Home > What is Automotive Plastic Mould?
Details
Details:
Model
Material
Brand
Origin
Application
Booling-Automotive Mold-1
P20, 718, S136, 2738 etc
Booling
China
Automotive parts
Booling provides automotive plastic mold processing, including blow molding and injection molding. By adopting advanced EDM technology, we ensure that the mold can be precisely formed to obtain automotive parts with performance and appearance.
Advantages of automotive mold:
- High precision
- High production efficiency
- Flexible design
- Easy to modify parameters
- Strict quality control
Related Hot Products
Booling automotive plastic mold adopts advanced CNC machining technology, provides design and customization services for molds of automotive interior and exterior trims, precision parts, etc., and professional solutions for complex styling designs. We provide automotive trial mold production and continuously optimize it according to production cycle and product quality to meet customers’ high-precision requirements for the automotive industry.
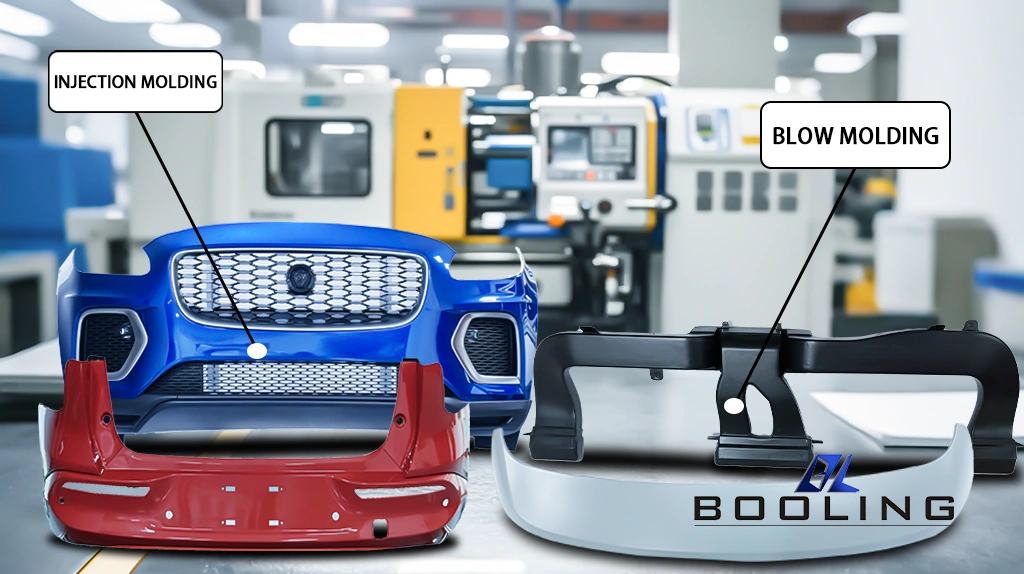
Types of Automotive Plastic Mold
Booling provides automotive injection and blow molding mold suitable for producing different parts.
Plastic injection molding is a widely used technology in the automotive industry. In this process, molten plastic is injected into the mold cavity under high pressure, and the finished product is ejected after cooling and solidification. The plastic injection mold can efficiently produce complex shapes and can realize injection moulding of the car bumper, automotive door trim, instrument panels, etc.
It is suitable for the production of large or hollow automobile parts, such as fuel tanks, water tanks, air ducts, luggage racks, pedals, etc. The structure of automobile blow molding molds is relatively simple, including cavity, blowing, and exhaust devices, and the manufacturing cost is low.
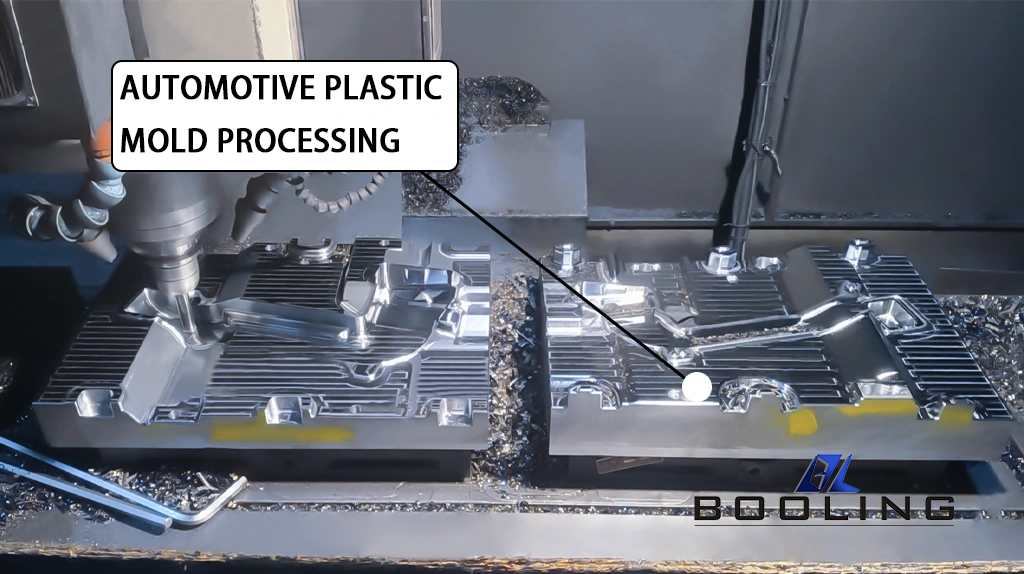
Processing Solutions for Automotive Plastic Mold
Booling provides customized design and processing solutions for automotive plastic molds to ensure the molding cycle and production quality of the molds.
- Analyze the 3D drawings, samples, or sample sizes sent by customers, analyze whether the product can be successfully molded, and provide customers with improvement suggestions and process analysis reports.
- Make reasonable and professional quotations based on the mold structure, ejection system, accessories and brand, hot runner brand, mold steel and surface treatment requirements, and provide customers with the time for the first mold trial.
- Provide customers with estimated mold dimensions to ensure that the mold meets the customer’s production equipment requirements.
- Before formal design, ensure that all processing data are frozen data, hand over all mold information to our designers, and provide mold plans and schedules. If the customer makes suggestions and modification plans, further modifications will be made according to the customer’s equipment configuration and operating habits.
- After the drawing review is passed, material preparation is carried out. Booling operators perform four-sided flying knife operations on the steel, milling the material surface over a large area, improving the efficiency of subsequent processing, and ensuring that the steel meets the specified size and flatness requirements. Drill the ring holes on the mold to ensure that the mold can be easily lifted by the equipment for subsequent handling or installation.
- Enter the CNC milling stage, and use the milling machine and other equipment to rough-process the mold to obtain the basic shape of the core and cavity. For molds with more complex shapes, by using graphite to process into the required electrode shape, pulse discharge is generated with the workpiece to achieve local melting and gasification of the material, ensuring the processing effect and dimensional accuracy.
- Through the collision operation, ensure that the movable mold and the fixed mold of the mold can be accurately matched after the mold is closed to avoid defects such as leakage of the mold. After the upper and lower molds of the mold are ground, deep hole drilling is performed, and then water channel drilling and wire cutting are performed to further improve the accuracy of the mold.
- According to customer needs, the mold is polished, leather-grained grained, and sandblasted.
- Assemble according to the mold drawing, and install the mold frame, cavity, core, guide mechanism, ejection mechanism, pouring system, and other structures. And debug, check for water leakage, and ensure that the transmission parts such as the oil cylinder, air cylinder, slider, ejector, etc. operate normally without defects such as jamming.
- After assembly, test the mold and shoot a complete mold test video to ensure that the production cycle of the parts meets customer expectations, weigh the parts and check the surface quality to ensure that there are no defects such as flash, burrs, and top white, to improve the utilization rate of materials.
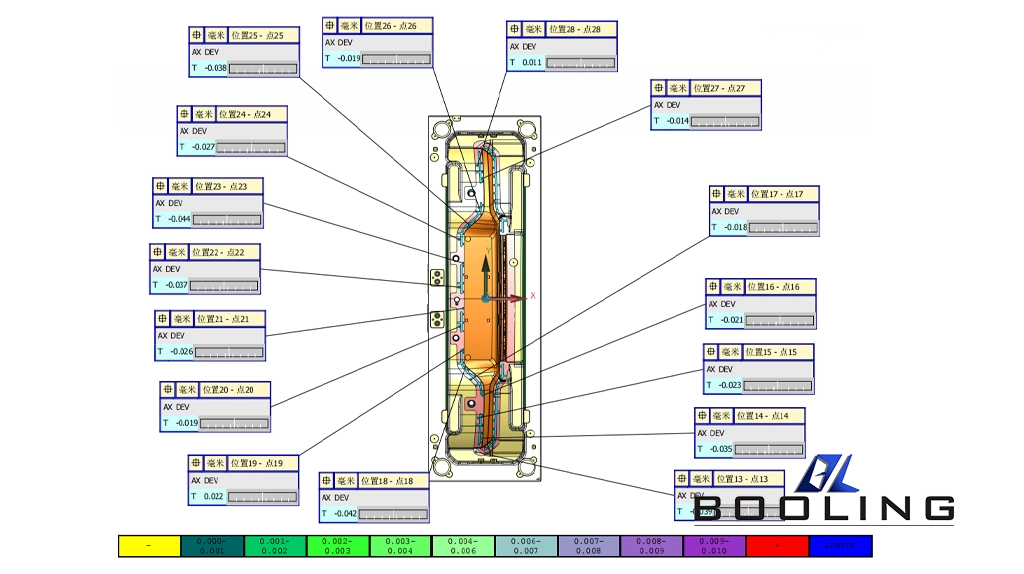
How to Choose a High-Quality Automotive Plastic Mold Manufacturer?
As an automotive mold manufacturer, Booling can produce high-quality products.
- We provide the production of automotive parts inspection fixtures to inspect the shape and position dimensions of the product, ensure that the mold can be assembled smoothly, and the tolerance is controlled within the allowable range.
- Use three-coordinate measuring instruments, blue light scanners and other equipment to inspect the mold and provide corresponding dimensional inspection reports.
- We have a complete mold processing line, including 11 red grinding machines, 5 EDM equipment, etc., to meet the precision processing requirements of automotive molds.
- We have provided customized mold processing services for many well-known automobile manufacturers such as Mercedes-Benz, Land Rover, Lotus, Jaguar, Renault, Chery, etc., including plastic mouldsfor auto bumpers, door panels, luggage racks, ABC columns, dashboards, tail wings, center consoles, headlights, and other products, providing customers with the most efficient production solutions.
- Our project department will formulate corresponding detailed plans before production, all positions have clear division of labor, and processing is carried out strictly in accordance with management procedures and control points, and relevant quality control systems have been established.
- A special schedule is developed for each mold, and all plans need to be signed by departments to ensure compliance with the process and production process. All photos in the schedule have corresponding watermarks and times to ensure the authenticity of the photos and reports so that customers can get clearer feedback.
- For emergency projects, we have a special response plan, record the plan and actual processing time of each process in detail, and arrange personnel to process this project urgently.
- Implement a reward system within the company to motivate employees to produce, ensure that the mold trial is successful within three times, improve efficiency and mold processing qualification rate, and achieve faster delivery.
- We provide complete after-sales service, including daily maintenance and repair of molds, provide spare parts for all wearing parts, and extend the service life of molds.
Automotive Mold Related Content
Applied’s expertise in modifying materials at atomic levels and on an ihdustrial scaleenables our customers to transform possibilities into reality.