Home > Overview of Key Processes for Bucket Mold
Details
Details:
Model
Material
Brand
Origin
Application
Booling- Househlod Mold Mold-1
P20, 718, S136, 2738 etc
Booling
China
Household Mold parts
Bucket molds are widely used in the production of plastic buckets. Booling uses advanced technologies such as precision CNC machining, electrical discharge machining, and wire cutting. By strictly controlling the molding process, material quality, and processing parameters, it ensures the final quality of the product and provides efficient mold production solutions for plastic bucket manufacturers.
Advantages of bucket mold processing:
- Product consistency
- High precision
- Ability to achieve one-piece molding
- Flexible design
Related Hot Products
Bucket mold plays a key role in the molding efficiency and quality of products. They require strict control of design and processing steps, and accurate 3D modeling and CNC processing. Bucket blow molding and injection molding molds are widely used in daily necessities, home furnishings, chemicals, logistics, and other industries to meet the needs of different manufacturers.
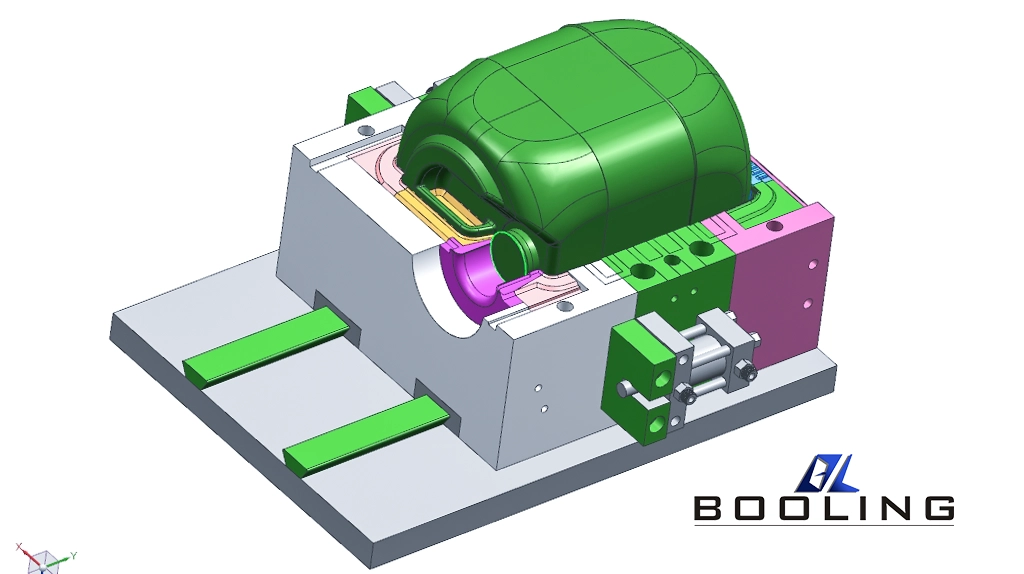
The Design Scheme of Bucket Mold
Water buckets can be processed and molded using blow molding or injection molding molds to meet the needs of different structures and sizes of molds.
The design software UG is widely used in the field of molds, capable of processing complex surfaces and structures, and is suitable for designing complex water bucket molds with lids, handles, and other models.
If the product already has a 3D design model, it is only necessary to import a format that is compatible with the design software, such as STEP, and confirm whether there are any issues with the file, such as broken surfaces or overlaps, for repair.
Use design software to design parting surfaces, cores, cavities, and other components. Set up a parting surface according to the shape of the water bucket and the demolding requirements, and use software to simulate the opening and closing of the mold to check whether the operation is reasonable.
Design the pouring, cooling, and demolding system. The design of using hidden or side gates ensures the aesthetics and sealing of the product. Optimize the design of the pouring system using mold flow analysis. Create cooling channels inside the cavity and core, with a diameter of generally 8-12mm. By continuously adjusting the water flow rate and temperature, ensure more uniform cooling and reduce product deformation.
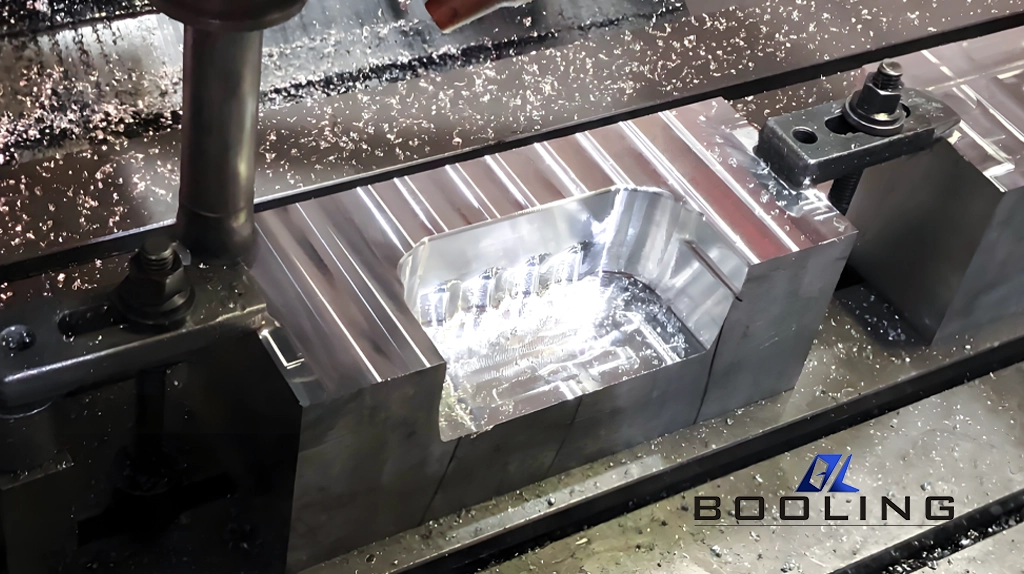
Key Processing of Bucket Mold
After the design is completed, it enters the processing stage, where high-precision molds are obtained through processes such as rough machining, precision machining, and heat treatment.
The rough machining of the mold has reserved a considerable amount of machining allowance to prepare for the precision machining of the mold. Using large CNC machining centers, gantry milling machines, and other equipment to quickly remove a large amount of steel, for complex surfaces, solutions such as cavity milling are often used to adapt to the shape of the surface. During rough machining, smaller cutting speeds and larger feed rates are usually used to ensure machining efficiency.
Before carrying out mold precision machining, it is necessary to inspect all equipment to avoid machining errors. Perform CNC milling precision machining and use UG software to produce milling tool paths for automatic machining. Using electrical discharge machining technology to process parts that cannot be processed by traditional processes, such as narrow grooves and deep holes, with precision.
Heat treat the mold to change its internal structure and improve its overall quality. Adopt processes such as tempering and quenching to extend the service life of the mold.
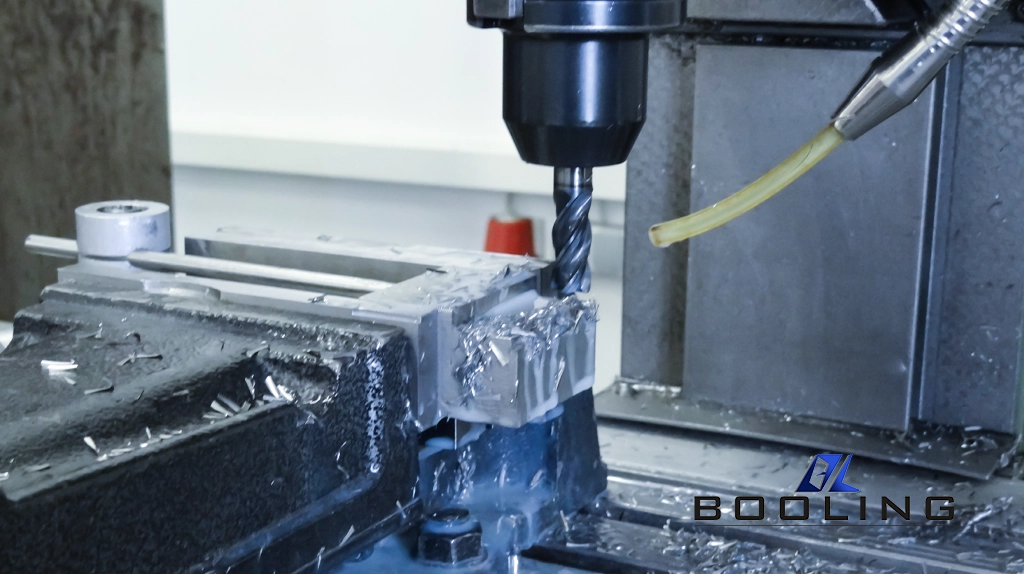
Assembly and trial Molding Of Bucket Mold
Assemble according to the design drawings and final assembly drawings of the bucket mold, ensuring that all parts are within the allowable tolerance range.
Assemble the designed cavity, core, and other components, and use coordinate measuring instruments, gauges, and other equipment to inspect the mold to ensure assembly accuracy. Use software to analyze the opening and closing movements, demolding, and other movements of the mold to ensure that each component does not interfere with each other.
Install the assembled and inspected molds on the machine for trial molding, and retain the trial production products for subsequent product and mold optimization.
Automotive Mold Related Content
Applied’s expertise in modifying materials at atomic levels and on an ihdustrial scaleenables our customers to transform possibilities into reality.