Home > Structural Design of Dustbin Mold
Details
Details:
Model
Material
Brand
Origin
Application
Booling- Househlod Mold Mold-1
P20, 718, S136, 2738 etc
Booling
China
Household Mold parts
Dustbin molds are used to produce large quantities of dustbin products, and the structure is sophisticated and complex. Booling mold designers use advanced moldflow software to analyze product molding and runner design before mold design. Based on their rich experience in designing and producing this mold, they provide dustbin manufacturers with good mold structure design solutions.
Advantages of Dustbin Mold Molding
- Precision size
- Precision processing of complex structures
- High production efficiency
- Wide selection of raw materials
- Flexible design
Related Hot Products
The design of the dustbin mold is flexible. It is necessary to consider factors such as the shape, size, wall thickness, etc. of the dustbin, and reasonably design the structure and shape of the mold. For dustbins with complex internal structures, more precise demoulding and ejection mechanisms are needed to shorten the molding cycle and improve production efficiency and product quality.
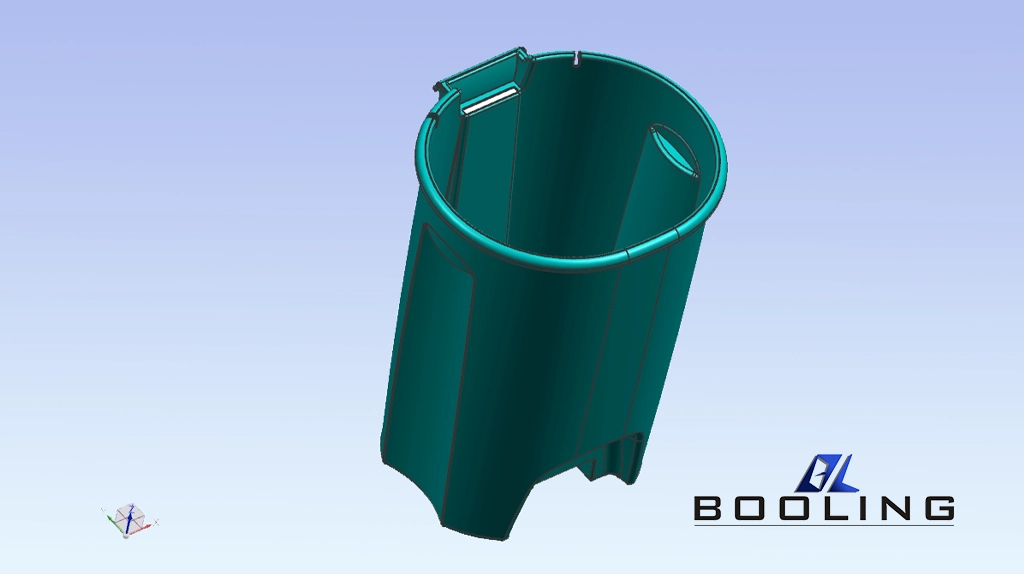
Design Points of Dustbin Mold Structure
When designing a dustbin mold, it is necessary to clarify the required production process, such as blow molding or injection molding, and clarify the production batch of the dustbin and the hardness of the mold steel.
When designing, it is necessary to calculate the size of the cavity and core according to the specific specifications of the dustbin, and fully consider the material shrinkage rate to avoid defects in the molded product.
The hardness of the mold cavity and core is generally around HRC50~HRC55, which ensures the wear resistance and service life of the mold while ensuring machinability.
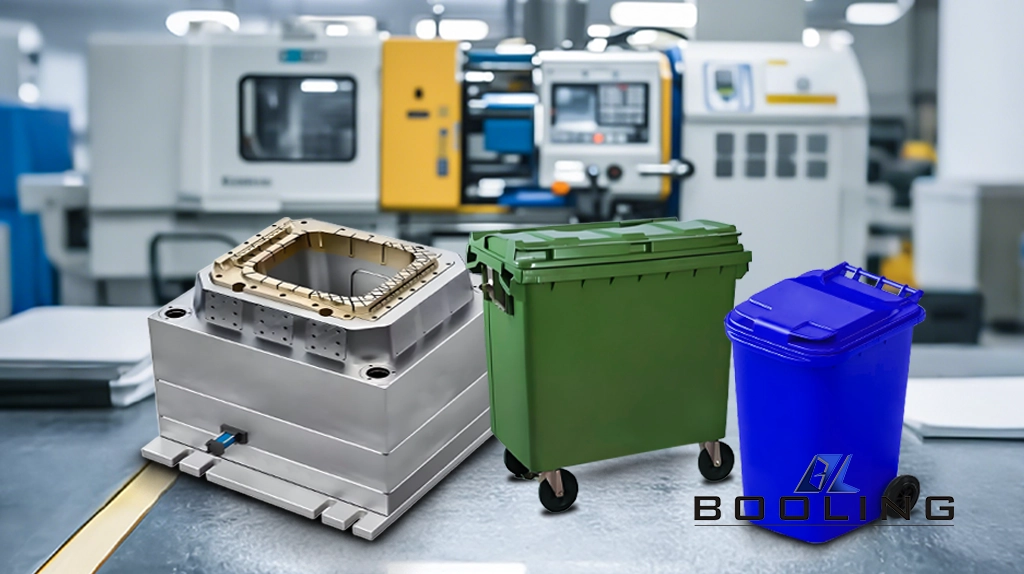
Structure of the dustbin injection mold
The dustbin injection molding mold is generally composed of a concave and convex mold, a pouring system, a guide mechanism, a demoulding and ejection mechanism, a cooling system, etc.
-Concave and convex mold: The concave mold is usually located in the upper mold seat, which is used to mold the external shape of the dustbin. The cavity conforms to the shape of the dustbin and determines the external contour; the convex mold is generally located in the lower mold seat, which is used to mold the internal shape of the dustbin, such as the molding of structures such as reinforcing ribs.
-Gating system: The pouring system of the mold directly determines the molding quality and cycle of the mold. Designers need to determine the type, number, and size of the gate according to parameters such as the structure, size, and appearance requirements of the dustbin.
The main channel is a channel connecting the injection molding machine nozzle and the diverter cavity, which can guide a large amount of plastic melt to quickly enter the mold; the diverter connects the main channel and each gate to evenly distribute the plastic melt to each cavity.
The cold material hole is generally set at the turning point of the diverter or the end of the main channel to collect cold materials with lower temperatures for subsequent cleaning.
-Guide mechanism: The mold guide mechanism is generally set on the lower mold base. Generally, 2 to 4 guide pins are required according to the shape and size of the mold. The guide pins and guide sleeves should have chip grooves at the parting surface, and the axis should be parallel.
-Mold removal and ejection mechanism: The ejection mechanism is generally set on the movable mold, which can ensure that the plastic parts do not deform during the demolding process, maintain a good product appearance, move accurately, reliably, flexibly, without jamming, and can be correctly reset and keep the reference surface flat when closing the mold
-Cooling system: The cooling system of the mold is generally composed of cooling channels and water pipe joints, which surround the cavity and quickly pass cooling water into the cooling channel to absorb the heat of the mold.
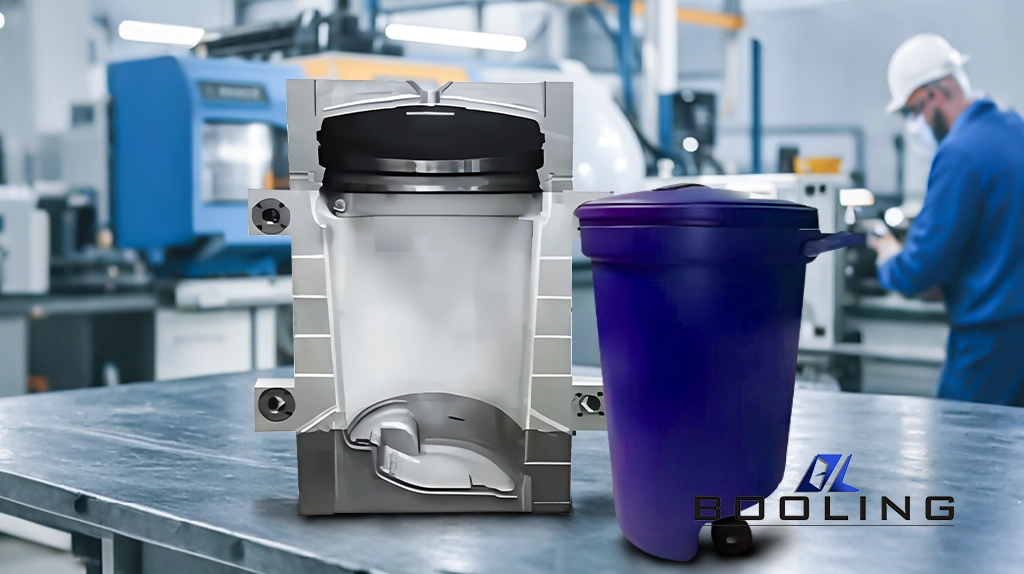
Structure of the Blow Molding Mold for Dustbin
The mold clamping mechanism, blowing system, exhaust system, etc. of the blow molding mold for dustbins are different from the structural composition of injection molds.
-Clamping mechanism: including structures such as upper and lower mold bases, which are the basic supporting parts of the mold; the guide device is generally composed of guide pins and guide sleeves, which guide the upper mold base to close to the lower mold base to ensure molding accuracy and prevent dislocation. The clamping device can ensure that the mold remains closed during the blow molding process to prevent plastic overflow.
-Blowing system: Compressed air enters the cavity through the air inlet channel, which is usually connected to the blowing nozzle in the blow molding machine and directly communicates with the mold cavity. The design of the blowing nozzle has an important influence on the quality of the dustbin molding and can help it expand evenly.
-Exhaust system: Precise exhaust is achieved through exhaust holes and exhaust grooves, which are usually opened on the parting surface or at the end of the mold cavity to exhaust all the gas generated when the parison is blown up, avoid defects such as bubbles, and ensure the quality of the dustbin products.
Automotive Mold Related Content
Applied’s expertise in modifying materials at atomic levels and on an ihdustrial scaleenables our customers to transform possibilities into reality.