Home > Application of PE Material by Blow Mold Manufacturers
HDPE Blow Molding
During the production process, HDPE blow molded products demonstrate their unique advantages, such as high rigidity, low temperature resistance, and stress cracking resistance, making them ideal materials for packaging and plastic container manufacturing.
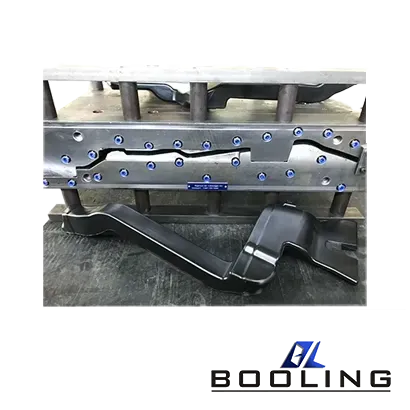
When blow mold manufacturers choose PE as a plastic raw material for production and application in fields such as automobiles and electronics, they should pay attention to its properties. The full name of PE material is polyethylene, which is the simplest type of molecular structure in resins. Unlike HDPE blow molding, PE blow molding is colorless, odorless, non-toxic, and has superior electrical insulation and chemical stability.
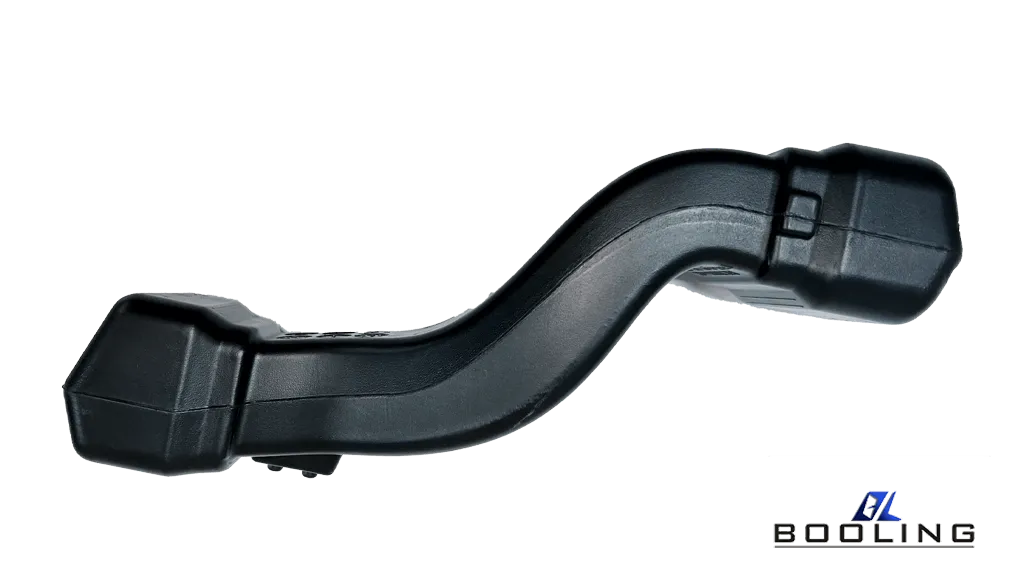
Classification and Basis of PE Materials
Before processing PE materials, blow mold manufacturers need to classify the materials. Polyethylene materials can be classified into the following categories due to differences in polymerization methods, conditions, and densities:
- Low-density Polyethylene (LDPE)
This type of polyethylene material is also known as high-pressure polyethylene because it is usually produced by high-pressure methods (14.17-196.2 MPa). The polyethylene produced by this method contains a large number of long and short branched chains in its molecular chain, with an average of 21 branched chains per 1000 carbon chain atoms. Therefore, LDPE has a lower density, lower crystallinity, lighter weight, greater flexibility, and better impact resistance, making it suitable for production in low-temperature environments. Blow mold manufacturers widely use LDPE in the production of pipes, films, synthetic leather, cable insulation, and sheaths.
- High-density Polyethylene (HDPE)
HDPE is mainly produced under low pressure, hence it is also known as low-pressure polyethylene. HDPE molecules have fewer branches and higher crystallinity, generally reaching 85%~95%, so their density is also high. Blow mold manufacturers generally use higher temperatures to process them, which have good hardness, tensile strength, and corrosion resistance, and can resist strong acid and alkali erosion. Suitable for various products such as hollow blow molding, injection molding, and extrusion.
- Ultra Low-Density Low Polyethylene (ULDPE)
A new fourth-generation linear structural resin formed by copolymerization of ethylene and polar monomers such as ethyl acetate or acrylic acid. The minimum density of this copolymer resin can reach 0.912g/cm3. Due to its lower density, it has a softness and toughness that other PE resins do not have, but at the same time, it also possesses the physical and thermal properties of high-density linear polyethylene. Blow mold manufacturers typically use ultra-low-density polyethylene to make stretch films and various hoses.
- Ultra-high Molecular Weight Polyethylene (UHMW-PE)
Ultra-high molecular weight polyethylene (UHMW-PE) is a linear structure of polyethylene and a thermoplastic engineering plastic with excellent comprehensive properties. It is a polymer compound with low viscosity and poor fluidity in its molten state, making it difficult for blow mold manufacturers to process it using conventional methods. Therefore, current blow mold manufacturers usually use extrusion, blow molding, or injection molding methods to process it. The main chain of UHMW-PE is long and entangled with each other, resulting in low crystallinity and density. In addition to being difficult to process, ultra-high molecular weight polyethylene also has disadvantages such as low surface hardness, low hot deformation temperature, poor bending strength, and poor creep performance. However, it has low friction and good crack resistance and can withstand extreme weather changes. UHMW-PE has a low shear rate and is generally not suitable for processing with thermoplastic materials. Blow mold
manufacturers can use processes such as cold pressing sintering or injection molding for processing.
- Linear Low-density Polyethylene (LLDPE)
Linear low-density polyethylene is different from general low-density polyethylene in that it has no long branched chains, is non-toxic and odorless, and appears in a milky white granular form. This is a new type of polyethylene developed by blow mold manufacturers in recent years, which has rapidly developed in the industry. LLDPE is polymerized under the combined action of a low-pressure method and highly active chemical agents, and the polymerization method is the same as HDPE. Therefore, its molecular structure is the same as HDPE, in a straight chain shape. Compared with LDPE, LLDPE has a higher softening temperature and melting temperature, and its physical and chemical properties are relatively good. It can resist extreme weather and has better crack resistance and impact resistance. Blow mold manufacturers usually use it to manufacture agricultural films, transparent films, and shrink films.
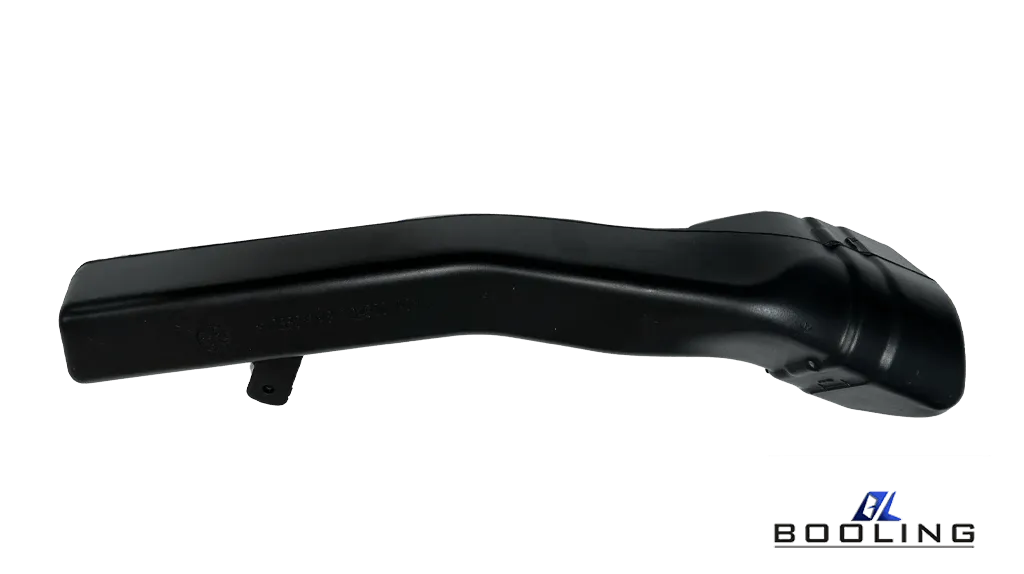
Characteristics of PE Materials
Blow mold manufacturers need to have an understanding of the characteristics of polyethylene to apply it correctly and appropriately.
The crystallization ability of PE material is good, but it is greatly affected by the mold temperature. If the mold temperature is high, the cooling rate of the solution will slow down, and the crystallinity of the plastic part will increase, thereby improving the overall strength of the blow-molded part.
- The molecular chain of PE material is flexible and the intermolecular interaction force is small, so it often does not require too high pressure when processed by blow mold manufacturers.
- Although the melting point of PE is not high, it has a higher specific heat capacity, so the material still needs to consume more heat during processing and plasticization.
- Therefore, blow mold manufacturers need to install plasticizing devices with higher heating power when designing.
- PE materials have outstanding thermal stability, and under normal circumstances, temperatures above 300 ℃ will cause decomposition, resulting in extremely excellent heat resistance.
- PE is a crystalline raw material with extremely low moisture absorption and moisture content, so blow molding mold manufacturers do not need to undergo drying treatment before processing.
- The cooling and solidification speed of PE melt is relatively slow, so if you want to fully cool, blow molding mold manufacturers should design a better cooling system for the mold.
- The forming temperature range of PE is wide, generally between 200 ℃ and 250 ℃, and a slight fluctuation in temperature has little effect on the forming of blow-molded parts when PE is in a molten state.
- When PE material is subjected to blow molding processing, the shrinkage rate is relatively high and has obvious directionality. The LDPE shrinkage rate is about 1.22%, and the HDPE shrinkage rate is about 1.5%. Therefore, PE material is prone to deformation, warping, and shrinkage defects. Therefore, blow molding mold manufacturers should maintain a uniform and stable molding temperature during processing, and not easily change it under normal conditions to prevent the occurrence of these defects.
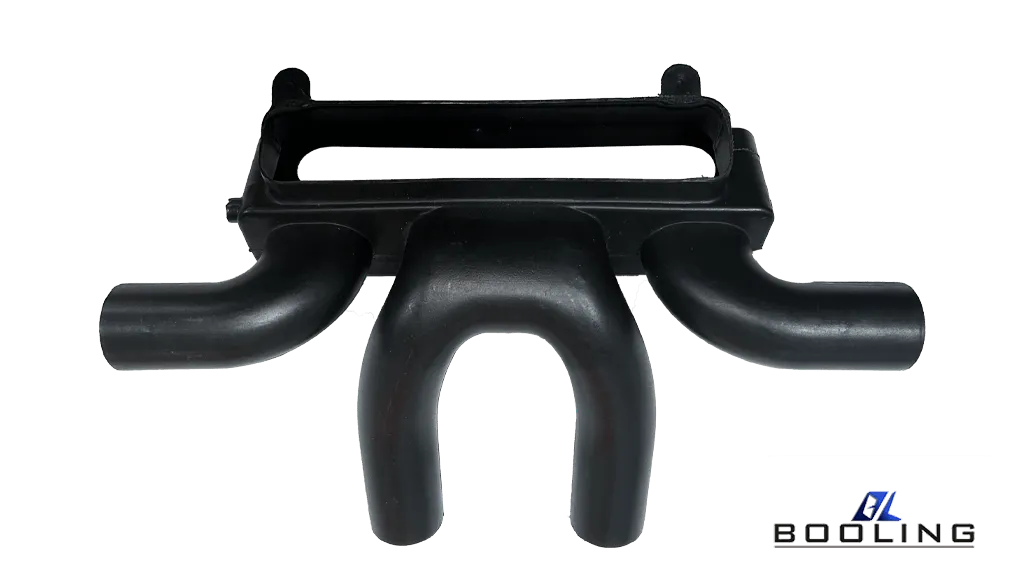
Blow Molding Process of PE
When blow mold manufacturers process and treat PE materials, they mainly consider the following key points:
- Extruder Temperature
When blow molding mold manufacturers process low-density polyethylene (LDPE), the temperature of the extrusion blow molding machine is generally controlled at around 160 ℃~170 ℃, and the temperature of the machine head must be uniform and stable. If the temperature is too high, it will cause the decomposition of the PE resin material and a decrease in physical properties; If the temperature is too low, it can lead to incomplete plasticization of the material, uneven blow molding expansion, low tensile strength of blow molded parts, rough surface, low smoothness, and even defects such as water ripples, affecting the aesthetics.
- Inflation Ratio
When blow molding mold manufacturers use PE material to blow mold thin films, the blow expansion ratio is one of the most critical processes. The so-called inflation ratio refers to the ratio of the diameter of the product to the diameter of the billet. An increase in the blowing ratio means that the lateral strength of the film will be improved. However, if the inflation ratio is too large, it can cause unstable film quality and easily lead to wrinkles. Therefore, the inflation ratio should be coordinated with the traction ratio. Blow molding mold manufacturers generally control the blow expansion ratio of low-density polyethylene (LDPE) films to around 2.5-3.0.
- Traction Ratio
The traction ratio is the ratio between the traction speed of the film and the extrusion speed of the pipe ring. The traction ratio is different from the inflation ratio, as it is the longitudinal stretching ratio, which gives the PE film a directional effect in the direction of extraction. If blow molding mold manufacturers increase the traction ratio, it may increase the longitudinal strength of the blow-molded parts, and the thickness of the film will also become thinner. However, if the traction ratio is too large, it will make it difficult to control the thickness of the film, become too thin, and cause the film to rupture.
- Dew Point
The dew point of blow molding, also known as the frost line, is the boundary between the viscous flow state and the high elastic state of plastic. During the blowing process of blow molding mold manufacturers, low-density polyethylene (LDPE) is extruded from the mold mouth in a molten state, at which point the material has good transparency. After the material leaves the mold mouth, it needs to be cooled through the cooling air ring of the mold to cool the expansion area of the film bubble. On blow-molded film bubbles, manufacturers usually see a boundary between transparency and blurriness, which is the dew point (frost line). During the blowing process of the manufacturer, the dew point to some extent affects the performance of the blown film. For example, if the dew point is higher and located above the blown film bubble, the blowing of the film is carried out in the liquid state, and the blowing only thins the film without the molecules being stretched. On the contrary, if the dew point is relatively low, inflation occurs in the solid state. At this time, the plastic is in a highly elastic state, and the inflation is like transverse stretching, causing the molecules to undergo orientation.
Related News
Applied’s expertise in modifying materials at atomic levels and on an ihdustrial scaleenables our customers to transform possibilities into reality.