Home > Blow Molding > ABS Blow Molding
ABS blow molding makes the ABS raw material heated to a molten state pass through the screw and die of the extruder into a cylindrical parison, placed in a blow molding mold, and blown into shape by compressed air. It is widely used in automobile tail wings, luggage racks, pedals, front and rear bumpers, medical beds, and other parts. Booling has rich experience in extrusion blow molding molds and provides high-quality blow molding solutions for countries such as the United States, Mexico, Russia, and Turkey.
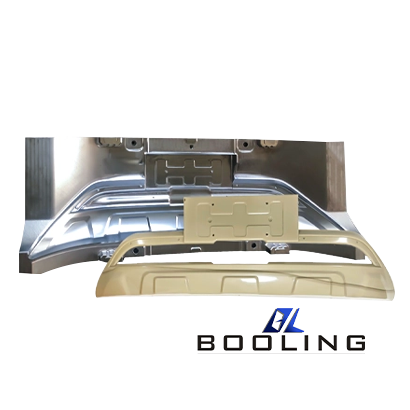
ABS Blow Molding
Blow molding grade ABS is in an opaque granular form with good mechanical properties and processability, making it an ideal choice for raw materials in the field of blow molding.
Key Points of ABS Blow Molding:
- ABS is a relatively hard plastic with good toughness and impact strength.
- Blow molding grade ABS is typically opaque and colored.
- ABS molds well after drying but has limited chemical resistance compared to polyethylene (PE) or polypropylene (PP).
- ABS can meet UL 94 V-0 flammability standards for certain grades.
- It is recyclable under code 7, but its toughness makes grinding difficult.
ABS Blow Molding Capabilities
ABS blow molding molds have excellent mechanical properties and diverse application areas. They are suitable for a variety of plastic molding equipment and have strong processing capabilities.
·
US
Metric
ABS
86.6in. x 27.6 in. x19.7in.
2200mm x 700mm x500mm
*ABS is a popular choice for blow molded products due to its good mechanical properties and processability.
ABS Blow Molding Material
ABS has good melt viscosity, fluidity, and elongation. It can maintain the stability of the product shape during the blow molding process, and the melt spreads more evenly in every corner of the mold.
Material
- ABS
The Advantage of ABS Blow Molding
Booling provides high-quality ABS blow molding molds with outstanding advantages.
- It has excellent electrical insulation properties and is used in the manufacture of electronic and electrical components, housings, and other parts
- It has excellent adaptability. Booling can change the performance of products by changing the ratio of ABS or processing it with other materials into composite materials for blow molding
- ABS materials are easier to process and are suitable for extrusion, injection molding, and other processes
- ABS blow molding products have a higher surface finish
- ABS blow molding products can remain stable in extreme temperature environments and have good mechanical properties and chemical resistance
- Recyclable to avoid waste of raw materials and resources
- Using mold processing, the product has a high degree of consistency
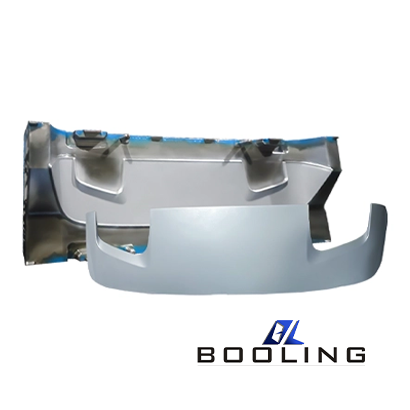
Application of ABS Blow Molding
ABS blow molding is suitable for the production of automotive parts (such as spoilers, pedals, bumpers, and ceiling lights), electronic equipment housings, small household appliances, daily necessities, and other products, and has good stiffness and impact resistance.
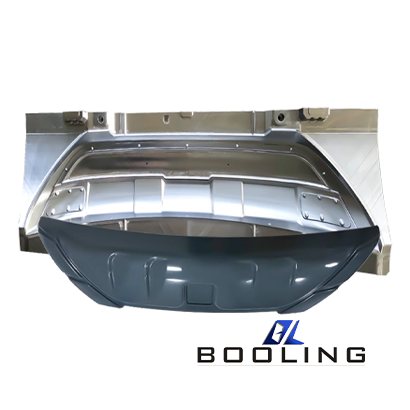
Guidelines for ABS Blow Molding
Booling provides customized ABS blow molding services and designs blow molding molds according to the personalized needs of customers.
ABS blow molding is a rapidly developing hollow product molding technology that is widely used in electronic equipment, household appliances, automobiles, and other fields. Booling obtains precise products through precise control of blow molding mold design, processing, and molding processes.
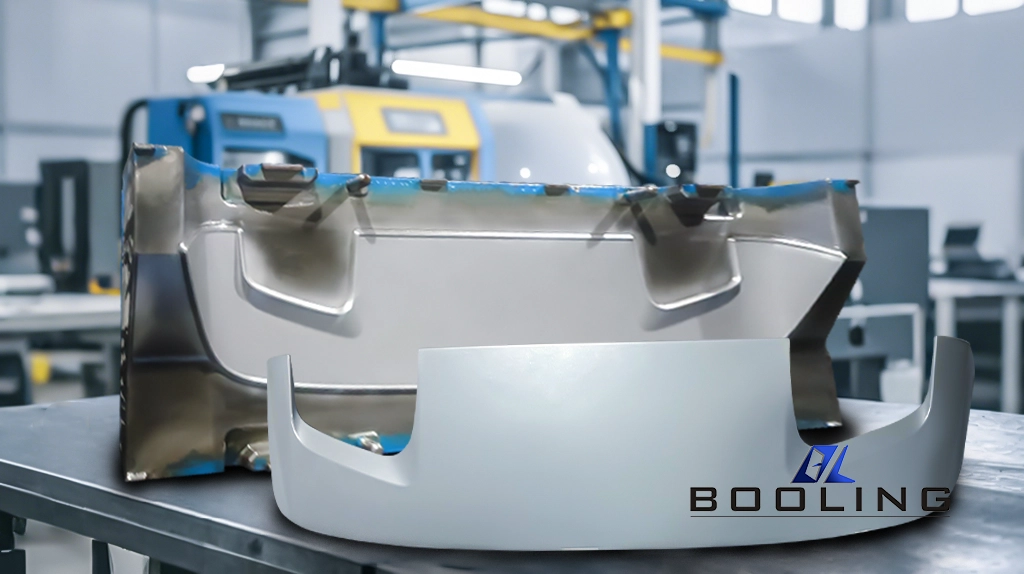
Application of ABS Blow Molding
Blow molding technology is an important means of producing ABS products and is widely used in automobiles, office supplies, packaging containers, household appliances, and other industries.
- Automobile: ABS blow molding molds have been widely used in the automotive field. Booling provides complete design and automated manufacturing solutions for blow molding molds for automobiles and medical parts
- Office supplies: ABS blow molding products have good surface gloss and smoothness, are easy to process and mold, and are suitable for the production of office supplies, such as the shells of products such as telephones, computers, fax machines, and copiers
- Household appliances: ABS blow molding has a wide market in the field of home appliances, such as washing machines, refrigerators, televisions, air conditioner shells, etc., all of which are processed by blow molding molds
- Packaging containers: Cosmetic bottles, medicine bottles, buckets, and other products of various sizes and sizes all use blow molding technology to ensure production efficiency and product consistency
ABS Blow Molding Process
The ABS blow molding process is complex. Booling provides a one-stop service from blow molding mold design to trial mold processing to ensure product accuracy and quality.
- Barrel and Head Temperature
The softening temperature of blow molding grade ABS is generally maintained between 170~190℃, while the processing temperature of the barrel generally needs to reach 170~230℃. The specific setting needs to consider the screw diameter. The temperature setting is directly related to the molding efficiency and quality. In general, the higher the temperature, the smoother the appearance of the ABS blow molding product, and the more surface gloss. Excessive temperature will cause the raw material to decompose and become brittle, the parison to sag, and increase the thickness difference between the upper and lower ends of the product. On the premise of ensuring processing efficiency and product quality, Booling will set the highest possible temperature to speed up the molding speed.
- Screw Speed
The higher the screw speed, the higher the melt temperature. The speed will also affect the output of the blow molding machine. Increasing the screw speed within the range permitted by conditions can increase the material extrusion volume and achieve the effect of increasing output. However, if the speed is too fast, the material will stay in the barrel for a short time, which will reduce the plasticizing effect and cause the defect of reduced output.
- Storage Volume and Time of Materials in the Storage Tank
The plastic melt extruded by the ABS blow molding equipment will be stored in the head and cavity in advance. After the storage reaches a certain amount, the piston will be pushed down by the limit switch, and the melt will pass through the narrow slit of the head to form a hollow leather material. Booling engineers will adjust the storage volume and storage time according to the product structure and size.
- Extrusion Speed
During the blow molding process, only the appropriate extrusion speed can produce high-quality products. A slower speed will increase the temperature difference between the upper and lower ends of the blank, and the lower end will produce weld marks. Extrusion speed is too fast, which will cause the mold to fail to close in time and increase the scrap rate. Engineers need to design the extrusion speed according to the rated temperature of the barrel, the pre-blowing speed, and the strength of the melt
- Blow Molding Pressure
Based on many years of blow molding experience, Booling engineers set the blowing pressure of the blow molding machine to about 0.4-0.6Mpa. For blow molding products with poor flow properties, the pressure needs to be increased to more than 1 MP. Stable blow molding pressure can ensure that the product has a higher surface finish and dimensional stability.