Home > LSR Injection Molding Process
LSR Injection Molding
Liquid silicone rubber has excellent elasticity, toughness, and temperature resistance, and can be injection molded to produce delicate and smooth products. Widely used in the manufacturing of medical devices such as catheters, syringes, etc.
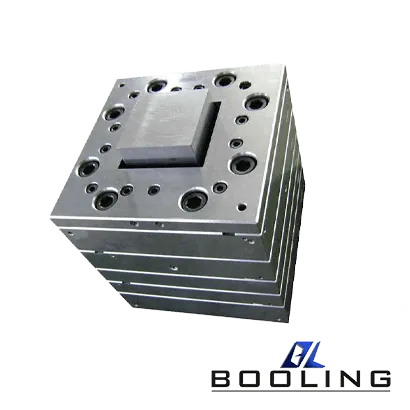
LSR Injection Molding Process
LSR injection molding is a high-precision and high-quality manufacturing process, and its basic principle is to package silicone rubber materials through an injection molding machine. A silicone rubber injection molding machine is a machine that injects silicone rubber in a liquid state into a molding mold according to predetermined dimensions and shapes. During the injection process, silicone rubber is injected into the syringe, pressed into the mold, and then cooled and solidified at a certain temperature to form a molded part.
LSR injection molding products are highly valued and praised by consumers and manufacturers. Liquid silicone rubber is made from silicone rubber products, which have good toughness, waterproof and moisture-proof properties, and are resistant to corrosion from various chemical substances such as acid and alkali. Therefore, it is generally used as a substitute for living plastic products. Liquid silicone rubber is composed of two parts: A rubber and B rubber. The ratio of the two is controlled by a quantitative device to be 1:1, and then the two are fully mixed through a static mixer. After injection into the injection tube, injection molding production is carried out.
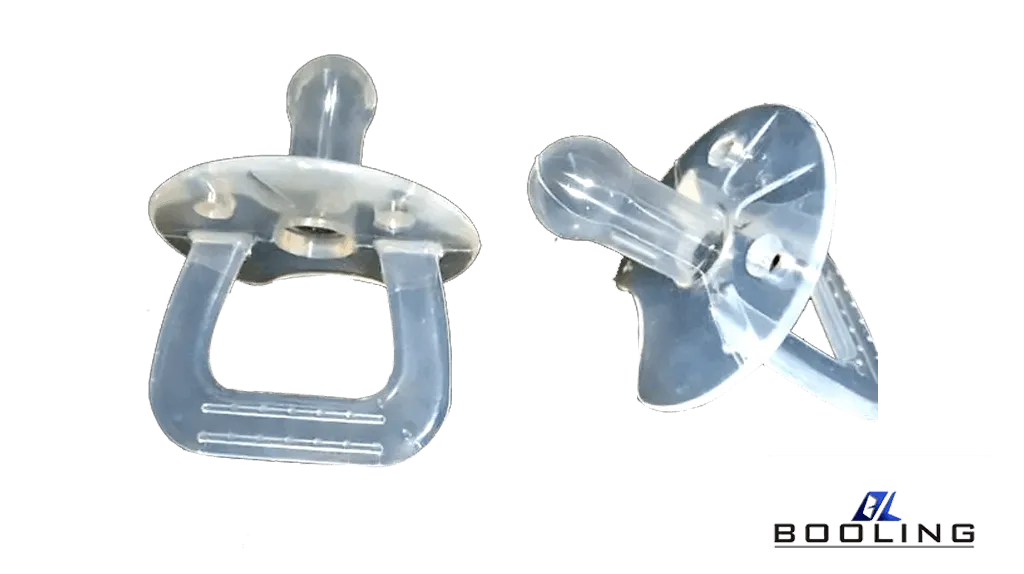
The Advantages of LSR Injection Molding
LSR injection molding combines the advantages of short-term automatic molding and plastic composite molding, including:
- Before forming vulcanization, there is no need for roller mixing, and there are no foreign objects mixed in the sealing system during operation. There is no need for rubber filtration treatment, which is more environmentally friendly compared to other processes and eliminates secondary pollution.
- The forming vulcanization cycle is short (10~40s), automated operation saves labor, and production efficiency is higher than that of high-temperature molding. Automated equipment can improve cost-effectiveness in feeding, metering, and other work.
- It can achieve no overflow, and no channel forming, reduce waste, and edge trimming treatment.
- The vulcanization process has no by-products and generally does not require secondary vulcanization, eliminating environmental pollution;
- Suitable for composite molding: Silicone rubber materials have good fluidity, low molding pressure, and a wide range of curing temperatures. Therefore, in addition to being able to form embedded parts, they can also be combined with plastics (PA, PC, PBC, etc.) or metal-embedded parts for composite molding and two-color molding.
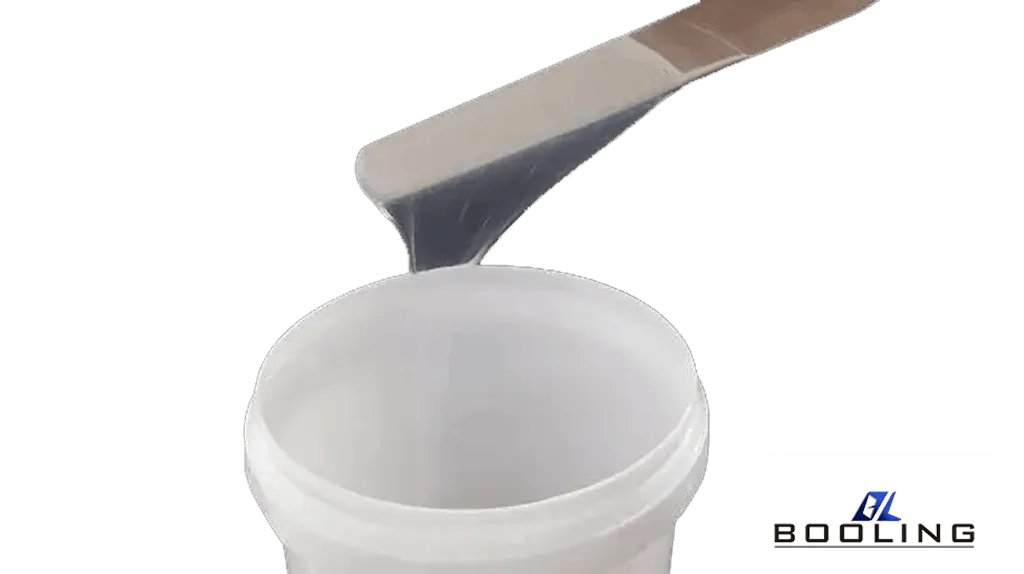
Application and Industry of LSR Injection Molding
LSR injection molding is an advanced processing technology that plays a crucial role in various industries. As an advanced material, liquid silicone rubber has excellent aging resistance and extreme temperature tolerance, which makes it widely used in many industrial fields. The material characteristics of LSR injection molding make it an ideal choice in industries such as healthcare, electronics, automotive, and home furnishings, providing reliable solutions for manufacturing high-performance products, such as:
In the medical sector, LSR injection molding provides an ideal material choice for the production of medical devices and components for medical purposes. Due to its high-temperature resistance and antibacterial properties, liquid silicone rubber can be used to manufacture medical device seals, infusion tubes, artificial organs, etc. In addition, as the material does not contain harmful substances and is easy to clean and disinfect, it can also be used to manufacture baby products such as medical hoses and baby milk bottles.
In the electronics industry, LSR molding also plays an important role. Due to its excellent temperature resistance and electrical insulation performance, liquid silicone rubber can be used to manufacture seals for electronic components, cable insulation layers, protective sleeves, etc. At the same time, this material is also widely used as a touch screen for electronic products such as mobile phones and tablets, providing excellent touch perception and wear resistance.
In the automotive field, LSR injection molding can be used to manufacture automotive wiper blades, waterproof seals, air filters, engine seals, and water tank sealants. Liquid silicone rubber is also used to manufacture hydraulic pipes and high-temperature seals for automotive engines, and its excellent high-temperature resistance ensures the efficient operation of automotive engines.
In the home industry, LSR products, such as kitchenware, baby products, toys, etc., provide users with a better user experience due to their good toughness and high-temperature resistance.
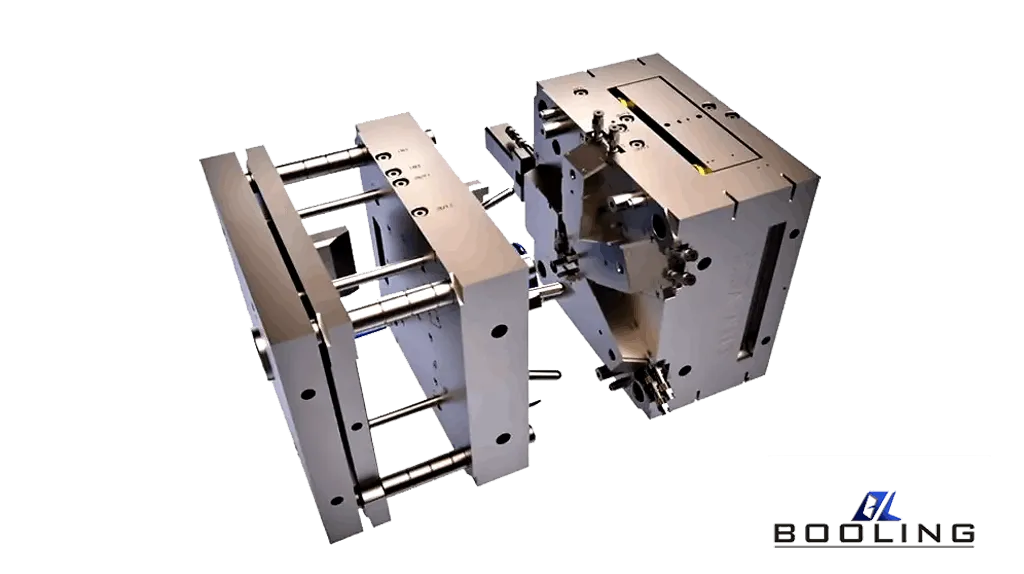
The Process Flow of LSR Injection Molding
- Preliminary Preparation
Determine product design drawings, dimensions, and accuracy requirements; Select suitable silicone rubber materials and conduct experiments; Prepare injection molding machines, molds, silicone rubber pretreatment equipment, etc.
- Pre Treatment of Silicone Rubber
Mixing of silicone rubber raw materials: Mix solid silicone rubber and liquid silicone rubber in a certain proportion and stir evenly.
Defoaming: Put the mixed silicone rubber into a vacuum tank to remove bubbles.
Heating: Heat the vacuum tank to the desired temperature to improve the flowability of silicone rubber and achieve optimal performance.
- Injection Molding
Mold installation: Install the mold on the injection molding machine and adjust the injection position and pressure to the desired position and value.
Feeding: Put the preprocessed silicone rubber into the hopper of the injection molding machine, and then open the injector for feeding.
Injection molding: According to product design requirements, control parameters such as temperature and pressure to perform injection molding. At the same time, pay attention to observing the condition of the mold to avoid problems such as material leakage or mold jamming.
- Demoulding and Dressing
Demolding: After the product cools and solidifies, open the injection molding machine to demold and remove the silicone rubber product.
Trimming: For products with scratches, burrs, and other issues, perform trimming to reduce the risk of rework and rejection.
- Post Processing
Inspection: Compare the size and appearance of silicone rubber products with the design requirements to ensure that the products meet quality requirements.
Packaging: Pack qualified silicone rubber products with clear product information.
Storage: Store packaged silicone rubber products in a dry, ventilated, and dark warehouse to avoid moisture or direct sunlight, which may cause surface erosion of the products.
Maintenance and Upkeep of the LSR Injection Molding Machine
The maintenance and upkeep of LSR injection molding machine are specific measures taken to turn unexpected mechanical failures into predictable and planned shutdowns or repairs, and to avoid chain mechanical failures, including:
Daily Maintenance of LSR Injection Molding Machine:
- Maintenance of Lubrication System. Before each shift operation, lubricating oil should be added to the specified daily lubrication points to ensure proper lubrication. If the machine equipment has a centralized lubrication system, the oil level should be checked regularly every day and lubricant should be added before the oil level drops to the specified lower limit. Before the initial start-up and operation of the machine equipment, lubricating oil should be added to the required lubricating oil position and can be added every three months thereafter.
- Regularly Check The Oil Level In The Fuel Tank. The oil level in the fuel tank should be checked regularly every day. If the oil level is below the center line of the dipstick mark, the oil level should be replenished promptly to meet the center line. During this operation, pay attention to the cleanliness of the oil on the work, which can prevent serious pollution of the oil by water, iron shavings, wood residue, cotton yarn, and other dirt, causing deterioration of the oil or blockage of various valves, and increasing maintenance costs.
- Regular Inspection of Heating Safety Devices. After taking over each shift, the heating safety device should be checked to see if everything is normal, if there is any poor contact with the heating coil, if there is any loose connection, and if the thermocouple is in good contact.
- Regular Inspection of Safety Facilities. Each shift should regularly check the electrical switches, especially the safety doors and limit switches, to ensure that everything is normal. Before taking over, special attention should be paid to whether the emergency stop switch and safety door are functioning properly. When the liquid silicone rubber machine is started, press the emergency stop switch to immediately stop the hydraulic pump or motor, and other functional components should stop moving immediately.
Daily Maintenance Steps for LSR Injection Molding Machine:
- To replace the adhesive, it is necessary to clean the pipeline. Before cleaning, it is necessary to close the feed valve and open the discharge valve to discharge the remaining rubber material from the rubber bucket. Then, close the discharge valve and open the feed valve to introduce the cleaning solvent, activate the machine body, and press the solvent out for flushing.
- If the air pressure intake is abnormal and water vapor is found, the water vapor in the pressure regulating filter should be removed or the air pressure source should be checked for abnormalities. Before using a large amount of glue, the silicone rubber dispensing machine should be tested in small quantities to master the product’s usage skills and avoid waste and usage errors. When the test is successful, the double liquid drip glue machine or double liquid filling glue machine can be used for large-scale production; If bubbles are generated during the mixing process, it is necessary to use a vacuum system to remove the bubbles from the glue or let it stand for 10-20 minutes before use, to eliminate the bubbles, obtain more glue, improve cost-effectiveness, and achieve optimal performance.
- Regularly wipe the machine part to increase its service life. The more glue is mixed together, the faster the reaction and curing speed will be. Therefore, it is necessary to make a reasonable mix of glue according to the actual production situation, otherwise, it will cause a waste of glue. Eliminate accidents and reduce costs and expenses. Nowadays, liquid control technology and dispensing equipment are playing an increasingly important role in various production fields in modern industry.
- When the machine is out of use for a long time, the power should be unplugged. This not only extends the lifespan of the machine but also saves electricity costs. With the progress of industrial development, liquid control technology and dispensing equipment are also constantly moving towards ultra-high precision control, diversification, and specialization. To avoid problems such as aging caused by UV radiation during the use of wholesale products in container bags, it is necessary to conduct UV resistance testing during product production to ensure its excellent performance.
Cleaning of LSR Injection Molding Machine after Use:
- After using this LSR injection molding machine for spraying, cleaning the liquid silicone rubber in the injection machine is a very important work step. If the residual silicone rubber after use is not cleaned promptly, it may cause malfunctions in the next use, thereby affecting the new silicone rubber liquid and causing irreparable cost losses.
- Regularly check whether the injection head of the LSR injection molding machine is intact. If the injection head malfunctions, the injection process will be greatly affected. Therefore, the injection head needs to be regularly inspected and replaced to ensure its patency.
- As an LSR injection molding machine equipment that requires lubrication, the staff should do a good job in lubrication to ensure the efficient and smooth operation of the equipment.
Related News
Applied’s expertise in modifying materials at atomic levels and on an ihdustrial scaleenables our customers to transform possibilities into reality.