Home > 3D Printing Service > Carbon Fiber 3D Printing
Carbon fiber 3D printing technology is a combination of high-performance composite materials and high technology, which can achieve high-strength and lightweight product production. Carbon fiber itself has extremely strong tensile strength and is lightweight. Booling uses 3D printing technology to replace the traditional long-cycle rapid prototyping mold development and processing technology, helping the latest products designed in the aerospace, automotive, and other industries to achieve weight reduction and cost savings.
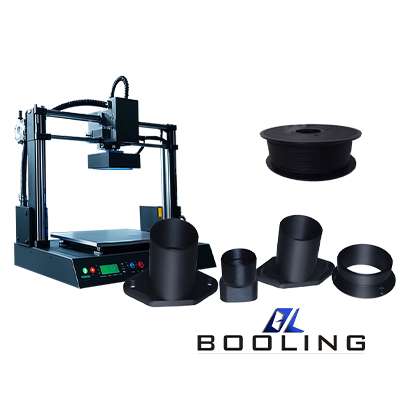
Carbon fiber 3D printing is a technology that produces products by adding material layer by layer. Booling combines the high strength and lightness of carbon fiber with the ability to create complex shapes of 3D printing technology to obtain higher quality 3D printed products.
High Strength-to-Weight Ratio
Create Complex Shapes
- Enhanced Mechanical Properties
Carbon Fiber 3D Printing Capabilities
Carbon fiber 3D printing provides excellent dimensional stability and heat resistance, and the product can maintain stable performance even in extreme temperature environments. Booling provides co-extrusion technology to more accurately control the overall path of 3D printing.
·
US
Metric
Carbon Fiber
47.2in. x 31.4 in. x 23.6 in.
1200mm x 800mm x600mm
*Carbon fiber 3D printing has the characteristic of high precision.
Carbon Fiber 3D Printing Material
Carbon fiber 3D printing products have the characteristics of high strength, extreme temperature resistance, and lightweight. Booling provides two types of printing materials: chopped carbon fiber and continuous carbon fiber to meet the manufacturing of products with different requirements.
Material:
l Chopped carbon fiber: Embedding carbon fiber particles in polymers such as polyetheretherketone (PEEK), PA, etc.
l Continuous carbon fiber: using a co-extrusion nozzle to lay continuous carbon fiber and matrix material
The Advantages of Carbon Fiber 3D Printing
Booling uses carbon fiber personalized 3D printing technology, and the design has high freedom, flexibility, and efficiency.
- Carbon fiber 3D printed products have extremely high mechanical properties and are lightweight, with a high strength-to-weight ratio
- Reduce the lead time and cost associated with mold making and machining, and speed up the manufacturing process, especially for some low-volume products and prototypes
- Booling provides customized design, high flexibility, fast iterative design, and on-demand production customization
- Reduce material waste and high utilization rate
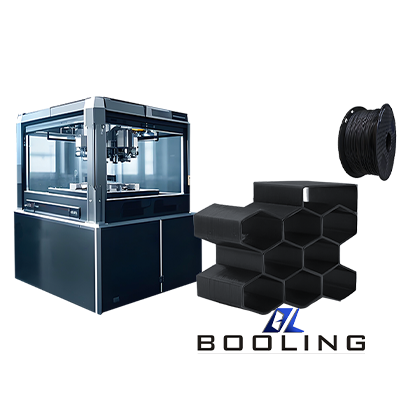
Application of Carbon Fiber 3D Printing
The most prominent feature of carbon fiber 3D printing is the ability to produce lightweight and high-strength products, which are suitable for the manufacture of automobiles, aerospace, medical devices, electronic equipment, etc. Bowling, as a 3D printing manufacturer with more than a dozen pieces of experience, has reduced the weight and cost of traditional materials during the processing and improved the overall quality of the product.
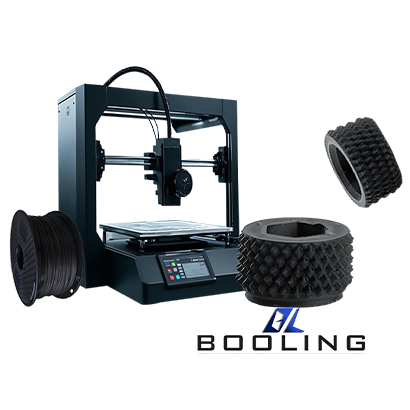
Guidelines for Carbon Fiber 3D Printing
Booling can provide answers to the most common questions about carbon fiber 3D printing technology. You can contact our engineers for one-on-one communication to learn more about 3D printing.
Carbon fiber 3D printing technology combines the versatility of 3D printing with the mechanical properties of carbon fiber raw materials. It can produce high-quality products with complex shapes and is widely used in aerospace, electronic equipment, automobiles, medical equipment, and other fields.
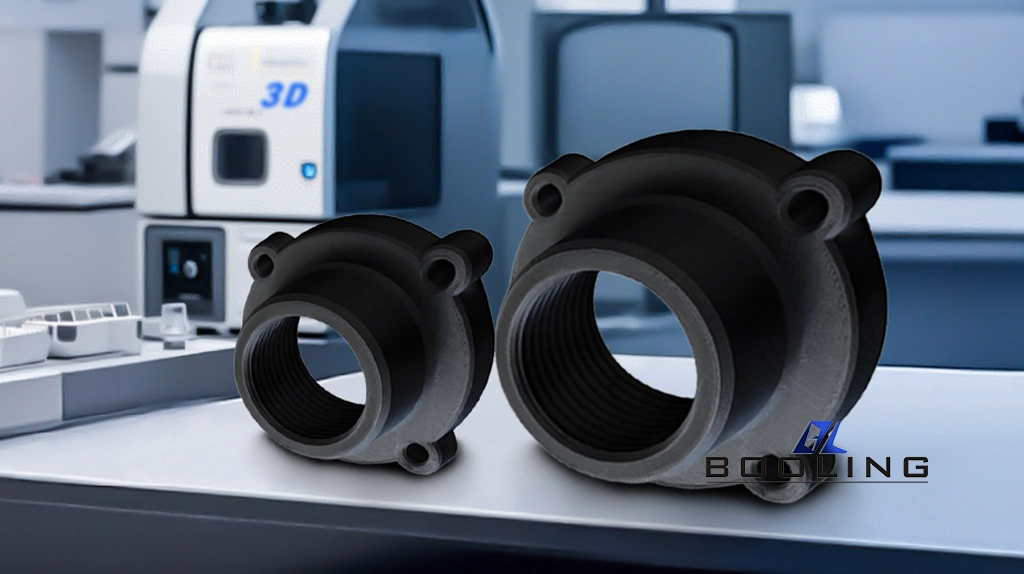
Principles of Carbon Fiber 3D Printing
Booling provides chopped carbon fiber and continuous carbon fiber 3D printing technology, using carbon fiber-reinforced materials for manufacturing to improve the mechanical properties of parts and products.
- Direct 3D printing
(1) Chopped carbon fiber printing
Chopped carbon fiber 3D printing technology involves combining carbon fiber with thermoplastics (such as PA, PEEK, etc.), and printing layer by layer through FDM technology to improve the stiffness and strength of the product and have high-temperature stability. Booling manufactures materials with specific functions by precisely controlling the arrangement and distribution of carbon fibers.
(2) Continuous carbon fiber
Continuous carbon fiber 3D printing is a process in which carbon fiber bundles are embedded in a polymer matrix and the material is composited by co-extrusion. The strength of the products printed using this process is greatly improved. Our engineers will use unique 3D printing equipment to perform this process to meet product requirements.
- Traditional carbon fiber 3D printing
(1) Wet printing
Carbon fiber wet printing technology is a process of cutting carbon fiber sheets, pressing them into a 3D printing mold, applying liquid resin, and bonding the sheets after solidification to obtain the desired shape.
(2) Prepreg lamination
Carbon fibers or other composite materials impregnated with resin are stacked and compacted in layers along a specific path and angle, and heated and cured to form a high-performance product. Booling’s prepreg lamination molding technology is mature, has strong designability, and is suitable for mass production.
(3) Resin transfer molding (RTM)
Put the dry carbon fiber reinforced material into the 3D printing mold, inject the resin into the mold cavity under a certain pressure and temperature, and cure it to form a part. Using automated equipment, Booling applies this process to mass production.
Carbon Fiber 3D Printing Types
Carbon fiber 3D printing technology has an excellent strength-to-weight ratio. We provide FDM, SLS, and CFF 3D printing technologies to meet the needs of different products.
- Fused Deposition Modeling (FDM)
In the FDM 3D printing process, filaments made of a mixture of carbon fiber and thermoplastics are extruded through a heated nozzle, and the parts are built layer by layer by deposition, eventually forming a composite 3D printed part with thermoplastics covering continuous carbon fiber filaments. Our engineers usually use this solution in the processing of some complex structures or small-batch customized products.
- Selective Laser Sintering (SLS)
This technology uses a carbon dioxide laser to selectively sinter powder materials. We provide the use of a variety of powder materials, such as wax, polycarbonate, nylon, or some metals.
- Continuous Fiber Fabrication (CFF)
CFF is mainly divided into key steps such as raw fiber preparation, pre-oxidation, carbonization, and graphitization. This method can embed continuous carbon fibers into the polymer matrix during the printing process, providing excellent strength and stiffness.
Application of Carbon Fiber 3D Printing
Booling provides customized carbon fiber 3D printing services to meet the needs of aerospace, automotive, consumer products, industry, and other fields.
- Aerospace
Structural parts: Carbon fiber 3D printed parts are lightweight and high-strength, and can replace metal parts in aircraft and spacecraft, reducing the total weight of spacecraft
Prototype design: Booling uses 3D printing technology to achieve rapid prototyping of aerospace components, reducing development and design time, and facilitating rapid testing and optimization of products
- Automobile
High-performance parts: Carbon fiber 3D printing has been widely used in automobile brackets, shells, aerodynamic parts, and other parts, reducing the overall weight of the car and improving strength and durability
Customized parts: Booling uses 3D printing technology to achieve customization and on-demand production services for parts and achieve after-sales guarantee
- Consumer goods
Sports equipment: Carbon fiber 3D printed products are high-strength and lightweight, and are widely used in the processing of sports equipment such as bicycles and rackets
Electronic equipment: Carbon fiber 3D printed electronic equipment housings and components are light and durable
- Industry
Tools and fixtures: Provide high strength and durability performance
Replacement parts: 3D printing technology can achieve on-demand production at a faster speed, reducing maintenance costs caused by downtime in manufacturing operations
Applications of Carbon Fiber 3D Printing
Carbon fiber 3D printing is used in a wide range of applications across various industries due to its exceptional properties and versatility:
1. Aerospace
Structural Components: Carbon fiber 3D printed parts are used in aircraft and spacecraft for structural components that require high strength and low weight.
Prototyping: Rapid prototyping of aerospace components allows for quick design iterations and testing, reducing development time and costs.
2. Automotive
Performance Parts: Carbon fiber 3D printed parts are used in high-performance vehicles for components such as brackets, housings, and aerodynamic parts.
Customization: The ability to produce custom parts on-demand is valuable for automotive manufacturers and aftermarket suppliers.
3. Defense
Lightweight Armor: Carbon fiber composites are used to create lightweight, high-strength armor for military vehicles and personnel.
Unmanned Systems: Carbon fiber 3D printed parts are used in drones and other unmanned systems for structural components and housings.
4. Consumer Goods
Sporting Equipment: Carbon fiber 3D printed parts are used in sporting goods such as bicycles, tennis rackets, and golf clubs for their strength and lightweight properties.
Electronics: Carbon fiber composites are used in consumer electronics for durable, lightweight housings and components.
5. Manufacturing
Tooling and Fixtures: Carbon fiber 3D printed tools and fixtures are used in manufacturing processes for their strength, durability, and customizability.
Replacement Parts: The ability to quickly produce replacement parts on-demand reduces downtime and maintenance costs in manufacturing operations.