Home > Blow Molding|Plastic Molding Process
Plastic Blow Molding
Plastic blow molding is an important technical means for producing plastic products, which has significant theoretical and practical significance in optimizing technical design, shortening molding cycles, and improving product quality. It is widely used in daily production, containers, medical devices, electronic appliances, automobiles, and other fields.
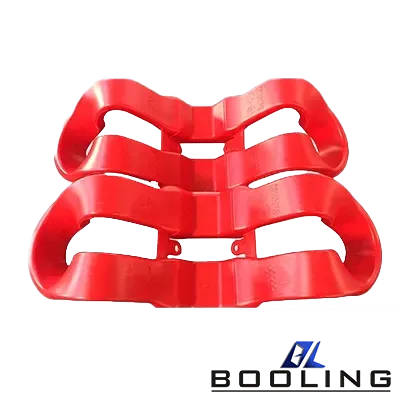
Blow Molding|Plastic Molding Process
Blow molding is placing the tube blank obtained by extrusion or injection molding into the corresponding mold, passing compressed air into the tube blank, and inflating it so that it adheres to the wall of the mold cavity. After cooling within a certain period of time, the mold is finally molded to obtain a hollow product. This process can be mainly used to produce various packaging containers such as bottles, pots, and barrels, as well as daily necessities and children’s toys.
Blow Molding Material Requirements
In this process, not all plastic raw materials are suitable for this method. The main reason is that the melt index is between 0.04 ~ 1.12. These raw materials are relatively excellent hollow blow molding materials, such as polyethylene, polyvinyl chloride, and polypropylene. , polystyrene, thermoplastic polyester, polycarbonate, polyamide, cellulose acetate, and polyacetal resin, among which polyethylene is the most widely used, ABS blow molding is often used to manufacture car tail fins, bumpers, etc.
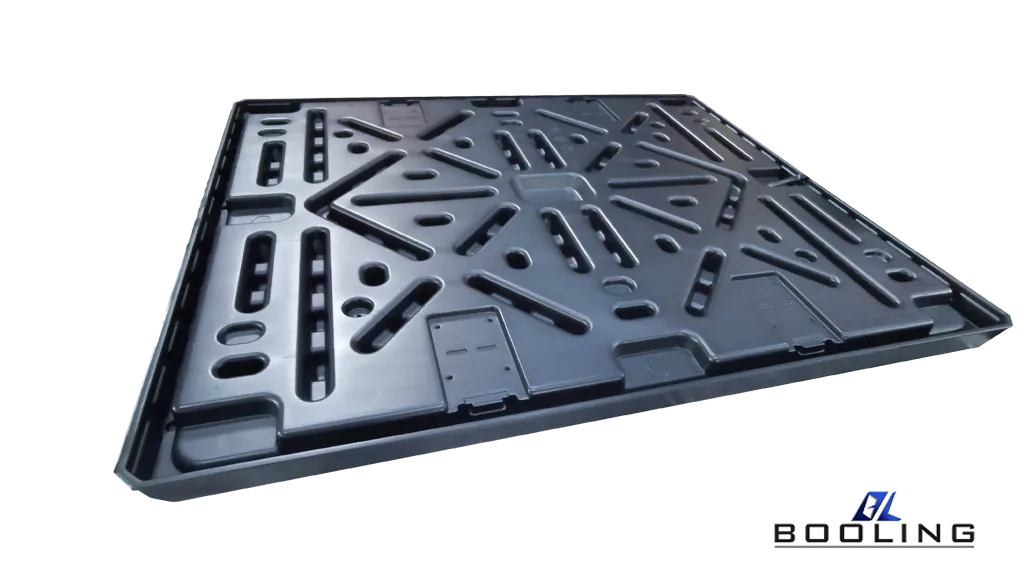
Blow Molding Process
The blow molding process includes three basic steps: parison molding, blow molding, and product cooling. The plastic is first processed into a molded blank (injection molding or extrusion), then the high-temperature parison is placed in the blow mold, and compression is injected into the parison. The air inflates it until it is close to the cavity wall, and the inflation pressure is maintained until the plastic part cools down and takes shape. The mold is then opened to obtain the hollow plastic part.
Blow molding is divided into injection blow molding, extrusion blow molding, stretch blow molding, and blown film methods;
- Injection Blow Molding
It mainly uses the injection molding method, which first makes the plastic into a bottomed parison, and then moves the parison to a blow mold to blow it into a hollow product. Its accuracy and cost are between extrusion blow molding and injection stretch blow molding, and it is suitable for producing 3 ml – 1-liter plastic (PE, HDPE) hollow containers.
Injection blow molding has significant advantages, mainly reflected in the fact that no waste is generated during the processing, the wall thickness of the product and the dispersion of materials can be well controlled, the molding precision of thin-necked products is high, and the product surface is very smooth.
Injection Blow Molding (IBM) Steps:
(1): The colloidal polymer is preheated and injected into the mold through the core rod, and the operating table is rotated 120° to the blow molding stage.
(2): Air is slowly injected into the mold through the mandrel, and the gel-like polymer prototype is cooled and solidified close to the inner wall of the mold.
(3): After waiting for complete cooling, the operating table rotates 120°, and the finished product is pushed out of the mold and transferred to the trimming link by the conveyor belt.
- Extrusion Blow Molding
This method mainly uses the extrusion method. First, the plastic is made into a bottomed parison, and then the parison is moved to the blow mold and blown into a hollow product. Extrusion blow molding is widely used in many blow molding factories, mainly because of its high production efficiency, low equipment cost, and wide selection of molds and machinery.
Extrusion Blow Molding (EBM) Steps
(1): Pour the polymer particles into the hard mold, and form a gel-like hollow columnar prototype through heating and continuous extrusion by the mandrel.
(2): When the hollow cylindrical prototype is extruded to a certain length, the molds on the left and right sides begin to close, and the top of the prototype is cut by a blade to a suitable length for a single piece. Air is injected into the prototype through the inflatable rod so that the prototype is cooled and solidified close to the inner wall of the mold. Form the desired shape.
(3): After waiting for cooling to complete, the molds on the left and right sides are opened and the parts are molded.
(4): Use repair tools to trim the edges of parts.
- Stretch Blow Molding
Stretch blow molding is a type of blow molding using biaxial directional stretching. The method is to first stretch the mold longitudinally and then blow it with compressed air to achieve transverse stretching. It is the process with the highest quality, precision, and cost among all blow molding processes, especially in the details of the bottle mouth. It is suitable for the manufacturing process of plastic containers with fine patterns on the surface and is suitable for the production of plastics between 3 ml and 1 liter (PE, HDPE ) hollow containers.
Stretch blow molding includes two methods: extrusion-stretch-blow molding and injection-stretch-blow molding. It is usually used by blow molding manufacturers to process biaxially oriented products, thereby reducing production costs and improving product performance. Stretch blow molding can greatly improve the transparency, impact strength, surface hardness, and rigidity of the product, and is suitable for blow molding of polypropylene and polyethylene terephthalate (PETP). Stretch blow molding includes injection parison directional stretch blow molding, extrusion parison directional stretch blow molding, multi-layer directional stretch blow molding, compression molding directional stretch blow molding, etc.
Steps of Injection Stretch Blow Molding (ISBM)
(1): The colloidal polymer is preheated and injected through the core rod to form a hollow sealed columnar prototype.
(2): The mandrel is taken out, the stretch rod is inserted, the molds on the left and right sides are closed, and the stretch rod is squeezed inside the gelatinous prototype, thereby elongating the polymer prototype longitudinally.
(3): The extension rod continues to elongate the gelatinous polymer prototype from the inside, and at the same time, the air is slowly injected through the extension rod, so that the gelatinous prototype fully fits the mold and is cooled and solidified.
(4): The left and right molds are opened, the completed plastic barrel is ejected by the extension rod, and it is completed.
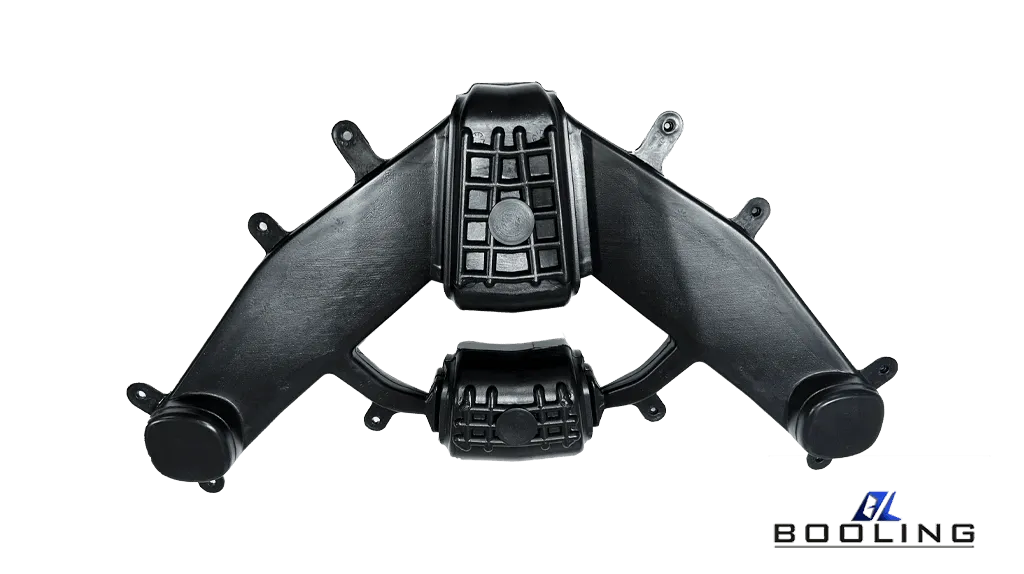
- Blown Film Method
There are many ways to blow thermoplastic films. The most common method is to use extrusion to extrude the plastic into a tube, and then use air blown into the tube to continuously expand it to a tubular film of a certain size. After cooling, Fold and roll into double-layer flat film. Plastic films can be manufactured by many methods, such as blow molding, extrusion, casting, calendering, casting, etc., but the blow molding method is the most widely used. This method is suitable for the manufacture of polyethylene, polyvinyl chloride, polyamide, and other films.
Blown Film Process
The material is plasticized and extruded through the equipment to form a pipe ring, which is blown and molded; then through cooling, traction, and coiling, the required product is finally obtained. In the blown film molding process, according to the different extrusion and pulling directions, it can be divided into three types: flat blowing, top blowing, and bottom blowing. This is the main molding process. Of course, there are also special blow molding methods, such as the above extrusion blowing method.
- Flat Extrusion and Upward Blowing Method
This method uses a right-angle machine head, that is, the discharging direction of the machine head is perpendicular to the extruder, and the extrusion pipe ring is upward. After it is pulled to a certain distance, it is clamped by a herringbone plate. The compressed air introduced from the bottom of the extruded tube is then Blown into a bubble tube, and its transverse size with the amount of compressed air, and its longitudinal size with the traction speed. After the bubble tube is cooled and shaped, a blown film can be obtained. The main plastic varieties suitable for the top-blowing method are PVC, PE, PS, PA, PVDC (vinylidene chloride), and EVOH.
Advantages: stable traction, small footprint, easy operation, large production folding diameter, suitable for producing film products of different thicknesses.
- Flat Extrusion and Blowing Method
This method uses a right-angle machine head, and the process in which the bubble tube is drawn out from the bottom of the machine head is called the flat extrusion down-blowing method. This method is especially suitable for raw materials with low viscosity and plastic films that require high transparency. Such as PP, PA, PVDC, and EVOH.
Advantages: There are no high requirements for the height of the factory building, which is conducive to film cooling, higher production efficiency, and can process plastics with greater fluidity.
- Flat Extrusion and Flat Blowing Method
The flat extrusion and flat-blowing machine head is a central type. This method uses a straight die head that is concentric with the extruder screw. The process in which the bubble tube and the center line of the machine head are on the same horizontal plane is called the flat extrusion and flat-blowing method. This method is only suitable for blowing. For small-diameter film products, such as LDPE, PVC, and PS films, the flat-blowing method is also suitable for the production of blown heat-shrinkable films.
Advantages: simple structure, relatively uniform film thickness, easy operation, easy film feeding, and can achieve a large inflation ratio.
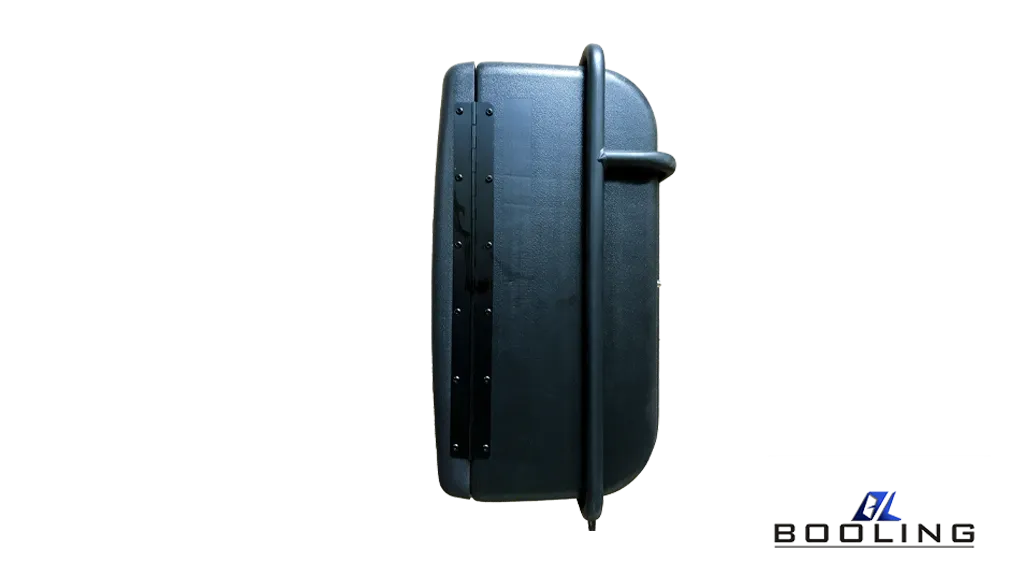
Related News
Applied’s expertise in modifying materials at atomic levels and on an ihdustrial scaleenables our customers to transform possibilities into reality.