Home > Blow Molding in the Medical Industry
HDPE blow molding technology is widely used in blow molding processes, including but not limited to plastic bags, packaging bottles, medicinal storage bottles, etc. In addition, HDPE blow molding products are also applied in fields such as geomembranes, and have an irreplaceable position in many industries.
Advantages of Blow Molding:
- Excellent Chemical Resistance
- Durability and Impact Strength
- Moisture Resistance
- Cost-Effectiveness
Blow molding is a versatile and widely used manufacturing process for producing hollow plastic parts. In the medical industry, blow molding plays a crucial role in creating a variety of essential products, such as fluid containers, medical waste management containers, and other specialized medical devices.
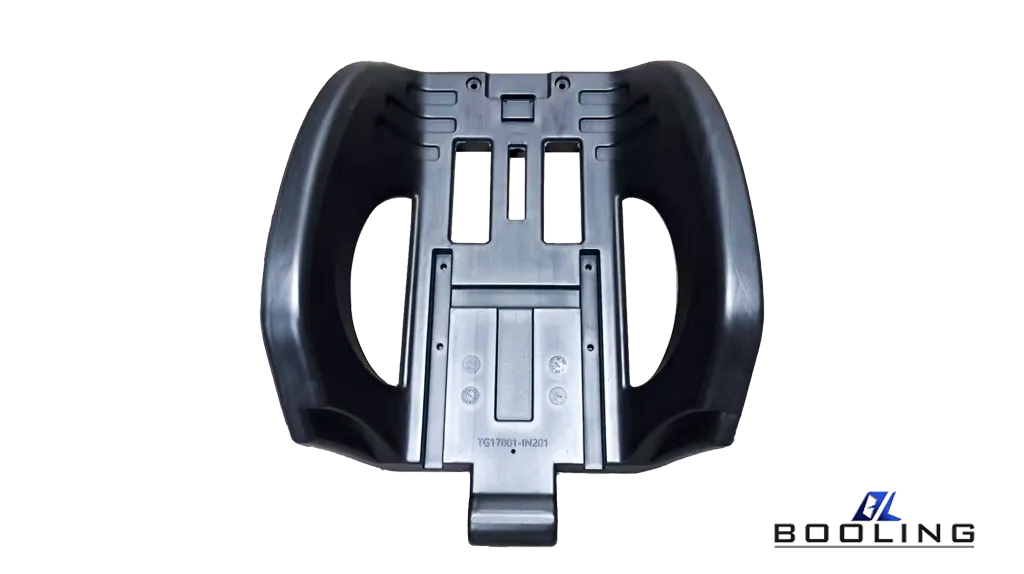
The Blow Molding Process
HDPE blow molding involves several key steps to transform plastic resin into hollow products. The process can be divided into three main types: extrusion blow molding, injection blow molding, and stretch blow molding. Each type has its unique applications and benefits, particularly in the medical industry.
- Material Selection and Preparation
The first step in the blow molding process is selecting the appropriate plastic resin. Common materials used in medical blow molding include high-density polyethylene (HDPE), polypropylene (PP), polycarbonate (PC), and polyethylene terephthalate glycol (PETG). These materials are chosen for their biocompatibility, chemical resistance, and durability.
Once the material is selected, it is fed into a hopper and moved into the barrel of an extruder. The plastic resin pellets are then heated and melted to a molten state, ensuring proper viscosity for the molding process.
- Formation of the Parison or Preform
After the plastic material is prepared, it is molded into a closed-end tube called a parison or preform. This step varies depending on the type of blow molding process used:
– Extrusion Blow Molding: A continuous stream of molten plastic is extruded through an annular die to form a seamless parison. The parison is then clamped between the mold halves and inflated to the desired shape.
– Injection Blow Molding: A preform is first injection molded from the heated plastic resin. The preform is then transferred to the blow mold, where it is reheated and inflated to the final shape.
– Stretch Blow Molding: In this process, the preform is stretched both axially and radially before being inflated, resulting in improved material properties and strength. This method is commonly used for producing PET bottles.
- Blowing Process
With the parison or preform held firmly between two mold halves, compressed air is injected into it. This action causes the tube to inflate, compelling it to align with the mold’s contours. The desired shape is meticulously crafted to match the intricacies of the mold’s design.
- Cooling and Ejection
Once the inflated polymer snugly fits the mold, the cooling process commences. At this stage, a core rod is introduced to assist in maintaining the desired shape. The core rod helps regulate the temperature, ensuring that the newly formed shape solidifies without any distortions. Upon reaching an optimal cooled state, the product is gently ejected from the blow mold machine. The finishing touch involves trimming off the excess plastic, especially around the area where the air injection occurred. This final step guarantees a polished and refined end product.
Applications of Blow Molding in the Medical Industry
Blow molding is extensively used in the medical industry to produce a wide range of products. Some common applications include:
1.Fluid Containers
Blow molding is ideal for producing fluid containers used in medical settings, such as intravenous (IV) bags, blood bags, and urine collection bags. These containers require precise dimensions, biocompatibility, and durability to ensure safe and effective use in medical procedures.
2.Medical Waste Management Containers
Medical waste management is a critical aspect of healthcare facilities. Blow-molded containers, such as sharps containers and biohazard waste bins, are designed to safely store and dispose of medical waste. These containers are made from durable materials that resist punctures and leaks, ensuring the safe handling of hazardous waste.
3.Respiratory Equipment
Blow molding is used to manufacture various components of respiratory equipment, including oxygen masks, nebulizer chambers, and ventilator parts. These products require high precision and biocompatibility to ensure patient safety and effective treatment.
4.Custom Medical Devices
Blow molding allows for the production of custom medical devices tailored to specific applications. This includes specialized containers, housings for medical instruments, and other unique components that require precise dimensions and material properties.
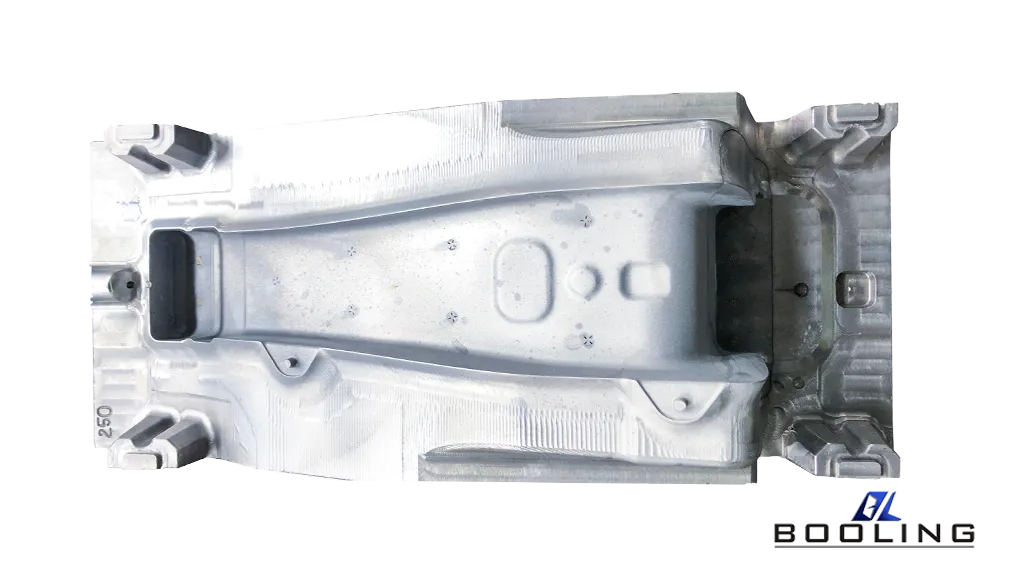
Advantages of Blow Molding in the Medical Industry
Blow molding offers several advantages that make it a preferred manufacturing method for medical products:
1.Cost-Effectiveness
Blow molding is a highly efficient and cost-effective production method, particularly for large-scale manufacturing. The process allows for the production of hollow parts, reducing material usage and overall costs. Additionally, the lower pressure required in extrusion blow molding further reduces expenses.
2.Design Flexibility
Blow molding enables the production of complex shapes and designs, including intricate contours, handles, and indentations. This design flexibility makes it suitable for a wide range of medical products, from simple fluid containers to complex respiratory equipment components.
3.High Productivity
Blow molding machinery is capable of producing large quantities of finished plastic products at high speeds. This high productivity makes blow molding an ideal choice for mass production, ensuring consistent quality and efficiency.
4.Versatility
Blow molding supports a wide range of materials, including HDPE, PP, PC, and PETG. This versatility allows manufacturers to select the most suitable material for their specific application requirements, ensuring biocompatibility and durability.
5.Seamless Construction
Blow molding creates seamless parts, eliminating the need for additional assembly or joining processes. This seamless construction enhances the structural integrity and durability of the finished products, which is crucial for medical applications.
Challenges of Blow Molding in the Medical Industry
Despite its numerous advantages, blow molding also presents some challenges that need to be addressed, particularly in the medical industry:
1. Stringent Quality Standards
Medical products must meet rigorous quality standards to ensure patient safety and efficacy. Blow molding processes must be carefully controlled and monitored to achieve the required precision and consistency. This includes implementing strict quality control measures and adhering to industry standards, such as ISO 9001:2015 and FDA regulations.
2.Material Compatibility
Selecting the appropriate material for medical blow molding is critical to ensure biocompatibility and chemical resistance. Not all materials are suitable for medical applications, and manufacturers must carefully evaluate the properties of each material to ensure it meets the specific requirements of the medical product.
3. Limited Wall Thickness Control
Blow molding may have limitations in achieving precise wall thickness control, especially for complex parts. This limitation can affect the strength and consistency of the finished products, which is particularly important for medical applications that require uniform wall thickness.
4.High Initial Costs
The initial costs of blow molding equipment and tooling can be high, particularly for custom medical products. However, these costs are often offset by the high productivity and cost-effectiveness of the blow molding process in large-scale production.
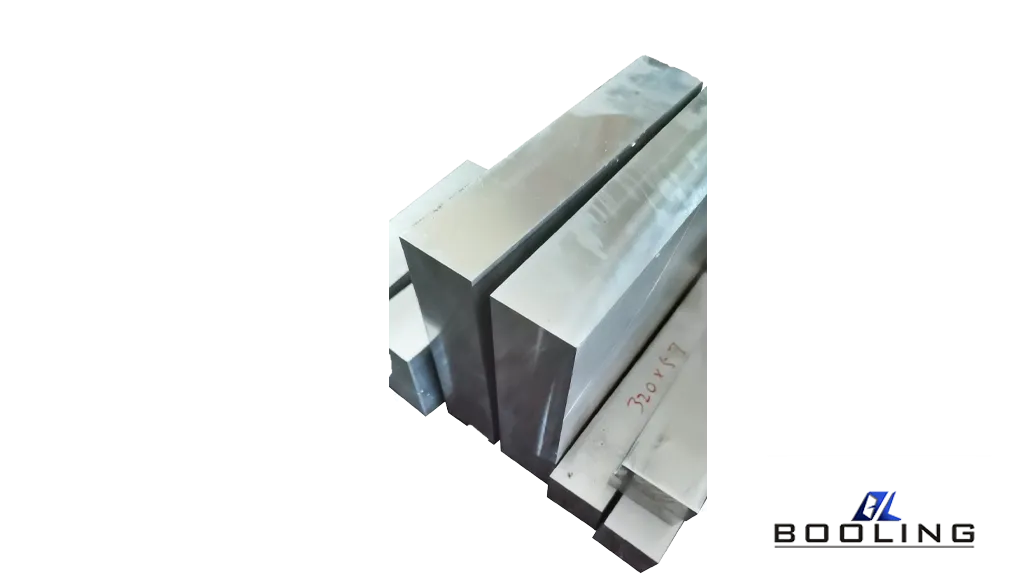
Case Studies and Examples
Case Study 1: IV Fluid Containers
A medical device manufacturer required a reliable and cost-effective solution for producing IV fluid containers. The company chose extrusion blow molding due to its ability to produce high-quality, seamless containers with precise dimensions. By using HDPE blow molding , the manufacturer ensured the containers were biocompatible and chemically resistant. The blow molding process allowed for the efficient production of large quantities of IV fluid containers, meeting the stringent quality standards required for medical applications.
Case Study 2: Sharps Containers
A healthcare facility needs durable and puncture-resistant sharps containers for the safe disposal of medical waste. The facility partnered with a blow molding manufacturer specializing in medical products. Using PP and PC materials, the manufacturer produced custom sharps containers that met the facility’s requirements for safety and durability. The blow molding process enabled the production of containers with complex shapes and secure lids, ensuring safe handling and disposal of sharps.
Case Study 3: Respiratory Equipment Components
A medical device company required high-precision components for respiratory equipment, including oxygen masks and nebulizer chambers. The company selected injection blow molding for its ability to produce intricate parts with high precision and consistency. By using PETG, the manufacturer ensured the components were biocompatible and durable. The blow molding process allowed for the efficient production of high-quality respiratory equipment components, meeting the stringent standards required for medical devices.
Future Trends in Medical Blow Molding
As technology continues to advance, several trends are emerging in the field of medical blow molding:
1.Sustainable Materials
The push for sustainability is driving the development of new, eco-friendly materials for blow molding. Biodegradable and recyclable plastics are being explored as alternatives to traditional materials, reducing the environmental impact of medical products.
2.Advanced Automation
Advancements in automation are enhancing the efficiency and precision of blow molding processes. Automated systems can monitor and control various parameters, ensuring consistent quality and reducing the risk of defects. This is particularly important for medical products that require high precision and reliability.
3.Customization and Personalization
The demand for customized and personalized medical products is increasing. Blow molding technology is evolving to accommodate the production of custom medical devices tailored to individual patient needs. This includes the development of new mold designs and materials that allow for greater flexibility and customization.
4.Integration with Other Manufacturing Processes
Blow molding is increasingly being integrated with other manufacturing processes, such as injection molding and thermoforming, to create complex medical products. This integration allows for the production of multi-component devices with enhanced functionality and performance.
Blow molding is a versatile and efficient manufacturing process that plays a crucial role in the medical industry. Its ability to produce complex, hollow plastic parts with consistent quality and high production rates makes it an attractive choice for a wide range of medical applications. While blow molding presents some challenges, such as stringent quality standards and material compatibility, its advantages, including cost-effectiveness, design flexibility, and high productivity, outweigh these drawbacks.
Blow molding related content
Applied’s expertise in modifying materials at atomic levels and on an ihdustrial scaleenables our customers to transform possibilities into reality.