Home > HDPE Extrusion Blow Molding: Key Processing Overview
The key process of HDPE extrusion blow molding lies in the manufacturing of the preform. In this process, manufacturers need to control the temperature, pressure, and cooling time of blow molding equipment to ensure the final quality of the product.
Advantages of Blow Molding:
- Excellent Chemical Resistance
- Durability and Impact Strength
- Moisture Resistance
- Cost-Effectiveness
HDPE blow molding is a widely used molding technology, among which extrusion blow molding is the most common. Its principle mainly involves two steps, including the extruder heating and melting the plastic raw material, and then pushing it through a screw to form a tubular billet; Then place the tubular billet into the heating mold, use compressed air to inflate it, tightly adhere to the inner wall of the mold cavity, cool and solidify to form the desired part.
Precautions for HDPE Extrusion Blow Molding
HDPE extrusion blow molding is similar to ordinary plastic blow molding, both have molding precautions. The setting of molding precautions can effectively avoid the occurrence of some adverse phenomena and obtain higher-quality products.
- Raw materials
From the usage pattern of plastic blow molding raw materials, manufacturers should pay attention to changes in the composition, intercomposition, and source of raw materials; The additives, moisture content, pre-mixing, and pre-drying steps of the initial raw materials cannot be ignored. Manufacturers need to follow the specified process requirements, such as drying some materials with high moisture content before processing and mixing some materials that require additives in advance.
- Personnel quality
To effectively solve the problems that arise during the HDPE blow molding process, manufacturers should focus on two main aspects: having good control instruments and mastering the process rules to have a detailed understanding of the entire HDPE extrusion blow molding process. For production control, manufacturers cannot do without precision instruments. Even if manufacturers have a good understanding of the production process, without precise control instruments that meet production requirements, some problems will not have good solutions, especially unexpected events that are not within the scope of pre-consideration in production. If not properly resolved, it will lead to corresponding cost increases.
- Feeding speed
The feeding speed of the extruder determines the process stability of HDPE extrusion blow molding. If there is an unstable feeding phenomenon during the extrusion blow molding process, manufacturers should consider whether there is a problem with the transportation of solid materials; Has the density changed, or has low-density addition has been carried out; Is there any bridging phenomenon in the hopper that caused material breakage. Secondly, it is necessary to check whether there are any issues with the friction performance of the feeding system; Pay attention to whether the insufficient filling in the screw groove is due to the fast rotation speed of the screw and the low feeding rate. Finally, it is necessary to consider whether these issues are related to the design of the feeding system or screw feeding section.
- Uniformity of feeding
During the feeding stage, only by maintaining the uniformity of the feeding can HDPE blow molded products maintain consistent performance; Manufacturers can make full use of recycled materials and constantly understand the changes in the impact of the proportion of recycled materials added on quality.
Heating Device for HDPE Extrusion Blow Molding
The plastic products produced by plastic mold manufacturers are applied in many fields, and people are increasingly dependent on plastic products. Plastic products are mainly used in the following fields and industries:
The initial step of HDPE extrusion blow molding equipment is the plasticization and melting of plastic raw materials, which relies on a heating device. At present, the most commonly used devices for extruders are resistance heating and electric induction heating, with resistance heating devices being the most commonly used, including strip heaters, cast aluminum heaters, and ceramic heaters.
Resistance heating device
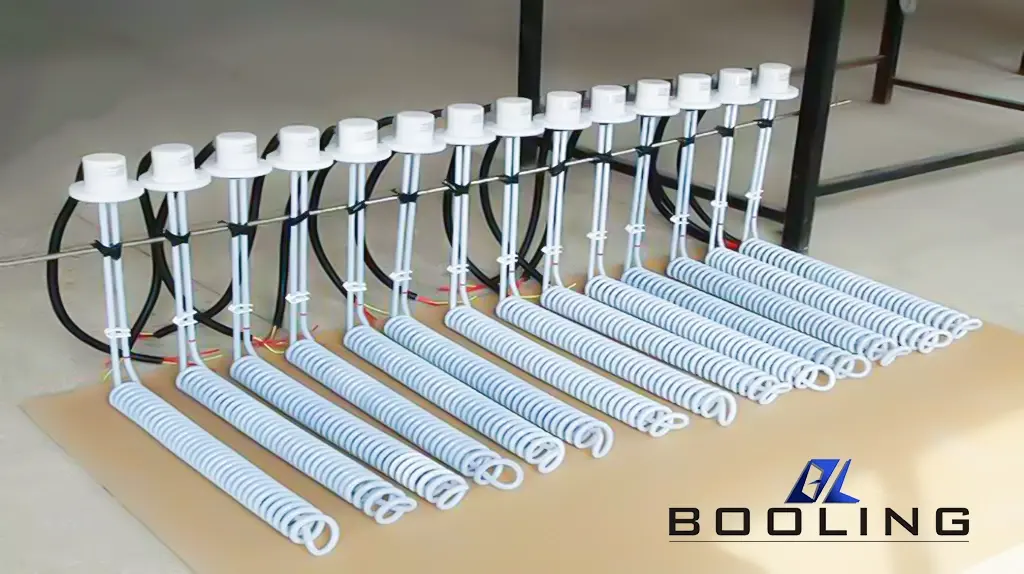
- Belt heater
A belt heater is a device that wraps resistance wires in mica sheets, covers them with iron sheets, and then surrounds them on the barrel or head of the machine. This type of heater has good toughness and is relatively inexpensive, but its durability is not high and it is easy to damage. When the heating temperature reaches 500 ℃ or above, mica will oxidize, resulting in the loss of its original performance. The heater should have good contact with the barrel. Improper installation can cause irregular overheating of the barrel and damage to the heater itself.
- Cast aluminum heater
A cast aluminum heater is a device in which a resistance wire is installed in a metal tube, surrounded by insulating materials such as magnesium oxide powder, bent into a certain shape, and then placed in a mold to be cast into the desired shape using aluminum alloy. To make loading and unloading easier, cast aluminum heaters are generally composed of two pieces. This equipment has low cost, can be shock resistant, explosion-proof, oxidation resistant, moisture-proof, durable, and has a long service life. The heat transfer efficiency of this device is very high, and the maximum heating temperature can reach 400 ℃. However, the temperature fluctuations of this device are significant, and manufacturers need to choose carefully.
- Ceramic heater
A ceramic heater is a device that passes resistance wires through ceramic blocks and then fixes them in an iron shell. This heater has the characteristics of high-temperature resistance, pollution resistance, long service life (even up to 4-5 years), and good insulation. The maximum heating temperature can reach 700 ℃, which can easily meet the processing requirements of engineering plastics that require high-temperature heating in some modern plastic processing industries.
Electric induction heating device
The electric induction heating device is composed of several sets of silicon steel sheets with main coils on the outer wall of the barrel at certain intervals. When manufacturers connect AC power to the main coil, electromagnetic waves are generated. When the electromagnetic waves pass through the silicon steel sheet and the barrel, they form a closed circuit, which generates induced electromotive force, causing secondary induced voltage and induced current. This current is also called eddy current.
This type of vortex will generate shear heat when it encounters resistance in the barrel. When using an electric induction heating device, the preheating and heating time is generally short, the heating is relatively uniform, and the temperature gradient in the radial direction of the barrel is relatively small; Can save electricity, and can about 30% of energy compared to resistance heaters; Being able to adjust temperature sensitively is one of its major advantages over ceramic heaters; Good durability and relatively long service life. However it is not suitable for processing plastics with high-temperature requirements, mainly because its heating temperature is limited by the insulation performance of the induction wire package.
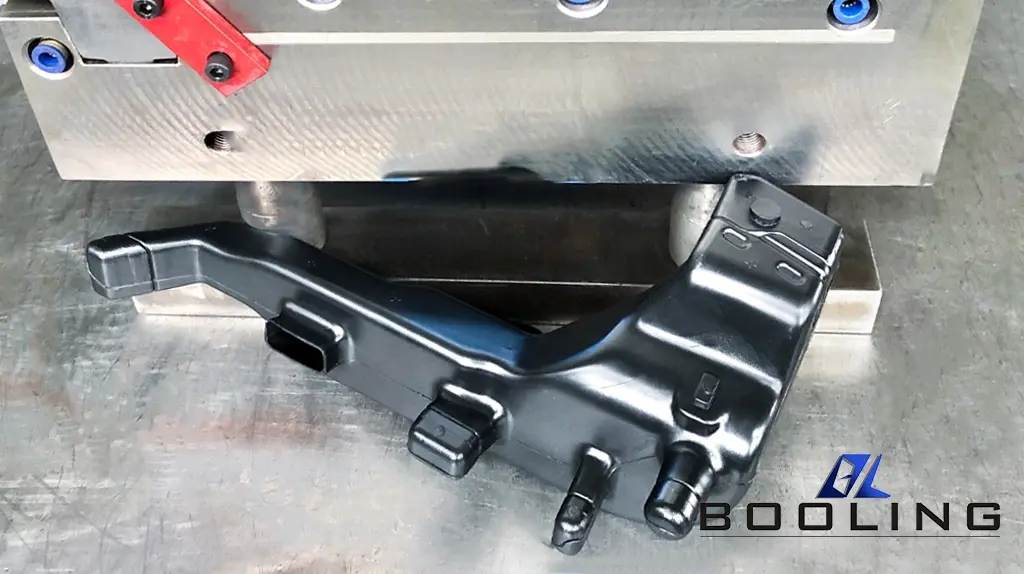
Common Defects and Solutions of HDPE Extrusion Blow Molding
The process of HDPE extrusion blow molding is not smooth, and there are many problems and defects. Manufacturers have obtained corresponding solutions based on experience and practice.
- Bending of the billet
-Reason
(1) The flow channel inside the machine head is blocked, causing poor feeding
(2) Uneven heating temperature of the machine head
(3) The extrusion speed is too fast, resulting in unstable molding
(4) Improper setting of mold position
-Solution
(1) Correct the head flow channel and check for blockages
(2) Adjust or redesign the position of the mold
(3) Reduce the extrusion speed to maintain stability as much as possible
(4) Check the head heater and maintain a uniform temperature for heating
- Severe sagging of the billet
-Reason
(1) The closing speed of the mold is too slow
(2) The melt temperature is too high, resulting in a longer cooling time
(3) The extrusion speed of the billet is too slow
-Solution
(1) Adjust the temperature of the material cylinder and machine head
(2) Appropriately accelerate the closing speed of the mold
(3) If possible, the extrusion speed can be appropriately increased
- The product has longitudinal stripes
-Reason
(1) Mold roughening reduces surface smoothness
(2) foreign objects are blocking the mouth mold of the machine head
-Solution
(1) Repair the light mold
(2) Remove residues from the mouth mold
- Product warping and deformation
-Reason
(1) The cooling time of the product is insufficient or the mold opening time is too early
(2) The intake speed is too slow
(3) The inflation time was too short to make the billet tightly adhere to the inner wall
-Solution
(1) Immediately introduce gas for inflation after closing the mold
(2) Increase coolant flow or extend cooling time
(3) Extend the blowing time
- Billet edge rolling
-Reason
(1) When rolling outward, it is necessary to consider that the mold core temperature is too high
(2) If it rolls inward, it is necessary to consider that the mold temperature is too high
-Solution
(1) Reduce the mold temperature appropriately
(2) Reduce the temperature of the mold core
(3) Adjust the gap of the mouth mold
- Uneven thickness of the product
-Reason
(1) Uneven heating of the machine head
(2) The position of the mouth mold is incorrect
(3) The center of the machine head is inconsistent with the center of the forming mold
(4) Improper adjustment of billet control points
(5) Improper correction of mold core
-Solution
(1) Adjust the center of the machine head and mold
(2) Adjust the gap between the mouth mold
(3) Adjust the control point position of the billet again
(4) Check the head heater
(5) Revise or redesign the mold core
The products produced by HDPE blow molding are applied in various fields, not limited to various buckets, bottles, cans, boxes, etc. The advantages of HDPE extrusion blow molding mainly lie in its ability to produce products with more uniform wall thickness, more stable size, lighter weight, and higher strength.
Blow molding related content
Applied’s expertise in modifying materials at atomic levels and on an ihdustrial scaleenables our customers to transform possibilities into reality.