Home > Injection Blow Molding | Bottle Manufacturing
HDPE Blow Molding
High density polyethylene (HDPE) is a thermoplastic resin with high crystallinity and non-polar properties. HDPE injection molded products have excellent acid and alkali resistance, low temperature resistance, as well as good mechanical strength such as flexibility, surface hardness, and tensile strength, and are widely used in the automotive industry.
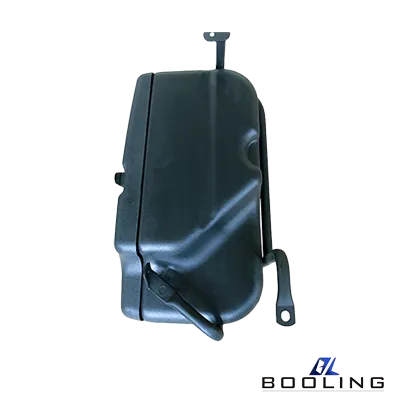
Injection Blow Molding | Bottle Manufacturing
In the world of plastic bottle production, injection blow molding stands out as a highly efficient and versatile manufacturing process. This technique combines the principles of injection molding and blow molding to create hollow plastic containers with exceptional precision, strength, and design flexibility. From small pharmaceutical vials to large beverage bottles, injection blow molding has become an indispensable method for producing high-quality plastic bottles across various industries.
Injection blow molding is a two-stage process that begins with the injection molding of a thick-walled, cylindrical preform. This preform is then transferred to a blow mold, where it is reheated and inflated with compressed air or gas to take the shape of the desired bottle. The stretching and blowing stages of this process impart enhanced mechanical properties and barrier characteristics to the final product.
The injection blow molding process offers several advantages over traditional plastic blow molding techniques, including:
- Precise Dimensional Control: The injection molding stage allows for tight control over the preform dimensions, resulting in consistent wall thickness and accurate bottle geometries.
- Design Flexibility: The ability to create complex bottle shapes, including intricate neck finishes, handles, and embossed features, makes injection blow molding highly versatile.
- Material Efficiency: The process minimizes material waste by utilizing the entire preform during the blow molding stage.
- Enhanced Barrier Properties: The biaxial orientation of the plastic molecules during the stretching and blowing stages improves the barrier properties of the bottles, making them suitable for packaging sensitive products.
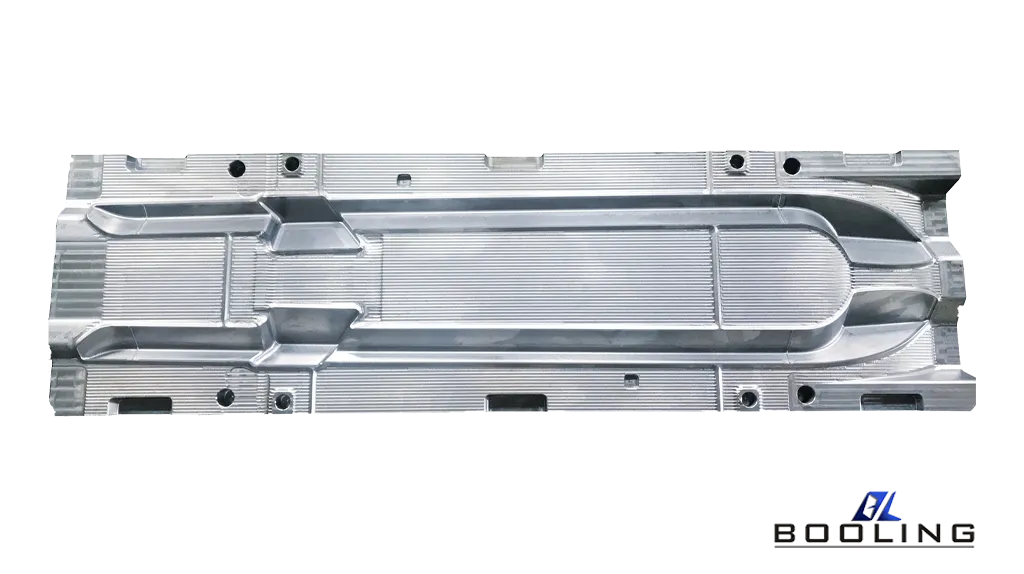
Material Selection for Injection Blow Molded Bottles
The choice of material is a critical factor in the success of injection blow-molded bottles. The selected material must meet specific requirements for processability, mechanical properties, barrier characteristics, and regulatory compliance. Some of the most commonly used materials in injection blow molding include:
- Polyethylene Terephthalate (PET)
PET is the material of choice for many beverage and food packaging applications due to its excellent clarity, chemical resistance, and barrier properties. PET bottles are widely used for carbonated soft drinks, water, juices, and other beverages.
- High-Density Polyethylene (HDPE)
HDPE is a versatile material known for its durability, chemical resistance, and impact strength. HDPE blow molding is commonly used for producing bottles for household chemicals, personal care products, and industrial applications.
- Polypropylene (PP)
PP offers good chemical resistance, heat resistance, and a wide processing window. It is often used for producing bottles for personal care products, pharmaceuticals, and certain food packaging applications.
- Polyamide (PA or Nylon)
Polyamides, such as nylon 6 and nylon 6,6, are known for their excellent mechanical properties, chemical resistance, and barrier characteristics. They are commonly used for producing bottles for automotive fluids, industrial chemicals, and specialized packaging applications.
The selection of the appropriate material depends on various factors, including the intended application, product requirements, regulatory compliance, and cost considerations. Material suppliers and blow molding experts can guide the most suitable material choice based on the desired performance characteristics and manufacturing constraints.
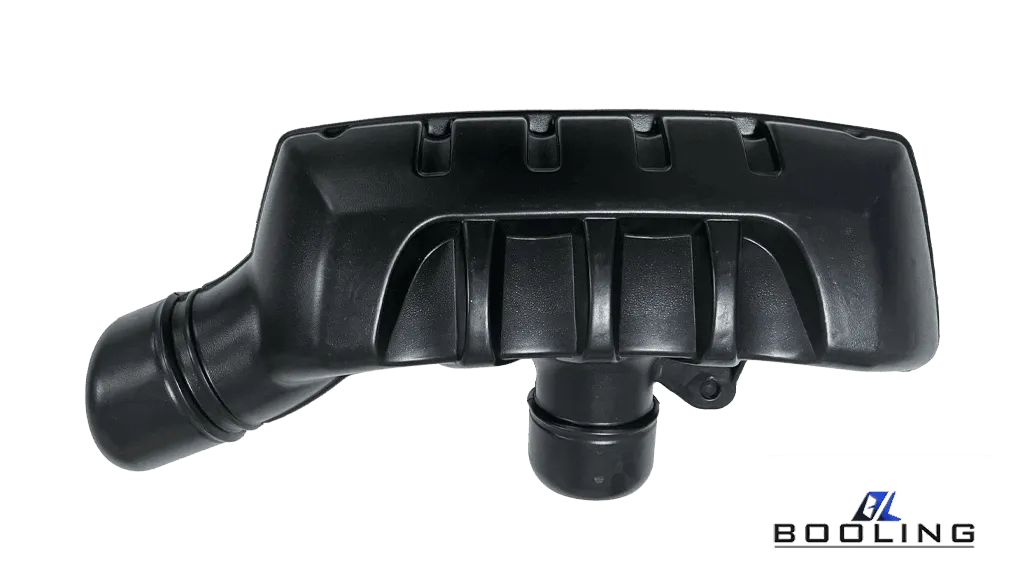
The Injection Blow Molding Process
The injection blow molding process for bottle production typically involves the following steps:
- Preform Injection Molding
The process begins with the injection molding of the preform, a thick-walled, cylindrical tube with a threaded neck finish. The plastic material, typically in the form of pellets or granules, is melted and injected into a preform mold cavity under high pressure. Once the preform has solidified, it is ejected from the mold.
- Preform Conditioning (Optional)
Depending on the material and application, the preforms may undergo a conditioning step before being transferred to the blow mold. This step involves reheating the preforms to a specific temperature, typically between 90°C and 110°C (194°F and 230°F), to ensure optimal stretching and blowing characteristics.
- Preform Transfer and Loading
The conditioned preforms are then transferred to the blow mold, where they are loaded into the mold cavities. This step is automated and precisely controlled to ensure accurate positioning and alignment of the preforms within the mold.
- Stretching and Blowing
Once the preforms are loaded into the mold cavities, the stretching and blowing process begins. A stretch rod is inserted into the preform, and the preform is stretched both axially (lengthwise) and radially (widthwise) to the desired dimensions. Simultaneously, high-pressure air or an inert gas is injected into the stretched preform, causing it to expand and conform to the shape of the mold cavity.
- Cooling and Solidification
After the stretching and blowing stages, the newly formed bottle is cooled within the mold cavity. This cooling process is essential for ensuring the bottle’s dimensional stability and strength. The cooling time is carefully controlled to prevent defects such as warpage or residual stresses.
- Bottle Ejection and Trimming
Once the bottle has cooled sufficiently, the mold opens, and the finished product is ejected. Any excess material, such as the preform gate remnants, is trimmed or deflated to produce the final bottle.
Throughout the injection blow molding process, various quality control measures are implemented to ensure the consistent production of high-quality bottles. These measures may include in-line inspection systems, leak testing, dimensional verification, and material testing to verify compliance with industry standards and specifications.
Optimizing the Injection Blow Molding Process
To achieve optimal results and maximize efficiency in the injection blow molding process, several factors must be carefully controlled and optimized:
- Preform Design
The design of the preform plays a crucial role in the success of the injection blow molding process. Factors such as wall thickness distribution, gate location, and material flow paths must be carefully considered to ensure proper material distribution and minimize defects during the stretching and blowing stages.
- Temperature Control
Precise temperature control is essential throughout the injection blow molding process. During preform injection molding, the melt temperature must be carefully monitored to ensure proper material flow and consistent preform quality. In the blow molding stage, the preform temperature must be optimized for efficient stretching and blowing, while the mold temperature must be controlled to facilitate proper cooling and solidification.
- Stretch Ratio and Blow Ratio
The stretch ratio (the ratio of the final bottle length to the initial preform length) and the blow ratio (the ratio of the final bottle diameter to the initial preform diameter) significantly impact the mechanical properties and barrier characteristics of the final product. Optimizing these ratios is crucial for achieving the desired performance characteristics.
- Process Monitoring and Control
Advanced process monitoring and control systems are essential for ensuring consistent and repeatable bottle production. These systems monitor and adjust various parameters, such as temperatures, pressures, stretch ratios, and cycle times, to maintain optimal process conditions and minimize defects.
- Mold Design and Maintenance
The design and maintenance of the injection molds and blow molds play a critical role in the quality of the final product. Proper mold design, including venting, cooling channels, and ejection systems, is essential for efficient and defect-free part production. Regular mold maintenance, such as cleaning and polishing, helps to ensure consistent part quality and extend the mold’s lifespan.
Quality Control and Testing
Quality control and testing are paramount in the production of injection blow molded bottles, as these products often serve critical functions in packaging and storing sensitive materials. Manufacturers employ a range of testing and inspection methods to ensure the highest levels of quality and reliability:
- Dimensional Verification: Bottles are subjected to rigorous dimensional inspections to verify compliance with design specifications and tolerances. This may involve the use of coordinate measuring machines (CMMs), laser scanners, or other precision measurement equipment.
- Leak Testing: Leak testing is a crucial step in the quality assurance process for bottles, particularly those used for containing liquids or gases. Various methods, such as air pressure testing, vacuum testing, or helium leak detection, are employed to identify any leaks or defects that could compromise the bottle’s integrity.
- Mechanical Testing: Mechanical testing, such as top load testing, drop testing, and burst pressure testing, may be performed to evaluate the mechanical properties and performance of the bottles under various conditions.
- Barrier Testing: For applications that require specific barrier properties, such as oxygen or moisture barriers, bottles may undergo specialized testing to evaluate their barrier performance and ensure compliance with industry standards.
- Environmental Stress Cracking Resistance (ESCR) Testing: Bottles intended for use in applications involving chemical exposure or environmental stress may undergo ESCR testing to assess their resistance to cracking and failure under these conditions.
- Regulatory Compliance Testing: Depending on the application, injection blow molded bottles may need to undergo specific testing to ensure compliance with relevant industry standards and regulations, such as those related to food contact, pharmaceutical packaging, or chemical resistance.
By implementing rigorous quality control measures and adhering to industry standards and regulations, manufacturers can ensure the consistent production of safe and reliable injection blow-molded bottles for a variety of applications.
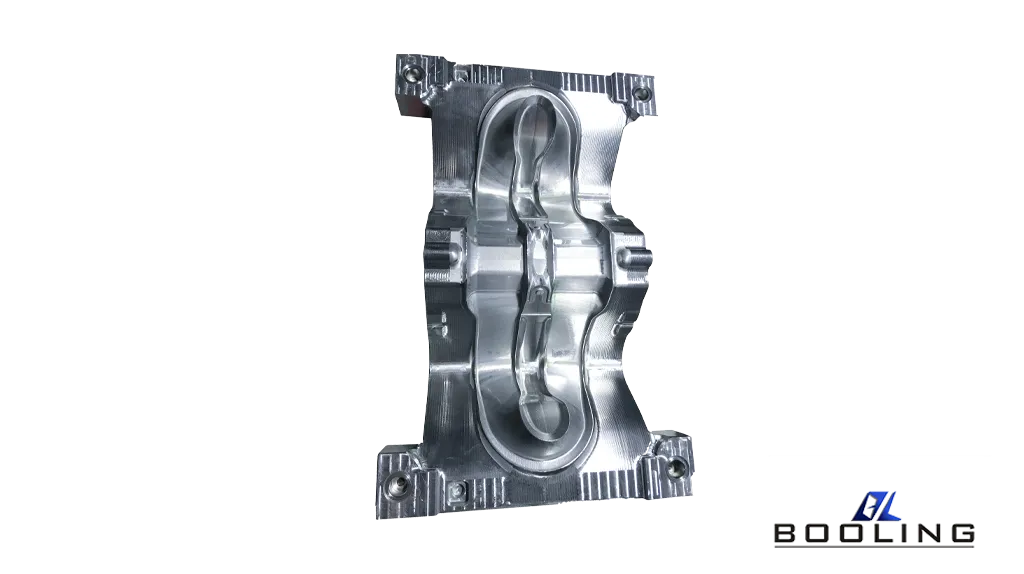
Applications of Injection Blow Molded Bottles
Injection blow molded bottles are found in a wide range of applications across various industries, thanks to their versatility, durability, and ability to meet specific performance requirements. Some common applications include:
- Beverage Industry
The beverage industry is one of the largest consumers of injection-blow molded bottles. PET bottles for carbonated soft drinks, water, juices, and other beverages are commonly produced using this process, taking advantage of the material’s clarity, barrier properties, and ability to withstand internal pressures.
- Food Packaging
Injection blow-molded bottles are widely used for packaging various food products, such as edible oils, sauces, and condiments. The barrier properties of materials like PET and HDPE help extend the shelf life of these products, while the lightweight design facilitates transportation and handling.
- Pharmaceutical and Healthcare
The pharmaceutical and healthcare industries rely on injection blow-molded bottles for packaging and storing medications, supplements, and other healthcare products. The sterile and inert nature of materials like PET and PP, combined with their barrier properties, makes them an ideal choice for these applications.
- Personal Care and Cosmetics
Injection blow-molded bottles are commonly used for packaging personal care and cosmetic products, such as shampoos, lotions, and perfumes. The design flexibility of the process allows for the creation of visually appealing and ergonomic containers.
- Automotive and Industrial
In the automotive and industrial sectors, injection blow molded bottles are used for various applications, including fluid storage, chemical handling, and lubricant packaging. The durability and chemical resistance of materials like HDPE and polyamides make them suitable for these demanding applications.
Injection blow molding is a highly efficient and versatile manufacturing process that enables the production of high-quality plastic bottles with exceptional precision, strength, and design flexibility. By combining the principles of injection molding and blow molding, this technique offers numerous advantages, including precise dimensional control, material efficiency, and enhanced barrier properties.
Related News
Applied’s expertise in modifying materials at atomic levels and on an ihdustrial scaleenables our customers to transform possibilities into reality.