Home > Injection Molding > EVA Injection Molding
Booling’s EVA injection molding products are soft, non-toxic, and environmentally friendly. They are produced through injection molding machines and molds and are integrated into the process of melting, injection molding, pressure holding, cooling, and solidification. We provide automated EVA injection molding solutions for manufacturers of products such as footwear, children’s toys, packaging, waterproof rolls, and medical devices.
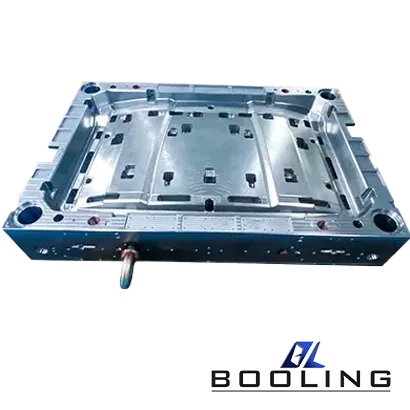
Booling injection molding is to mix EVA materials and foaming agents, and inject them into the mold cavity through an injection molding device for rapid molding.
- Melt Index
- Acetic Acid Content
EVA Injection Molding Capabilities
EVA has excellent moldability and can maintain good fluidity during injection molding to achieve rapid molding.
·
US
Metric
EVA with Ethyl Acetate below 5%
1500mm x 1300mm x 450mm
59 in. x 51.2 in. x 17.7 in.
Ethyl Acetate in 5%~10% EVA
59 in. x 51.2 in. x 17.7 in.
1500mm x 1300mm x 450mm
Ethyl Acetate at 20%~28% EVA
59 in. x 51.2 in. x 17.7 in.
1500mm x 1300mm x 450mm
EVA with Ethyl Acetate Higher than 30%
59 in. x 51.2 in. x 17.7 in.
1500mm x 1300mm x 450mm
*EVA injection molding can also be precisely customized.
EVA Injection Molding Material
EVA is a copolymer of ethylene and vinyl acetate. It has good flexibility and elasticity, excellent processing performance, and can achieve lightweight production.
Material
- EVA
The Advantage of EVA Injection Molding
Ethylene acetate polymer has unique properties and has been widely used in various industries in combination with injection molding.
- It has excellent chemical properties and can withstand the effects of acids, alkalis and solvents
- It can resist the effects of ultraviolet rays, radiation, and ozone, maintain structural integrity in harsh environments, and is durable
- EVA is flexible and impact-resistant. Its special copolymer molecular structure can easily bend the material without affecting its overall performance, making it an ideal application material for applications that require impact resistance or deformation
- It has processing versatility and can be easily processed using various technologies
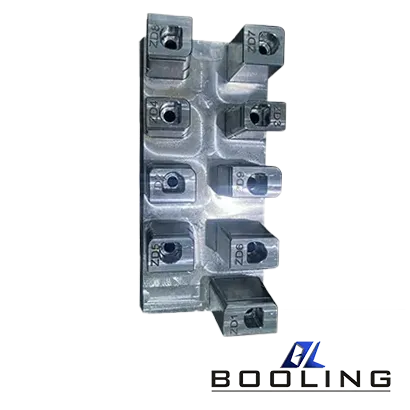
Application of EVA Injection Molding
EVA injection molding is widely chosen by manufacturers in the automotive, footwear, construction, packaging, medical, and other industries due to its excellent durability and performance, increasing the diversity of product creation.
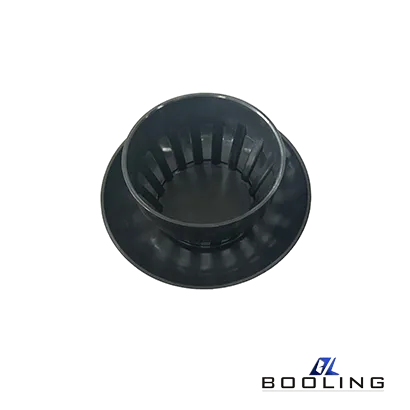
Guidelines for EVA Injection Molding
As a professional polymer molding process, EVA injection molding is suitable for product processing with high requirements for dimensional accuracy and surface smoothness.
The versatility of EVA injection molding technology comes from the copolymerization of monomers ethylene and vinyl acetate, which has better flexibility and elasticity and is used in hot melt adhesives, foaming materials, and various insulation materials. Booling meets the processing requirements of different EVA products by adjusting the internal vinyl acetate content.
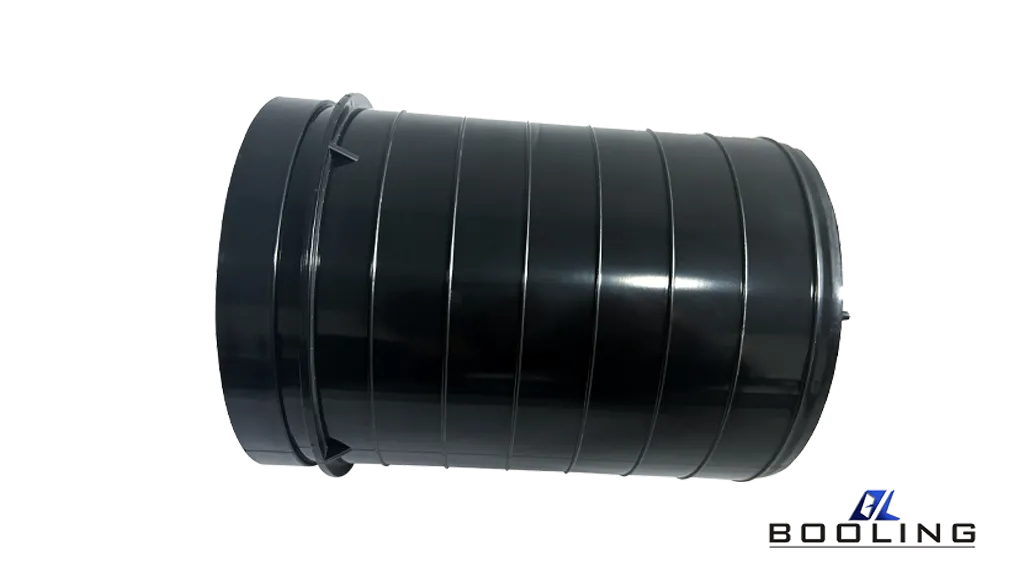
Composition of EVA Injection Molding Materials
EVA and ethylene-vinyl acetate polymers are widely used in the production of foam products.
- Main ingredients: composed of ethylene and vinyl acetate. The performance of the final product is determined by the content of vinyl acetate. For example, a content of 5% to 40% is suitable for the processing of films and hot melt adhesives, 40% to 70% is suitable for rubber materials with high elasticity, and 70% to 95% is suitable for the processing of various coatings.
- Additives: Improve overall performance by adding foaming agents and fillers.
EVA Injection Molding Process
EVA injection molding is a widely used plastic processing technology. The polymer is melted and injected into the mold cavity at a certain pressure and temperature. After cooling and solidification, EVA products are formed.
- Material preparation: After the EVA particles are dried and the impurities are screened out, the adverse effects such as bubbles caused by excessive moisture content in the subsequent processing can be avoided. If recycled materials are used, they need to be crushed
- Mold preparation: The mold is usually made of high-strength aluminum and steel. The design of the mold cavity needs to consider the size and size of the final structure to ensure the shape is accurate
- Melt plasticization: The processed EVA material is sent to the barrel of the injection molding machine for heating and plasticization. The friction and shear force applied by the screw can ensure that the material is always in the viscosity required for processing
- Cooling: After the mold cavity is filled, the molten material is cooled, exhausted, and solidified. The cooling water channel designed by Booling can achieve more efficient heat transfer
- Demolding: Through the design of appropriate draft angles, the friction between the finished product and the mold is reduced, which is convenient for demolding. When designing the parting surface, avoid designs that are too thin or have sharp corners to avoid damage to the product during demoulding.
How to Control the Quality of EVA Injection Molding?
The quality of EVA injection molding products tests the manufacturer’s product manufacturing accuracy and the level of mold making. Booling ensures the smooth operation of the mold and the processing level of the product by carefully monitoring and optimizing each production stage.
- Material Evaluation
Through a series of evaluations and optimizations of raw materials, verify whether their specifications meet the processing requirements. Including testing of material size, weight, operating temperature range, composition, and performance, this step can reduce the risk of defects in the final product
- Process Monitoring
During the entire processing process, by closely monitoring and constantly adjusting various parameters, maintain optimal processing conditions such as temperature, pressure, and time
- Dimension and Performance Inspection
After injection molding is completed, we will conduct a comprehensive quality inspection of the EVA finished product, including size, structural rationality, and performance, tolerance, etc., using coordinate measuring machines and optical inspection systems to detect the slightest deviation.