Home > 3D Printing Service > Carbon Fiber 3D Printing
Carbon Fiber 3D Printing
Carbon fiber 3D printing combines the exceptional properties of carbon fiber with the versatility and precision of 3D printing, This technology enables the production of high-strength.
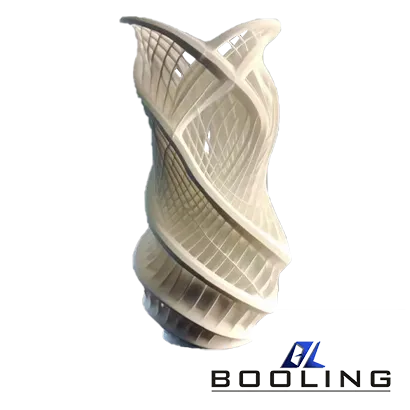
Carbon Fiber 3D Printing
High Strength-to-Weight Ratio
Create Complex Shapes
- Enhanced Mechanical Properties
Carbon Fiber 3D Printing Capabilities
Carbon fiber-reinforced parts are exceptionally strong and lightweight.
·
US
Metric
Carbon Fiber
47.2in. x 31.4 in. x 23.6 in.
1200mm x 800mm x600mm
*Carbon fiber 3D printing has the characteristic of high precision.
Carbon Fiber 3D Printing Material
Parts are printed with carbon fiber composite materials for carbon fiber 3D printing and exhibit high tensile strength, stiffness, impact resistance, heat resistance, and chemical resistance.
Material
- Carbon Fiber
The Advantages of Carbon Fiber 3D Printing
Carbon fiber 3D printin utilizes a composite material made from polymer and chopped carbon fiber, resulting in parts that are not only lightweight but also exceptionally strong and durable.
Advantage:
- Strong mechanical performance
- Fast time
- Customized design
- Design diversity
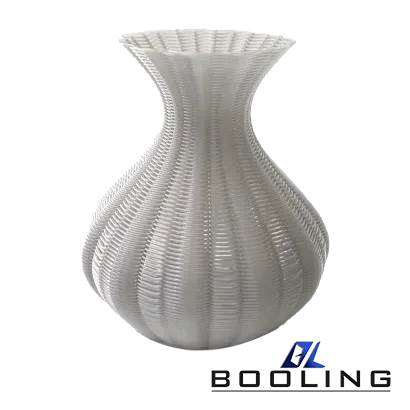
Application of Carbon Fiber 3D Printing
Carbon fiber 3D printing technology enables the production of high-strength, lightweight parts with complex geometries, making it ideal for a wide range of applications in industries such as aerospace, automotive, defense, and consumer goods.
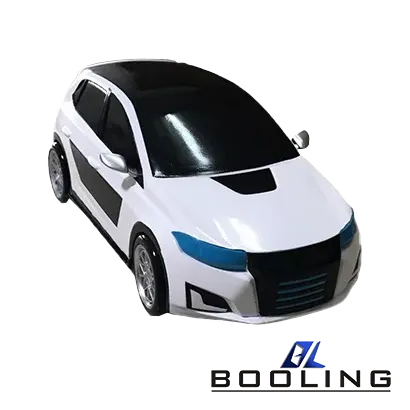
Guidelines for Carbon Fiber 3D Printing
Carbon fiber 3D printing is a unique printing technology.
Carbon Fiber 3D Printing
Carbon Fiber 3D Printing
Carbon fiber 3D printing combines the exceptional properties of carbon fiber with the versatility and precision of 3D printing, This technology enables the production of high-strength, lightweight parts with complex geometries, making it ideal for a wide range of applications in industries such as aerospace, automotive, defense, and consumer goods.
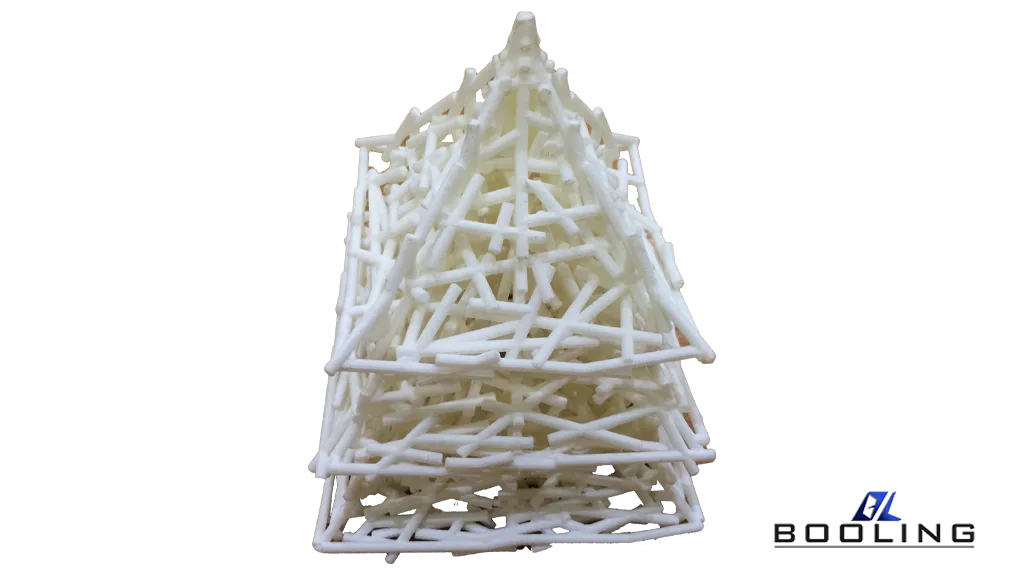
Principles of Carbon Fiber 3D Printing
Carbon fiber 3D printing involves the use of carbon fiber-reinforced materials to create parts with enhanced mechanical properties. There are two primary methods for incorporating carbon fiber into 3D printed parts: chopped fiber and continuous fiber.
1. Chopped Fiber Printing
Chopped fiber printing involves mixing short carbon fibers with a polymer matrix. These fibers are typically a few millimeters in length and are distributed throughout the material, providing improved strength and stiffness. This method is compatible with various 3D printing technologies, including Fused Deposition Modeling (FDM) and Selective Laser Sintering (SLS).
2. Continuous Fiber Printing
Continuous fiber printing embeds long strands of carbon fiber into the polymer matrix during the printing process. This method offers superior mechanical properties compared to chopped fiber printing, as the continuous fibers provide reinforcement along the entire length of the part. Continuous fiber printing is typically performed using specialized 3D printers designed to handle the unique requirements of this process.
Advantages of Carbon Fiber 3D Printing
Carbon fiber 3D printing offers several key advantages over traditional manufacturing methods and other 3D printing materials:
1.High Strength-to-Weight Ratio
Carbon fiber-reinforced parts are exceptionally strong and lightweight, making them ideal for applications where weight reduction is critical, such as in aerospace and automotive industries.
2.Enhanced Mechanical Properties
Parts printed with carbon fiber composites exhibit high tensile strength, stiffness, and resistance to impact, heat, and chemicals.
3.Design Flexibility
3D printing allows for the creation of complex geometries and intricate designs that would be difficult or impossible to achieve with traditional manufacturing methods.
4.Reduced Production Time and Costs
3D printing can significantly reduce lead times and costs associated with mold making and machining, especially for low-volume production and prototyping.
5.Customization and Iteration
The ability to quickly iterate designs and produce custom parts on demand is a significant advantage for industries that require rapid prototyping and customization.
Types of Carbon Fiber 3D Printing
There are several types of carbon fiber 3D printing, each with its own set of characteristics and applications:
1.Fused Deposition Modeling (FDM)
FDM is one of the most common 3D printing technologies used for carbon fiber composites. In this process, a filament made of a polymer mixed with chopped carbon fibers is extruded through a heated nozzle and deposited layer by layer to build the part. FDM is suitable for producing strong, lightweight parts with good dimensional accuracy.
2.Selective Laser Sintering (SLS)
SLS uses a laser to sinter powdered material, including carbon fiber-reinforced nylon powders, layer by layer to create the final part. SLS is known for its ability to produce parts with complex geometries and excellent mechanical properties.
3.Continuous Fiber Fabrication (CFF)
CFF is a specialized 3D printing technology that embeds continuous carbon fibers into a polymer matrix during the printing process. This method provides superior mechanical properties compared to chopped fiber printing and is ideal for applications requiring maximum strength and durability.
Methods of Carbon Fiber 3D Printing
The methods used in carbon fiber 3D printing can be broadly categorized into two main approaches: direct 3D printing and the use of 3D printed molds for traditional carbon fiber fabrication.
Direct 3D Printing
Direct 3D printing involves the use of carbon fiber-reinforced filaments or powders to create parts directly from a digital model. This method is suitable for producing functional prototypes, custom tools, and end-use parts with high strength and durability. The two main types of direct 3D printing are:
Chopped Fiber Printing: This method uses filaments or powders mixed with short carbon fibers. It is compatible with FDM and SLS technologies and offers good mechanical properties and design flexibility.
Continuous Fiber Printing: This method embeds continuous carbon fibers into the polymer matrix during the printing process, providing superior strength and stiffness. It requires specialized 3D printers designed for continuous fiber fabrication.
3D Printed Molds for Traditional Carbon Fiber Fabrication
3D printing can also be used to create molds for traditional carbon fiber fabrication methods, such as wet lay-up, prepreg lamination, and resin transfer molding (RTM). This approach combines the benefits of 3D printing with the established techniques of carbon fiber manufacturing, offering cost-effective and efficient solutions for producing high-quality carbon fiber parts.
Wet Lay-Up: In this method, sheets of carbon fiber are cut and pressed into a 3D printed mold, then painted with a liquid resin. The resin cures and solidifies, binding the sheets into the desired shape.
Prepreg Lamination: Prepreg carbon fiber sheets, which are pre-impregnated with resin, are placed into a 3D printed mold and formed into the final shape using heat and pressure. This method is highly repeatable and consistent, making it suitable for batch production.
Resin Transfer Molding (RTM): Dry carbon fiber is placed into a 3D printed mold, and resin is injected into the mold cavity under high pressure. This method is typically automated and used for larger-volume manufacturing.
Maintenance of Carbon Fiber 3D Printing Equipment
Proper maintenance of carbon fiber 3D printing equipment is essential to ensure consistent part quality and extend the lifespan of the machinery. Here are some key maintenance practices:
1. Regular Cleaning:
Keep the printer’s build platform, nozzles, and other components clean to prevent material buildup and ensure smooth operation. Use appropriate cleaning tools and solvents recommended by the printer manufacturer.
2. Nozzle Maintenance:
Carbon fiber-reinforced materials can be abrasive and may cause wear on the printer’s nozzle. Regularly inspect and replace the nozzle as needed to maintain print quality.
3. Calibration:
Periodically calibrate the printer to ensure accurate layer deposition and dimensional accuracy. This includes bed leveling, extruder calibration, and checking the alignment of the print head.
4. Lubrication:
Lubricate moving parts, such as rails and bearings, to reduce friction and wear. Use lubricants recommended by the printer manufacturer.
5. Software Updates:
Keep the printer’s firmware and software up to date to benefit from the latest features, improvements, and bug fixes.
6. Material Storage
Store carbon fiber-reinforced filaments and powders in a dry, cool environment to prevent moisture absorption, which can affect print quality. Use airtight containers with desiccants to maintain optimal material conditions.
Applications of Carbon Fiber 3D Printing
Carbon fiber 3D printing is used in a wide range of applications across various industries due to its exceptional properties and versatility:
1. Aerospace
Structural Components: Carbon fiber 3D printed parts are used in aircraft and spacecraft for structural components that require high strength and low weight.
Prototyping: Rapid prototyping of aerospace components allows for quick design iterations and testing, reducing development time and costs.
2. Automotive
Performance Parts: Carbon fiber 3D printed parts are used in high-performance vehicles for components such as brackets, housings, and aerodynamic parts.
Customization: The ability to produce custom parts on-demand is valuable for automotive manufacturers and aftermarket suppliers.
3. Defense
Lightweight Armor: Carbon fiber composites are used to create lightweight, high-strength armor for military vehicles and personnel.
Unmanned Systems: Carbon fiber 3D printed parts are used in drones and other unmanned systems for structural components and housings.
4. Consumer Goods
Sporting Equipment: Carbon fiber 3D printed parts are used in sporting goods such as bicycles, tennis rackets, and golf clubs for their strength and lightweight properties.
Electronics: Carbon fiber composites are used in consumer electronics for durable, lightweight housings and components.
5. Manufacturing
Tooling and Fixtures: Carbon fiber 3D printed tools and fixtures are used in manufacturing processes for their strength, durability, and customizability.
Replacement Parts: The ability to quickly produce replacement parts on-demand reduces downtime and maintenance costs in manufacturing operations.