Household Molds
The household molds produced by BOOLING mainly include storage products, kitchen and bathroom products, furniture and other products, and our engineers mainly manufacture them through injection molding, blow molding, extrusion, die-casting or forging, smelting, stamping and other processes to meet the needs of different users.
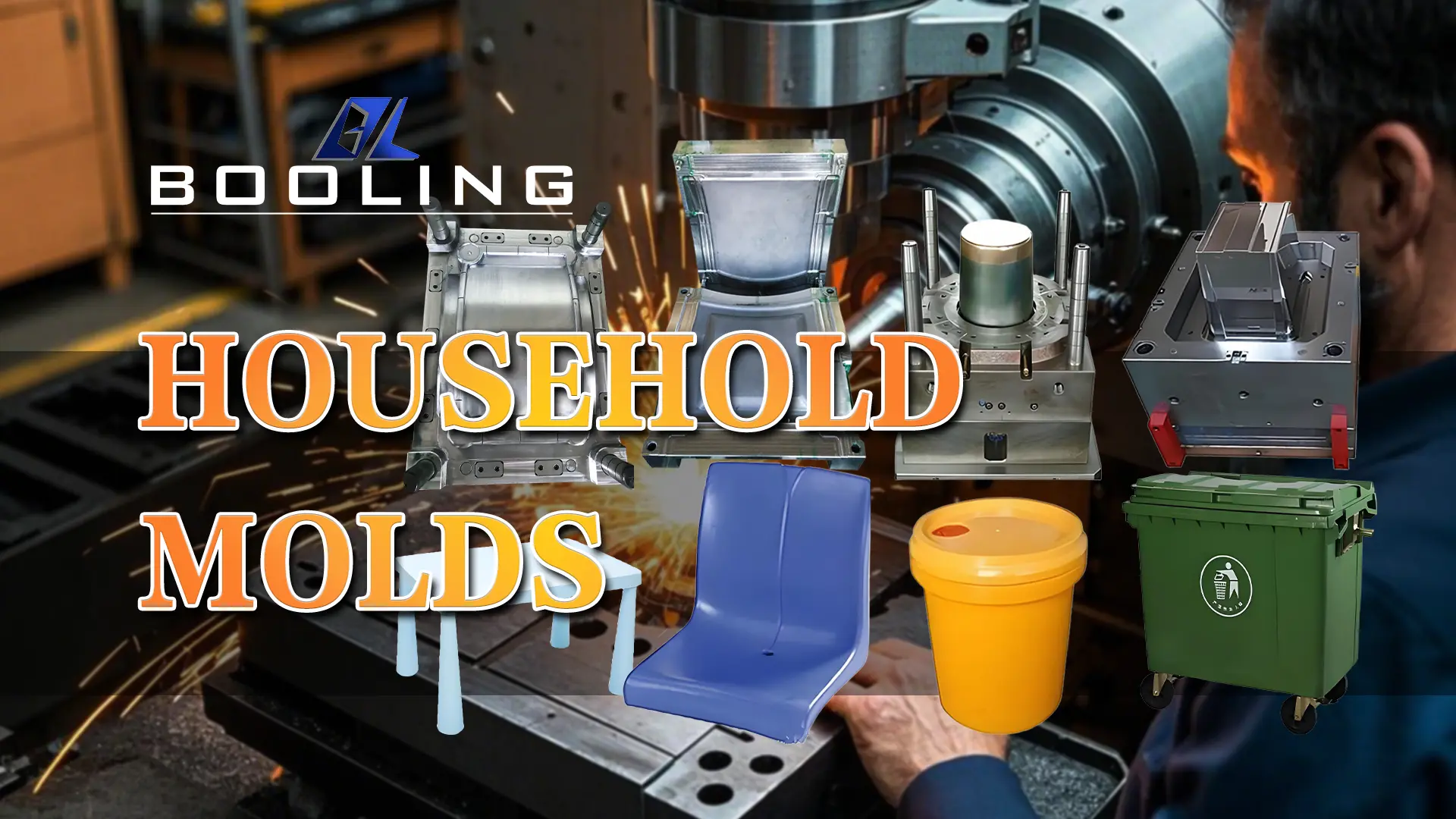
About Household Molds
There are many types of household mold, which can be divided into injection molds and blow molds. The household goods molds produced by BOOLING mainly adopt the current mainstream molding technology. Many engineers strictly control the product quality and precision to ensure that the products produced maintain long-term stability and durability in appearance.
If you are not sure how to design drawings or manufacture your products, you can contact our engineers and we will provide you with the best molding solutions.
The dustbin mold determines the shape and function of the dustbin. Booling can improve the molding rate of the dustbin mold through hot runner injection molding technology to ensure the size and precision of the product. This type of dustbin is used in public places, offices, and other scenes.
Booling chair mold is designed with a hot runner injection system and high-hardness mold steel for durability. The chairs produced are suitable for various scenarios, such as offices, restaurants, outdoor camping, cafes, schools, etc. They can adapt to extreme weather changes, will not easily age and become brittle, and have a long service life.
Bucket mold involves multiple aspects of technology, including process parameter analysis, injection molding machine selection, etc. Booling Bucket mold mainly uses grinders, drilling machines, CNC, EDM, high-speed finishing, deep hole drilling, wire cutting, and other technologies to ensure the accuracy of the bucket mold.
Table molds are mainly made of high-strength steel or other metals. Our engineers will accurately design the shape of the table according to the appearance structure and size required by the user.
Booling’s plastic washbasin mold uses fan-shaped or side gates to ensure that the melt can be evenly dispersed inside the mold to obtain a product with uniform wall thickness.
The kitchenware mold can be made of various materials, such as various thermoplastics and silicone, to meet the life needs of different users. Booling uses advanced five-axis machining technology to reduce the wear of the tool during the machining process and can cut in a more flexible way to improve machining accuracy.
Manufacturing Process of Household Mold
Booling has rich manufacturing experience in household mold manufacturing. Our engineers can reverse design the samples according to the customers’ provided samples and ensure that each mold meets the customers’ specific needs through advanced analysis software and precision processing equipment.
Injection molding is a cutting-edge manufacturing process that involves injecting molten material, typically thermoplastics or thermosetting polymers, into a carefully crafted mold cavity. This cavity, created using advanced CAD/CAM software and precision machining techniques, serves as a blueprint for the final product.
BOOLING 3D printing service mainly provides customized services for industries such as medical models, aerospace, and automotive parts design and manufacturing. The main types of 3D printing technology are FDM, SLA, SLS, DLP, binder spraying, material spraying, DMLS, SLM, electron beam melting, and LOM.
We conduct DMF technical analysis for customers based on product design, and with the professional technical support of our team, propose reasonable solutions before mold making. Booling blow molded products are more prone to shedding burrs, greatly improving production efficiency and facilitating workers to operate during stretching and blow molding processes in the workshop manufacture.
A checking fixture in the automotive industry is a precision tool used to inspect and verify the concentricity, runout, and other dimensional standards of components, ensuring they meet the required specifications through various types of inspection and testing methods.
Booling’s 3D blow molding is mainly used in air ducts around automobile engines. It has the outstanding advantages of seamless welding and uniform wall thickness.
BOOLING Stamping Die specializes in the design and manufacture of precision progressive dies for automotive sheet metal punching and bending applications. Our expert team offers comprehensive services from prototype development to final press-ready tooling, ensuring high-quality cutting and forming solutions for even the most complex stamped parts.
FAQs about Household Mold
Household Mold Product Types
There are many types of household products produced using mold, mainly including:
1. Home Furnishing Storage: Plastic Storage Baskets, Hangers, Shoe Racks, Drawers, etc.;
2. Kitchen Home Furnishings: Dishwashers, Tableware, Bowls, Baskets, Trash Cans, Storage Boxes, Boxes, etc.;
3. Bathroom Supplies: Laundry Baskets, Buckets, Bathtubs, Storage Racks, Baskets, etc.;
4. Furniture: Chairs, Tables, Stools, etc.
Quality Control of Household Goods Mold
During the processing, Booling pays great attention to the quality control of molds.
1. Three-coordinate Measuring Machine
Booling’s coordinate measuring machine can measure the dimensions of all types of household injection mold parts. It can measure flatness, concentricity, roundness, etc.
2. Checking Fixture
-Processing Materials:
1) Steel: low carbon steel/Q235/20#/45#, etc.
2) Stainless steel: 301, 302, 303, 304, 316, 420, 430, etc.
3) Aluminum: 6061, 6063, 7075, 5052, etc.
4) Brass/copper/bronze/etc.
5) Plastic: ABS, PP, PE, PC, Delrin, acrylic, etc.
-Testing Machine: coordinate measuring machine, micrometer, caliper, etc.
-Accuracy
1) Surface Roughness: Ra0.4 (no need for polishing or grinding)
2) CNC Machining: ±0.005
3) Turning: ±0.005
4) Grinding: ±0.003
5) Wire Cutting: ±0.002
6) Inner diameter/outer diameter grinding: ±0.002
-Process: stamping, deep drawing, laser cutting, bending, welding, CNC, etc.
Advantages of Booling Household Mold
Booling has engineers with 20+ years of experience in household mold, providing customers with reasonable mold prices to obtain lower home product production costs while providing complete machine parameters for production services.
1. Use the product’s 3D printing service to help customers check whether the product design needs to be optimized.
2. The feasibility of product molding will be analyzed in advance before mold opening, such as demoulding slope, strength, deformation, ejection, etc.
3. The mold processing steps are divided into three steps: rough machining, semi-finishing, and finishing. According to the customer’s requirements for product precision, adopt appropriate processing technology to ensure the market demand and market value of the product.
4. The mold production has a high level of automation and a short production cycle. The mold is developed quickly according to customer needs to seize the market opportunity for customers.
5. Spare parts for vulnerable parts of the mold are prepared for customers at any time so that users can rest assured in subsequent production.
6. Debug suitable processing parameters for customers in advance, such as:
1). Mold Temperature: 60~80℃
2). Barrel Temperature:
· Front Section: 220~260℃
· Middle Section: 290~310℃
· Back Section: 300~320℃
· Nozzle: 290~300℃
3). Injection Pressure: 60~70Mpa
4). Injection Speed: customized
5). Injection Time: depends on the size of the plastic product. The best injection time should be when the molten plastic fills the mold and the surface is cooled and shaped.
Which countries are BOOLING's household Mold currently used in?
Booling has engineers with 20+ years of experience in household mold, providing customers with reasonable mold prices to obtain lower home product production costs while providing complete machine parameters for production services.
1. Use the product’s 3D printing service to help customers check whether the product design needs to be optimized.
2. The feasibility of product molding will be analyzed in advance before mold opening, such as demoulding slope, strength, deformation, ejection, etc.
3. The mold processing steps are divided into three steps: rough machining, semi-finishing, and finishing. According to the customer’s requirements for product precision, adopt appropriate processing technology to ensure the market demand and market value of the product.
4. The mold production has a high level of automation and a short production cycle. The mold is developed quickly according to customer needs to seize the market opportunity for customers.
5. Spare parts for vulnerable parts of the mold are prepared for customers at any time so that users can rest assured in subsequent production.
6. Debug suitable processing parameters for customers in advance, such as:
1). Mold Temperature: 60~80℃
2). Barrel Temperature:
· Front Section: 220~260℃
· Middle Section: 290~310℃
· Back Section: 300~320℃
· Nozzle: 290~300℃
3). Injection Pressure: 60~70Mpa
4). Injection Speed: customized
5). Injection Time: depends on the size of the plastic product. The best injection time should be when the molten plastic fills the mold and the surface is cooled and shaped.