Home > Custom HDPE Blow Molding
HDPE Blow Molding
The blow molding process can accurately control the wall thickness, making the wall thickness of HDPE blow molded products uniform and able to withstand external pressure, ensuring the stability and durability of the product. At the same time, HDPE blow molded products have certain cost-effectiveness. The price of HDPE material itself is moderate, and combined with the simplicity and efficiency of blow molding technology, the overall production cost is relatively low.
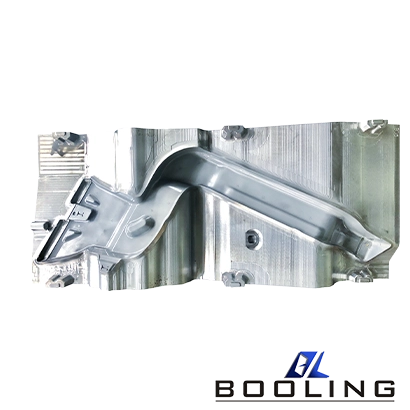
Custom HDPE Blow Molding
HDPE blow molding uses high-density polyethylene as the main raw material, heats the raw material to a molten state through an extruder, and then forms a tubular billet through a mold. It is placed in the mold and blown by compressed air until it tightly adheres to the inner wall of the mold, forming the desired plastic blow-molded product.
The principle of HDPE blow molding is mainly based on the plasticity of thermoplastic. When heated, HDPE plastic becomes soft and is shaped by the mold cavity, resulting in hollow plastic products.
HDPE blow molded products are widely used in the packaging industry, such as plastic bottles, barrels, cans, and other containers. Due to their excellent durability, insulation, and airtightness, they are used in the manufacturing of waterproof materials, insulation layers, and some industrial components.
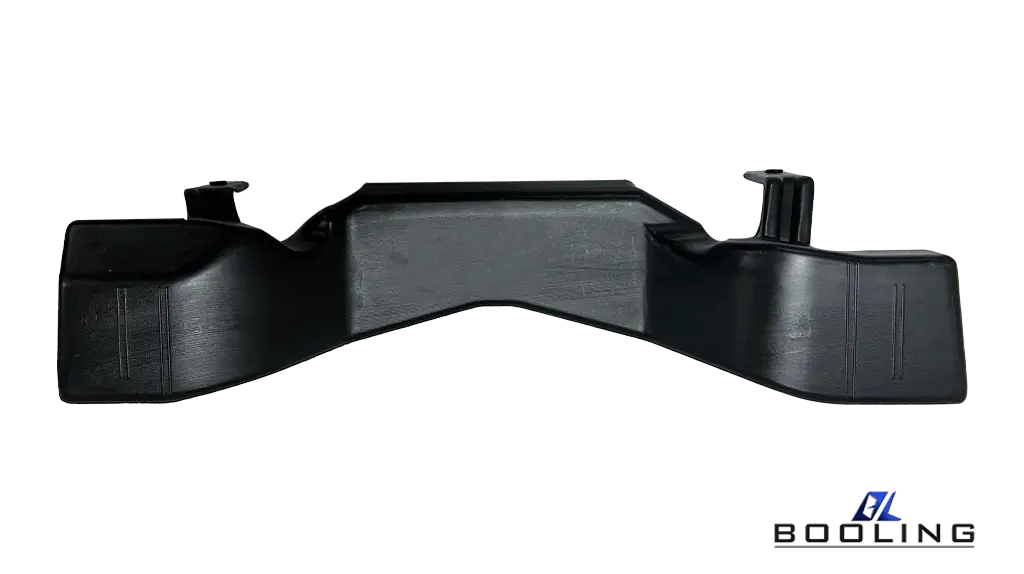
Blow Molded Grade HDPE
HDPE is an excellent blow molding material. Manufacturers need to have a certain understanding of the characteristics of these materials when using them.
- Chinese Full Name: High-density polyethylene
- Alias: Low-pressure ethylene
- Monomer Composition: Ethylene
- Basic Characteristics: High-density polyethylene is an opaque white wax-like material with a specific gravity lighter than water, ranging from 0.941 to 0.960. It is soft and tough, but slightly harder and more stretchable than LDPE. It is non-toxic and odorless.
- Combustion Characteristics: Flammable, can continue to burn after leaving the fire, with a yellow flame at the top and a blue flame at the bottom. It melts during combustion, with liquid droplets and no black smoke emitted. At the same time, it emits the odor of paraffin burning.
- Main Advantages: acid and alkali resistance, organic solvent resistance, excellent electrical insulation, and can still maintain a certain degree of toughness at low temperatures. Surface hardness, tensile strength, rigidity, and other mechanical strengths are higher than LDPE, close to PP, and tougher than PP, but the surface smoothness is not as good as PP.
- Main Disadvantages: poor mechanical performance, poor breathability, easy deformation, easy aging, easy brittleness, lower brittleness than PP, easy stress cracking, low surface hardness, and easy scratching. Difficult to print, surface discharge treatment is required during printing, electroplating is not allowed, and the surface is dull.
- Application Scenarios: Used for extruding packaging films, ropes, woven bags, fishing nets, and water pipes; Injection molding of low-grade daily necessities and shells, non-load bearing components, rubber boxes, turnover boxes; Extrusion blow molded containers, hollow products, bottles.
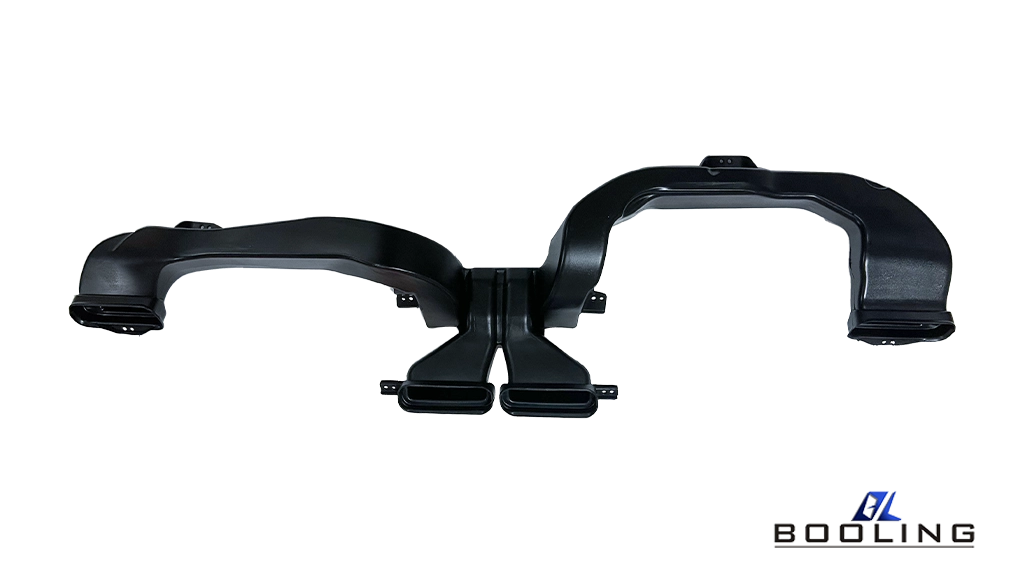
Advantages of HDPE Blow Molding
The advantages of HDPE blow molding are outstanding, with high dimensional accuracy and uniform wall thickness, no joint seams on the surface, excellent environmental performance, and certain design flexibility. This has led to its application in multiple industries, especially in the manufacturing of packaging and containers. Taking HDPE blow molding as an example, the overall advantages of HDPE blow molding will be introduced.
- Injecting plastic melt into a blow-molded billet mold and subjecting it to a certain directional effect around the cavity. In addition, the temperature of billet inflation is lower than that of extrusion blow molding, and the orientation effect generated by inflation can be retained more, which helps to improve the strength and other properties of HDPE blow molded products.
- HDPE blow-molded bottles have high dimensional accuracy, making it easier to ensure the uniformity of bottle wall thickness and bottle specifications according to requirements.
- The surface of the bottle does not form seams, and there is no need to trim the edges after molding. Generally, no scraps are produced, and the scraps produced by extrusion blow molding are generally 5% -30%
- HDPE blow-molded bottles have high glossiness, and the transparency of the bottle body formed by transparent polymers is obvious.
- A movable bottom module can be installed on the HDPE blow molding mold to make the shape design of the bottom of the bottle more flexible and suitable for the molding of hard plastic bottles and wide-mouth plastic bottles.
- Injection blow molding requires two types of molds: injection molding molds and blow molding molds. The mold requirements are high, so the cost of injection blow molding is relatively high, about 2-3 times that of the calibration blow molding period. Due to the high pressure of the mold body in the mold cavity, the joint stress of the blow molding gripper body is high, and the clamping force required for the mold is high. Bottles with low solvent content are mostly used for injection molding and blow molding, which cannot form complex-shaped products and have significantly higher energy consumption.
- In addition, the sealing degree of polyethylene bottle mouth in drug packaging affects the safety of drugs, while injection molding and blow molding methods have high dimensional accuracy of threads and uniform wall thickness of the bottle body, which are suitable for special requirements of drug packaging. Therefore, to prevent the evaporation of medicinal gas inside the bottle and the infiltration of polluted air from the outside, manufacturers now use HDPE injection molding to produce high-quality medicinal plastic bottles.
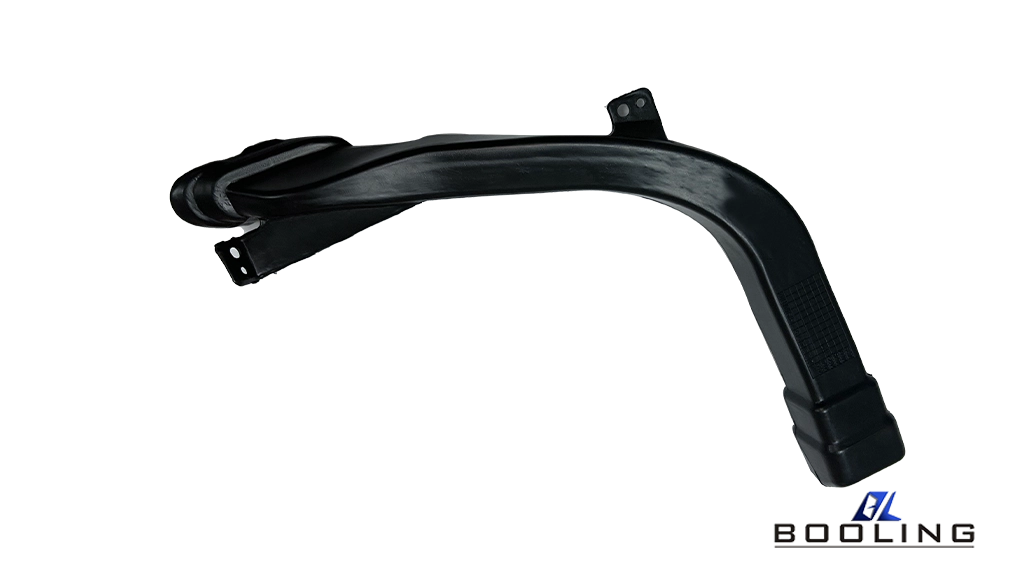
Application of HDPE Blow Molding
The application of HDPE blow molded products is very extensive, and the products produced have good physical and chemical properties, including corrosion resistance to chemical agents, strength, stiffness, electrical insulation, as well as certain transparency and glossiness.
- Daily Necessities: HDPE blow molded products are also widely used in the daily necessities industry, such as laundry detergent bins, garbage bins, water buckets, etc. These products have the characteristics of high strength, easy cleaning, and long lifespan, making them very suitable for use in homes and public places.
- Food Packaging: Blow molding technology is widely used in the field of food packaging, such as beverage bottles, food packaging barrels, freshness boxes, etc. Blow-molded products have the characteristics of good sealing, low-temperature resistance, transparency, and lightweight, making them very suitable for packaging and transporting food.
- Chemical Industry: HDPE blow molding technology can produce various types of chemical storage containers, packaging bags, and industrial pipelines. Especially for highly corrosive chemicals, HDPE blow molding can produce high-density plastic containers, which are very suitable for storing and transporting these highly dangerous goods.
- Toy: HDPE blow molding technology can manufacture toys of various shapes and colors, such as swimming rings, slides, home playground equipment, park supplies, etc. HDPE blow-molded toys are highly favored by consumers due to their safety, environmental friendliness, and durability.
- Automotive Industry: HDPE blow molding technology can be used to manufacture automotive components such as fuel tanks and water tanks. These blow-molded products have characteristics such as oil resistance and temperature resistance, which can meet the requirements of the automotive working environment.
- Agricultural field: In the agricultural industry, the application of HDPE blow-molded products is mainly reflected in the packaging of agricultural materials, such as fertilizer packaging, pesticide packaging, etc. The weather resistance and impact resistance of HDPE blown film help to better protect the quality of agricultural materials.
- Medical Industry: In the medical industry, HDPE blow molding technology can produce various medical devices, such as medical syringes, oxygen equipment, blood bags, infusion sets, drug bottles, etc. HDPE blow molded products have the characteristics of non-toxic, sterile, and hygienic, which can ensure the safety of medical work.
- Electronics Industry: HDPE blow molding technology is also used to manufacture plastic products such as electronic product casings and insulators. These products have good insulation performance, temperature resistance, and other characteristics, which can meet the requirements of electronic products.
- Construction field: HDPE blow molding technology can manufacture plastic products for construction, such as plastic pipes, plastic sheets, etc. These products have characteristics such as corrosion resistance and thermal insulation and can be applied to water supply and drainage systems, insulation materials, etc. in the field of construction.
HDPE blow molding raw materials themselves have high surface hardness and tensile strength, which enables them to produce products with stable and consistent quality, shape, and accuracy. These characteristics make HDPE material an ideal material for manufacturers to carry out blow molding production, and it has been widely applied and promoted, widely used in industries such as food, medical, chemical, toy, automotive, construction, electronics, agriculture, and daily necessities.
Related News
Applied’s expertise in modifying materials at atomic levels and on an ihdustrial scaleenables our customers to transform possibilities into reality.