Automotive Molds
Automotive molds are the main tools for producing automotive plastic parts and sheet metal parts, which mainly include automotive injection molds, blow molding molds, stamping molds, etc. The quality, precision, and surface quality of these automotive parts mostly depend on the quality of the molds.
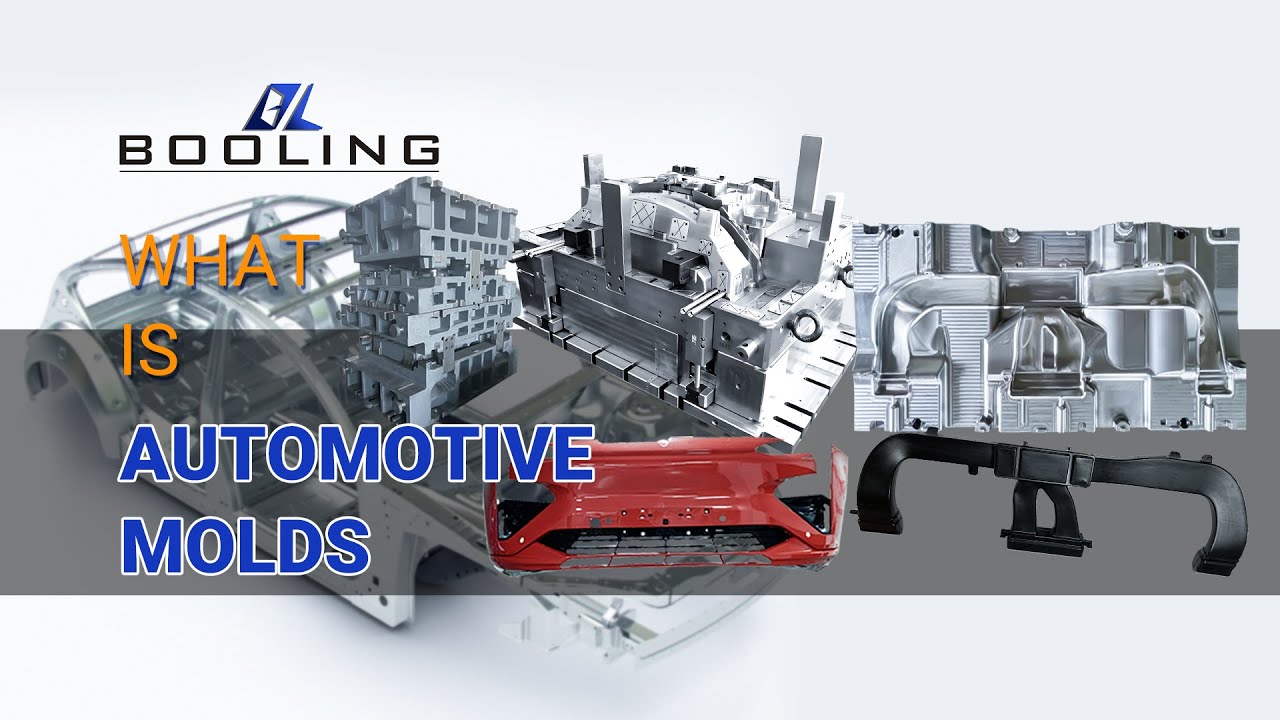
About BOOLING Automobile Molds
Automobile molds are mainly used to produce automobile interior and exterior trims, including plastic products and sheet metal products, such as headlights, dashboards, door trims, air-conditioning vents, body plastic parts, engine crankshafts, connecting rods, steering knuckles, gears, wheels, and other high-strength and high-reliability parts. It can be manufactured through injection molding, blow molding, extrusion, die casting, or forging molding, smelting, stamping, and other processes to meet different needs.
BOOLING Mold analyzes the 3D drawing data of automobile parts, combines customer machines, selected robots, product structures, etc. to design a reasonable mold structure, and provides customers with more feasible and efficient production solutions.
Booling’s custom car bumper mold is made of high-quality steel, processed through CNC machining, heat treatment, surface treatment, and other processes, with the characteristics of high precision and high production efficiency. The car bumper is an important part of the vehicle, playing the role of protecting and beautifying the car body.
Dashboard mold have very high requirements for processing and surface treatment, and need to combine aesthetics and practicality. In addition to processing, Booling can also provide raw material procurement and packaging and delivery services. Booling’s designers can create precise 3D models and use precision CNC equipment for processing to obtain high-quality final products.
The car lamp mold is designed with a hot runner system, as well as plastic materials such as ABS and PC. It is workable for cars, Passenger cars, SUVs, RV cars, and pickup trucks. It is made with high-hardness steel to make sure the car lamp is transparent enough through light, ensures a good light guiding effect of car lights, and prevents glare when there is no light level or high brightness.
The car pillar mold uses high-precision CNC machine tools to process it to ensure its wear and corrosion resistance. After fine processing, Booling can ensure the mold’s accuracy of around ±0.01mm.
Our auto door panel mold uses 5-axis finishing technology, combining CNC technology and automated production, and is both practical and beautiful. If you are still looking for a suitable automotive mold supplier, Booling is a good choice.
Booling’s auto grille mold uses 5-axis high-precision technology to achieve precision injection molding of car grilles. Car grilles can meet the car’s needs for air intake and heat dissipation and the high aesthetic requirements of the car’s front face.
Booling’s automotive air duct mold uses five-axis linkage processing technology to achieve rapid processing of high-performance air ducts. Automotive air ducts are the main equipment for regulating air circulation in the car.
The car spoiler mold adopts CNC milling processing technology and uses the CNC milling machine processing center to control the machining trajectory of the milling cutter to achieve a high-speed, small-feed cutting method to ensure machining accuracy.
Manufacturing Process of Automobile Molds
The manufacturing of automobile molds is a complex process, which involves many aspects such as mold structure design, process design, material selection, etc. The manufacturing of automobile molds mainly utilizes 3D printing technology, injection molding, blow molding, etc.
Injection molding is a cutting-edge manufacturing process that involves injecting molten material, typically thermoplastics or thermosetting polymers, into a carefully crafted mold cavity. This cavity, created using advanced CAD/CAM software and precision machining techniques, serves as a blueprint for the final product.
BOOLING 3D printing service mainly provides customized services for industries such as medical models, aerospace, and automotive parts design and manufacturing. The main types of 3D printing technology are FDM, SLA, SLS, DLP, binder spraying, material spraying, DMLS, SLM, electron beam melting, and LOM.
We conduct DMF technical analysis for customers based on product design, and with the professional technical support of our team, propose reasonable solutions before mold making. Booling blow molded products are more prone to shedding burrs, greatly improving production efficiency and facilitating workers to operate during stretching and blow molding processes in the workshop manufacture.
A checking fixture in the automotive industry is a precision tool used to inspect and verify the concentricity, runout, and other dimensional standards of components, ensuring they meet the required specifications through various types of inspection and testing methods.
Booling’s 3D blow molding is mainly used in air ducts around automobile engines. It has the outstanding advantages of seamless welding and uniform wall thickness.
BOOLING Stamping Die specializes in the design and manufacture of precision progressive dies for automotive sheet metal punching and bending applications. Our expert team offers comprehensive services from prototype development to final press-ready tooling, ensuring high-quality cutting and forming solutions for even the most complex stamped parts.
FAQs about Automobile Molds
What Products Can Automotive Mold Make?
According to different manufacturing processes, automotive mold products can be divided into injection-molded parts, blow-molded parts, and stamped parts.
- Injection molded parts mainly include bumpers, instrument panels, car lights, door handles, seats, engine hoods, and other interior and exterior decorations.
- The automotive parts manufactured using blow molding molds mainly include car air conditioning ducts, tail fins, spoilers, luggage racks, truck fuel tanks, RV footrests, and toolbox or storage boxes inside the car.
- Stamping dies are widely used in automotive parts, mainly including connecting plates, reinforcing plates, fixing plates, pillar inner plates, etc.
-Connection board: Front cabin water guide main board connection board
-Reinforcement plate: left/right upper beam (rear) reinforcement plate, rear cover hinge reinforcement plate
-Pillar inner panel: rear fender inner panel, front and rear bumper frame, D-pillar inner panel, left longitudinal beam inner panel body
-Fixed plate: Rear combination lamp fixed plate
Manufacturing Process of Automobile Mold
Automotive molds require high precision in processing. Booling molds use the latest data analysis and industrial drawing software to provide reasonable and competitive mold design solutions, providing customers with efficient production processes.
1. Product analysis: Conduct an overall analysis based on the provided drawings or samples, and provide a feasibility analysis report for product molding.
2. Mold design and data analysis: Analyze the structural shape of the mold based on the size of the product, determine the mold cavity, flow channel, cooling system, etc., and design the mold according to customer requirements.
3. Mold making: Based on the precision requirements of the product surface and mold structure, rough machining, semi-precision machining, and precision machining are distinguished to meet the customer’s size requirements and control the mold cost.
4. Mold size inspection: The precision components of the mold can be calibrated using a coordinate measuring instrument.
5. Product quality control: Use inspection tools for testing automotive plastic and sheet metal parts.
6. Cutting and punching fixtures: provide more stable and accurate product size assurance for the processing of post-production processes.
How to customize your automotive mold?
1. Contact Booling and provide samples or 3D drawings
2. Booling will provide a quotation according to customer needs within 24 hours
3. Confirm the order
4. Design mold drawings
5. Customer confirms the mold drawings
6. Prepare materials
7. Production and processing
8. Assembly and polishing
9. Trial mold T1
10. Mold repair and adjustment
11. Trial mold T2 delivery
12. Mold packaging and delivery
13. Customer confirms receipt
Rapid Prototyping Technology of Automobile Mould
- Automotive injection molding mold
Injection molding is a process that utilizes pressure for processing, in which molten plastic resin is injected into a mold under high pressure, cooled, and solidified into a shape. The components produced using automotive injection molds mainly include bumpers, instrument panels, headlights, door handles, etc., which have complex shapes. - Automotive blow molding mold
Blow molding is a production process that uses air compression to produce molded blanks from molten plastic, which are then inflated with air. The components produced using automotive blow molding molds have the characteristics of lightweight, meeting the current market demand for reducing carbon emissions. - Automotive stamping die
Stamping die is a common tool for sheet metal automotive parts processing. By placing a metal sheet in the die and using the pressure and motion of the die and stamping equipment, the metal sheet is processed into the desired shape, such as car shock absorbers, and interior panels (luggage compartment, engine compartment assembly, etc.). Stamping molds play an important role in improving the weight-bearing capacity and support of automotive parts.
Automobile Mould Customization Service
BOOLING provides customized services for the automotive manufacturing industry. Users can contact our engineers based on their drawings and corresponding requirements, and we will provide you with the best solution.
1. Customized logo-can make multiple logo inlays to facilitate customer ODM production
2. Customized product surface effects, polish surface, leather grain, sandblasting, etc. are optional, and can also be customized according to samples
3. Design the structure and size of the mold according to the customer’s machine parameters
4. Design the number of mold cavities according to the market demand for parts to improve production efficiency
5. After the mold is made, we can provide customers with product OEM production services
6. We can provide 3D printing services before mold production to facilitate product design optimization and market research
7. We can provide rapid mold production, suitable for small batch production, and the rapid mold delivery cycle is short: 7-20 days
Logistics and transportation of automobile molds
1. Clean the core and cavity with oil
2. Spray rust inhibitor on the core and cavity
3. Spray rust-proof paint on the mold surface
4. Film covers the mold surface
5. Mold accessories packaging
6. Custom mold wooden box packaging
7. Loading by sea or sending to the airport for air transportation