Home > Extrusion Blow Moulding Equipment
ABS Blow Molding
The entire process of ABS blow molding can be divided into three stages: billet formation, billet inflation, and cooling solidification. Its special process is particularly suitable for large-scale and high-capacity container production.
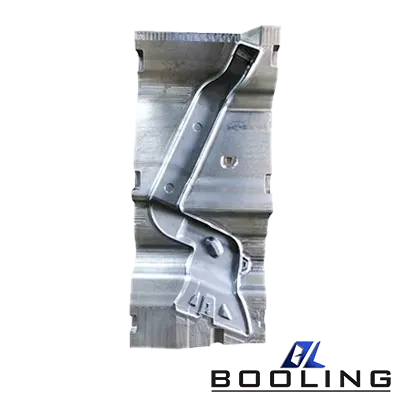
Extrusion blow moulding can be said to be the most popular process in blow molding, mainly used for blow molding precision seamless hollow products, and is widely used. Extrusion blow moulding is mainly the process of extruding or injecting thermoplastic raw materials into a semi-molten tubular billet, which is then heated and softened. After being placed in a mold, compressed air is introduced to blow and expand the billet, making it tightly adhere to the inner wall of the mold cavity, thus forming a hollow product.
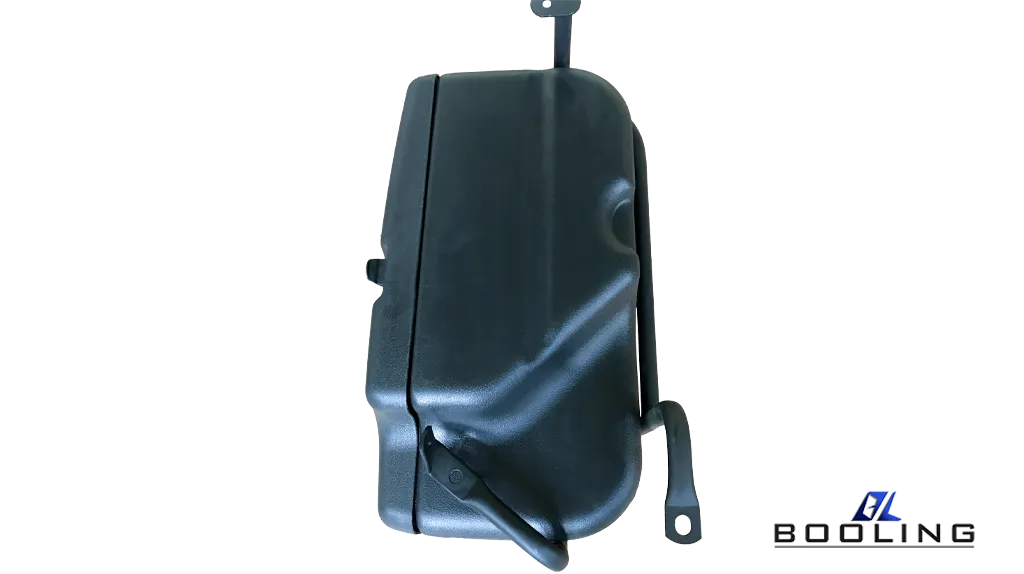
Classification of Extrusion Equipment Machines
There is much equipment for extrusion blow moulding, and manufacturers need to understand the classification of blow molding machines to choose the appropriate blow molding extrusion equipment based on their own use and usage environment. In addition, when use polypropylene, polyethylene, or ABS blow molding, it is necessary to choose blow molding equipment with a water absorbing device.
-According to the capacity of blow molding containers, extrusion blow moulding machines can be divided into small blow molding machines, medium blow molding machines, and large blow molding machines. Small blow molding machines can be used to manufacture containers and bottles below 5L; A medium-sized blow molding machine can be used to manufacture 5-60L bags and some industrial accessories; Containers above 50L require the use of large blow molding equipment for processing. The above blow molding equipment also needs to be selected according to the actual production and processing situation of the manufacturer, which is relative.
-According to the structure of the billet head, extrusion blow molding machine equipment can be divided into repeated screw blow molding machine, ordinary right angle blow molding machine, plunger storage chamber blow molding machine, right angle blow molding machine with storage cylinder, and right angle blow molding machine with multi-point programmable storage cylinder.
-According to the form of mold locking devices, extrusion blow moulding equipment can be divided into hinge type single mold blow molding machines, single mold blow molding machines, double or multi mold reciprocating blow molding machines, multi rotary disc blow molding machines, and multi mold vertical blow molding machines.
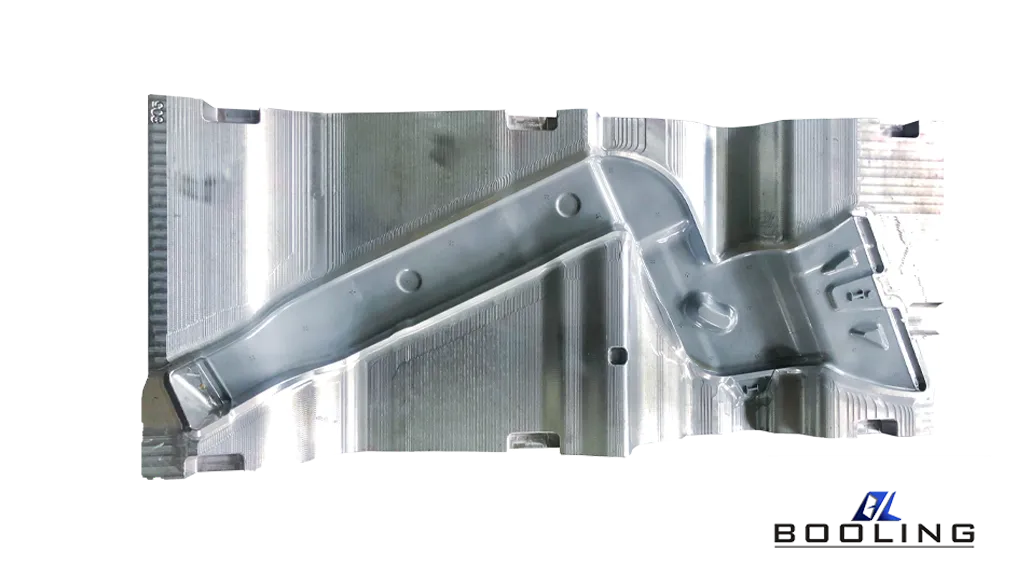
Selection of Extrusion Blow Moulding Equipment
When manufacturers choose extrusion blow moulding equipment, they need to consider the following performance characteristics of the injection molding machine:
- The extrusion blow moulding equipment should have good molding processing performance, stable and convenient operation, not easily changed when setting molding parameters, simple maintenance, and diverse and convenient channels for purchasing required components and parts.
- The extrusion blow moulding equipment should be stable, safe, and durable. The parameters during processing and forming should be stable and have small fluctuations. Moreover, extrusion molding equipment should have a certain protection mechanism, such as protection for molds and operators. Manufacturers should consider this when selecting machines.
- Blow molding manufacturers should consider the basic performance of the extruder, which is the main basis for selecting an extruder. This includes whether the equipment meets quality requirements, what is the output, what is the power, and what is the flow rate. Manufacturers can obtain the most cost-effective and efficient extrusion molding equipment by comparing the basic parameters of various models of extruders.
Structure of Extrusion Blow Moulding Equipment
The structure of extrusion blow moulding equipment is relatively complex, mainly consisting of an extrusion system, transmission system, cooling and heating system, etc.
-Squeeze System
- Screw: this is the most important component in extrusion blow moulding equipment, which directly affects the application scope and production efficiency of extrusion molding blow molding equipment. Generally made of high-strength metals with excellent performance.
- Cylinder: It is generally a metal cylinder made of sturdy alloy steel or composite steel pipes that are resistant to high temperature, high pressure, and corrosion. The barrel and screw work together to crush, soften, melt, plasticize, exhaust, and compact plastic, and continuously and uniformly transport the rubber material to the molding system. Generally, the barrel should follow the principle of fully heating and plasticizing the plastic.
- Hopper: The bottom of the hopper is generally equipped with a cutting device, which can adjust and cut off the material flow. The hopper of the blow molding equipment can also control the speed and quantity of plastic particle transportation according to the machine’s needs.
- Head: The head of the extrusion blow moulding equipment and the head of the mold are composed of a carbon steel outer shell and an alloy steel inner sleeve. The head is equipped with a molding mold, which is used to transform the rotational motion of the molten plastic into parallel linear motion, to evenly and smoothly guide it into the mold sleeve and give the plastic raw materials necessary molding pressure. After the plastic is plasticized and compacted inside the machine barrel, it passes through a porous filter plate along a certain flow channel, passes through the neck of the head, and flows into the molding mold of the head. The appropriate fit between the core and sleeve of the mold should be made to form a continuously decreasing circular gap so that the plastic melt can form a continuous and dense tubular coating layer around the core wire. To ensure a reasonable plastic flow channel inside the extrusion blow molding equipment head, manufacturers often install diversion sleeves to eliminate dead corners of accumulated plastic and pressure fluctuations during plastic extrusion. Some manufacturers also set pressure-equalizing rings. To adjust and correct the concentricity of the mold core and sleeve, the head of the extrusion blow molding equipment is often equipped with a device for mold correction and adjustment. The external part of the machine head is also equipped with a heating device and a temperature measurement device.
-Transmission System
Driven by the transmission system, the screw begins to operate. The system of extrusion blow moulding equipment usually consists of structures such as electric motors, reducers, and bearings. When other conditions remain stable and unchanged, the design and manufacturing of a gearbox are often proportional to its external dimensions and weight, because the gearbox has a larger shape and weight, often consuming more materials, and using larger bearings, which will increase the energy and time required for design and manufacturing. When the screw diameter of the extrusion blow moulding machine is the same, the energy consumption of a high-speed and efficient extruder is much greater than that of a conventional extruder. The power of the motor will be doubled, and the reducer should also be correspondingly increased. But if the screw speed is high, it means that the deceleration is relatively low. Compared to those with high reduction ratios, reducers with the same weight and size have an increased gear module and a greater ability to withstand loads. Therefore, the increase in volume and weight of the reducer in the extrusion blow moulding equipment is not linearly proportional to the increase in motor power.
-Heating and Cooling Device
- Nowadays, extrusion blow moulding equipment usually uses electric heating technology, including resistance heating and induction heating. Heating plates can be installed in various parts of the machine’s neck, body, and head. The heating device heats the inside from the outside to raise the temperature of the plastic inside the barrel, reaching the temperature required for subsequent extrusion blow moulding operations.
- The manufacturer sets up a cooling device to ensure that the plastic can be within the temperature range required by the process. Specifically, it is to timely eliminate the excess heat generated by screw rotation, and shear friction, to avoid the high temperature of extrusion blow moulding equipment, which may cause plastic decomposition, scorching, prolonged cooling time, or difficult solidification and shaping. Barrel cooling can be divided into water cooling and air cooling. For general small and medium-sized extrusion blow molding equipment, manufacturers usually use air cooling, while for large equipment, water cooling or a combination of the two forms is often used; The cooling of the screw mainly adopting central water cooling, with the main purpose of increasing the conveying rate of solid materials, maintaining stable glue output, and improving the accuracy and quality of the product.
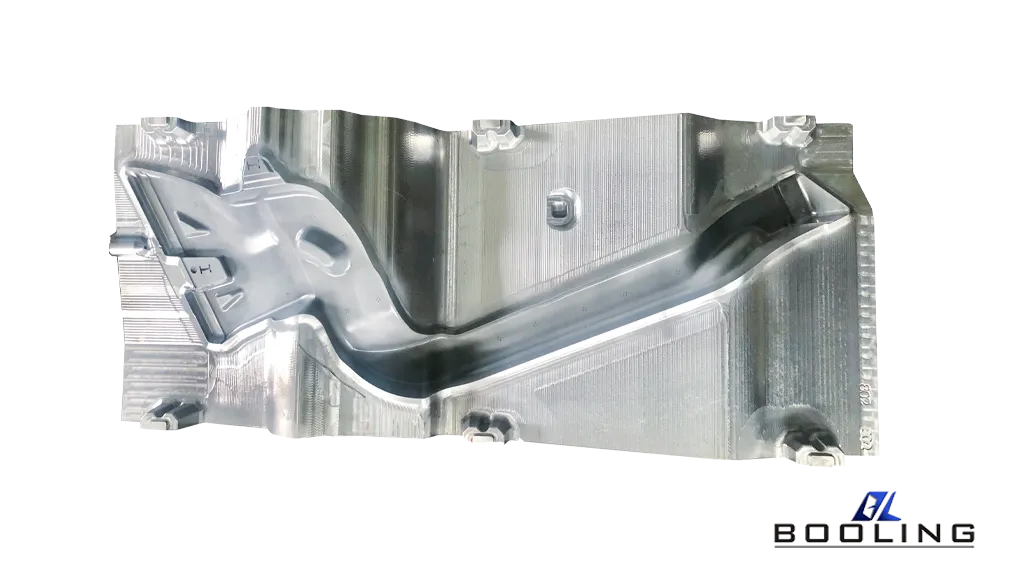
Maintenance of Extrusion Equipment
The structure of extrusion blow moulding equipment is relatively complex, and there is a certain degree of processing difficulty, which also makes it prone to friction and damage during molding. Therefore, manufacturers need to regularly maintain and repair the machine during use to ensure its service life.
- Manufacturers should regularly inspect the cutting tools and screws of the extrusion blow moulding equipment. After using the brand-new equipment for an hour, they should use tools to reinforce the screws promptly and enhance the stability between the blade and the tool holder; Lubricating oil should be regularly added to the bearings of the extrusion blow moulding equipment to ensure lubrication between the bearings; Manufacturers should also regularly check the sharpness of the cutting tools to ensure that they are not passivated and avoid damage to other components; When encountering a loose belt, it is necessary to adjust it promptly.
- Before the second start-up of the extrusion blow moulding equipment, it is necessary to clear the remaining material in the hopper or barrel to prevent blockage and reduce the resistance to start-up. Regularly inspect the bearings for wear.
- When replacing parts, maintain the original angle and parameters, for example, when replacing tools, pay attention to the gap between the moving and fixed tools. But if the recycled material is thin, the gap can be adjusted appropriately.
- Manufacturers should place the extrusion blow moulding equipment in a well-ventilated and dry location to ensure sufficient heat dissipation, prevent corrosion, and maintain good operational performance and a longer lifespan.
The extrusion blow moluding process has certain processing difficulties, and the manufacturer is developing a new technology to solve the problems encountered during the extrusion blow molding process.
Related News
Applied’s expertise in modifying materials at atomic levels and on an ihdustrial scaleenables our customers to transform possibilities into reality.