Home > Common Plastics for Blow Molding: HDPE Molding Guide
There are various types of plastics to choose from in blow molding technology, and the processing methods are flexible. Manufacturers typically use HDPE materials for blow molding manufacturing in fields such as food packaging, personal care, cosmetics, and pharmaceuticals.
Advantages of HDPE Blow Molding:
- Excellent Chemical Resistance
- Durability and Impact Strength
- Moisture Resistance
- Cost-Effectiveness
HDPE is a common plastic raw material in blow molding, widely used in the production of various containers and automotive parts. The products manufactured by the HDPE blow molding process have stable chemical and physical properties, can adapt to various outdoor activities, and are easy to process, with strong flexibility and adaptability.
Properties of Blow Molding Material HDPE
HDPE blow molding is widely used in the manufacturing of food packaging and industrial containers, primarily due to its advantages and unique properties.
High-density polyethylene (HDPE) is polymerized from ethylene monomers under low pressure, hence it is also known as low-pressure polyethylene. It has a low density of 0.9410.965g/cm2 and can produce lightweight products. The appearance is a white powder or milky white flattened spherical, with high surface hardness and crystallinity of up to 80%~90%, making it a classic crystalline material. During the blow molding process, the softening temperature of HDPE material is 120-130 ℃, and the operating temperature is around 105 ℃.
HDPE blow molding material has outstanding characteristics, including high strength, hardness, stiffness, glossiness, creep resistance, and moisture permeability resistance. Its chemical properties are good, and it can withstand chemical reagents such as oil, grease, acid, and alkali. HDPE material for injection molding has good electrical insulation, tear resistance, impact toughness, and low-temperature resistance, but these properties are weaker than LDPE. However the material will be damaged by some strong oxidants because it cannot resist oxygen and carbon dioxide, and its impermeability is poor. The transparency of general HDPE materials is poor, and their toughness, flexibility, thermal-oxidative aging, and photo-aging properties are poor. They are prone to aging and becoming brittle under long-term outdoor use. Manufacturers generally use special-grade HDPE materials to manufacture blow-molded containers, because some general-purpose HDPE material blow-molded containers may experience stress cracking if they are used to hold detergents or some oily items for a long time, and their performance is not very strong.
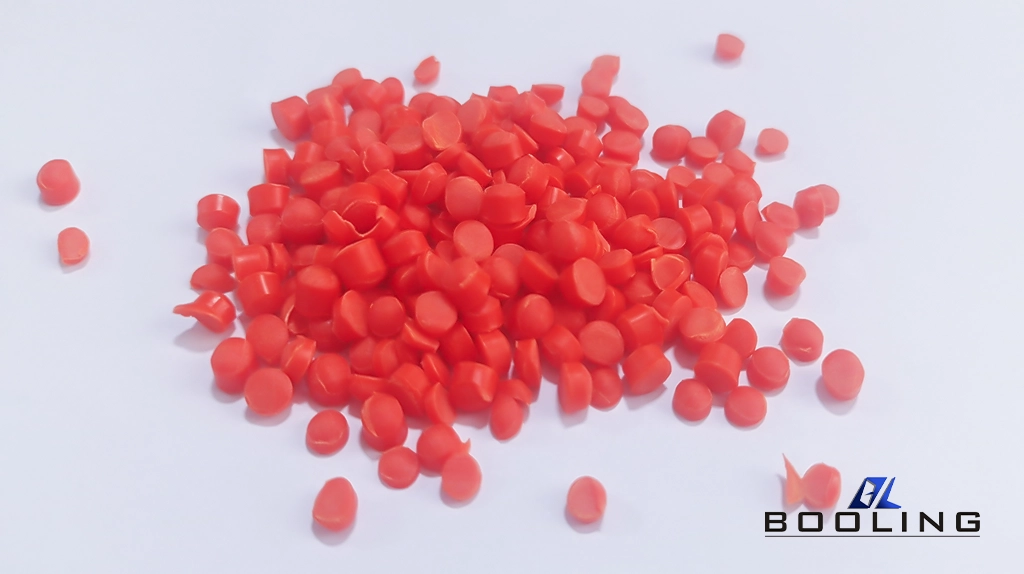
Characteristics of HDPE Blow Molding Processing
The HDPE material used in blow molding processing can generally be sterilized by heating and can be well applied in the field of medical devices. Its processing characteristics mainly include:
The HDPE material used in the extrusion blow molding process has a melt flow rate of 1g/10min or less and generally has a molecular weight distribution range from medium to wide. The HDPE material with this characteristic has a lower melt flow rate, which can make the formed billet have better melt strength, and can also change the self-weight sag of the billet to a certain extent; In addition, a wider molecular weight distribution of HDPE can reduce die pressure, decrease the fracture of the preform melt, improve production speed, enhance processing performance, and provide more efficient processing technology.
The HDPE material used for injection blow molding should have a medium to wide molecular weight distribution range and maintain a melt flow rate of 1g/10min or higher. In addition, a special feature is that when producing cosmetic or shampoo bottles using injection blow molding, a small amount of lubricant (such as 0.1%~0.5% zinc stearate) can be added to the HDPE blow molding material, or HDPE with a narrow molecular weight distribution range can be used. This material can improve the surface roughness of the bottle and provide better appearance performance.
High-density polyethylene (HDPE) is widely used by manufacturers in blow molding to produce various containers and bottles. Its products can be hot-filled and steamed for disinfection, which makes it widely used in the medical field; In addition, it can be used as packaging for various chemical industrial products such as acid, alkali, salt solutions, and organic solvents; Its smaller water absorption can also make it suitable as a moisture-proof packaging. In addition, HDPE can also manufacture high-quality components, such as HDPE blow molded flooring filled with mica, car seats, and air purifier casings, bringing higher comfort and appearance performance.
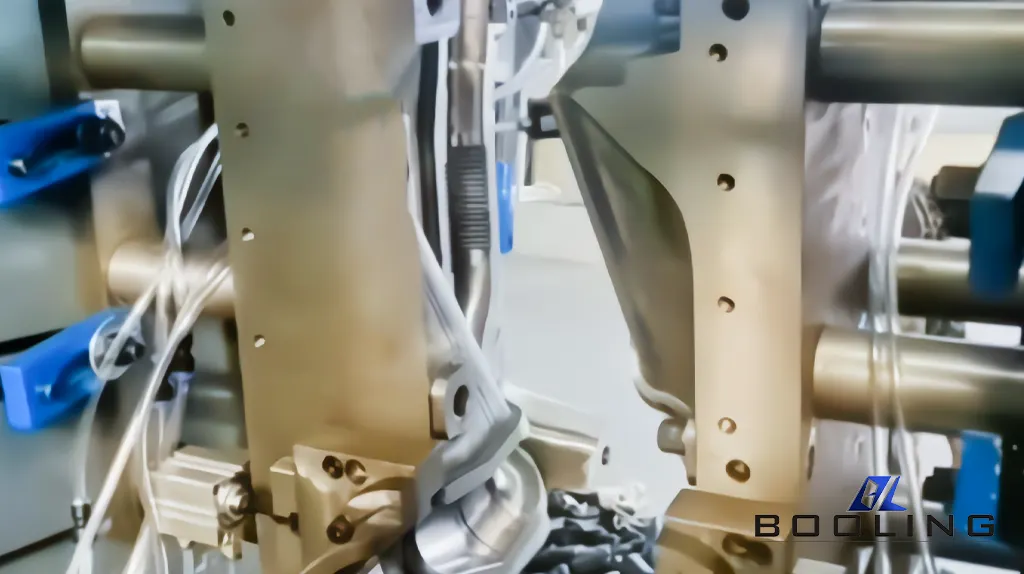
HDPE Blow Molding Processing Type
The types of HDPE blow molding are mainly divided into extrusion, one-step, and two-step blow molding. The specific principles and processes include:
- Extrusion blow molding
HDPE extrusion blow molding is mainly achieved by continuously extruding hollow tubes (preforms) through an extruder, then manually cutting them with scissors or using an automatic cutting device to cut them into small sections, and then moving them into an extrusion blow mold for blowing molding.
Advantages: Extrusion blow molding requires less investment, has simple equipment, is cost-effective, and can be quickly put into production.
- One-step method of “injection blowing”
Under the one-step blow molding method, the “injection and blow molding” of HDPE raw materials can be completed on the same machine. The one-step equipment is divided into two-station and three-station “injection blowing” according to different models.
The three stations of the three station “injection blowing” bottle-making machine are distributed in an equilateral triangle at a 120 ° angle. The three stations are the injection molding station, HDPE blow molding station, and bottle removal station. These three workstations can operate simultaneously, greatly reducing the molding cycle and achieving high production efficiency. In addition, manufacturers usually connect it to a conveyor belt for automatic counting and packaging, which can ensure the cleanliness of the product and achieve “non-contact” with human hands throughout the entire production process, without the need for subsequent disinfection steps.
The two stations of the “injection blowing” plastic machine can be arranged vertically or forward and backward, namely the injection molding station and the blow molding station. Due to the lack of a dedicated bottle removal and cooling station in the two-station blow molding process, it is difficult to achieve fully automatic counting and packaging under this technology. Generally, bulk manual counting is used, which greatly slows down the production cycle and cycle efficiency.
Advantages: The one-step HDPE blow molding process has a high degree of automation and high production capacity. The containers produced have high flatness at the bottle mouth and excellent sealing. The raw materials for this process are generally HDPE or PP, which produce bottles with uniform walls and excellent barrier properties. In the production of medicine bottles, they can maintain a long shelf life. At present, the one-step blow molding method adopted by manufacturers is mainly based on three-station equipment.
Two-step method of “injection blowing”
The two-step blow molding of HDPE material is divided into two steps: injection and blow molding, which are carried out on two different equipment processes.
- Start by injection molding the preform, which can be done on a regular injection molding machine. At this point, the bottle mouth of the preform has already been formed;
- After completing the injection molding of the preform, the manufacturer needs to heat and adjust the temperature of the preform, mainly by placing it on a honeycomb shaped heater or an automatic circulating heating conveyor belt, moving it to a bottle blowing machine, and blowing it into shape with compressed air to form a hollow container.
Advantages: The bottle mouth produced by the two-step HDPE blow molding process is relatively flat and has good sealing performance. The manufacturing equipment is relatively simple, with less investment and faster production speed. The development of new varieties is fast, the manufacturing cost of molds is low, and the cost price is high; Moderate, and low.
HDPE blow molding customization services account for a large proportion of the manufacturing of plastic containers. It has excellent electrical insulation, impact resistance, and toughness, and holds a high position in manufacturers’ blow molding solutions.
Blow Molding Related Content
Applied’s expertise in modifying materials at atomic levels and on an ihdustrial scaleenables our customers to transform possibilities into reality.