Home > Blow Molding > Plastic Blow Molding
Plastic blow molding helps manufacturers efficiently produce a variety of hollow plastic products. Booling has rich production experience in processes such as parison preparation, mold closing, blow molding, cooling and curing, and demolding post-processing. Plastic blow molding is a one-time molding technology with millimeter-level precision. We have developed mature plastic blow molding automation production solutions for manufacturing plants in the United States, Mexico, India, Russia, Brazil, and other countries.
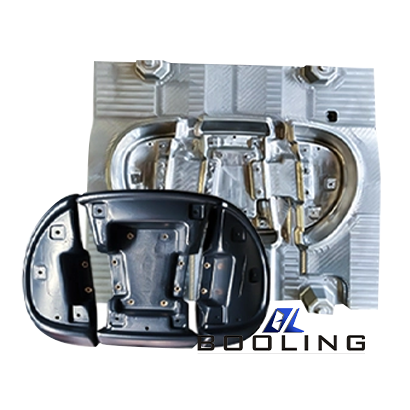
Plastic blow molding is a hollow product molding technology. Booling provides extrusion, injection, stretch blow molding processes, and molds to meet the processing needs of different products and manufacturers.
- Extrusion
- Injection
- Stretch
Plastic Blow Molding Capabilities
Plastic blow molding has strong capabilities and can be customized to produce products with complex shapes and a wide range of sizes, with extremely high flexibility.
·
US
Metric
ABS
82.7 in. x 51.2 in. x 19.7 in.
2100mm x 1300mm x500mm
PE
82.7 in. x 51.2 in. x 19.7 in.
2100mm x 1300mm x500mm
PP
82.7 in. x 51.2 in. x 19.7 in.
2100mm x 1300mm x500mm
PVC
82.7 in. x 51.2 in. x 19.7 in.
2100mm x 1300mm x500mm
TPE
82.7 in. x 51.2 in. x 19.7 in.
2100mm x 1300mm x500mm
*Key advantages are low tooling costs, ability to create complex shapes, and high production rates.
Plastic Blow Molding Material
Plastic blow molding materials range widely, Booling provides the following blow molding materials:
Materials:
- ABS
- HDPE
- PP
- LDPE
- PVC
- Polystyrene
- Polycarbonate
- Acrylic
- PET
- TPE
The Advantage of Plastic Blow Molding
Booling excels in using plastic blow molding to produce large quantities of consistent and precise parts.
- Plastic blow molding technology has strong molding capabilities and is versatile
- Blow molding has fast processing speed, a short production cycle, and a shortened delivery time
- Blow molding is a continuous process that can achieve high-speed production
- The mold structure is simple, and mold parts can be replaced in time to adjust production parameters
- The product has no seams, and the surface pattern and text are clear
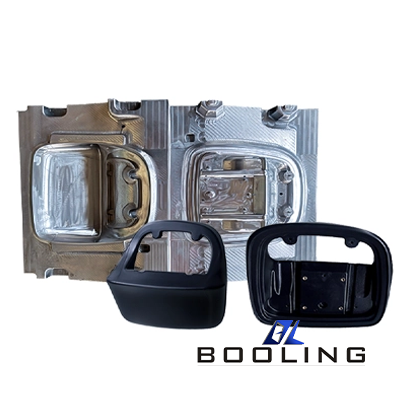
Application of Plastic Blow Molding
Plastic blow molding technology can produce products with consistent wall thickness and complex shapes and is widely used in industries such as automobiles, construction, industry, daily necessities, and packaging containers.
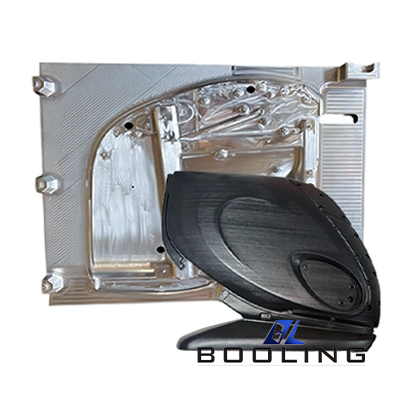
Guidelines for Plastic Blow Molding
Booling provides customized plastic molding services. Engineers will solve users’ processing problems one-on-one and provide one-stop service.
Plastic blow molding is versatile and flexible. It is a technology that converts plastic materials into seamless hollow parts. Booling can produce more durable and cost-effective products by using plastic blow molding. It provides the production of bucket containers, automotive parts, and other products.
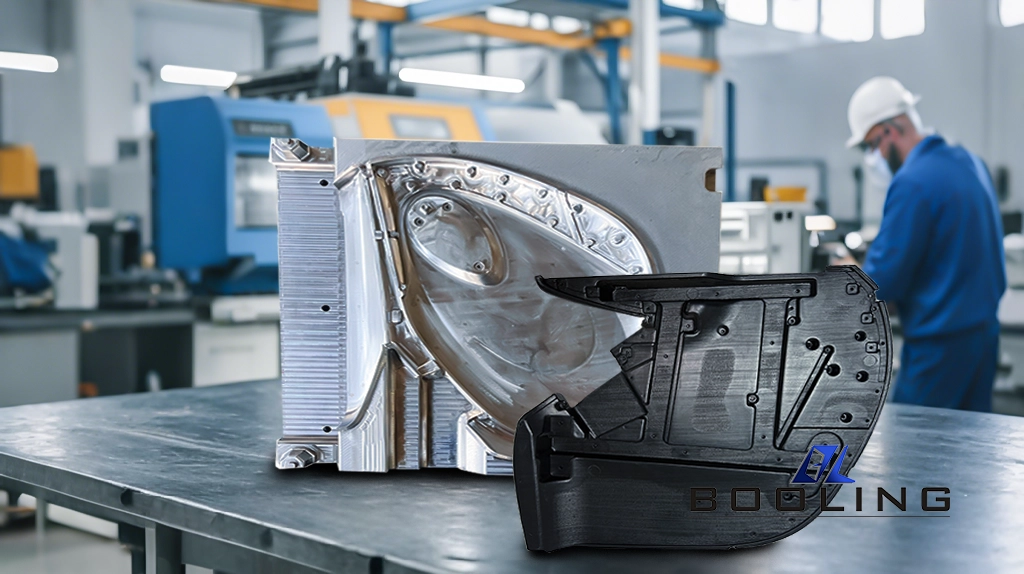
Types of Plastic Blow Molding
Booling provides extrusion, injection molding, and stretch blow molding molds and products to achieve precision manufacturing of different products.
- Extrusion Blow Molding: This is the most common process in blow molding. The die extrudes the molten material to form a parison, and after clamping, the mold is closed and compressed air is introduced to expand it to fit the inner wall of the mold. Extrusion blow molding technology is particularly suitable for the production of large containers.
- Injection Blow Molding: This is a technology that combines injection molding and blow molding. Preforms are manufactured by injection molding, transferred to the blow mold, and air is introduced to form. Injection blow molding technology is suitable for the production of small containers.
- Stretch Blow Molding: For stretch blow molding, engineers stretch the preform axially and radially to improve the strength and transparency of the material. Stretch blow molding technology is suitable for the production of PET bottles.
How to Control the Quality of Plastic Blow Molding Products?
In order to ensure that molds and products meet industry standards and customer requirements, Booling has a quality control system to achieve the production of high-quality defect-free products.
- Clear Product Requirements
Booling engineers will clarify and plan product requirements before entering production.
(1) Select appropriate plastic materials based on the required strength, flexibility, temperature resistance, and chemical resistance of the product
(2) Analyze the special structure, size, wall thickness, transparency, and other requirements of the product
(3) Ensure that the product production process and material selection meet market demand and regulatory standards
(4) Ensure that the selected process meets the production requirements of the product
- Processing Quality Control
(1) Conduct experiments on blow molding air pressure, temperature, and mold closing speed to find the optimal parameters to ensure that the product is defect-free and achieves reliable production
(2) Monitor process parameters at any time and optimize them at any time to improve production efficiency
(3) Conduct quality inspections to ensure that the product is defect-free, such as weld marks, water ripples, etc.
(4) Ensure that the color and transparency of the processed product meet the final requirements
- Quality Assessment
(1) Conduct dimensional inspections with the help of calipers or micrometers. Booling has automatic optical and laser inspection systems to further ensure product accuracy
(2) Visually inspect parts for surface defects such as bubbles, cracks, and uneven color distribution
(3) Test the physical and mechanical properties of the product to ensure that the product meets the final requirements, such as tensile strength test, impact resistance test, etc.
(4) Perform performance tests such as drop, leakage, and fatigue
(5) Booling can also provide 3D printing technology to predict and optimize the performance of blow molds and products and identify potential defects