Home > Injection Molding > Liquid Silicone Injection Molding
Liquid Silicone Injection Molding
The components produced by liquid silicone resin (LSR) injection molding have excellent performance and can be used to manufacture insulated electrical appliances, medical equipment, and automotive components.
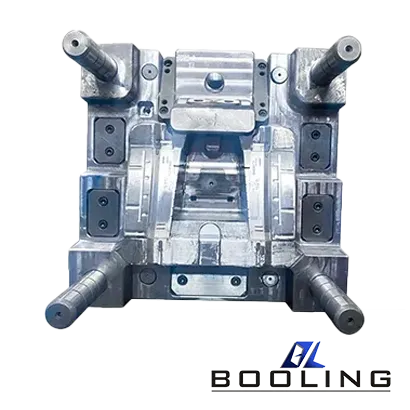
Liquid Silicone Injection Molding
- Two plate mold
- Plate
- Injection mold with lateral parting and core pulling mechanism
- Injection mold with movable inserts
- Automatic thread removal injection mold
- Hot runner injection mold
Liquid Silicone Injection Molding Capabilities
The injection ability of liquid silicone resin is very strong, providing injection for various customized products.
·
US
Metric
Silicone
59 in. x 51.2 in. x 17.7 in.
1500mm x 1300mm x 450mm
*Liquid silicone resin provides strict tolerances and excellent sealing performance.
Liquid Silicone Injection Molding Material
The selection of liquid silicone injection molding materials depends on the properties of the product and the environment in which it is used.
Material
- Liquid Silicone
The Advantage of Liquid Silicone Injection Molding
Liquid silicone resin injection molding has advantages that conventional injection molding does not have.
Advantage:
- Excellent Elongation
- High Tensile Strength
- Strong Liquidity
- Strong Stability
- High Elasticity
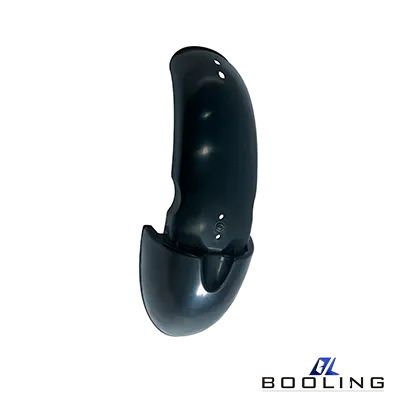
Application of Liquid Silicone Injection Molding
Liquid silicone injection molding technology is applied in various products to improve product performance and user experience. It has its presence in fields such as electronic products, medical devices, and automotive manufacturing.
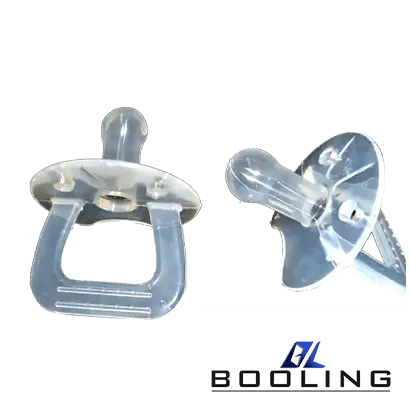
Guidelines for Liquid Silicone Injection Molding
Liquid silicone injection molding is a valuable asset in the injection molding process.
Liquid Silicone Injection Molding Guide
Liquid Silicone Injection Molding
The components produced by liquid silicone resin (LSR) injection molding have excellent performance and can be used to manufacture insulated electrical appliances, medical equipment, and automotive components. At the same time, the products manufactured by this technology are exported to countries such as Spain and Japan. This process has great appeal to suppliers in various industries. The main principle of this technology is to inject liquid silicone resin material into the heated mold cavity, then cool and solidify inside, and form the desired product shape after injection.
In the field of liquid silicone injection molding, the manufacturer’s understanding of material properties is crucial. Liquid silicone is a unique polymer with extraordinary flexibility, chemical resistance, and thermal stability. It differs greatly from traditional thermoplastic plastics. Liquid silicone resin has a better ability to withstand extreme temperatures and has a lower possibility of degradation. Therefore, it is very suitable for products that require long-term exposure to ultraviolet radiation. In addition, liquid silicone resin is widely used in the electronic components and medical equipment industry due to its excellent electrical insulation and environmental performance.
The first step in the liquid silicone resin injection molding process is to select and prepare liquid silicone resin materials. This step mainly involves thoroughly mixing the two parts of organic silicon compounds. The next step is to inject liquid silicone resin into the mold cavity that has been heated to a certain temperature under high pressure, fully and tightly filling every complex detail and pattern of the mold design. Once the filling and pressure holding are completed, the silicone resin will undergo a cooling and solidification process, transforming from liquid to solid elastic products.
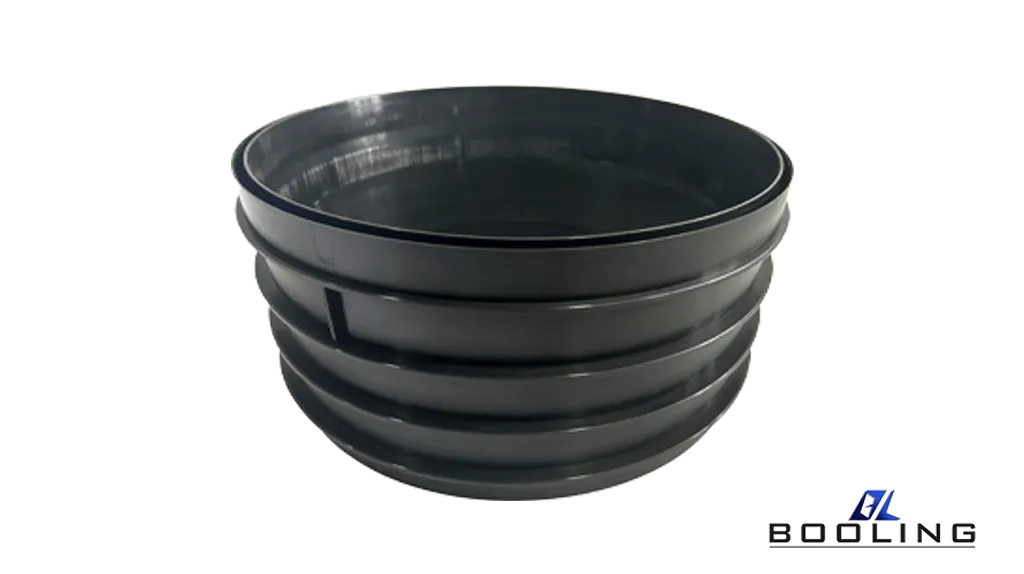
The Difference Between Solid Silicone and Liquid Silicone
Even for organic silicon materials themselves, there are significant differences in their properties between different forms (solid and liquid). Not only do they have different physical forms, but their applications, performance, and manufacturing processes also differ. Manufacturers need to fully understand the subtle differences between these two forms of silicone, as this is crucial for both daily necessities and high-precision industries such as automobiles and healthcare.
Solid silicone, also known as high-consistency rubber (HCR), is a pre-cured, non-flowable material that maintains its shape and integrity even under extreme conditions. It is typically supplied in the form of sheets, rods, or custom-molded parts. The manufacturing process of solid silicone involves injection molding, where the material is heated, injected into a mold cavity, and then cured to achieve its final form. This process allows for the creation of intricate and complex shapes with exceptional dimensional stability and durability.
Liquid silicone, on the other hand, is a low-viscosity, pourable material that can be easily processed and shaped before curing. It is often referred to as room-temperature vulcanizing (RTV) silicone or liquid silicone rubber (LSR). The manufacturing process for liquid silicone typically involves injection molding, where the liquid material is injected into a heated mold cavity and cured through a chemical reaction or exposure to heat. This process enables the production of intricate and precise parts with excellent surface finishes and dimensional accuracy.
One of the key advantages of liquid silicone is its ability to flow and conform to complex geometries, making it ideal for applications that require intricate designs or tight tolerances. Injection molding of liquid silicone allows for the creation of thin-walled parts, undercuts, and intricate details that would be challenging or impossible to achieve with solid silicone. Additionally, liquid silicone offers superior clarity and transparency, making it a popular choice for optical applications and medical devices where visibility is essential.
In contrast, solid silicone excels in applications that demand exceptional tear resistance, abrasion resistance, and long-term durability. Its non-flowable nature ensures dimensional stability and resistance to deformation, even under high temperatures or harsh environments. Injection molding of solid silicone enables the production of parts with consistent mechanical properties, making it suitable for applications such as seals, gaskets, and components in the automotive and aerospace industries.
Both solid and liquid silicone resins have unique advantages and are widely used in various industries. Manufacturers should make careful choices based on actual processing conditions and applications, such as the required performance of the product, the complexity of the design, and other factors. This plays a crucial role in ensuring the accuracy and consistency of part production, determining whether suppliers can produce high-quality components that meet modern industrial and customer demanding standards.
Applications Industries of Liquid Silicone Injection Molding
One of the most prominent industries leveraging liquid silicone injection molding is the medical field. From intricate surgical instruments to implantable devices, LSR components offer biocompatibility, sterilizability, and precision manufacturing. These qualities are essential for ensuring patient safety and enabling advanced medical procedures. Liquid silicone injection molding also plays a vital role in producing medical tubing, gaskets, and seals, contributing to the reliability and durability of life-saving equipment.
The automotive industry has also embraced liquid silicone injection molding for its ability to create high-performance components. Silicone gaskets, seals, and grommets are commonly found in engines, transmissions, and various automotive systems, providing excellent resistance to extreme temperatures, vibrations, and chemical exposure. Additionally, LSR components are used in interior applications, such as instrument panel assemblies and decorative trim, enhancing both functionality and aesthetics.
Consumer electronics is another sector that heavily relies on liquid silicone injection molding. From smartphone cases and protective covers to wearable devices and remote controls, LSR components offer a combination of durability, grip, and shock absorption. The ability to produce intricate designs and textures through injection molding has made it a go-to solution for enhancing user experience and product appeal.
The kitchen and household appliance industry has also embraced liquid silicone injection molding for its versatility. Silicone gaskets, seals, and components are found in ovens, refrigerators, dishwashers, and other appliances, ensuring reliable performance and energy efficiency. Additionally, LSR is used in the production of kitchen utensils, bakeware, and food-grade containers, thanks to its non-toxic and heat-resistant properties.
Liquid silicone injection molding has also made significant inroads into the sports and leisure industry. From grip handles on exercise equipment to protective gear and footwear components, LSR offers a unique combination of flexibility, durability, and shock absorption. These properties are essential for ensuring athlete safety and enhancing performance during high-impact activities.
The aerospace and defense sectors have also recognized the value of liquid silicone injection molding. LSR components are used in aircraft interiors, sealing systems, and various aerospace applications due to their resistance to extreme temperatures, vibrations, and environmental conditions. Additionally, the precision and repeatability of injection molding make it suitable for producing critical components with stringent tolerances.
In the industrial and manufacturing sectors, liquid silicone injection molding is utilized for producing seals, gaskets, and other components that require chemical resistance, temperature stability, and durability. These components are found in various applications, including pumps, valves, and fluid handling systems, ensuring reliable and efficient operation in demanding environments.
The energy and power generation industries have also embraced liquid silicone injection molding for its ability to produce high-performance components. LSR components are used in solar panels, wind turbines, and other renewable energy systems, offering excellent weatherability and resistance to environmental factors. Additionally, silicone insulators and bushings are commonly found in electrical and power distribution systems, ensuring safe and reliable operation.
Finally, the transportation industry, including automotive, aerospace, and marine applications, has benefited from liquid silicone injection molding. LSR components are used in sealing systems, vibration dampeners, and various other applications where resistance to extreme temperatures, chemicals, and environmental conditions is essential. The ability to produce complex geometries and intricate designs through injection molding has further expanded the applications of LSR in this sector.
Most manufacturers believe that liquid silicone resin injection molding is an indispensable universal manufacturing process that can produce high-quality, durable, and precise components in various industries. Modern mold manufacturers are constantly improving and developing new technologies, so the demand for LSR materials will also continue to grow, which will drive progress in this field.
A Comprehensive Guide to Maintaining Silicone Rubber Molds
The preparation of molds for liquid silicone injection molding is the foundation for manufacturers to maintain. Before the start of each injection molding cycle, the manufacturer needs to thoroughly clean and rust the surface and interior of the mold. This step can ensure the surface smoothness and aesthetics of the final product, extend the service life of the mold, and improve production efficiency.
During the injection molding process, the mold endures immense pressure and heat, subjecting it to significant stress. To counteract this, regular inspections are paramount. Skilled technicians meticulously examine the mold for signs of wear, such as cracks, deformities, or surface imperfections. Early detection of these issues allows for timely repairs or replacements, minimizing downtime and costly production delays.
Lubrication plays a pivotal role in maintaining silicone rubber molds. The application of specialized mold release agents not only facilitates the smooth ejection of molded parts but also protects the mold’s surface from abrasion and chemical degradation. Choosing the appropriate lubricant and adhering to the recommended application protocols is crucial to ensure optimal performance and longevity.
Temperature control is another critical aspect of mold maintenance. Silicone rubber molds are designed to withstand high temperatures, but excessive or uneven heat exposure can lead to warping, discoloration, or premature degradation. Implementing precise temperature monitoring systems and adhering to recommended operating temperatures is essential to maintain the mold’s structural integrity and dimensional accuracy.
In addition to these preventive measures, regular mold storage practices play a vital role in preserving the mold’s condition. Proper storage techniques, such as keeping the mold in a cool, dry environment and protecting it from physical damage, can significantly extend its lifespan and ensure consistent performance over multiple production cycles.
The maintenance practices of the manufacturer can fully utilize the injection molding ability of liquid silicone. Adhering to these guidelines will greatly improve product quality, reduce scrap rates and defects, prevent unplanned downtime, and accelerate the injection molding process.