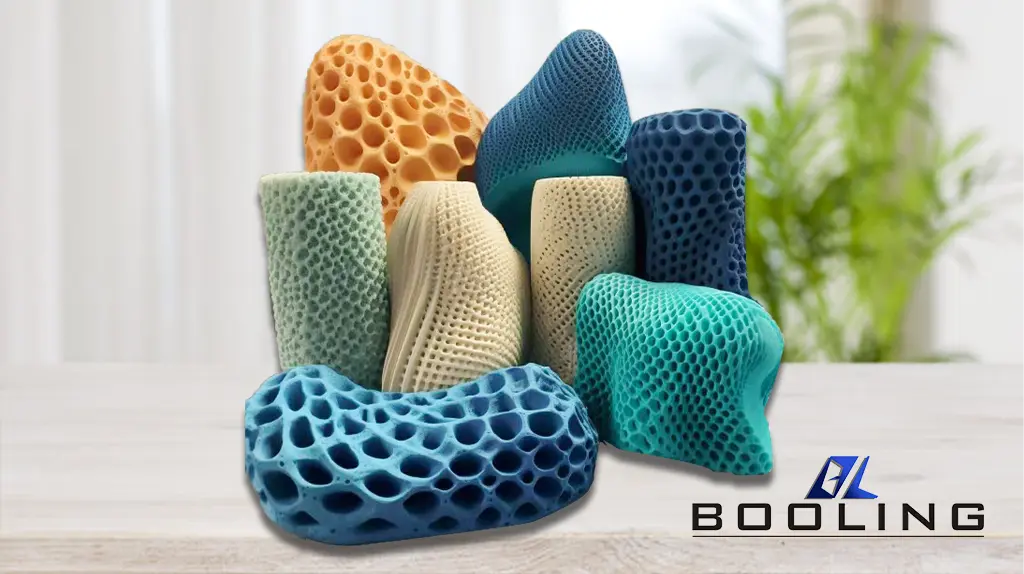
Custom 3D Printing Materials
Booling can provide a full range of 3D printing customized products and parts processing material options to meet the customized needs of various industries. The following is our core material system:
- Ceramic 3D printing
Ceramics, as an emerging material in 3D printing technology, is used by Booling as a raw material for making tableware, artworks, and other products. Common ceramic materials include zirconia ceramics, alumina ceramics, and silane ceramics. Ceramic products printed in 3D not only have excellent wear resistance and corrosion resistance but also have a unique gloss on the surface. Our ceramic 3D printing technology has been successfully applied to high-end dental restorations, and the product life has been increased by more than 3 times.
Metal is the most widely used material in 3D printing, and common metals include titanium alloy, aluminum alloy, stainless steel, etc. We usually use powder bed fusion technology or directed energy deposition technology for processing. Metal 3D printed products are corrosion-resistant and high-strength, suitable for small-batch production of products in electronic equipment, aerospace, automobile, medical, dental, and other industries.
- Plastic 3D printing
Common plastics that can be used for 3D printing include ABS, PLA, etc., which are usually processed in filament or powder form. We provide plastic 3D printing services such as FDM, SLA, SLS, etc. to quickly create plastic physical products.
Nylon materials have high strength and good toughness. SLS technology is usually used for laser sintering to create more complex 3D products. Nylon products have good wear resistance and strong stability, and can achieve lightweight production.
We continue to invest in material research and development and are committed to providing customers with better 3D printing solutions. The latest developed carbon fiber reinforced nylon material has been successfully applied to UAV structural parts, with a weight reduction effect of 40%.
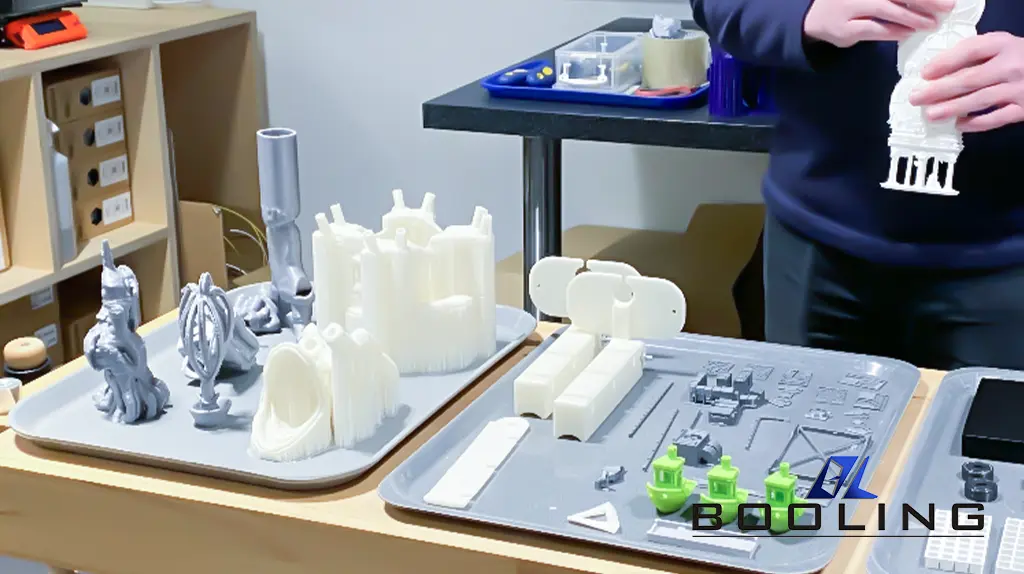
Common Processes for Custom 3D Printing
Custom 3D printing technology has a variety of commonly used processes. Our company provides fused deposition modeling (FDM), stereolithography (SLA), selective laser sintering (SLS), etc.
-FDM: Booling operators heat filamentary thermoplastics to a molten state, extrude them through a nozzle, and stack them layer by layer according to the originally set 3D model path. The extruded materials are solidified layer by layer to form the final 3D solid model. Compared with other additive manufacturing technologies, the materials used in our FDM technology are cheaper and relatively easier to operate.
-SLA: It is the earliest 3D printing technology, which mainly uses photosensitive resin for processing and requires cleaning equipment to remove uncured resin on the surface of the molded part. SLA 3D printing technology has a faster molding speed and can produce complex parts with higher precision.
-SLS: Sprinkle the raw material powder on the formed part and scrape it flat. Using computer control technology, a high-intensity laser beam is used to scan the current powder layer according to the part’s cross-sectional profile information. The powder absorbs energy under high-intensity laser irradiation. When the temperature rises to the sintering temperature, the powder particles melt at the junction and bond to each other to form the cross-section of the part, which is then bonded to the lower layer. The workbench descends, and the process is repeated layer by layer. After removing excess powder, the final part is obtained.
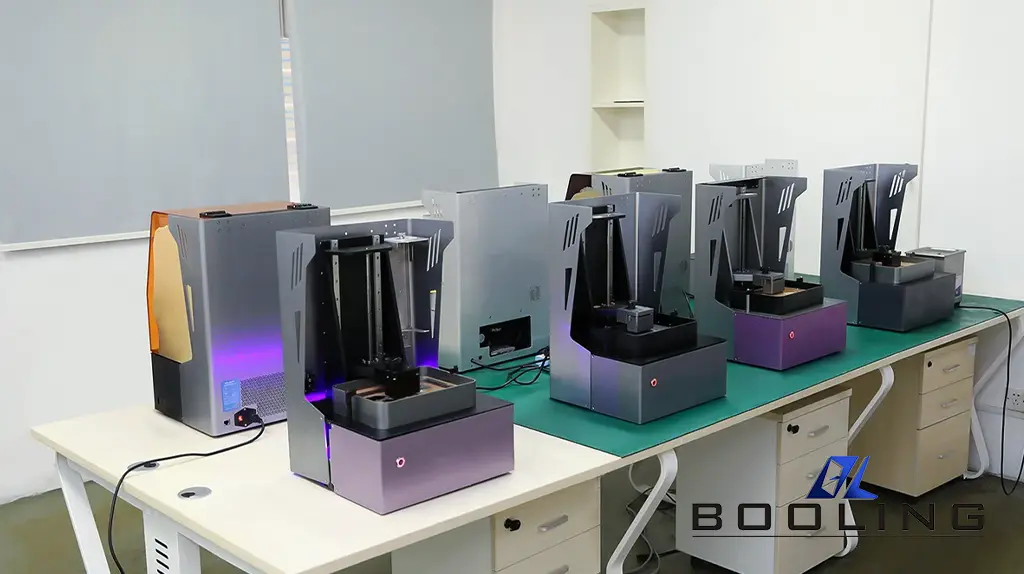
Custom 3D Printing Environment Standards & Specifications
At Booling, we are well aware that “excellent printing quality begins with strict environmental control”. After years of practical accumulation, we have established an industry-leading 3D printing environment management system.
- Machine placement environment: Place the printer on a stable platform for processing to avoid vibration and machine shaking, which may cause deviations and interfere with printing quality.
- Printing environment: Avoid using it in direct sunlight. It is more appropriate to process it in an environment with low humidity and high cleanliness. Generally, in order to obtain higher quality printed products, Booling’s designers will print in a constant temperature environment.
- Equipment placement requirements: Avoid placing custom3D printing equipment around flammable and explosive materials or high heat sources. Try to place the machine in a ventilated, cool and dust-free environment.
By implementing this set of environmental standards, the first pass rate of our printed products has increased from 92% to 98.5%. ” —— Manager Li, Quality Control Manager of Booling
3D Printing Service Related Content
Applied’s expertise in modifying materials at atomic levels and on an ihdustrial scaleenables our customers to transform possibilities into reality.