Home > Metal Punching Dies
Metal Stamping Die
Metal stamping dies, as an efficient production tool, are widely used and important process equipment in industrial production. This mold can meet the requirements of stamping, flanging, bending, deep drawing, 3D forming, and assembly processes for complex parts.
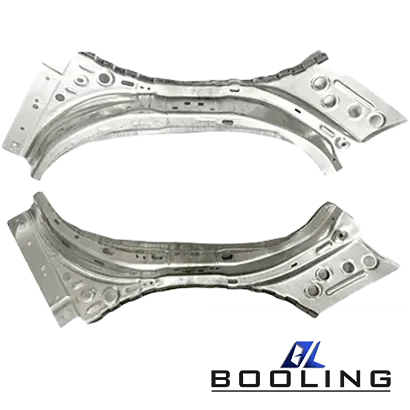
Metal Punching Dies
The technology of metal punching dies is stamping technology, which is widely used in the stamping manufacturing of metal raw materials, profiles, and pipes. Metal stamping die consists of two parts, an upper die and a lower die. The installation positions of the upper and lower molds for custom stamping die are different.The upper mold is installed on the slider of the punching machine, while the lower mold is installed on the workbench of the punching machine. The gap between the upper and lower dies plays a crucial role in determining the size of the hole, while the shape of the concave mold edge determines the shape of the hole. When the slider of the punch drives the upper die to move downwards, the punch of the upper die will move relative to the concave die of the lower die, thereby punching the required holes on the metal plate.
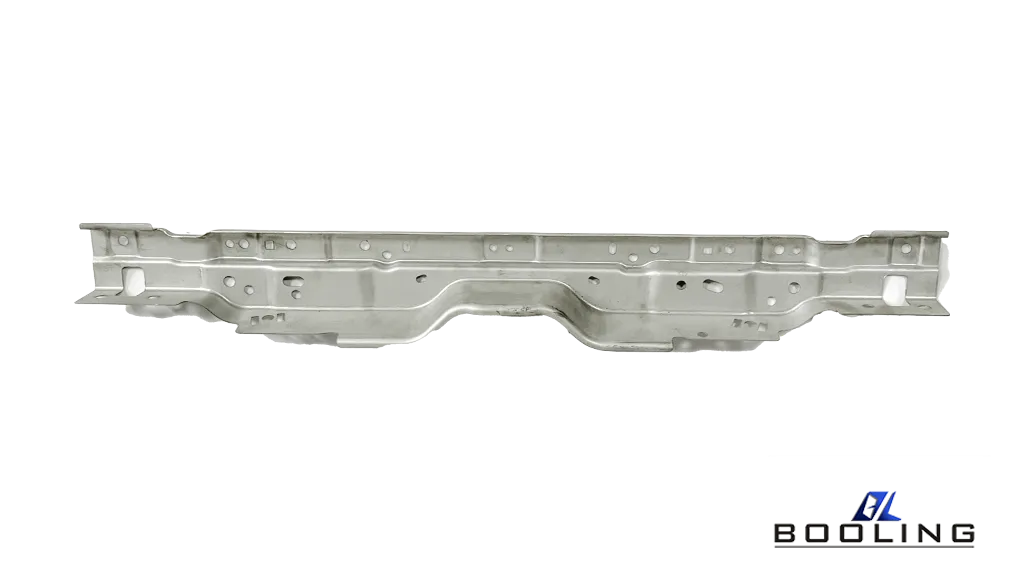
The Structural Of Metal Punching Dies
Upper Mold: The function of the upper mold is to install and fix the punch. It mainly consists of two structures, one is the punch and the other is the fixing plate. For quick replacement, some punches are connected to the fixed plate through threaded connections or quick clamping structures.
Lower Mold: The lower mold mainly consists of a concave mold, a cushion plate, and a fixing plate. The concave mold is used to form a punching shape, the cushion plate is used to adjust the position of the concave mold, and the fixing plate is used to fix the lower mold as a whole on the workbench
Gap: The gap between the upper and lower molds is crucial for the quality of punching. Excessive clearance may lead to increased punching burrs or uneven workpieces; If the gap is too small, it may cause increased mold wear or jamming. Therefore, selecting the appropriate clearance is the key to improving the quality of punching and extending the lifespan of the mold.
Guiding Device: To reduce friction and wear during the punching process, and improve mold life and punching accuracy, many metal punching dies are equipped with guiding devices. The guide device is usually composed of a guide pillar and a guide sleeve. The guide pillar is fixed on the fixed plate of the lower mold, and the guide sleeve is placed on the punch, allowing the punch to move along a fixed trajectory during the punching process, reducing the influence of lateral forces on the mold.
Safety Protection Devices: To prevent accidental injury to operators during the punching process, some metal punching dies are equipped with safety protection devices, such as safety protection baffles and photoelectric protection devices. These devices can effectively reduce the contact opportunities between operators and molds, and improve production safety.
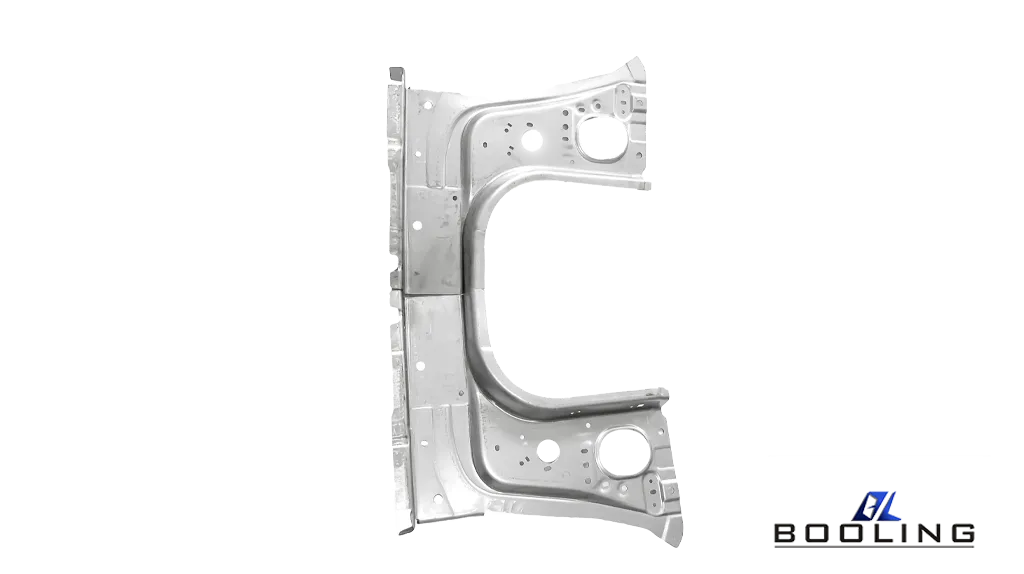
Material of Metal Punching Dies
There are many types of materials for metal punching dies, mainly including Cr12MoV, Cr12, Cr12Mo1V1, SKD11, D2, DC53, 2379, 2510, DF2, SKH-9, and tungsten steel. Technicians must choose the corresponding metal material based on the performance of the workpiece when selecting materials, which must meet working conditions, manufacturing requirements, precision, and other conditions. The process technology adopted for different metal materials will also vary, and corresponding surface treatment technology and heat treatment process will be selected. Processing metal punching dies with the correct process can help increase material performance and service time.
1.Cr12MoV Mold Steel: With high hardness and wear resistance, it is suitable for manufacturing metal punching dies bending dies, etc.
2.Cr12 : With high hardness and wear resistance, it is suitable for manufacturing metal punching molds and bending molds.
3.Cr12Mo1V1 : It is a type of mold steel with high wear resistance and toughness, suitable for manufacturing various stamping molds.
4.SKD11 : With high hardness and wear resistance, it is suitable for manufacturing various stamping molds.
5.D2 : With high hardness and wear resistance, it is suitable for manufacturing various stamping molds.
6.DC53 : With high hardness, wear resistance, and toughness, it is suitable for manufacturing various stamping molds.
7.2379 : With high hardness and wear resistance, it is suitable for manufacturing various stamping molds.
8.2510 : relatively affordable, suitable for manufacturing sample molds, single punch molds, etc. that do not require high mold life requirements.
9.DF2 : suitable for manufacturing various stamping molds.
10.SKH-9 : With high hardness and wear resistance, it is suitable for manufacturing various stamping molds.
11.Tungsten Steel: extremely hard and wear-resistant, suitable for manufacturing various stamping molds.
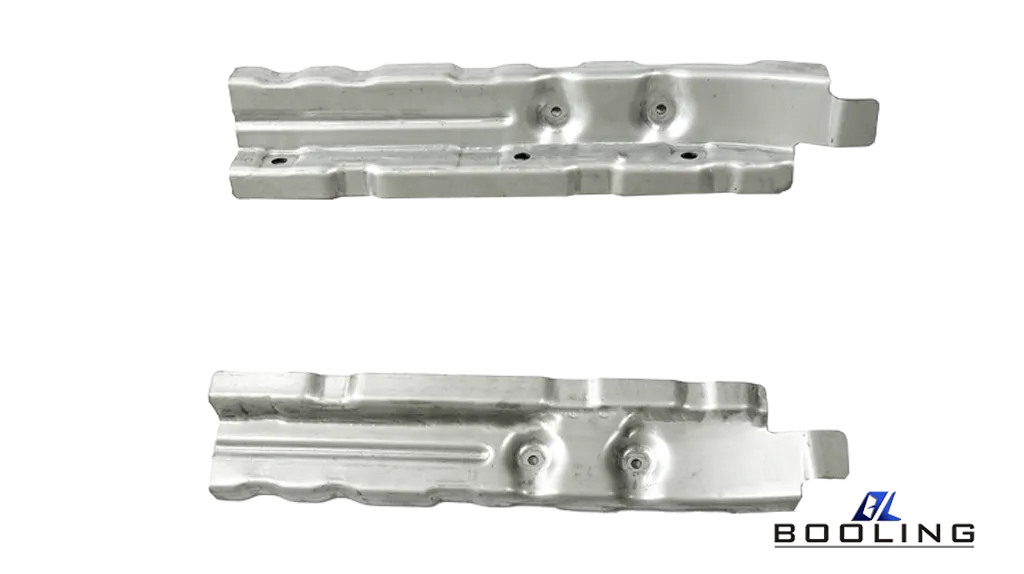
Design Points of Metal Punching Dies
- Punch: There are many types of punches, but a type with a top pin must be used.
- Stripping Board: The material is generally A3, and the fixing method is shown in the structural diagram. The brand of the guide pillar and guide sleeve is selected according to customer requirements. To prevent moving workpieces. For example, if a spring flies out of the mold and causes injury, a protective angle iron should be added around the discharge plate.
- Pressure Plate: It serves as a pressure plate and acts on the material sheet to prevent product deformation.
- Spring: It is a widely used elastic component in molds, mainly used for functions such as unloading, pressing, pushing, and ejecting. The length selection should ensure mold opening
Pre-compress by about 2mm in the state, and the compression amount of the spring in the closed mode state is less than or equal to the maximum compression amount. Green springs are used for punching and forming molds, such as
If there are special needs, other specifications can be considered. Priority should be given to the spring specifications of No. 25, and other specifications may be used in special circumstances. The distance from the center of the spring hole is approximately
Equal to the outer diameter of the spring, maintaining an actual wall thickness greater than 5mm compared to other spring holes. Priority should be given to the key areas of stress in the arrangement of springs, and then the whole process should be considered
Balance of body forces.
- Lower Mold Insertion: fixed inside the lower template, the front cannot be chamfered, and its brand should be used according to customer requirements.
- Ball Lock Punch: Quick disassembly is required, and the quick disassembly ball lock seat should be preferred as long as it does not affect the strength of the discharge plate.
- Punching Clearance: According to the general structural standard () punching clearance. Unless otherwise requested by the customer, the punch should be placed in the gap between the discharge plates.
The punch enters the concave mold by 5-8mm (please confirm with the department head in special circumstances).
- Equal Height Sleeves: There are generally three specifications: M6, M8, and M10. Taking into account the size and stress conditions of the activity board, M8 is generally preferred, while M6 and M10 can be selected based on the size of the template. The length of the sleeve is determined based on the itinerary of the activity board and the thickness of the relevant board. Usually, after the equal-height cylinder is arranged, it will be arranged again.
Application Fields of Metal Punching Dies
The processing principle of metal punching dies is to use the impact force and pressure generated by machines to process steel plates, aluminum plates, steel strips, and other materials into various shapes of holes or shapes. Metal punching dies have many properties, such as high quality, high precision, high efficiency, and homogeneity. They are widely used in the following fields:
- Metal Workpiece Manufacturing: such as metal products, mechanical manufacturing, electrical equipment, automotive parts, etc.
- Interior Decoration: such as suspended ceilings, walls, and partitions.
- Craft Production: such as metal handicrafts, railings, hangers, screens, etc.
- Cable Conduit: such as electrical conduit, pipe joints, pipe sleeves, etc.
- Electronic Products: such as mobile phones, computers, tablet TVs, LED displays, speakers, etc.
The advantages of metal punching dies. Compared to traditional mechanical cutting and drilling methods, punching has the following advantages.
- Efficiency: With fast punching speed and processing speed, it can greatly improve production efficiency.
- High Precision: The production accuracy of stamping molds is high, and the accuracy of the hole diameter at the same position is higher than that of traditional cutting, with smaller errors, which can improve the quality stability of the product.
- Flexible Design: Metal punching dies can create various shapes of holes and shapes according to design requirements, with high flexibility, suitable for diverse products and workpieces.
- Cost Saving: Compared with traditional mechanical processing methods, metal punching dies have lower costs and can save processing time and costs due to their fast processing speed.
The processing method and process flow of punching holes
The Processing Methods for Punching
- Single-hole Stamping: Use a mold to press once on the steel plate to complete the machining of a hole.
- Continuous Stamping: Passing a strip of steel through multiple holes on a mold to create multiple holes in the strip, with high processing efficiency, suitable for continuous processing of small holes and large-scale punching.
- Chapter-shaped Stamping: completing punching processing with patterns on steel plates, suitable for the production of metal handicrafts, decorative parts, cable reels, and other products.
The punching process generally includes the following steps:
- Material Preparation: Select appropriate steel plates, aluminum plates, or other metal materials.
- Mold Design: Design suitable metal punching molds according to requirements.
- Punching Processing: Place the material on the punching machine for processing.
- Surface Treatment: Finally, the processed product is cleaned, polished, and coated.
Metal stamping dies are a high-precision, high-quality, and high-efficiency processing method widely used in the manufacturing of various metal processing workpieces, such as process manufacturing, electronic products, automotive components, and other fields.
Related News
Applied’s expertise in modifying materials at atomic levels and on an ihdustrial scaleenables our customers to transform possibilities into reality.