Home > Injection Molding: Top 10 Most Common Plastics
Plastic Injection Molding
Plastic injection molded products have the characteristics of high cost-effectiveness and beautiful appearance, and are widely used by manufacturers in various fields such as automobiles, aerospace, daily necessities, industry, etc., penetrating into every corner of life.
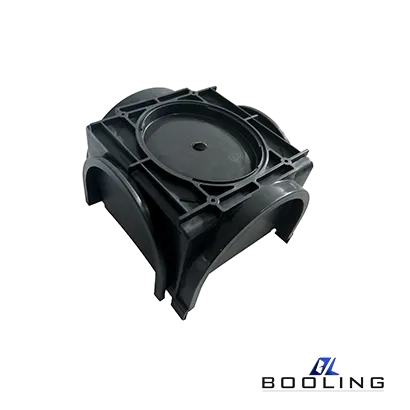
Injection Molding: Top 10 Most Common Plastics
Plastic injection molding is a widely adopted manufacturing process, from automotive parts to consumer goods and medical devices, injection-molded products are ubiquitous in our daily lives. This process lies in its ability to produce complex geometries with exceptional precision, consistency, and efficiency. At the heart of injection molding lies the selection of the right plastic material, which plays a crucial role in determining the performance, durability, and cost-effectiveness of the final product.
Thermoplastic Polyurethane (TPU)
Thermoplastic Polyurethane (TPU) is a family of engineering thermoplastics known for their excellent flexibility, abrasion resistance, and resilience. TPU injection molding offers a unique combination of properties that make them suitable for demanding applications.
- Properties and Advantages
– Excellent flexibility and elasticity
– High abrasion resistance and tear resistance
– Good chemical resistance and weather ability
– Excellent impact resistance and resilience
- Applications
– Automotive components (seals, gaskets, hoses)
– Industrial components (belts, rollers, linings)
– Footwear and sporting goods
– Medical devices and tubing
- Processing Considerations
– Requires careful drying to prevent moisture-related defects
– Susceptible to hydrolytic degradation at high temperatures
– Relatively high melt viscosity, requiring higher injection pressures and temperatures
Injection molding is a versatile manufacturing process that offers a wide range of plastic material options, each with its unique properties and characteristics. Injection molders should carefully evaluate factors such as mechanical properties, chemical resistance, thermal stability, and cost-effectiveness to ensure that the final product meets the required performance standards and production efficiency.
Thermoplastic Elastomers (TPE)
Thermoplastic Elastomers (TPE) are a family of flexible and resilient materials that combine the properties of thermoplastics and elastomers. TPE injection molding provides excellent flexibility, impact resistance, and ease of processing for products.
- Properties and Advantages
– Excellent flexibility and elasticity
– High impact resistance and tear resistance
– Good chemical resistance and weather ability
– Ease of processing and coloring
- Applications
– Automotive components (seals, gaskets, grips)
– Consumer products (grips, handles, over-molded components)
– Medical devices (tubing, seals, grips)
– Sporting goods and outdoor equipment
- Processing Considerations
– Requires careful drying to prevent moisture-related defects
– Susceptible to warpage and shrinkage, necessitating proper mold design and cooling
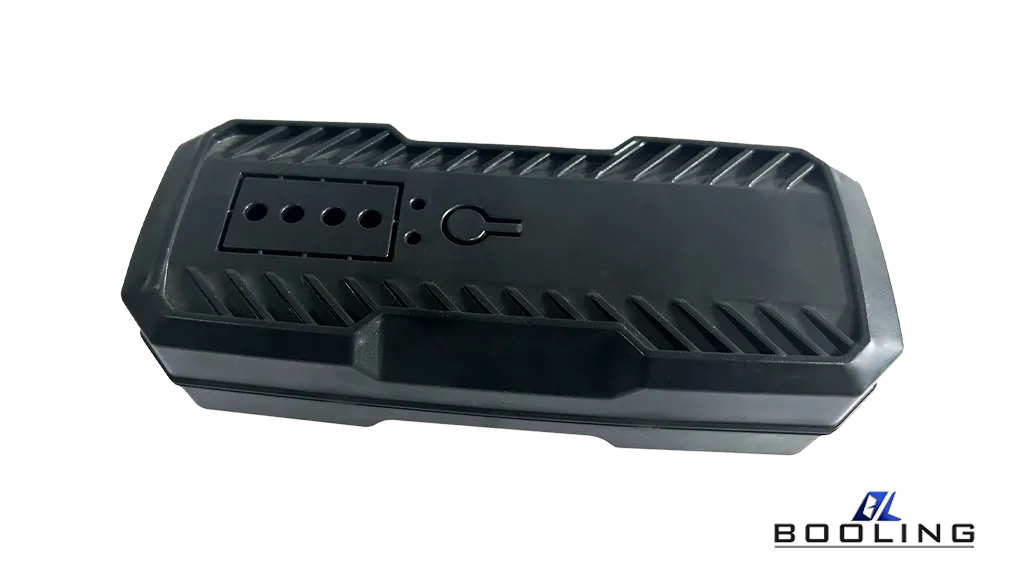
Polyethylene (PE)
Polyethylene (PE) is a thermoplastic polymer renowned for its excellent chemical resistance, moisture resistance, and electrical insulation properties. It is available in various densities, including high-density polyethylene (HDPE) and low-density polyethylene (LDPE), each with its unique characteristics.
- Properties and Advantages
– High impact strength and toughness
– Excellent chemical resistance to acids, bases, and solvents
– Good moisture resistance and electrical insulation properties
– Lightweight and cost-effective
- Applications
– Packaging materials (bottles, containers, films)
– Automotive components (fuel tanks, battery cases)
– Industrial piping and fittings
– Consumer products (toys, housewares)
- Processing Considerations
– Requires careful drying to prevent moisture-related defects
– Susceptible to warpage and shrinkage, necessitating proper mold design and cooling
– HDPE has a higher melt viscosity compared to LDPE, requiring higher injection pressures
Polypropylene (PP)
Polypropylene (PP) is a versatile and widely used thermoplastic polymer known for its excellent chemical resistance, high heat resistance, and good mechanical properties. Its lightweight nature and cost-effectiveness make it a popular choice for a wide range of applications.
- Properties and Advantages
– High stiffness and strength-to-weight ratio
– Excellent chemical resistance to acids, bases, and solvents
– Good heat resistance, with a melting point around 160°C (320°F)
– Excellent electrical insulation properties
– Recyclable and environmentally friendly
- Applications
– Automotive components (battery cases, bumpers, interior trim)
– Household products (containers, kitchenware, toys)
– Packaging materials (bottles, caps, closures)
– Consumer electronics (housings, enclosures)
- Processing Considerations
– Relatively low melt viscosity, allowing for easy flow and filling of complex molds
– Requires careful drying to prevent moisture-related defects
– Susceptible to warpage and shrinkage, necessitating proper mold design and cooling
Polycarbonate (PC)
Polycarbonate (PC) is an engineering thermoplastic known for its exceptional impact resistance, transparency, and heat resistance. Its unique combination of properties makes it suitable for a wide range of demanding applications.
- Properties and Advantages
– High impact strength and toughness
– Excellent heat resistance, with a glass transition temperature around 150°C (302°F)
– Excellent optical clarity and transparency
– Good dimensional stability and rigidity
- Applications
– Automotive components (headlights, taillights, instrument panels)
– Consumer electronics (housings, displays, lenses)
– Medical devices (surgical instruments, sterilization trays)
– Safety equipment (helmets, visors, safety glasses)
- Processing Considerations
– Requires careful drying to prevent moisture-related defects
– Susceptible to stress cracking and chemical attack by certain solvents
– Relatively high melt viscosity, requiring higher injection pressures and temperatures
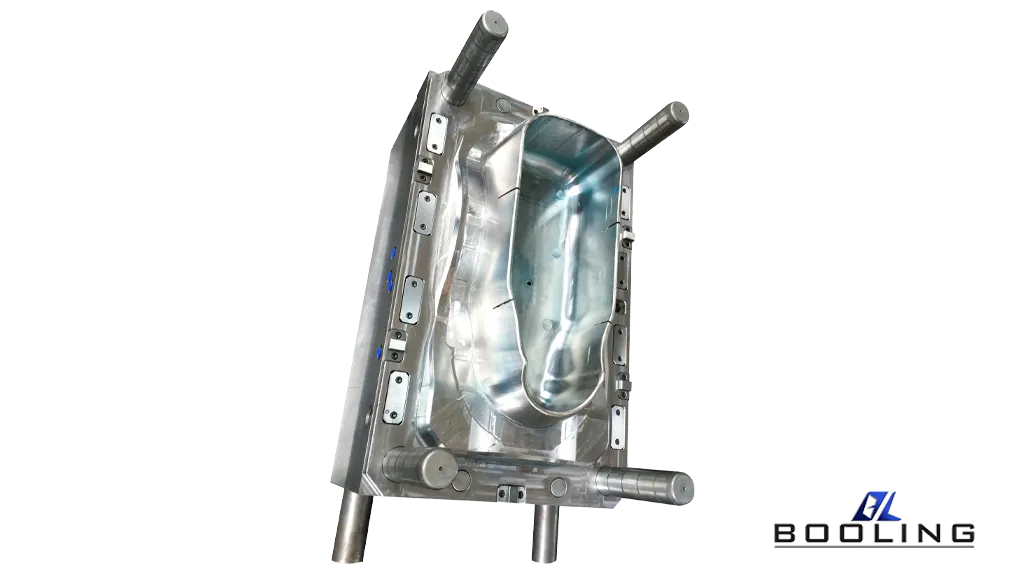
Nylon (Polyamide)
Nylon, or polyamide, is a family of engineering thermoplastics known for their excellent strength, toughness, and wear resistance. Different types of nylon, such as Nylon 6 and Nylon 6,6, offer unique properties tailored to specific applications.
- Properties and Advantages
– High tensile strength and impact resistance
– Excellent wear resistance and abrasion resistance
– Good chemical resistance to oils, greases, and solvents
– Good dimensional stability and rigidity
- Applications
– Automotive components (gears, bearings, bushings)
– Industrial components (rollers, cams, sprockets)
– Electrical and electronic components (connectors, insulators)
– Sporting goods and outdoor equipment
- Processing Considerations
– Requires careful drying to prevent moisture-related defects
– Susceptible to warpage and shrinkage, necessitating proper mold design and cooling
– Relatively high melt viscosity, requiring higher injection pressures and temperatures
Acetal (Polyoxymethylene, POM)
Acetal, also known as polyoxymethylene (POM), is an engineering thermoplastic renowned for its excellent dimensional stability, stiffness, and low friction properties. Its unique combination of properties makes it suitable for precision applications.
- Properties and Advantages
– High stiffness and dimensional stability
– Excellent wear resistance and low friction properties
– Good chemical resistance to solvents and fuels
– Good electrical insulation properties
- Applications
– Automotive components (gears, bearings, fuel system components)
– Industrial machinery components (cams, rollers, guides)
– Consumer products (zippers, fasteners, hinges)
– Medical devices and instruments
- Processing Considerations
– Requires careful drying to prevent moisture-related defects
– Susceptible to thermal degradation at high temperatures
– Relatively high melt viscosity, requiring higher injection pressures and temperatures
Polystyrene (PS)
Polystyrene (PS) is a thermoplastic polymer known for its excellent clarity, ease of processing, and cost-effectiveness. Its versatility and affordability make it a popular choice for various applications.
- Properties and Advantages
– Excellent clarity and transparency
– Good stiffness and dimensional stability
– Good electrical insulation properties
– Cost-effective and easy to process
- Applications
– Packaging materials (food containers, cups, trays)
– Consumer products (toys, housewares, appliance components)
– Construction materials (insulation boards, panels)
– Medical devices and disposables
- Processing Considerations
– Relatively low heat resistance and impact strength
– Susceptible to environmental stress cracking
– Requires careful mold design and cooling to prevent warpage and shrinkage
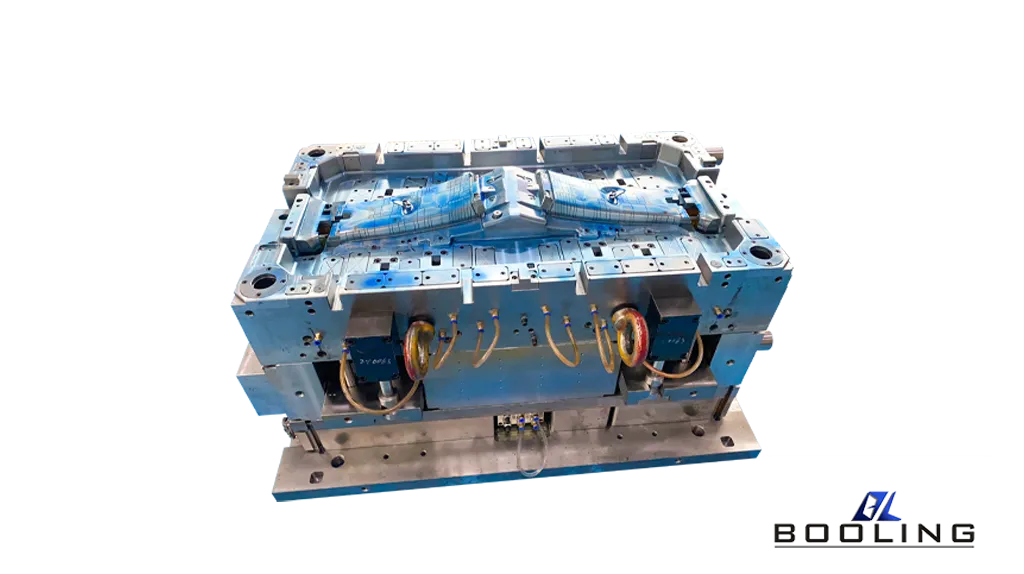
Polyethylene Terephthalate (PET)
clarity, chemical resistance, and barrier properties. Its versatility and recyclability make it a popular choice for various applications.
- Properties and Advantages
– Excellent clarity and transparency
– Good chemical resistance and barrier properties
– High strength and stiffness
– Recyclable and environmentally friendly
- Applications
– Packaging materials (bottles, containers, films)
– Consumer products (housewares, appliance components)
– Industrial components (electrical insulators, bearings)
– Automotive components (interior trim, lighting components)
- Processing Considerations
– Requires careful drying to prevent moisture-related defects
– Susceptible to hydrolytic degradation at high temperatures
– Relatively high melt viscosity, requiring higher injection pressures and temperatures
Acrylonitrile Butadiene Styrene (ABS)
Acrylonitrile Butadiene Styrene (ABS) is a widely used thermoplastic known for its excellent impact resistance, toughness, and ease of processing. Its versatility and cost-effectiveness make it a popular choice for a wide range of applications.
- Properties and Advantages
– High impact strength and toughness
– Good heat resistance, with a glass transition temperature around 105°C (221°F)
– Excellent dimensional stability and rigidity
– Good chemical resistance to acids, bases, and solvents
- Applications
– Automotive components (interior trim, dashboard components)
– Consumer electronics (housings, enclosures, computer peripherals)
– Household products (appliance housings, toys)
– Construction materials (pipes, fittings)
- Processing Considerations
– Requires careful drying to prevent moisture-related defects
– Susceptible to warpage and shrinkage, necessitating proper mold design and cooling
– Relatively high melt viscosity, requiring higher injection pressures
Related News
Applied’s expertise in modifying materials at atomic levels and on an ihdustrial scaleenables our customers to transform possibilities into reality.