Home > Common Metal Materials for Stamping Dies
Metal Stamping Die
The metal material of metal stamping die plays an important role. The main materials used include tool steel, stainless steel, and aluminum alloy, which have high wear resistance, toughness, and dimensional stability.
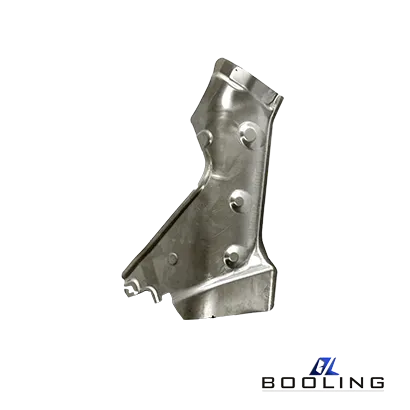
Common Metal Materials for Stamping Dies
In the world of metal forming, metal stamping dies play a crucial role in shaping and transforming raw materials into intricate and functional components. These specialized tools are employed across a wide range of industries, from automotive and aerospace to electronics and consumer goods. The choice of metal materials used in the construction of stamping die is a critical factor that determines their performance, durability, and the quality of the stamped parts.
Stamping dies are precision tools used in the stamping process, which involves applying tremendous force to deform and shape metal sheets into desired geometries. Metal stamping die is typically composed of multiple components, each serving a specific purpose in the stamping operation.
The die block, which houses the die cavity or impression, is the main component of the stamping die. The punch, designed to match the shape of the die cavity, applies pressure to the workpiece, forcing it into the die cavity. Other components, such as stripper plates, guide pins, and bushings, ensure proper alignment, positioning, and ejection of the stamped part.

Metal Materials for Stamping Dies
The selection of metal materials for stamping dies is crucial, as these tools must withstand the immense forces, wear, and temperatures associated with the stamping process. The following are some of the most commonly used metal materials for stamping dies:
- Tool Steels
Tool steels are the most widely used materials for stamping dies due to their exceptional strength, hardness, and wear resistance. These steels are typically heat-treated to achieve the desired properties.
- D2 Tool Steel: D2 tool steel is a high-carbon, high-chromium steel known for its excellent wear resistance, compressive strength, and toughness. It is commonly used for stamping dies, punches, and other tooling applications that require high durability.
- A2 Tool Steel: A2 tool steel is a cold-work tool steel that offers a combination of high wear resistance, toughness, and dimensional stability. It is often used for stamping dies, forming tools, and other applications where resistance to abrasion and deformation is essential.
- H13 Tool Steel: H13 tool steel is a chromium-molybdenum hot-work steel that exhibits excellent resistance to thermal fatigue, softening, and heat checking. It is widely used for stamping dies, extrusion dies, and other tooling applications that involve high temperatures and thermal cycling.
- Stainless Steels
Stainless steels are valued for their corrosion resistance and durability, making them suitable for stamping dies used in harsh or corrosive environments.
- 420 Stainless Steel: 420 stainless steel is a martensitic grade that offers good hardness, wear resistance, and corrosion resistance. It is often used for stamping dies, cutting tools, and other applications where a combination of strength and corrosion resistance is required.
- 440C Stainless Steel: 440C stainless steel is a high-carbon martensitic grade known for its exceptional hardness, wear resistance, and corrosion resistance. It is commonly used for stamping dies, punches, and other tooling applications that require high durability and resistance to corrosive environments.
- Aluminum Alloys
While not as durable as tool steels, aluminum alloys are sometimes used for stamping dies due to their lightweight and good thermal conductivity.
- 7075 Aluminum Alloy: 7075 aluminum alloy is a high-strength, heat-treatable alloy that offers good mechanical properties and resistance to wear. It is often used for stamping dies, particularly in applications where weight reduction is a priority.
- 6061 Aluminum Alloy: 6061 aluminum alloy is a versatile alloy that offers a good balance of strength, corrosion resistance, and machinability. It is sometimes used for stamping dies, particularly in applications where weight and cost are important considerations.
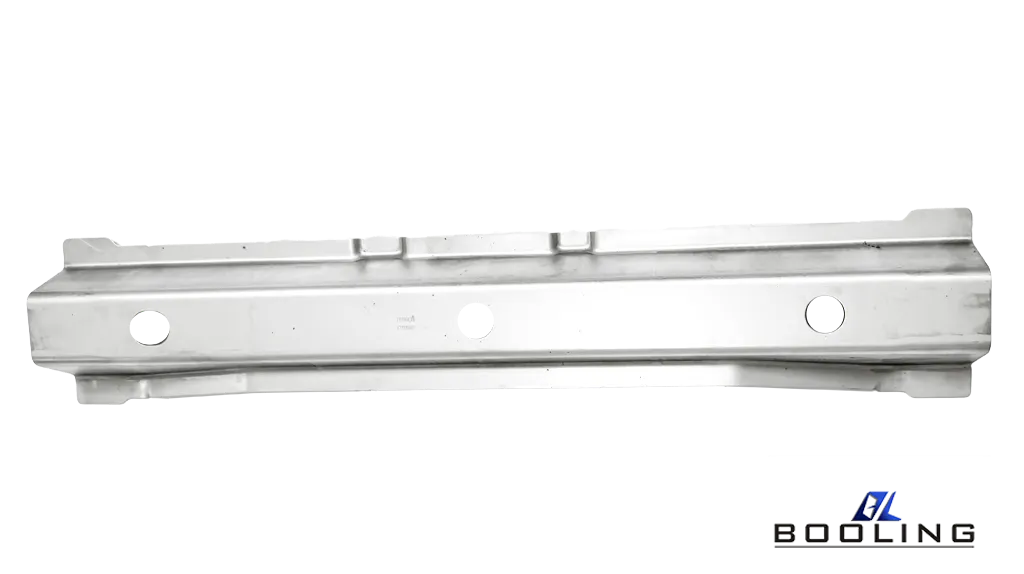
Precautions Before and After Using Stamping Dies
To ensure the optimal performance and longevity of stamping dies, it is essential to follow proper precautions before and after their use. These precautions help to minimize wear, prevent damage, and maintain the precision and accuracy of the dies.
Precautions Before Use
- Die Design and Clearances: Proper die design and clearances are crucial for ensuring smooth material flow and preventing excessive stress on the die components. Precise clearances between the punch and die must be maintained to control material flow and prevent galling or seizing.
- Material Selection: The choice of material for the workpiece is critical. Selecting the appropriate material grade and temper can significantly impact the stamping process and the wear on the die components. Materials with good formability and compatibility with the die materials should be chosen.
- Die Preparation: Before use, the die components should be thoroughly cleaned and inspected for any signs of wear, damage, or defects. Proper lubrication and surface treatments, such as nitriding or coatings, can enhance the die’s performance and longevity.
- Setup and Alignment: Proper setup and alignment of the die components are essential for ensuring accurate and consistent stamping operations. Misalignment can lead to premature wear, damage, and poor part quality.
- Operator Training: Operators should be properly trained in the safe and efficient use of stamping dies. Understanding the stamping process, die components, and maintenance procedures can help prevent accidents and extend the die’s lifespan.

Precautions After Use
- Cleaning and Inspection: After each use, the die components should be thoroughly cleaned to remove any debris, lubricants, or contaminants that may have accumulated during the stamping process. Regular inspections should be conducted to identify any signs of wear, cracks, or damage.
- Lubrication and Storage: Proper lubrication and storage of the die components are essential for preventing corrosion and maintaining their condition. Dies should be stored in a clean, dry environment, and any moving parts should be lubricated to prevent seizing or galling.
- Maintenance and Repair: Regular maintenance and repair of stamping dies are crucial for ensuring consistent performance and extending their service life. This may involve activities such as polishing, resurfacing, or replacing worn components.
- Record Keeping: Maintaining accurate records of die usage, maintenance, and repairs can help identify patterns and trends that may indicate the need for preventive measures or design modifications.
- Continuous Improvement: Continuously evaluating and improving the stamping process, die design, and maintenance procedures can help optimize performance, reduce downtime, and increase the overall efficiency of the stamping operation.
The choice of metal materials for stamping dies is a critical factor that determines their performance, durability, and the quality of the stamped parts. From tool steels to stainless steels and aluminum alloys, each material offers unique properties and advantages tailored to specific applications and operating conditions.
Related News
Applied’s expertise in modifying materials at atomic levels and on an ihdustrial scaleenables our customers to transform possibilities into reality.