Home > 3D Printing Service > Nylon 3D Printing
Nylon 3D printing mainly relies on two processes: Selective Laser Sintering (SLS) and Fused Deposition Modeling (FDM), of which SLS technology is the most widely used. Booling engineers provide customers with the high-quality assurance of high-strength, high-wear-resistant complex 3D printed parts through data preparation, slicing, powder laying, laser sintering, post-processing, and other processes.
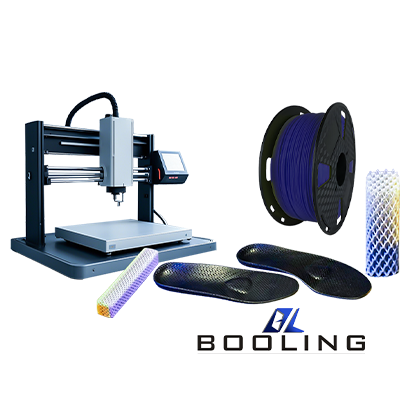
Nylon 3D printing is a versatile additive manufacturing technology capable of producing durable parts with complex geometries.
Types of Nylon 3D Printing:
- Selective Laser Sintering
- Fused Deposition Modeling
Nylon 3D Printing Capabilities
Booling provides high-quality nylon 3D printing, which uses nylon filaments or powders for additive manufacturing, and can maintain millimeter-level errors with high precision.
·
US
Metric
Nylon
47.2in. x 31.4 in. x 23.6 in.
1200mm x 800mm x600mm
*Nylon 3D printing has the characteristic of high precision.
Nylon 3D Printing Material
Nylon 3D printing materials have excellent strength, wear resistance, and heat resistance. Booling provides various types of raw materials such as PA12, PA6, PA66, etc. to meet the processing needs of different products.
- PA12: has excellent tensile and bending strength, and realizes the manufacture of strong and durable parts
- PA6: has a low melting point and good processing ability, suitable for the production of products with high surface requirements
- PA66: suitable for applications in scenarios with higher strength and heat resistance. It can also be modified and reinforced by glass fiber or other fillers
The Advantage of Nylon 3D Printing
- Nylon is a more durable thermoplastic, and its 3D-printed products have stronger mechanical properties
- Nylon 3D printing has flexibility and a high rigidity-flexibility ratio. Thin-walled printed parts are flexible and thick-walled printed parts are rigid, which is very suitable for producing parts such as movable hinges and snap parts
- Nylon parts are light in weight and can achieve lightweight development in the aerospace and automotive industries
- It has good surface finish, simple post-processing steps, and shortens the manufacturing process
- It has excellent wear resistance and impact resistance and is suitable for parts that are subject to wear, such as gears and pulleys
- The design is more flexible
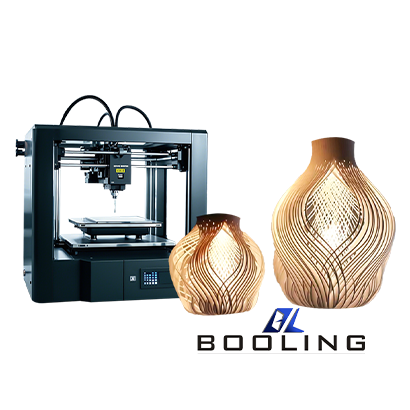
Application of Nylon 3D Printing
The research and development of nylon 3D printing technology meets people’s personalized needs in daily life. Booling provides 3D printing services for products in various fields such as medical, automotive, aerospace, home, and consumer goods.
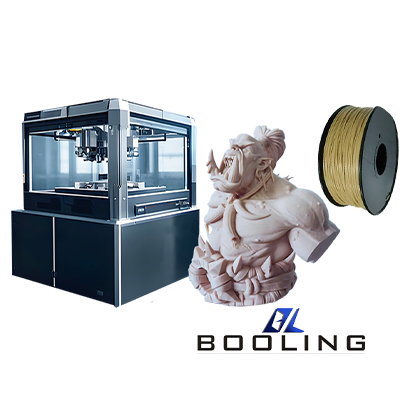
Guidelines for Nylon 3D Printing
Nylon 3D printing is a unique printing technology. Nylon is an ideal material for manufacturing complex parts due to its lightweight and high strength.
Nylon is a common and widely used material in the field of 3D printing. It is also called polyamide (PA), which has high strength, durability, and flexibility. Booling nylon 3D printing technology is an ideal choice for a variety of applications from functional prototypes to end-use parts, and it can realize the production of products without the help of tools such as molds.
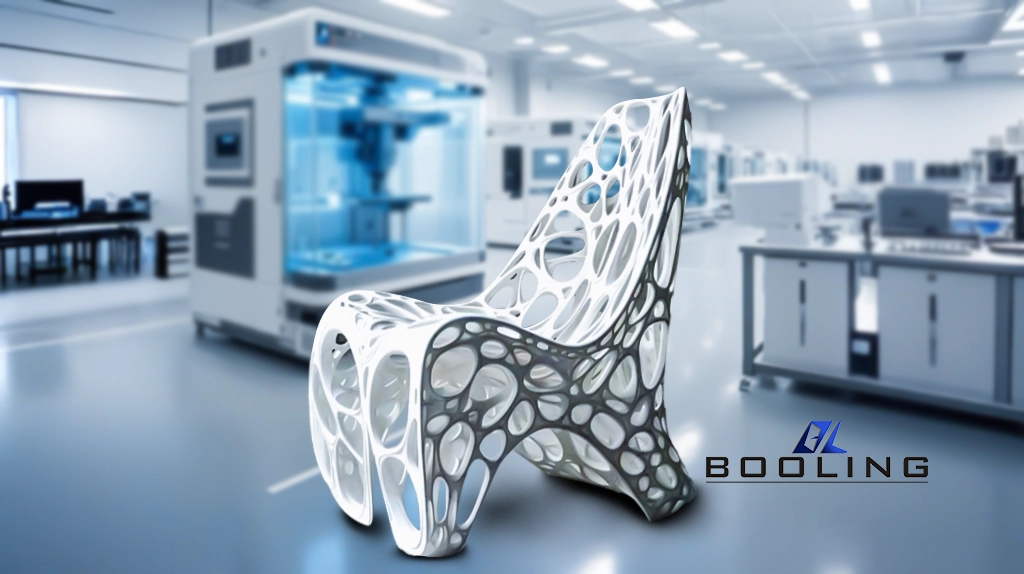
Nylon 3D Printing Methods
Nylon 3D printing is a process that uses nylon filaments or powders for additive manufacturing. Booling provides direct 3D printing and 3D printing molds for traditional nylon manufacturing.
- Direct 3D printing
Direct 3D printing is a method that uses nylon filaments or powders to directly convert digital models into physical parts. It is suitable for producing high-strength and durable functional parts that can be used directly in production.
(1) Fused Deposition Modeling (FDM): This method uses nylon filaments to build parts layer by layer after being sent out through a heated nozzle. The parts produced by FDM technology have high dimensional accuracy and low weight. Booling engineers will carefully manage the moisture absorption problem during the printing process to avoid the warping of the parts.
(2) Selective Laser Sintering (SLS): Use lasers to sinter powdered nylon materials layer by layer to shape the final parts. Unlike FDM technology, SLS technology uses nylon powder and can produce parts with complex collective shapes. Booling developed SLS technology to create moving and interlocking parts, eliminating the need for individual parts assembly and improving efficiency.
- 3D printed molds for traditional nylon manufacturing
3D printing technology can be used to create molds, such as injection molding molds. Booling combines the special advantages of nylon materials with the fast and efficient characteristics of 3D printing to provide the best solution for producing high-quality nylon parts.
Material Properties of Nylon 3D Printing
Booling provides a variety of 3D printing nylon materials to meet the requirements of different products, such as standard nylon filaments, carbon fiber reinforced nylon, glass-filled nylon, nylon powder for SLS, etc.
- Standard nylon filament: commonly used in the FDM 3D printing process, with high mechanical strength and softening point, can maintain stability in high-temperature environments, and has the characteristics of shock relief and noise reduction.
- Carbon fiber reinforced nylon: Carbon fiber reinforced nylon is a stable composite material that can improve the mechanical properties of the product and improve its heat resistance.
- Glass-filled nylon: Glass-filled nylon filament contains a certain amount of glass fiber to enhance the strength, toughness, heat resistance, and wear resistance of the material. This nylon material has been widely used in parts that need to withstand greater pressure, such as products in the fields of automobiles and aerospace.
- Nylon powder for SLS: Nylon powder used in the SLS process has excellent wear resistance, toughness, and heat resistance and has been widely used. Booling can achieve efficient recycling of old powder and reduce manufacturing costs.
Application of Nylon 3D Printing
Nylon material has the characteristics of high strength, wear resistance, and good mechanical properties. Combined with 3D printing technology, it has become the best solution for the manufacture of complex parts. Nylon 3D printing has been widely used in automobiles, aerospace, sporting goods, electronic equipment, medical equipment, and other fields.
- Automobile: Nylon 3D printing is used to produce high-performance automotive brackets, housings, and aerodynamic parts. Booling provides on-demand customized production of automotive parts to meet the needs of automakers and the aftermarket.
- Aerospace: Nylon materials have good stability at extreme temperatures and can be used to produce internal structural parts and external parts of aircraft and spacecraft to achieve high strength and low weight. Booling also provides rapid prototyping of aerospace components to help companies achieve rapid product updates, iterations, testing, and optimization, and reduce development time and costs.
- Sporting goods: Nylon 3D printed products are light and high-strength, and can be used in the manufacture of sporting goods such as bicycles and tennis rackets.
- Electronic equipment: Nylon composites can be used to manufacture lightweight and durable electronic equipment housings and components.
- Medical equipment: Nylon 3D printing can be used to produce customized prostheses and orthotics with extremely high biocompatibility, ergonomics, and patient comfort. Booling provides nylon 3D-printed surgical instruments and anatomical models to achieve visibility in medical education.
How to Achieve Quality Control of Nylon 3D Printing?
For nylon 3D printing, Booling has a strict quality control program to prevent product defects caused by nylon material absorbing water.
- Drying: Excessive water absorption by nylon materials can cause defects in printed parts. Engineers place nylon filaments in a sealed container with desiccant and dry them before printing
- Heated bed: During the printing process, the heated bed is generally set to a temperature of about 45°C to prevent product warping and obtain the best printing effect
- Printer: Use a printer with a substitute class to maintain a stable printing environment to prevent the risk of warping due to temperature fluctuations
- Print settings: Timely adjust the printing parameters to optimize the printing quality, such as layer height, printing speed, and cooling, and provide the best parameter setting solution
- Post-processing: Nylon 3D-printed products generally have a good surface finish. Booling performs additional sanding, dyeing, or painting to further enhance the appearance and function of the parts