Home > 3D Blow Molding Services
3D Blow Molding
3D blow molding technology allows for higher precision and manufacturing efficiency on some blow molded parts, enabling highly customized workpieces to meet different applications and usage scenarios, ensuring high-quality production in large batches.
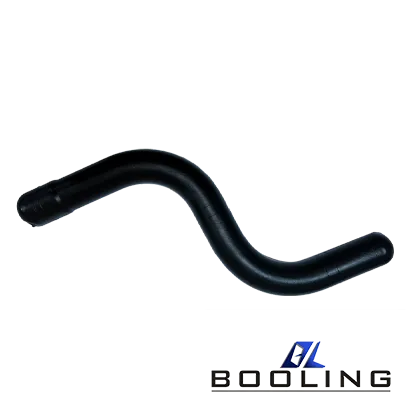
3D blow molding technology is an emerging manufacturing process that achieves customized structures and time-triggered methods through FDM 3D printing. This technology provides users with the ability to design and create hollow volume shape changes using thermoplastic materials, meeting the needs of different application scenarios.
Compared to traditional blow molding technology, plastic blow molding services can greatly reduce manufacturing costs and greatly improve product accuracy and quality.
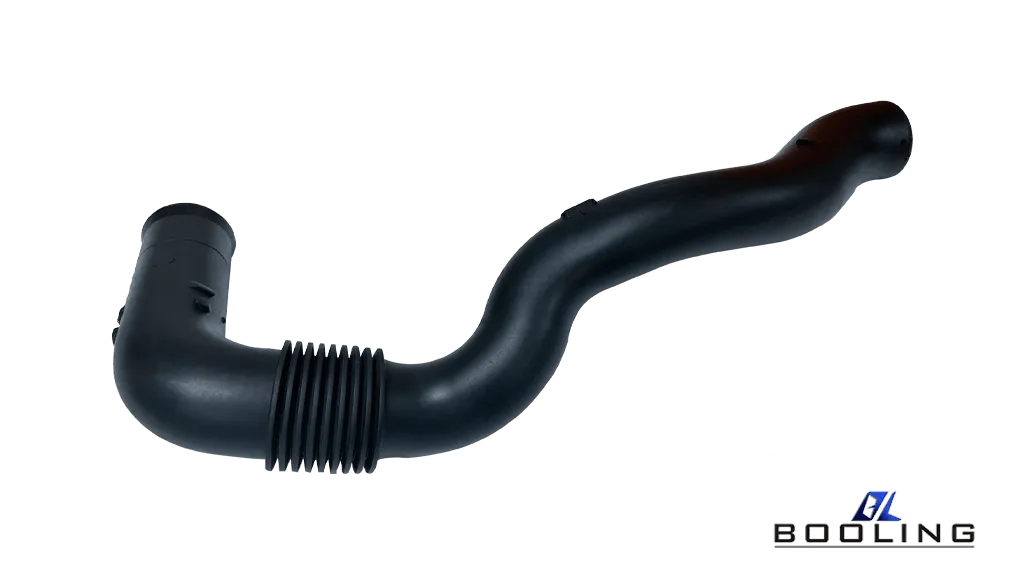
3D Blow Molding Movable Die Type
The 3D blow molding movable die head is an important component of blow molding equipment, and the design of this part needs to be adjusted according to the actual processing to better control the material extrusion of blow molding. The movable die head can be divided into movable die head type structure and movable die head mold type structure according to the different ways of obtaining the billet.
-Process
- The movable die head type is achieved by moving the die head (or directly moving the billet coming out from below the die head) in a certain position to place the pre-inflated billet according to the shape of the mold cavity and continue it to the end of the cavity. During this process, the mold remains stationary. Once the blank is filled in the cavity, the lower mold moves horizontally and closes with the upper mold, completing the blowing process. Take out the product and complete the cycle process.
- A movable die head mold type hollow blow molding has a mechanism for moving the mold. By moving the mold in the working and working directions, the material in the machine head is placed in the mold cavity, and then the lower mold is moved directly above the upper mold to complete the production of the product by closing the mold and blowing air. To achieve a simpler and faster filling process, some have mechanisms that allow the extruded mold to change around the mold cavity at the same time. By swinging the grooves 107 on the mold surface and pulling the soft sleeve 109 to move, a complex multi-dimensional mold is formed to fill the mold cavity. It is to use a flat plate device installed at 45 ° or adjusted from 45 ° to 90 °, or a right-handed plate to move the mold under the machine head in the y direction, and directly place the billet in the mold cavity. The billet head is pre-clamped, and the mold moves under the head when the billet is extruded. This means that most of the blanks are contained within the mold, with only flying edges at the end of the product. For car ducts, this flying edge area is often a corner material, as the two ends of the plastic pipe will be modified, making the two ends of the product open. The bottom or right plate moves on the z and y planes to allow the billet to enter the mold cavity according to the shape of the cavity. Align the bottom plate with the center and top, or the left plate is close to the bottom plate, and then insert the air needle for blow molding. One blow molding cycle can begin. The upper plate is opened, and the lower plate moves in a shuttle style towards the operator in the y direction. Then, it is manually or mechanically removed, and the lower plate rises to the highest point to start the cycle again. By using an electrical automatic control mobile device, the mold can swing freely in two directions along the inclined template.
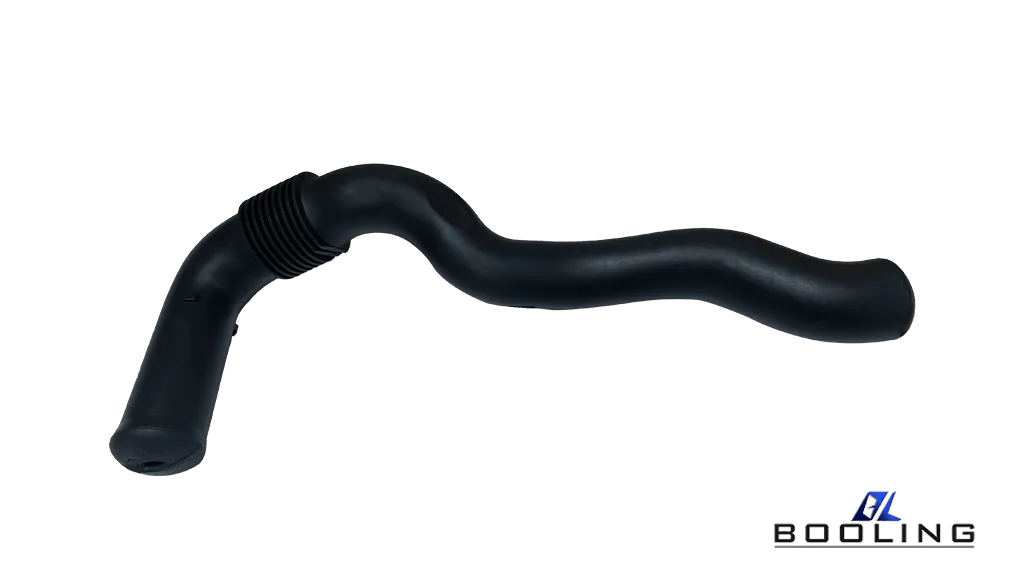
Characteristics of 3D Blow Molding Movable Die Head
In the 3D blow molding die, although the extruded plastic parts have a pre-set shape, they will still deform due to their weight and temperature. The characteristics of a movable die mainly include:
-Characteristics
- Can continuously produce and sequentially extrude 3D blow molded products, using one extruder to produce one arc on the product, and then using another extruder to produce the second arc on the product. Several different thermoplastic elastic polyolefin materials can be combined to produce products, making the two ends of the product soft. Hard materials can provide strength for 3D blow molding, while medium soft materials can be shock-resistant and easy to assemble. To increase the value of the product, many assembled products were merged into finished products, eliminating the indentation and connecting components on the end face of the serpentine tube.
- Uniform wall thickness can be obtained because the billet is continuously clamped in the mold, which reduces residual stress in molding and increases the integrity of the product shape. Products can have a good appearance. If brackets or inserts are required on 3D blow-molded products, injection molding inserts can be used for embedded molding during the blow-molding cycle. Because most products are produced using flat plates in an inclined position, the inserts can easily remain in the mold during the molding cycle. Similarly, because the bottom plate of the mold is moved towards the operator, it is also convenient for the operator to insert inserts into the mold. By systematically moving the mold cavity, a compression molding flange can also be formed on the movable die-type molded product, and the local blank is clamped between the two to form the flange. Other applications include agricultural pipelines, automotive gas pipes, and furniture handrails. Furniture handrails reflect the changes in the movable mold type processing process of 3D blow molding. To achieve the requirements of a good hand feel and reasonable structure, complex-shaped products can be molded from materials with hard inner layers and soft outer layers, or double-wall plastic products can be blow molded.
-The application of movable die mold type hollow 3D blow molding products is mainly used for pipeline parts in automobiles. It is a good choice to use the movable die mold type processing method to shape these pipe fittings. When using conventional blow molding methods to shape these pipe fittings, the generated burrs can reach 2-3 times the product quality. Products formed using the mold moving method have significantly reduced burrs, which can reduce the workload of the next step and save auxiliary decoration equipment. According to the number of extruders in the equipment, two or three different plastic materials can be used simultaneously during processing.
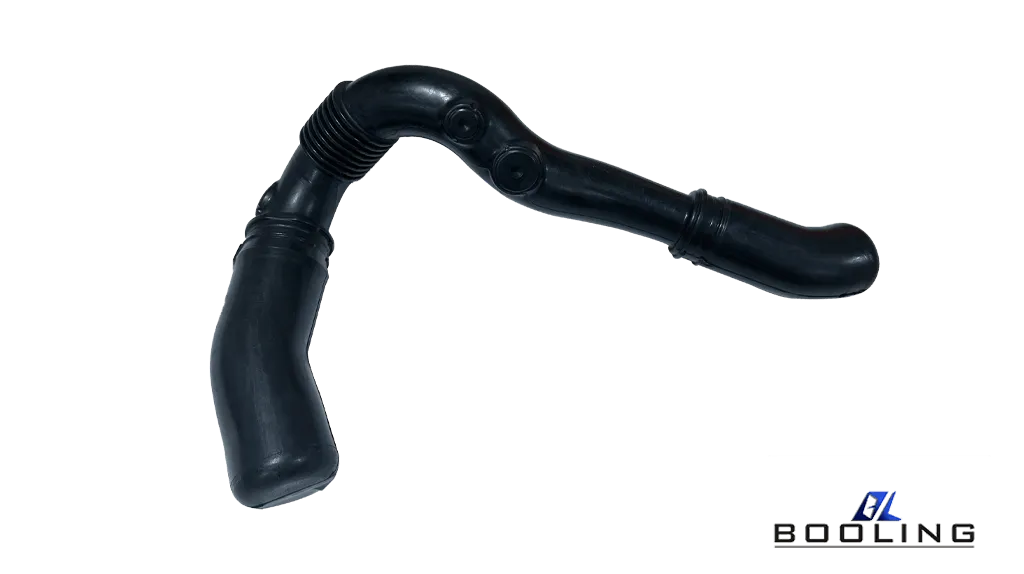
3D Blow Molding Raw Material Pretreatment Equipment
The raw materials for 3D blow molding are similar to those for ordinary blow molding, and both require pre-treatment before processing. The pre-treatment equipment for 3D blow molding raw materials mainly includes:
-Vibrating Screen
A vibrating screen is a device that uses a flat or slightly inclined screen body to perform sieve analysis through vibration. Vibration sieve analysis is usually suitable for sieving granular resins and high-density fillers. If the sieve body is made into a closed type, it can also be used for screening powdered materials.
Characteristic:
- Power saving: The magnet of the electromagnetic vibrating screen only consumes electrical energy when it is attracted, and does not consume electrical energy when it is disconnected;
- Due to the open type of the sieve body, dust is prone to fly during sieving, resulting in poor hygiene conditions. The vibration generated by the reciprocating variable speed motion causes the moving parts to collide and produce significant noise;
- The screening efficiency is high, and the sieve holes are not easily clogged, which is conducive to improving the efficiency and speed of 3D blow molding;
- The sieve structure is simple and open, which is conducive to the maintenance or replacement of the net.
-Translational Sieve
The translational sieve uses an eccentric wheel device to drive the sieve body to undergo a planar circular variable speed motion.
Characteristic:
- During 3D blow molding, the entire screen can be utilized, with a screening efficiency higher than that of cylindrical screens but lower than that of vibrating screens, but the screen holes are prone to clogging;
- The screening body is usually sealed, so it is not easy to produce dust flying during screening, and the hygiene conditions are good;
- The vibration and noise generated by the flat circular variable speed motion of the screen body are small;
- The sealing of the sieve body makes maintenance or replacement of the sieve inconvenient;
- The translational sieve analysis has a wide range of applications, usually suitable for powdered and granular resins, high-density fillers, and other powdered additives filtering.
-Rotating Sieve
The common types of rotating screens are mainly round and simple decorations, which are mainly composed of a sieve mesh and a sieve frame. The screen mesh is usually made of copper wire mesh, alloy wire mesh, or other metal wire mesh. During work, the materials that need to be sieved are placed on a rotating screen, and the circular mesh is driven by a driving device to rotate and achieve material sieving. The structure of this sieve body is simple and open, which is conducive to the maintenance or replacement of the net, but the screening efficiency is low. The usage area of the screen mesh only accounts for 1/8-1/6 of the total screen mesh area. Due to its open structure, dust is easily generated during screening, resulting in poor hygiene conditions. Rotational analysis is usually suitable for screening high-density powdered fillers, such as calcium carbonate, talc powder, clay, etc.
3D blow molding can provide lightweight product production, especially in automotive manufacturing, which can significantly improve the utilization rate of plastic materials, reduce energy consumption and production cycles, and bring more possibilities for the development of various industries.
Related News
Applied’s expertise in modifying materials at atomic levels and on an ihdustrial scaleenables our customers to transform possibilities into reality.