Home > Injection Molding > ABS Injection Molding
ABS Injection Molding
ABS injection molding technology, with its advantages of high efficiency, flexibility, and versatility, has been applied by many mold suppliers in fields such as automobiles, aerospace, and industry.
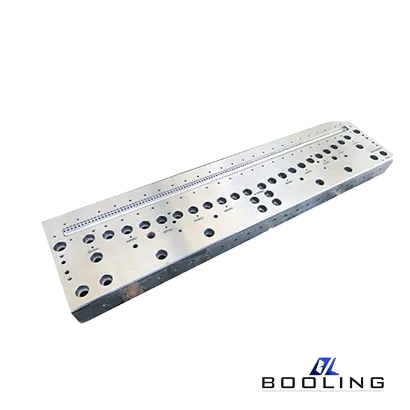
ABS Injection Molding
- Heat Resistant ABS Injection Molding
- Injection Molding of Matte ABS
- Low Odor ABS Injection Molding
- Electroplated ABS Injection Molding
ABS Injection Molding Capabilities
Injection molding is a commonly used modern manufacturing process, and in more precise injection molding, ABS is a commonly used material.
·
US
Metric
ABS
59 in. x 51.2 in. x 17.7 in.
1500mm x 1300mm x 450mm
*ABS plastic has excellent physical and chemical properties. It is very easy to process and has a low melting point, making it suitable for plastic injection molding and 3D printing processes.
ABS Injection Molding Material
ABS injection molding materials are copolymers composed of acrylonitrile, butadiene, and styrene, and their contents can be changed arbitrarily to produce various resin materials.
Material
- ABS
The Advantage of ABS Injection Molding
The advantages of ABS injection molding make it a preferred choice for many manufacturers seeking durable, versatile, and cost-effective plastic components. Its combination of strength, energy efficiency, and chemical resistance supports a wide range of applications across different sectors
Advantage:
- Easy to Stain
- Good Impact Resistance
- Not Easily Combustible
- Good Weather Resistance
- Good Liquidity
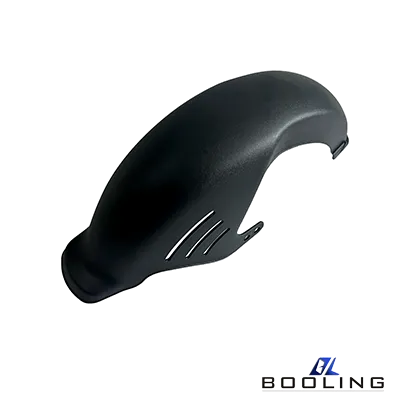
Application of ABS Injection Molding
ABS injection molding products are often used in furniture and electrical appliances to manufacture TV casings, washing machine panels, etc; In electronic products, it is often used to manufacture computer casings, keyboards, etc; In automotive components, it is often used to manufacture automotive dashboards, headlights, etc; In medical device manufacturing, it is often used to manufacture surgical instruments, etc; In addition, it is often used in door frames, toys, and sports equipment in building materials.
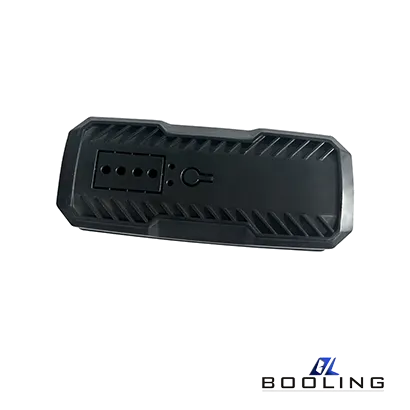
Guidelines for ABS Injection Molding
The main steps in ABS injection molding are material processing and mold manufacturing.
ABS Injection Molding Guide
ABS Injection Molding
ABS injection molding technology, with its advantages of high efficiency, flexibility, and versatility, has been applied by many mold suppliers in fields such as automobiles, aerospace, and industry. This process can combine the excellent properties of acrylonitrile butadiene styrene (ABS) materials with the precision of injection molding technology to produce various high-quality plastic parts.
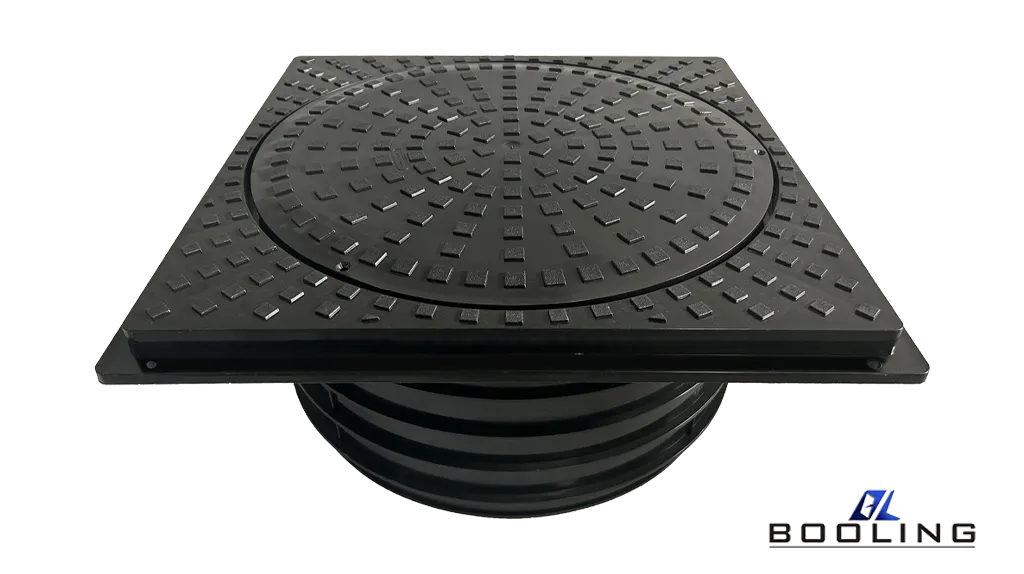
Advantages of ABS Material
ABS injection molding technology can achieve complex designs, precise tolerances, diverse product colors, and smooth surfaces, making it the preferred choice for many industries. In the field of injection molding, ABS (acrylonitrile butadiene styrene) has become a widely used and highly sought-after material by consumers and manufacturers. This makes it necessary for manufacturers to conduct comprehensive and in-depth discussions on this technology and material.
One of the standout features of ABS is its exceptional toughness and impact resistance. This thermoplastic material possesses an inherent ability to withstand substantial forces and impacts without compromising its structural integrity. In injection molding, ABS components exhibit remarkable resilience, making them ideal for applications where durability and shock absorption are paramount, such as automotive parts, protective gear, and consumer electronics.
ABS excels in maintaining dimensional stability during and after the injection molding process. Its low shrinkage rate ensures that molded parts retain their intended shape and size with high precision. This characteristic is particularly advantageous in applications that demand tight tolerances and intricate designs, such as medical devices, precision instruments, and intricate mechanical components.
ABS offers a wide range of coloring and finishing possibilities, allowing for customization and aesthetic appeal. Through injection molding, ABS can be easily colored with various pigments or dyes, enabling the production of vibrant and visually appealing products. Additionally, ABS surfaces can be polished, painted, or plated, providing a multitude of finishing options to meet diverse design requirements.
ABS is highly compatible with injection molding processes, making it a cost-effective material choice. Its excellent flow properties and low processing temperatures facilitate efficient and streamlined production. Furthermore, ABS is relatively inexpensive compared to other engineering plastics, contributing to cost savings without compromising performance.
Applications of ABS Injection Molding
The automotive industry has embraced ABS injection molding for its ability to produce lightweight yet durable components. From interior trim pieces and dashboard assemblies to exterior body panels and bumpers, ABS injection-molded parts contribute to enhanced vehicle safety, aesthetics, and fuel efficiency. The material’s impact resistance and ability to withstand harsh environmental conditions make it a preferred choice for automotive applications.
In the consumer electronics sector, ABS injection molding plays a pivotal role in manufacturing sleek and functional products. Computer housings, television casings, and mobile device enclosures are just a few examples where ABS injection molding excels. The material’s dimensional stability, ease of coloring, and resistance to heat and chemicals make it an excellent choice for these applications, ensuring long-lasting and visually appealing products.
The construction industry has also embraced ABS injection molding for various applications. From plumbing fixtures and electrical enclosures to window frames and decorative architectural elements, ABS injection-molded components offer durability, resistance to moisture and chemicals, and ease of installation. The material’s versatility allows for intricate designs and seamless integration into modern building structures.
In the medical field, ABS injection molding has proven invaluable for producing a wide range of medical devices and equipment. Surgical instrument handles, prosthetic components, and diagnostic equipment housings are among the many applications where ABS injection molding excels. The material’s biocompatibility, stabilizability, and resistance to chemicals make it a preferred choice for these critical applications, ensuring patient safety and product reliability.
The toy and recreational industry has long recognized the benefits of ABS injection molding. From action figures and building blocks to sports equipment and playground structures, ABS injection-molded products offer durability, vibrant colors, and intricate detailing. The material’s impact resistance and ability to withstand outdoor conditions make it an ideal choice for toys and recreational products designed for both indoor and outdoor use.
While ABS injection molding offers numerous advantages, it is essential to consider the environmental impact of plastic production and disposal. Efforts are underway to develop more sustainable practices, such as incorporating recycled ABS into injection molding processes and exploring biodegradable alternatives. By embracing responsible manufacturing and disposal methods, the benefits of ABS injection molding can be enjoyed while minimizing environmental harm.
The versatility and effectiveness of ABS injection molding technology have been well-validated in a wide range of industries. ABS injection molding technology will continue to provide manufacturers and customers with higher quality and cost-effective products, whether it is in the automotive and electronic appliance fields, as well as in medical, construction, and entertainment applications. Modern technology and sustainable development are constantly advancing, and demand is also increasing, making ABS injection molding a more important manufacturing technology.
What Steel Materials Can be Used for ABS Injection Molds
In the field of plastic injection molding, ABS (acrylonitrile butadiene styrene) has become a prominent material in the production of various products. ABS injection molds are key tools for shaping and forming these multifunctional plastic components. How to choose the materials for making ABS injection molds is a matter of caution and priority for manufacturers, as it directly affects the performance and service life of the molds, as well as the quality and accuracy of the final products.
When it comes to ABS injection molds, the steel material must possess exceptional mechanical properties to withstand the high pressures and temperatures involved in the molding process. Stainless steel and tool steel are two primary categories of materials that are commonly used for ABS injection molds. These materials offer a unique combination of strength, hardness, and corrosion resistance, making them well-suited for the demanding conditions of injection molding.
Stainless steel, particularly grades such as 420 and 440C, are popular choices for ABS injection molds. These steels exhibit excellent corrosion resistance, which is essential when dealing with high temperatures and potential chemical interactions during the molding process. Additionally, stainless steel offers good wear resistance, ensuring that the mold can withstand repeated cycles of injection and ejection without excessive wear or deformation.
Tool steels, on the other hand, are renowned for their exceptional hardness and wear resistance. These steels are specifically designed for applications that require high strength and durability. Common tool steel grades used for ABS injection molds include H13, S7, and D2. These materials can be heat-treated to achieve the desired hardness levels, ensuring that the mold can withstand the high pressures and abrasive nature of the ABS material during the injection molding process.
When selecting the appropriate steel material for ABS injection molds, it is essential to consider factors such as the complexity of the part design, the required surface finish, and the production volume. For intricate designs or high-volume production runs, tool steels like H13 or D2 may be preferred due to their superior wear resistance and ability to maintain dimensional accuracy over an extended period.
In addition to the steel material itself, the surface treatment and coatings applied to ABS injection molds can significantly enhance their performance and longevity. Techniques such as nitriding, chromium plating, or applying specialized coatings can improve wear resistance, reduce friction, and facilitate easier part ejection, ultimately extending the mold’s lifespan and improving the quality of the molded ABS components.
Choosing the appropriate steel raw materials for ABS injection molds is the first and most crucial step in the process. Manufacturers need to consider the mechanical, chemical, and wear resistance required for injection mold production, as well as the actual processing and production environment. After selecting the appropriate steel, manufacturers need to perform appropriate surface treatment on the steel to ensure the production of high-quality ABS molded parts while maximizing the efficiency of the injection molding process and the lifespan of the mold.
ABS Plastic Injection Molding Process
One of the primary considerations in the ABS injection molding process is temperature control. ABS plastic exhibits a relatively narrow processing window, necessitating precise temperature management throughout the various stages, including barrel heating, mold temperature, and cooling cycles. Improper temperature settings can lead to issues such as warpage, sink marks, or incomplete filling, compromising the quality and dimensional accuracy of the final product.
Another critical aspect to consider is the selection of appropriate injection molding parameters. These parameters encompass factors such as injection pressure, injection speed, holding pressure, and cooling time. Striking the right balance among these variables is essential to ensure consistent part quality, minimize defects, and optimize cycle times. Experienced molders often rely on empirical data and simulations to fine-tune these parameters for each unique application.
The design of the mold itself plays a pivotal role in the ABS plastic injection molding process. Factors such as gate location, runner system design, and cooling channel placement can significantly impact the flow behavior of the molten ABS plastic, potentially influencing part quality and cycle times. Collaboration between design engineers and molding experts is crucial to ensure that the mold design aligns with the specific requirements of the application and the material properties.
In addition to the technical considerations, the ABS plastic injection molding process also necessitates a thorough understanding of the material’s behavior during the molding cycle. ABS plastic is known for its tendency to exhibit molecular orientation and residual stresses, which can impact the mechanical properties and dimensional stability of the final product. Proper drying procedures and careful selection of processing aids or additives may be required to mitigate these effects and achieve the desired performance characteristics.
The injection molding of ABS plastic also presents unique challenges when it comes to part ejection and post-mold operations. Due to its inherent rigidity and potential for static charge buildup, ABS plastic components may require specialized ejection mechanisms or surface treatments to facilitate smooth ejection and prevent defects such as part sticking or surface imperfections.
As the demand for sustainable and environmentally friendly practices continues to grow, the ABS plastic injection molding process has adapted to incorporate recycled and bio-based materials. While these materials offer promising alternatives, they may require adjustments to processing parameters and mold designs to accommodate their unique properties and ensure consistent part quality.
Throughout the ABS plastic injection molding process, quality control and monitoring are paramount. Implementing robust quality assurance protocols, such as in-line inspection systems, statistical process control (SPC), and regular material testing, can help identify and address potential issues promptly, minimizing waste and ensuring consistent product quality.
ABS plastic injection molding is a complex and multifaceted molding process, and manufacturers need to have a deep understanding of its process parameters, material characteristics, and structural design. By combining these factors with the professional competence of designers, we can fully utilize the full potential of ABS plastics to produce high-quality, durable, and long-life products to meet the development and usage needs of various industries.