Home > Air Conditioner Mold: Overview of Key Processes
Details
Details:
Model
Material
Brand
Origin
Application
Booling-Home Appliance Mold-1
P20, 718, S136, 2738 etc
Booling
China
Home Appliance parts
Air conditioner molds are key tools for manufacturing air conditioner parts, mainly including injection molding, blow molding, and other processing techniques, which can produce products with high precision and high efficiency to meet the needs of different parts and air conditioner manufacturers.
Advantages of Air Conditioner Mold Processing
- High efficiency
- Achieve mass production
- Flexible process selection
- Wide material selection
- Cost-effective
Related Hot Products
Air conditioner molds are frequently used in household appliance molds. These molds use high-precision processing equipment and advanced processing technology, such as five-axis machining centers, EDM equipment, wire cutting machines, injection molding, blow molding, and other processing technologies, to meet high-quality and high-precision processing requirements and provide guarantees for subsequent product production.
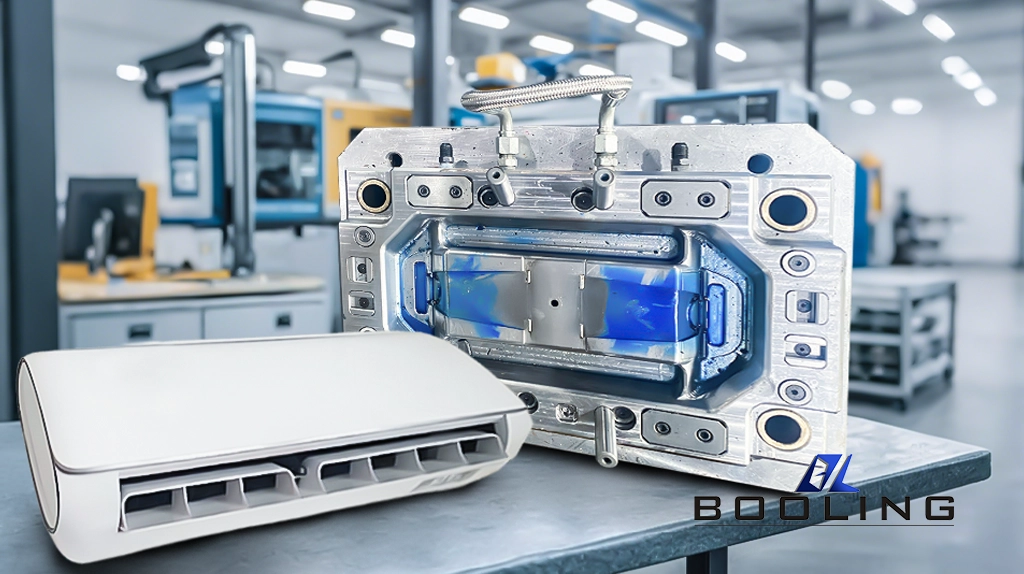
Key Manufacturing Processes of Air Conditioner Mold
Injection molding and blow molding are two processes suitable for air conditioner parts with different requirements, and there are also differences in molds.
-Injection molding
It is mainly to push the plastic into the barrel of the injection molding machine, heat it to a uniform molten state, and move it forward under the push of the screw, inject the molten plastic into the closed mold cavity through the nozzle, fill it into every corner of the mold, and obtain the required product after pressure cooling.
Injection molding can produce more precise and complex air conditioner parts to meet the processing requirements of complex parts. Most of the parts in the air conditioner, such as the inner and outer machine housing, remote control panel housing, display housing, air guide plate, grille, etc., are processed by injection molds.
-Blow molding
Blow molding is widely used in the manufacture of various hollow parts. The cavity closed in the mold cavity is inflated with gas pressure, and the required product is obtained after cooling and shaping.
Blow molding is divided into extrusion, injection molding stretch blow molding, etc., to manufacture plastic products of different requirements and sizes. No waste is generated during the processing, and the adaptability to materials is strong.
Pipes, connectors, and other parts in air conditioners are generally processed by blow molding to achieve designs of different shapes to meet special performance requirements.
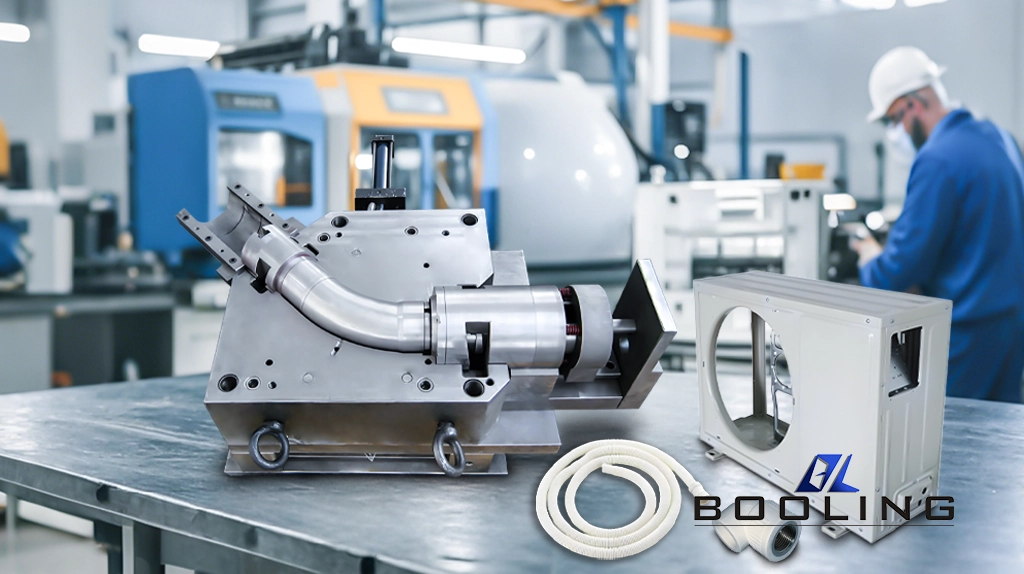
Key Processing Technology of Air Conditioner Mold
Through rough processing, fine processing, heat treatment, surface treatment, and other processes, the precision processing of air conditioner molds can be achieved.
The steel is processed into blanks by forging, cutting, and other methods, and a certain processing allowance is left. The key parts of the mold such as the cavity and core are finely processed, and key processes such as EDM and wire cutting are used to further improve the dimensional accuracy of the mold.
The processed parts are subjected to heat treatment processes such as quenching and tempering to improve the hardness, strength, and toughness of the mold, and improve the comprehensive performance and internal structure of the mold. Surface treatments such as polishing and chrome plating are carried out to reduce the surface roughness of the mold and improve the surface quality.
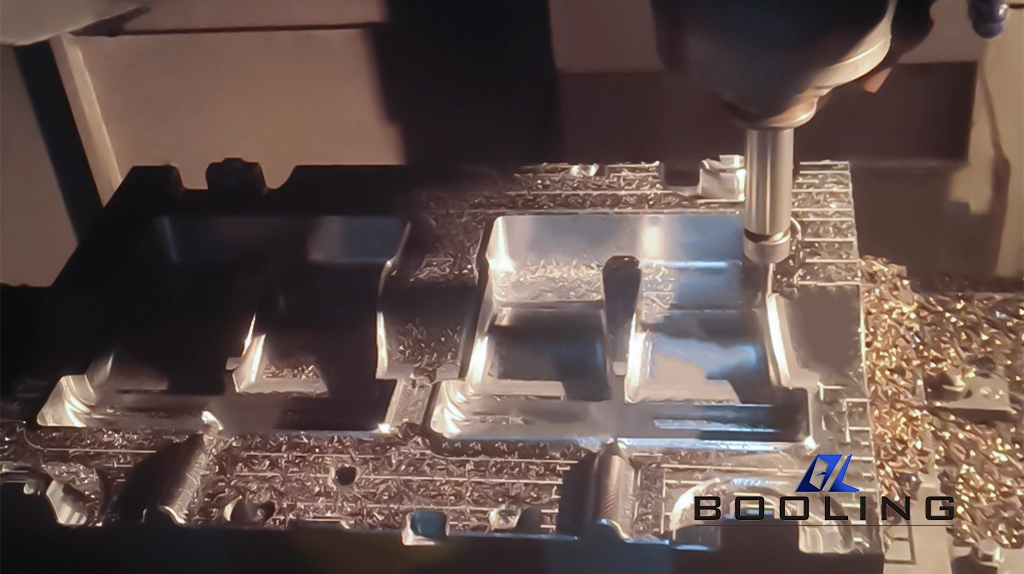
Key Manufacturing Equipment for Air Conditioner Molds
Air conditioner molds are divided into rough machining, semi-finishing, finishing, and other processing procedures, using high-precision processes and processing equipment.
- Precision machining machine tools
Integrating milling, boring, drilling, tapping, and other processing equipment, can complete multiple processes in one clamping, improve processing efficiency, and reduce clamping errors.
- EDM machine
For steel with relatively high hardness and melting point, traditional machine tools cannot be further processed. At this time, EDM technology can be used. In this process, the electrode and the process do not come into direct contact, and no deformation or damage will occur due to cutting.
- Wire cutting machine
The workpiece is cut by the electro-erosion effect generated by the pulse discharge of the linear electrode and the workpiece, and various shapes of mold steel can be processed. In this process, the electrode wire moves continuously, and the loss generated is small, which can realize automated wire-cutting processing and reduce processing costs and cycles.
Automotive Mold Related Content
Applied’s expertise in modifying materials at atomic levels and on an ihdustrial scaleenables our customers to transform possibilities into reality.