Home > 3D Printing Service > Silicone 3D Printing
Silicone 3D printing technology is also known as additive manufacturing technology. Liquid silicone materials are stacked layer by layer and solidified to form silicone parts with complex shapes. Compared with traditional technology, silicone 3D printing can form silicone parts without the help of molds and achieve millimeter-level accuracy. By utilizing personalized customization and 3D scanning technology, silicone 3D printing has become a key technology for the manufacture of low volume of complex products.
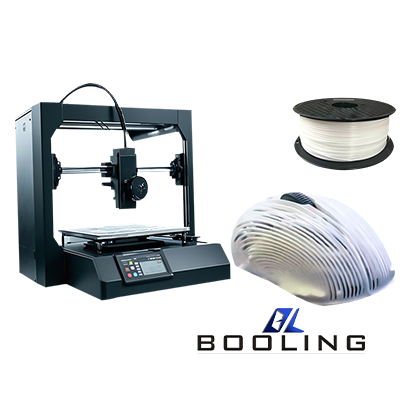
Silicone 3D printing technology is often used to create models in the fields of mold manufacturing, industrial design, etc., and has now been gradually developed for the direct manufacturing of products, achieving replication capabilities and customization, with a certain degree of design freedom.
- Entity Replication Capability
- Customized
- Design Degrees of Freedom
Silicone 3D Printing Capabilities
Booling provides silicone 3D printing processing, such as rapid prototyping and low volume production of complex products, and provides on-demand customized processing.
·
US
Metric
Silicone
47.2in. x 31.4 in. x 23.6 in.
1200mm x 800mm x600mm
*Silicone materials have the characteristics of high-frequency insulation, good water resistance, and good resistance to high and low temperatures.
Silicone 3D Printing Material
Silicone 3D printing can print 3D models with higher flexibility and durability through the printer to withstand higher loads and pressures. Booling provides materials such as silicone resin and light-curing silicone to achieve higher precision printing effects.
Material
- Silicone
The Advantages of Silicone 3D Printing
As a widely used manufacturing technology, silicone 3D printing eliminates the mold manufacturing step in the traditional processing process and shortens the project processing cycle.
- Silicone has high transparency and combines the characteristics of conductivity, insulation, and biocompatibility. It is widely used in visual inspection models
- Silicone 3D printing does not require any molds, has high design freedom, and saves processing costs and time
- Each 3D printed component can be customized and produced on demand according to different requirements
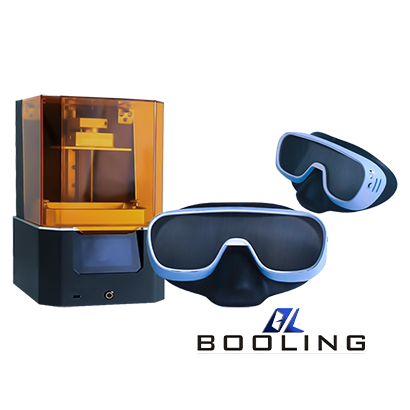
Application of Silicone 3D Printing
Silicone materials have certain transparency and biocompatibility and have been widely used in the fields of automobiles, aerospace, medical equipment, electronic products, wearable devices, etc.
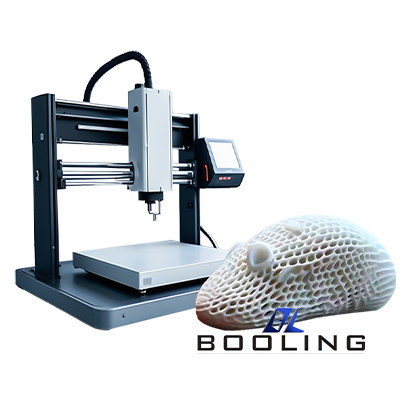
Guidelines for Silicone 3D Printing
Silicone 3D printing technology is suitable for the processing of small and medium-sized batches of products. Booling uses this technology to process complex product prototypes or samples, improving processing feasibility.
Silicone 3D printing is a product construction technology that prints layer by layer based on digital model files. It is often used in model manufacturing in the fields of molds, industrial design, etc. to improve the feasibility of precision processing. Booling uses this technology to directly manufacture products. Silicone materials have extremely high stability and can remain stable even in extreme temperature environments.
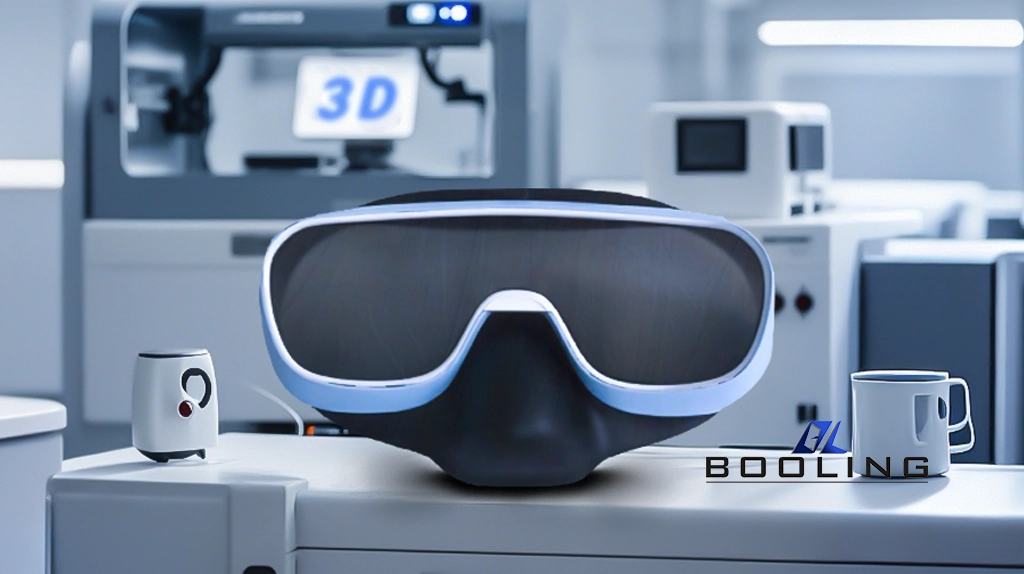
Silicone 3D Printing Technology
Silicone 3D printing technology has simple equipment and fast molding speed and has been widely used in the field of advanced manufacturing.
- Fused deposition modeling
Engineers use print heads and 3D laser scanning technology to selectively fuse and deposit 2D molding materials layer by layer for printing. Silicone cannot be melted or printed like extruded filaments, but fused deposition technology is used before formal processing and manufacturing. Booling uses the FDM heating head to heat thermoplastics to a semi-fluid state and moves along a pre-set two-dimensional geometric trajectory under the control of the software. The material solidifies instantly after extrusion to form a thin layer with a contour shape.
When engineers choose support materials, they generally choose water-soluble materials or materials with a lower melting point than the molding material to facilitate the subsequent cleaning and removal of support structures. The main purpose of support materials is to provide processing stability and prevent products with suspended structures from sagging or collapsing.
- Curing or vulcanization
Silicone materials are in a liquid or gel state when not cured, and the method of use is simple, but it is not suitable for building solid 3D products. Booling cures vulcanizes, or catalyzes each printed layer to form crosslinks in the polymer chain.
Engineers use ultraviolet light or high temperature to complete the curing process or use room temperature vulcanized (RTV) silicone resins, which harden when reacted with substances such as catalysts. Booling provides a VAT photopolymerization process, which uses the photochemical reaction principle of photosensitive resin to achieve micron-level processing accuracy.
- Post-processing
Although the layer-by-layer vulcanization or catalytic curing method can keep the silicone hard enough for the next layer to be printed, it is not enough to cure the entire part.
After the silicone product is removed from the 3D printer, it needs to go through a long post-curing process, such as processing in an oven, to further promote the chemical reaction of the silicone and remove unwanted particles and support materials.
3D printing Customization Service
Booling provides a 3D printing customization service, which is suitable for the processing and manufacturing of small and medium batches, product prototypes, and complex samples.
- No need to use any molds or molding tools, directly complete the conversion of digital models to physical objects, reduce production costs, speed up production, and is suitable for low volume production and processing
- Greatly shorten the process cycle, quickly improve products during product development, and optimize product structure
- Each 3D-printed component is customizable. Silicone 3D printing customization technology is widely used in the oral and nursing industries to meet customization needs and help stimulate the production of anatomical models of human tissue
- Booling provides 3D printing of integrated functional components and complex structural prototypes
Application of Silicone 3D Printing
Silicone has certain biocompatibility and flexibility, good insulation, waterproofness, and extreme temperature resistance, and is used in various fields such as consumer goods, automobiles, acoustics, medical, and robots.
- Consumer goods: Silicone 3D printing can produce customized products that come into direct contact with the skin, such as earphone earbud adapters, earphone pads, etc. Silicone products have durability and shock absorption properties, making them high-quality manufacturing materials for protective covers and shells of electronic devices such as smartphones and tablets
- Automobile: Silicone 3D printed parts are used in automobile engines and other parts to reduce and isolate the vibration and noise of the car and improve the comfort of passengers
- Acoustics: Used to make sound insulation materials, such as soundproof screens, mufflers, and shock absorbers
- Medical: Silicone 3D printed products have extremely high biocompatibility and can be used in the manufacture of medical implants, prostheses, and prosthetic inserts. It can also be used to make medical models and auxiliary materials for some shell surgeries
- Robotics: Silicone 3D printing is an ideal process for making soft robots, such as some fixtures that can grasp and manipulate delicate objects