Home > Injection Molding > Polycarbonate Injection Molding
Polycarbonate injection molding products have high transparency and good impact toughness, using the technology of integrated molding of molds and injection molding machines, polycarbonate materials undergo melting, injection molding, pressure holding, cooling, curing, and other processes to form products with high transparency. Booling provides complete automated production solutions for manufacturers of lighting equipment, microscopes, lamps, and other products.
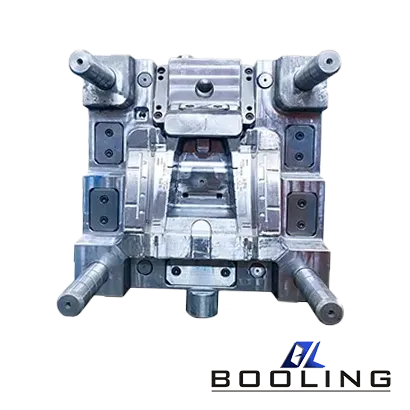
- Injection temperature
- Drying treatment
- Mold temperature
- Injection pressure
- Injection rate
Polycarbonate Injection Molding Capabilities
Polycarbonate has good processing properties and can be combined with injection molding technology to achieve complex structures, details, and precise portrayals.
·
US
Metric
Polycarbonate
59 in. x 51.2 in. x 17.7 in.
1500mm x 1300mm x 450mm
*The use of the demoulding machine should be strictly controlled during the injection molding process of polycarbonate.
Polycarbonate Injection Molding Material
Polycarbonate (PC) is a polyester class of carbonic acid. Carbonic acid itself is not stable, but its derivatives (such as phosgene, urea, carbonate, carbonate) have a certain degree of stability.
Material
- Polycarbonate(PC)
The Advantage & Disadvantage of Polycarbonate Injection Molding
Polycarbonate, as a high molecular weight amorphous polymer containing carbonate groups, has outstanding advantages in injection molding.
- High transparency and light transmittance
- Strong impact strength and hardness
- Able to withstand extreme temperatures
- No toxic substances are produced when heated
- Low shrinkage and stable processing
- Polycarbonate injection molding efficiency is high and has a short molding cycle
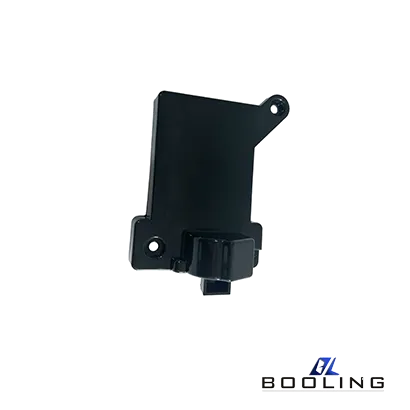
Application of Polycarbonate Injection Molding
Polycarbonate injection molding has excellent impact resistance and transparency and is widely used in optics, automobiles, construction, sports equipment, and other fields.
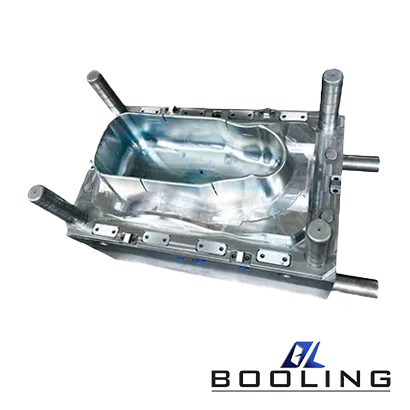
Guidelines for Polycarbonate Injection Molding
Polycarbonate uses high-precision hot runner molds to mold products, achieving production without a cold pouring period and improving efficiency.
Due to its versatility and high quality, polycarbonate injection molding is widely used in the production of automotive parts, and medical and industrial products. This technology combines the special properties of polycarbonate polymers with the high efficiency of injection molding, becoming the best solution for the production of plastic products.
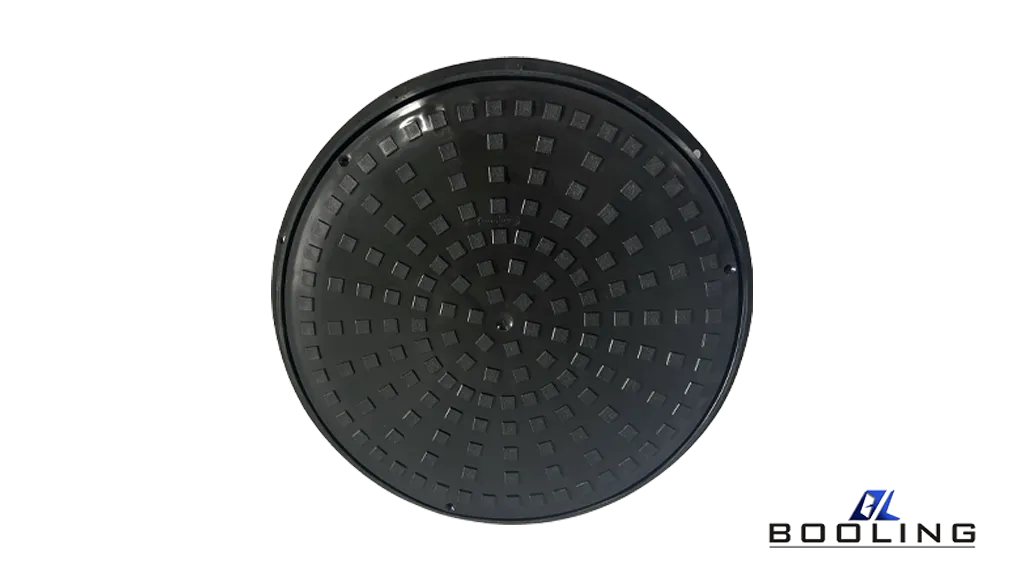
Polycarbonate Injection Molding Process
Booling can achieve seamless integration of polycarbonate materials and injection molding technology to achieve efficient production.
- Heating: The treated polycarbonate material is heated and softened in the barrel of the injection molding machine
- Injection: Under the influence of the screw speed, the polycarbonate melts while moving forward and is injected into the mold cavity through the nozzle
- Plastic flow: The molten plastic flows in the cavity. Polycarbonate has excellent fluidity and can be evenly distributed to every corner of the cavity
- Solidification: Maintain a certain pressure in the mold and enter the cooling stage. The cooling time generally accounts for 70% of the entire processing flow. Booling designs the cooling water channel close to the mold cavity and increases the number to increase the cooling rate
- Demolding: After cooling, the plastic part is ejected and enters the post-processing and inspection stage
Polycarbonate Injection Molding Quality Control Program
Polycarbonate injection molding efficiency is reflected in the production of products. Booling has an exclusive program for product inspection and management to ensure that the products meet the final processing requirements.
- First Inspection: Before each batch of production, the first or first few products produced after the material is replaced and the abnormality is handled are inspected to prevent subsequent products from being unqualified. The purpose of the first inspection is to discover and eliminate potential problems and ensure the quality of subsequent production products
- Patrol Inspection: Engineers need to inspect the products every few hours to promptly discover and avoid production defects, avoid the emergence of a large number of unqualified products, and rework
- Final Product Inspection: After the product is produced, the final product needs to be inspected. The sampling inspection method is used to inspect the size, appearance, structure, and position accuracy of the product to ensure that it meets the final requirements
Application of Polycarbonate Injection Molding
Polycarbonate injection molding products combine impact resistance, transparency, thermal stability, and lightweight, becoming the choice of manufacturers in various industries.
- Automobile: Polycarbonate parts are light and durable, with good light transmittance and wear resistance, suitable for the processing of headlights, dashboards and interiors;
- Optics: Polycarbonate materials have excellent light transmittance and impact resistance, suitable for the production of microscopes, glasses, goggles, and other products, maintaining optical clarity
- Sports protective equipment: now suitable for the processing of goggles and helmets, with good weather resistance and impact resistance to ensure the safety of users
- Aerospace: Polycarbonate meets the advantages of lightness and durability, can withstand extreme temperatures, and helps to improve the durability and fuel efficiency of aerospace products
- Electronic equipment: Polycarbonate has good heat resistance and moisture resistance, which can achieve rapid manufacturing of smart electronic equipment and wire and cable casings