Home > Checking Fixture > Fixture Testing
The fixture testing can detect the size, shape, and quality of parts to ensure that the dimensions of the parts meet the design tolerance requirements. Booling’s fixtures can provide manufacturers with strict and reliable quality control during the mass production stage. Booling designers design the most suitable gauges and tolerance detection solutions for the product according to the design specifications. We have provided fixture testing for South Korea, Argentina, Russia, India, and other countries.
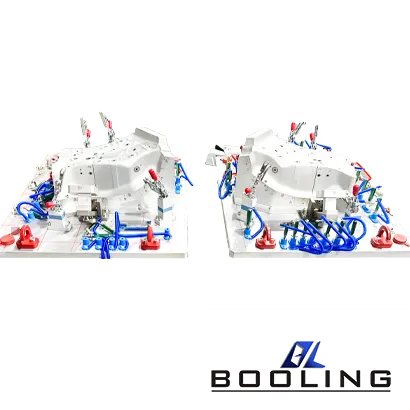
The test of the test fixture needs to be carried out in a stable and consistent environment to ensure that the test results are repeatable and accurate. Booling provides safe and reliable test suite creation to obtain more accurate test results.
Key Points of the Test Fixture Testing:
- Accurate positioning
- Measurement
- Analysis
Fixture Testing Capabilities
The checking fixture testing can ensure that the size, shape, and position of the product meet the design requirements, and control the quality of the development, trial production, formal production, product optimization, and other stages. Booling provides processing and manufacturing of stamping parts, injection molded parts, and machined parts inspection fixtures.
·
US
Metric
Cast iron
70.9in. x 27.6 in. x19.7in.
1800mm x 700mm x500mm
aluminum alloy
70.9in. x 27.6 in. x19.7in.
2200mm x 700mm x500mm
steel
70.9in. x 27.6 in. x19.7in.
2200mm x 700mm x500mm
*The main reference material for large and medium-sized gauges is steel plate or steel plate with resin added.
Fixture Testing Material
The choice of materials is mainly based on the use environment and function of the checking fixture, mainly including:
- Metal: mainly aluminum alloy, steel, etc., suitable for inspection and testing of high-strength parts
- Resin: Resin materials have low cost and lightweight, suitable for testing some sheet metal parts and injection molds
- Composite materials: Some checking fixture materials meet specific needs, such as carbon fiber reinforced materials, etc.
Material
- Acrylic Resin
- Aluminum Alloy
- Steel
- GCr15
- SKD 11
The Advantage of Fixture Testing
Checking fixture testing is a product quality control process with outstanding advantages.
- Booling checking fixture design focuses on practicality and is easy to operate and maintain
- Comprehensive testing can be performed to comprehensively control product performance and quality
- Fixture testing can reduce on-site failures and warranty claims
- Simplify the production process and improve the smoothness of production line operation
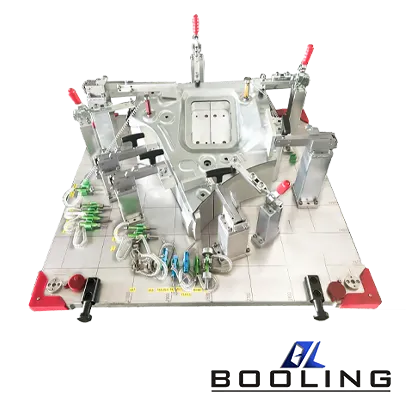
Application of Fixture Testing
The purpose of fixture testing is to control quality. It is suitable for the production and testing of large-scale precision products, such as stamping parts, injection molded parts, machined parts, etc. in the automotive, home appliance, industrial and other industries.
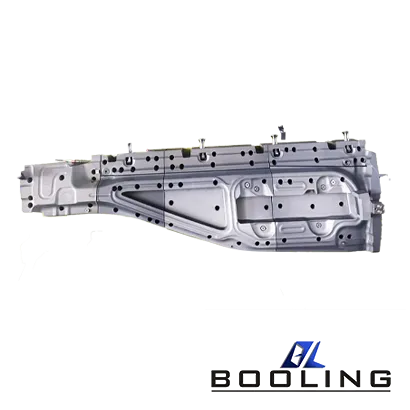
Guidelines for Fixture Testing
Checking fixture testing can achieve precise control of part quality and provide data support for product defect modification, quality improvement, parameter optimization, and new product development.
Checking fixture testing is a very important process in the manufacturing industry, which can help product quality meet design standards and customer requirements. Booling provides processing and testing of various checking fixtures, such as single-piece gauges, part assemblies, and combined gauges, to meet the accuracy requirements of different inspection objects.
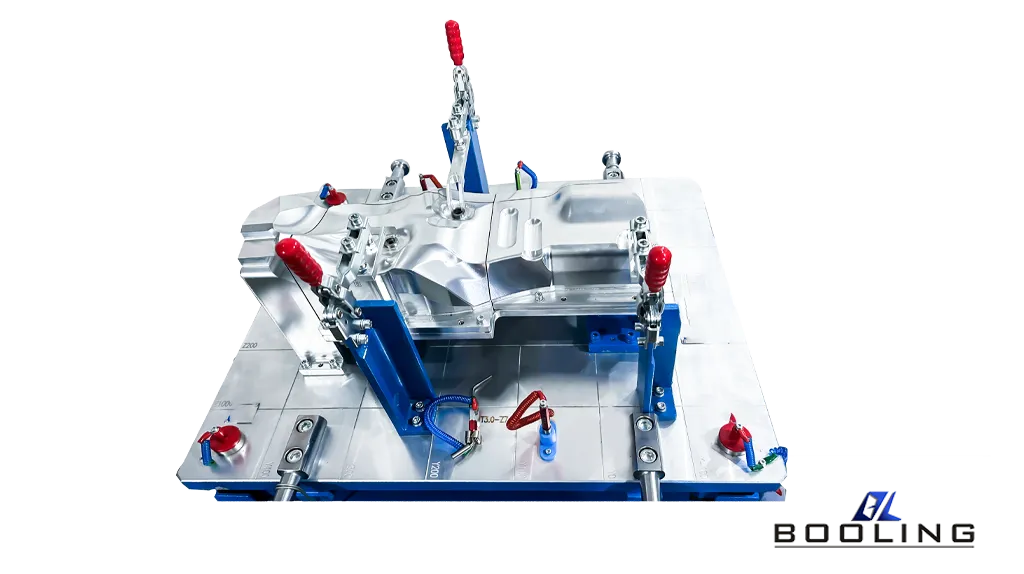
Technical Types of Fixture Testing
Booling provides the design and processing of different fixtures to meet the inspection needs of different equipment and workpieces.
- Single-piece Fixture Testing
A single-piece fixture is a tool that performs comprehensive inspection by simulating the state of the product in actual assembly. It mainly measures whether the edge and hole position of the material have changed to meet the specified requirements. When conducting a single-piece fixture test, the test standards and operating methods must be followed and adjustments must be made promptly.
- Part Assembly Fixture Testing
The assembly fixture is a tool that detects the contact surface, weld assembly holes, reference surface, and the matching of each component. Engineers measure the dimensional accuracy of the stamping die assembly to check whether the welding is successful. The assembly fixture is mainly suitable for welding inspection.
- Combination Fixture
The combination fixture is a multifunctional measuring tool, also known as a functional main model fixture, which mainly includes a base, a carrier model, a standard part module, and a connector. It can evaluate the size and accuracy of parts by simulating the actual assembly process of automotive parts.
Quality Control of Fixture Testing
The accuracy of the fixture directly affects the quality of the final product. Booling has set up a special quality control system to ensure the accuracy and repeatability of the fixture testing.
- Requirements for Fixture Testing: Engineers inspect the parts of the fixture and perform daily maintenance. The testing and use of the fixture must be strictly by the contents of the operation manual to avoid incorrect operation methods.
- Storage of Fixtures: Booling has set up a special fixture storage area with flat ground without potholes to prevent bumps. The fixture environment should be kept clean and dry, and sprayed with rust inhibitor or covered with film to prevent excessive moisture from rusting the metal fixture. When the fixture is stored, it should be marked for the next use.
- Transportation of Fixtures: Before transporting the fixture, check whether each connection mechanism is in a clamped state to prevent looseness and bumps. The fixture is a high-precision equipment that must be kept stable during transportation and moved as close to the ground as possible. Booling uses a flatbed truck to move the fixture and customizes special wooden box packaging to ensure quality.
Maintenance of the Checking Fixture
Maintenance and care of the checking fixture can extend the service life and ensure test accuracy. Regular inspection and maintenance can help to find potential problems and ensure the accuracy of the measurement results.
- Storage: When the checking fixture is not in use, it should be cleaned and rust-proofed with anti-rust oil and lubricating oil regularly, and a thin film should be covered on the checking fixture to prevent dust and rust.
- Daily maintenance: Every time the checking fixture is tested, it is necessary to check whether the marking, measurement points, coordinate values, positioning pins, etc. of the checking fixture meet the requirements. Clean the dust on the equipment panel, simulation block, and components to meet the cleanliness standard. Check whether the measurement value of the checking fixture reference hole is accurate and whether the measurement point needs to be adjusted. Check whether the flip mechanism and clamping device are damaged and report to the Booling engineer in time for repair or replacement.
- Regular maintenance: Regularly check whether there is any damage to the components in the checking fixture and ensure that the screws are tightened. Apply anti-rust oil to the moving and positioning parts of the checking fixture. If there are damaged or worn parts, they need to be reported to the technician in time for timely repair.