Home > Automotive Checking Fixture Testing Guideline
Automotive Checking Fixture Testing Guideline
Fixture Testing
Details
Details:
Model
Material
Brand
Origin
Application
Booling-Fixture-1
Metal
Booling
China
Aerospace, Automotive, Medical, Tooling
Automobile fixture testing is a device used to testing whether the size and accuracy requirements of automobile parts or molds meet the requirements, which can greatly improve the safety performance and reliability of automobile parts.
Advantages of Fixture Testing:
- Comprehensive Testing
- Product Performance Analysis
- Reduced Field Failures and Warranty Claims
- Streamlined Production Process
- Repeatability and Consistency
Related Hot Products
There are many roles for the automotive checking fixture in the machining industry, as fixture testing has a wide range of uses and various performance characteristics. They are specialized tools that can be continuously used. It can also be divided into multiple different types, such as a stamping single item checking fixture, part assembly checking fixture, and combination checking fixture, according to the detection object.
Advantages of Automotive Checking Fixture
Due to the unique advantages and performance of the checking fixture, they have been widely used in the automotive field, such as:
In the production of automobiles, the main function of checking fixtures is to be able to inspect automotive parts. Under the action of checking fixtures, manufacturers use visual checking or measuring instruments to inspect holes of different properties on automotive parts and calipers to inspect multiple parts such as the parts and their surroundings. In addition, the car checking fixture can also detect the connection position between parts, ensuring that the parts maintain good quality during trial production or production start-up. Manufacturers can judge the quality and usability of parts based on the testing data provided by the checking fixture, and make timely corrections.
Another key function of the automotive checking fixture is to measure some functional dimensions of automotive components. Manufacturers can also use checking fixtures for numerical testing when needed. Many parts cannot be measured using certain tools, but specific values can be measured using a coordinate measuring machine. Therefore, manufacturers will use this to support the parts and use inspection fixtures as measuring brackets.
In the production of automotive parts, the checking fixture plays a crucial role in the quality checking of the parts and plays a decisive role in determining their performance.
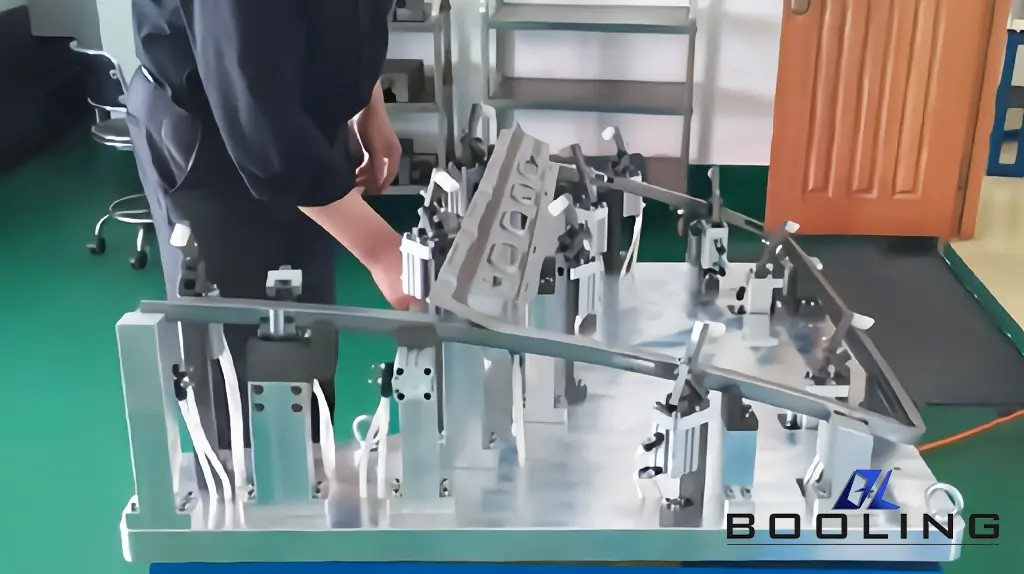
Design of the Automotive Checking Fixture
For the design of the automotive checking fixture, manufacturers need to consider precision, material selection, and the structural requirements for the actual use of the checking fixture.
- Manufacturing accuracy requirements for the automotive checking fixture
- Manufacturing accuracy: The manufacturing accuracy of automotive checking fixtures should meet relevant standards and customer needs. Manufacturers should manufacture the automotive checking fixture to ensure the accuracy of the final measurement results.
- Error assessment: Automotive checking fixtures require high precision, so their errors should also be controlled within a small range. In actual manufacturing and use, it mainly depends on the customer’s requirements and the accuracy of the product.
- Selection of materials for the automotive checking fixture
- Tensile strength: The automotive checking fixture should have durability, so the materials selected by manufacturers should ensure high tensile strength.
- Corrosion resistance: The requirement for the automotive checking fixture is to be able to be reused in various environments, and the manufacturing materials should have good chemical properties and be able to withstand corrosion from various reagents.
- Hardness requirement: The use of the automotive checking fixture may be frequent. To ensure their quality, the manufacturing materials selected by the manufacturer should have sufficient hardness to prevent deformation and damage during the checking process.
- Types and structural requirements of the automotive checking fixture
- Classified by purpose: The Automotive checking fixture can be mainly divided into shape and position tolerance checking fixtures, dimension checking fixtures, specialized checking fixtures, etc.
- Structural requirements: The purpose of making the automotive checking fixture is to ensure the accuracy and precision of parts, so checking fixtures need to have a stable structure and allow manufacturers to perform daily cleaning, maintenance, and disassembly.
- Design Basis for the Automotive Checking Fixture
The design and actual use of the automotive checking fixture should comply with the requirements of the manufacturing quality system, ensuring that the design of inspection fixtures is reasonable, safe to use, highly accurate, and easy to maintain.
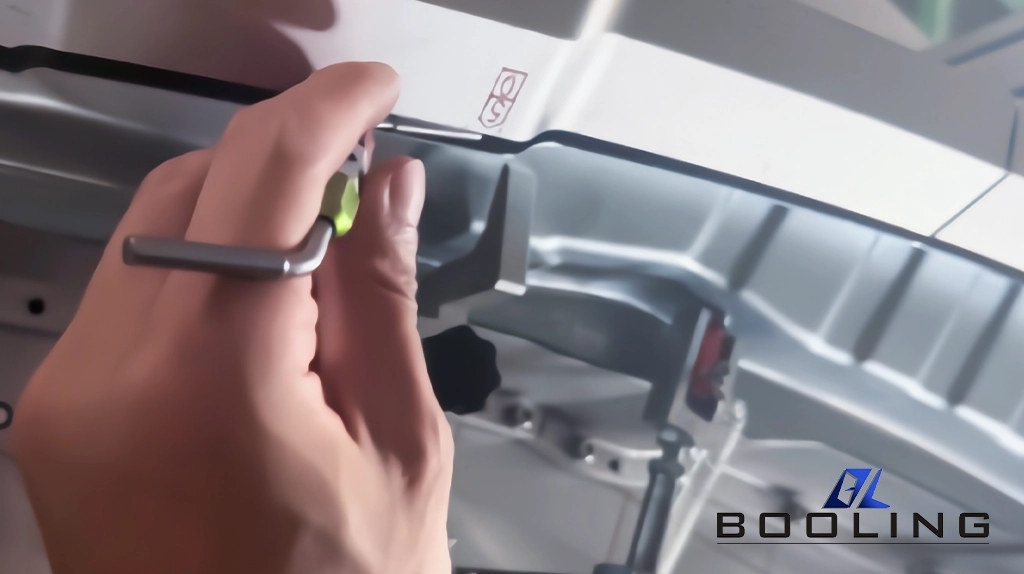
Automotive Checking Fixture Standard
Before officially using the automotive checking fixture, the operator needs to understand the checking fixture required for this checking work in advance, refer to the checking fixture operation manual in detail, and focus on understanding the positioning, clamping, checking, and loading/unloading of the checking fixture. For complex checking fixtures, operators need to undergo specialized training before using the checking fixtures.
For resin-based interior and exterior inspection fixtures, the strength of individual automotive checking fixtures is poor. Manufacturers are prohibited from hammering or lifting them during installation or disassembly to prevent damage to the structure of the checking fixture. The flange part of the checking fixture has low strength and is easily damaged when used improperly or violently, so manufacturers need to be cautious when installing glass or sealing strips on the checking fixture and pay extra attention to ensure their quality. In addition, manufacturers should handle metal components with care when installing them to avoid scratching or damaging checking fixtures. Before officially putting the automotive checking fixture into use, manufacturers need to conduct self-checking of the status of the checking fixtures, mainly include following standards:
- Check if the car checking fixture is kept clean and free of impurities such as iron filings, especially the measuring reference surface or moving parts, which can easily scratch the checking fixture.
- Manufacturers need to check whether the anti-loss links are secure and whether the checking pins are complete.
- Check whether the positioning device is effective and whether the guiding part can operate normally.
- Check if there is any shaking phenomenon in the clamping device, and if so, adjust it promptly to prevent damage to the mold and components.
- Check whether the cutting edge is damaged by collision and whether the section template device is loose.
- The working surface of the car checking fixture determines the accuracy of the checking, and the manufacturer needs to confirm whether there is any damage.
- Check if the markings on the car checking fixture are intact, clear, and free of stains.
- Daily wipe and inspect the measuring surface of the fixture to avoid dirt affecting measurement accuracy, and check whether the certificate label of the fixture is within the validity period of the calibration.
- Conditional manufacturers can use extreme samples to verify the accuracy of the checking fixture before use, ensuring that it maintains optimal performance. The inspection fixtures must pass the manufacturer’s self-checking before they can be put into use.
The automotive single-piece checking fixture is a tool used to measure certain parts during the production process of parts, while the assembly checking fixture is a tool that can be used for measuring certain parts during the production process of parts and for measuring finished parts. Car checking fixture is a precision mechanical manufacturing equipment. Due to the specialized nature of the checking fixture, it is a high-tech precision testing equipment that requires high precision and high surface quality for products.
Related News
Applied’s expertise in modifying materials at atomic levels and on an ihdustrial scaleenables our customers to transform possibilities into reality.