Home > Stretch Blow Moulding Equipment
Plastic Blow Molding
The application fields of plastic blow molding products are very wide, including but not limited to various industries such as food, medical, chemical, toys, automobiles, construction, electronics, agriculture, and daily necessities.
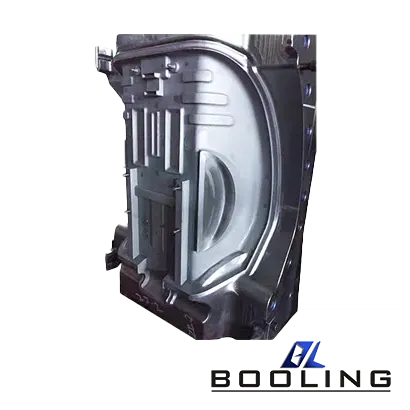
Stretch blow moulding is a hollow product with excellent longitudinal and radial strength formed by extruding or injecting a billet, adjusting the temperature stretching it longitudinally, and then blowing it radially with compressed air. Products manufactured through stretch blow molding technology can effectively improve the physical properties of plastics, with excellent strength, durability, and surface stiffness, involving multiple fields such as food packaging, personal care, industrial containers, and medical devices.
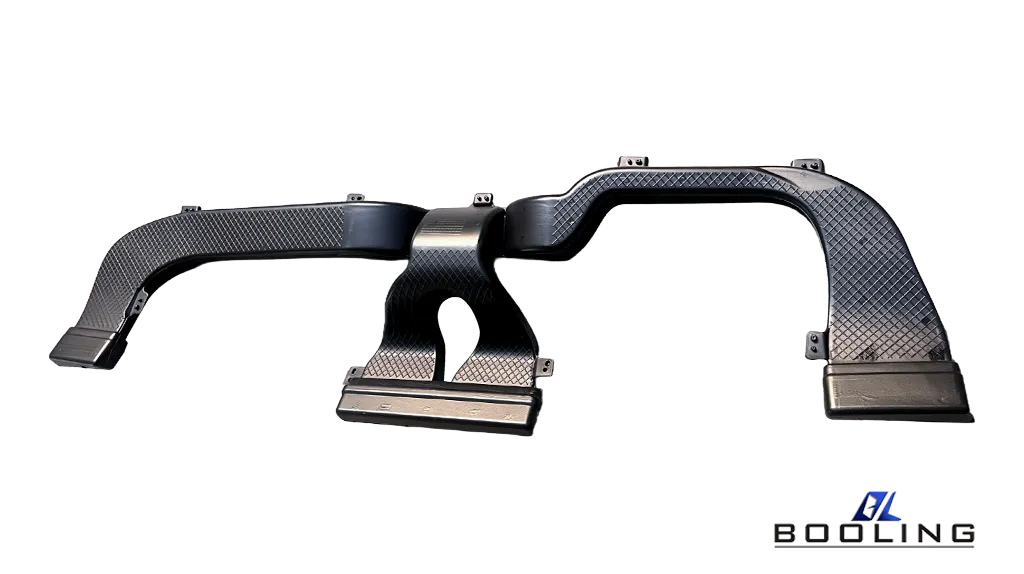
Key Points for Selecting Stretch Blow Moulding Machines
Manufacturers should consider various aspects when selecting stretch blow moulding equipment to provide better plastic blow molding services through the equipment.
- Manufacturers should choose between one-step or two-step injection stretch blow moulding hollow molding machines based on the blow molding market, their own factory buildings, funds, and other conditions. In general, the one-step method is suitable for processing products with a wide variety of products and small batches.
- When selecting heating methods, companies should prioritize those that are fast, evenly heated, and have good economic performance. If it is required that the billet can be uniformly heated in thickness and all directions during stretch blow moulding, a longer wavelength infrared heating method can be considered. For one-step stretch blow moulding, a heating core and heating tank can be used, and when heating near the inner and outer surfaces of the billet, ensure that it is in the center position. For two-step equipment, suppliers may consider using a heating method where the core shaft holding the billet rotates with the billet. Manufacturers can pre-set and strictly control the axial temperature distribution of the billet, and the axial temperature can even be set to 8 segments or more.
- When selecting a one-step injection stretch blow moulding hollow molding machine for processing, the manufacturer must consider whether the material is sufficiently dry, whether the cooling water and compressed air supply are running properly, and other aspects. If using a two-step injection stretch blow moulding hollow molding machine, it is also necessary to consider whether the billet conveying and other supporting equipment are reasonable.
- If the company chooses the one-step method for stretch blow moulding of hollow parts, the plasticization level, injection device, and injection volume must be balanced with each other; When selecting two-step equipment, the ability of the injection molding machine to process mold defects is matched with that of the blow molding machine.
- Manufacturers attach great importance to shortening the molding cycle and improving productivity, especially in cases where there are multiple cavities, stretch blow moulding equipment must have sufficient and effective heating and cooling equipment. Due to the influence of the hot runner on mold damage, the design of stretch blow moulding molds (hot runner, valve chamber gate, etc.) must strictly ensure the uniformity of each billet. For two-step injection stretch blow moulding hollow molding machines, shortening the heating time can effectively shorten the molding cycle, and the main measures at this time are to increase the heating rate and mold temperature.
- The injection device of the stretching blow moulding hollow forming equipment should consider adopting a linear reciprocating screw structure, equipped with appropriate screws and nozzles to ensure more uniform plasticization and reduce the risk of deformation or shrinkage of the small billet. When conducting PET bottle blow molding, manufacturers can effectively reduce viscosity loss by adopting a linear reciprocating screw structure (usually the compression ratio of PET bottles is around 2.3).
- During the blow molding process, the stretching speed, time, pressure, and blow molding rate all greatly affect the performance of the formed product. Manufacturers should consider the stretching stroke, stretching cylinder air intake, blow molding pressure, and blow molding time when selecting and debugging equipment.
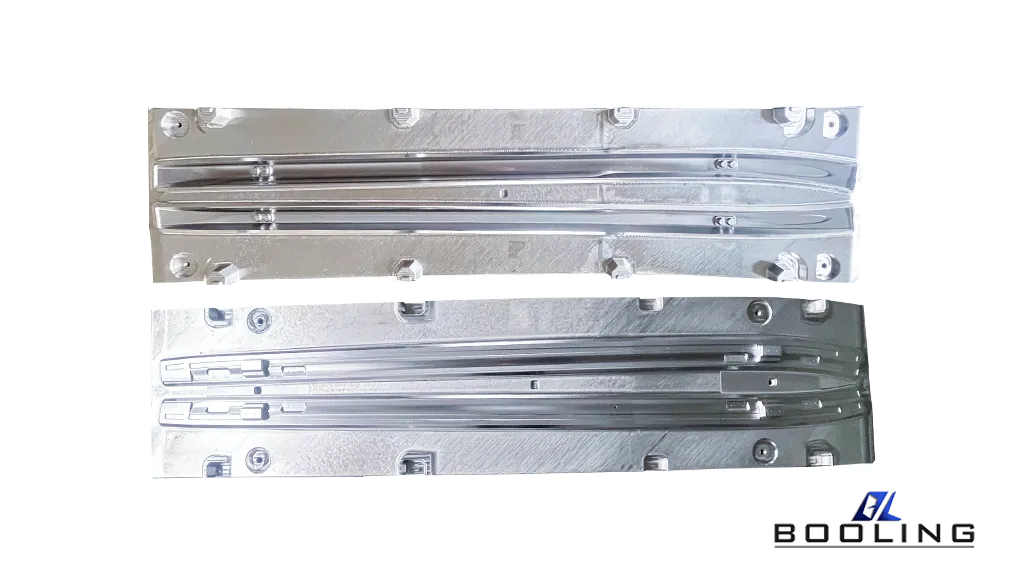
Safety Protection Mechanism of Stretch Blow Moulding Equipment
In general, manufacturers need to understand the safety protection measures of the equipment when carrying out stretch blow moulding processing. In case of accidents during processing, they can emergency stop and provide safety protection.
-Safety Alarm Device for Hydraulic System
- To ensure a more flexible and smooth coordination between various parts, an alarm will be triggered when the lubricating oil in the hydraulic system is insufficient.
- Insufficient hydraulic oil will also trigger an alarm, which can effectively prevent the impact of insufficient oil suction on the efficiency of hydraulic transmission.
- The alarm triggered by high hydraulic oil temperature is to prevent damage to various components of hydraulic transmission promptly, resulting in greater losses.
- The oil filter in the oil suction pipeline has an alarm for insufficient oil supply, which can prevent air from entering the hydraulic oil and affecting the hydraulic transmission work.
-Safety Door
During the production process of stretch blow moulding, operators often need to take parts and adjust or clean the molds between the opening and closing molds. To ensure the personal safety of blow molding operators and prevent accidental start-up of the mold during the mold opening and closing process from harming the operators, safety doors must be installed on the mold closing device for stretch blow moulding. The mold-closing action can only be carried out when the safety door is closed. If the safety door is opened or not fully closed, the mold-closing action cannot be carried out, and even during the mold-closing process, emergency braking will occur.
The travel switch restricts the action of the safety door. When the safety door is closed and the mold closing travel switch is pressed, the closing oil cylinder can work normally and start the injection action. The operator opens the safety door, resets the mold-closing travel switch, and cuts off the power. The travel switch should be installed in a concealed location to avoid accidental contact and accidents.
-Mold Protection Device
a mold is an important tool for stretch blow moulding, with a complex structure and manufacturing process. If there are problems or damages to the mold, it will not only affect the quality of plastic products but also make production impossible. Therefore, manufacturers should focus on protecting the safety of stretch blow moulding molds. To prevent collisions when the mold is closed when the mold is about to come into contact, the speed of the stroke should be appropriately slowed down until the mold contacts and touches the micro travel switch, to accelerate the speed. For example, in the process of low-pressure mold closing, if there are foreign objects between the two molds, high-pressure mold closing cannot be carried out to avoid damaging the mold.
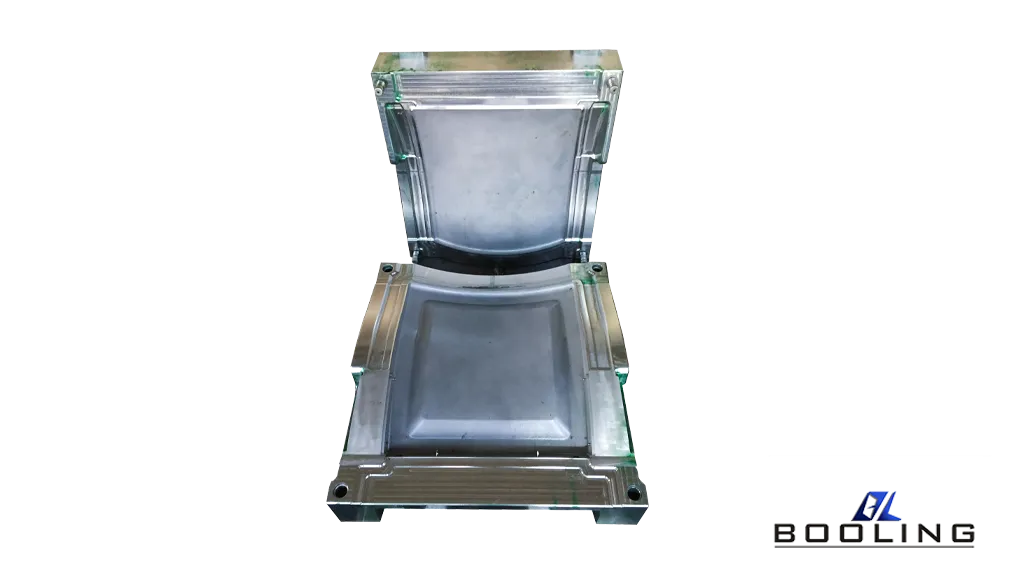
Installation and Maintenance of Stretch Blow Moulding Equipment
The installation and maintenance of stretch blow moulding equipment require manufacturers to have a wealth of professional knowledge and practical experience to lay a good foundation for subsequent stretch blow moulding processing.
-Installation
- When installing stretch blow moulding equipment, the cooling water interface should have sufficient flow and pressure. Cold water pipes used for cooling molds should be coated with insulation materials.
- To ensure smooth operation of the machine, the level should be adjusted during installation. For two-step equipment, the entire assembly line should be considered, and supporting equipment such as billet making, conveying, secondary heating, stretching and blow moulding processing, labeling and packaging, and product collection should be reasonably arranged.
- The workshop where stretching and blow moulding equipment is installed must be kept clean, ventilated, and dry. After the machine is determined, the foundation leveling and bearing capacity should be measured.
- At the same time, the auxiliary equipment of the machine is also crucial, including material drying devices, air compressors, and refrigeration equipment.
-Maintenance
- Regularly inspect and add lubricating oil to all parts of the stretch blow moulding equipment, especially the transmission parts with significant wear. At the same time, it is necessary to regularly inspect the three major components of the pneumatic system, namely the water filter, pressure-reducing valve, and oil mist collector, drain water promptly, and add lubricating oil.
- Manufacturers should keep the machine clean and the environment tidy. Especially after processing hard PVC materials, it is necessary to clean the stretching and blow moulding machine barrel and screw promptly. During shutdown or storage, anti-rust treatment should be applied to the stretch blow moulding mold, such as attaching a layer of anti-rust oil.
- The hydraulic oil cooler should be regularly cleaned with trichloroethane solution or carbon tetrachloride solution to improve its heat exchange rate and ensure that the hydraulic oil operates at normal temperatures.
- Regularly check the liquid level of the hydraulic system oil tank and replace the hydraulic oil regularly.
The advantages of stretch blow moulding are extremely prominent, including its ability to effectively alter the physical properties of plastic materials and manufacture products with higher transparency. Many domestic manufacturers of stretch blow moulding products have exported their products to many countries such as India, the United States, Nigeria, and Spain. However, there are also many limitations to stretch blow moulding, so manufacturers need to consider comprehensively when choosing manufacturing methods and equipment, and provide more comprehensive blow molding services.
Related News
Applied’s expertise in modifying materials at atomic levels and on an ihdustrial scaleenables our customers to transform possibilities into reality.