Home > What is Stretch Blow Molding?
Plastic Blow Molding
The principle of plastic blow molding mainly involves three processes: blank forming, blow molding bulging, and product cooling. This process method is suitable for manufacturing hollow plastic products with complex shapes and high dimensional accuracy requirements, and is a blessing for high-precision industries such as the automotive industry.
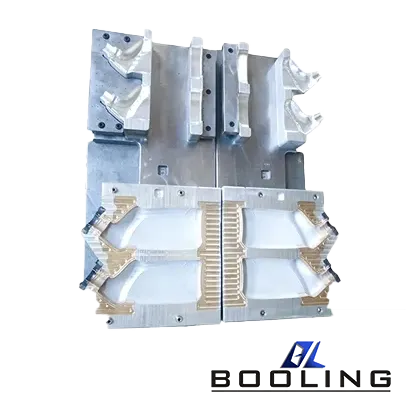
In the world of plastic manufacturing, stretch blow molding has emerged as a highly versatile and efficient process for producing hollow plastic containers and bottles. This technology combines the principles of extrusion, injection molding, and blow molding to create lightweight, durable, and cost-effective products. From water bottles and beverage containers to automotive fuel tanks and pharmaceutical vials, stretch blow molding has become an indispensable manufacturing technique across various industries.
Stretch blow molding is a two-stage process that involves the formation of a preform, followed by the stretching and blowing of the preform into the desired container shape. This process is particularly suitable for producing containers made from polyethylene terephthalate (PET), a widely used thermoplastic polymer known for its strength, transparency, and barrier properties.
The stretch ABS blow molding process can be further divided into two main categories: one-stage and two-stage processes.
1.One-Stage Stretch Blow Molding
In the one-stage stretch blow molding process, the preform is injection molded, conditioned to the appropriate temperature, and then immediately transferred to the blow mold, where it is stretched and inflated to form the final container shape. This process is often used for producing smaller containers, such as those for pharmaceuticals, cosmetics, and personal care products.
2. Two-Stage Stretch Blow Molding
The two-stage stretch blow molding process involves the injection molding of preforms, which are then stored and reheated before being transferred to the blow mold. This process is commonly used for producing larger containers, such as those for beverages, food products, and household chemicals. The two-stage process allows for greater flexibility in production scheduling and inventory management.
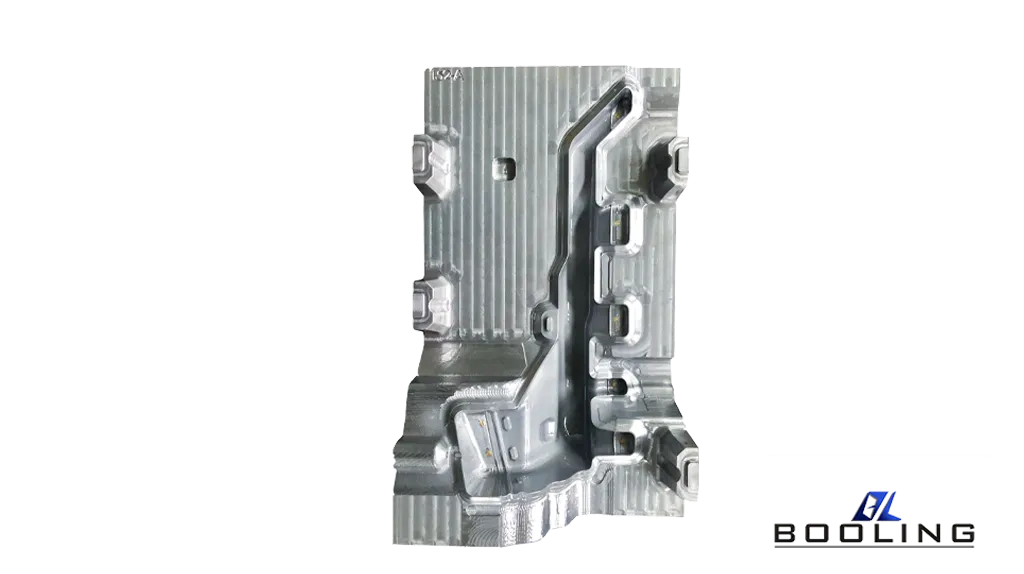
The Stretch Blow Molding Process
The stretch blow molding process consists of several key steps, each playing a crucial role in the production of high-quality plastic containers.
- Preform Production
The first step in the stretch blow molding process is the production of the preform. A preform is a test-tube-shaped plastic article that serves as the starting point for the final container.
In the injection molding stage, molten PET resin is injected into a preform mold, where it cools and solidifies into the desired preform shape. The preform typically has a threaded neck finish and a thick-walled body, which will be stretched and blown into the final container shape.
- Preform Conditioning (Optional)
In the two-stage stretch blow molding process, the preforms are stored and may undergo a conditioning step before being transferred to the blow mold. This step involves reheating the preforms to a specific temperature, typically between 90°C and 110°C (194°F and 230°F), to ensure optimal stretching and blowing characteristics.
- Preform Transfer and Loading
The conditioned preforms are then transferred to the blow mold, where they are loaded into the mold cavities. This step is automated and precisely controlled to ensure accurate positioning and alignment of the preforms within the mold.
- Stretching and Blowing
Once the preforms are loaded into the mold cavities, the stretching and blowing process begins. A stretch rod is inserted into the preform, and the preform is stretched both axially (lengthwise) and radially (widthwise) to the desired dimensions.
Simultaneously, high-pressure air is injected into the stretched preform, causing it to expand and conform to the shape of the mold cavity. This process is known as blow molding, and it is responsible for creating the final container shape.
- Cooling and Ejection
After the stretching and blowing stages, the newly formed container is cooled within the mold cavity. This cooling process is essential for ensuring the container’s dimensional stability and strength.
Once the container has cooled sufficiently, the mold opens, and the finished product is ejected from the mold cavity, ready for further processing or packaging.
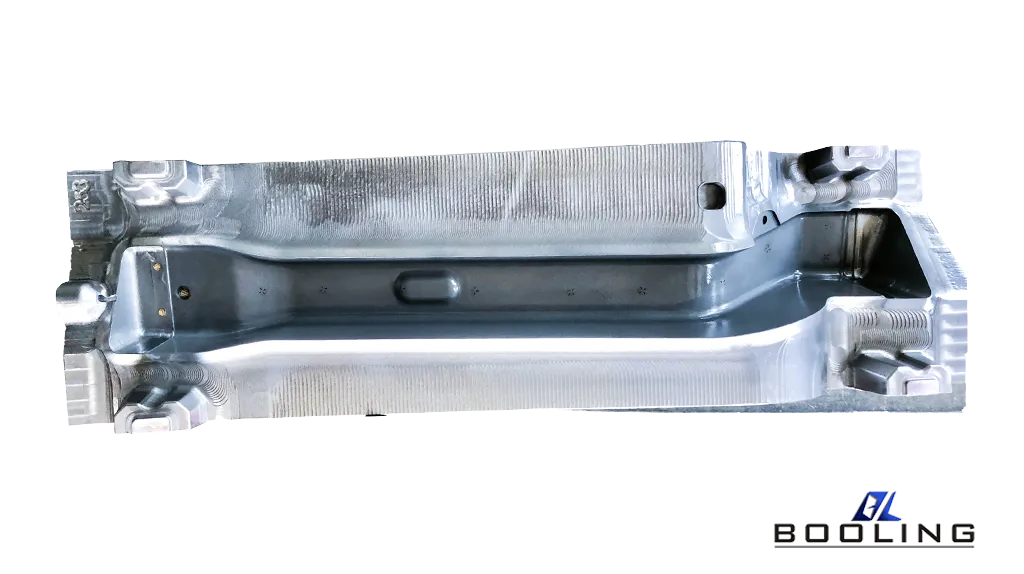
Advantages of Stretch Blow Molding
Stretch blow molding offers several advantages that have contributed to its widespread adoption across various industries:
- Lightweight and Durable Containers
One of the primary advantages of stretch blow molding is its ability to produce lightweight yet durable containers. The biaxial orientation of the plastic molecules during the stretching process results in improved mechanical properties, such as increased strength, impact resistance, and barrier properties.
- Design Flexibility
Stretch blow molding allows for a wide range of container designs and shapes, from simple cylindrical bottles to complex, multi-layered containers with intricate geometries. This design flexibility enables manufacturers to create products that meet specific functional and aesthetic requirements.
- Material Efficiency
Stretch blow molding is a highly efficient process in terms of material usage. The preform’s thick-walled design and the subsequent stretching and blowing stages result in a uniform distribution of material throughout the container, minimizing waste and reducing overall production costs.
- High Production Rates
Modern stretch blow molding machines are capable of producing containers at high rates, making the process suitable for large-scale production. Automated systems and efficient cycle times contribute to increased productivity and cost-effectiveness.
- Barrier Properties
Containers produced through stretch blow molding can exhibit excellent barrier properties against gases, moisture, and other environmental factors. This characteristic is particularly important for products that require extended shelf life or protection from external contaminants, such as food and beverage containers, pharmaceuticals, and personal care products.
- Recyclability
PET, the primary material used in stretch blow molding, is highly recyclable. This characteristic aligns with the growing emphasis on sustainability and environmental responsibility in the manufacturing industry.
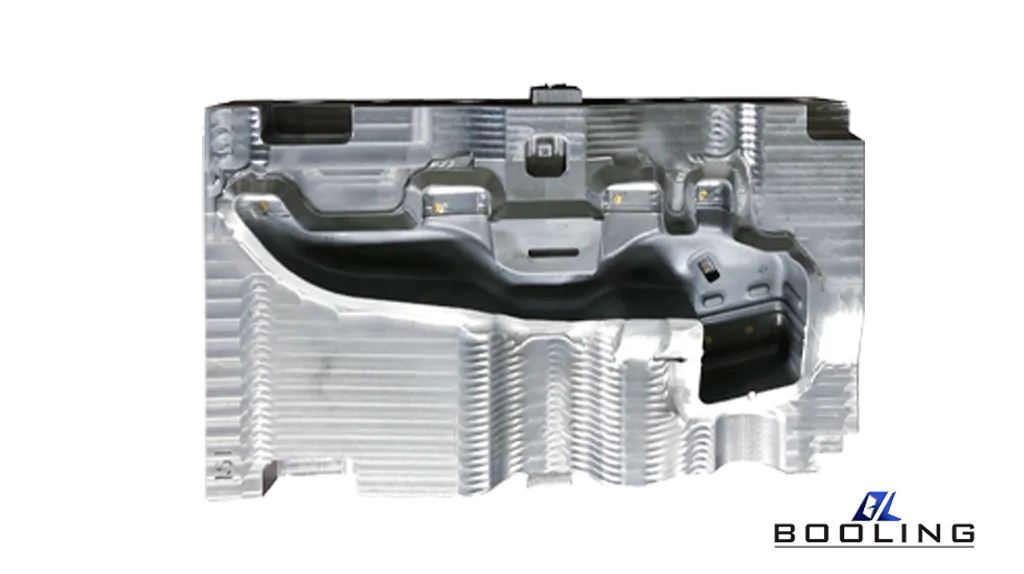
Applications of Stretch Blow Molded Products
Stretch blow molded products are found in a wide range of applications across various industries, including:
- Beverage Industry
The beverage industry is one of the largest consumers of stretch blow molded products. PET bottles for carbonated soft drinks, water, juices, and other beverages are commonly produced using this process, taking advantage of the lightweight, durable, and transparent nature of the containers.
- Food Packaging
Stretch blow-molded containers are widely used for packaging various food products, such as edible oils, sauces, and condiments. The barrier properties of PET help extend the shelf life of these products, while the lightweight design facilitates transportation and handling.
- Pharmaceutical and Healthcare
The pharmaceutical and healthcare industries rely on stretch blow molded containers for packaging and storing medications, supplements, and other healthcare products. The sterile and inert nature of PET, combined with its barrier properties, makes it an ideal choice for these applications.
- Personal Care and Cosmetics
Stretch blow-molded bottles and containers are commonly used for packaging personal care and cosmetic products, such as shampoos, lotions, and perfumes. The design flexibility of the process allows for the creation of visually appealing and ergonomic containers.
- Automotive Industry
In the automotive industry, stretch blow molded containers are used for various applications, including fuel tanks, windshield washer fluid reservoirs, and other fluid storage components. The lightweight and durable nature of these containers contributes to improved fuel efficiency and overall vehicle performance. Furthermore, in the automotive industry, ABS blow molding has the highest frequency of use.
- Industrial and Household Products
Stretch blow molded containers find applications in various industrial and household products, such as cleaning supplies, lubricants, and chemical storage containers. The versatility of the process allows for the production of containers with specific shapes, sizes, and material properties to meet diverse requirements.
Stretch blow molding is a versatile and efficient manufacturing process that has revolutionized the production of hollow plastic containers across various industries. From lightweight and durable beverage bottles to fuel-efficient automotive components, stretch blow molded products have become an integral part of daily lives.
Related News
Applied’s expertise in modifying materials at atomic levels and on an ihdustrial scaleenables our customers to transform possibilities into reality.