Home > Key Points of 3D Blow Molding Design
Details
Details:
Model
Material
Brand
Origin
Application
Booling-Blow Mold-1
P20, 718, S136, 2738 etc
Booling
China
Home Appliance parts
3D blow molding, also known as edgeless blow molding technology, can achieve high-quality design and manufacturing of complex automotive pipes, meet the requirements of one-piece molding of curved surfaces and bends, and the dimensional accuracy can reach the millimeter level.
Advantages of 3D blow molding:
- Achieve integrated molding of complex shapes
- High dimensional accuracy
- Good product appearance quality
- Generate less waste
Related Hot Products
Based on the traditional blow molding process, the 3D blow molding process is more complex and sophisticated and can produce products with higher quality and precision. Booling Engineers have further optimized the molding parameters through computer simulation technology and advanced CNC systems, effectively improving production efficiency and reducing production costs.
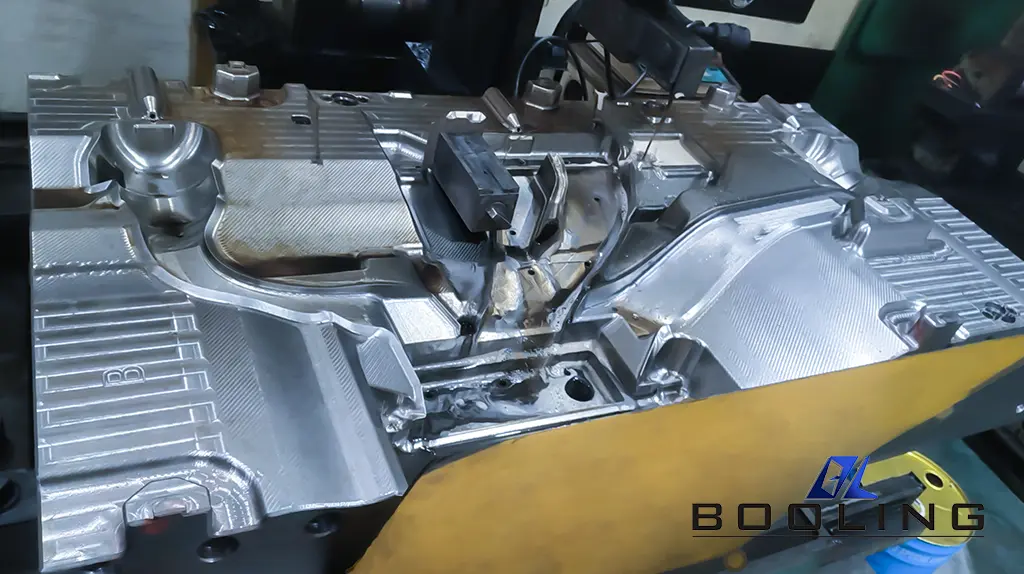
Significant Advantages of 3D Blow Molding
3D blow molding is usually used in exhaust pipe automotive molds. It can be combined with automation technology to achieve complex molding solutions.
- 3D printing technology has the advantage of no welds. The material has good fluidity when under pressure and heat, and can be better ductile in the mold to achieve one-piece molding. It does not require the use of traditional welding processes and will not produce welds.
- It has higher cost-effectiveness, almost no waste is generated during the processing, and the amount of material used can be accurately controlled, further reducing costs.
- High production efficiency and avoid post-processing procedures. For some products with more complex shapes, 3D blow molding has a shorter production cycle.
- The design is more flexible, realizing the design of complex shapes such as curved surfaces to meet the functions and needs of different products.
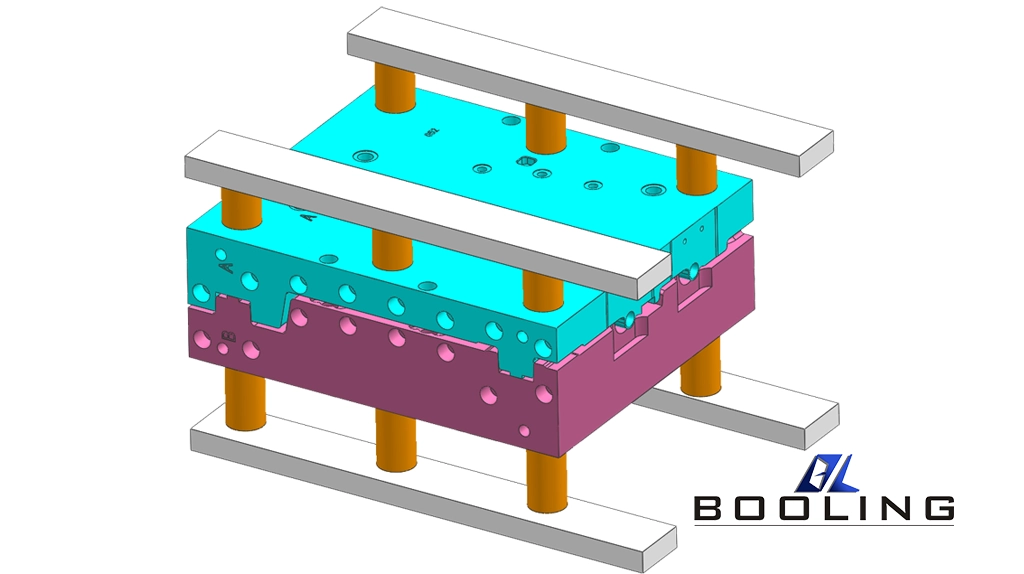
Key Points of 3D Blow Molding Mold Design
3D blow molding has a complex design and has a precise cavity, core, exhaust, cooling system, and other structures.
-Material
You can choose HDPE, PP, PVC, PET, PS, and other materials, considering the product’s use requirements, performance characteristics, and processing technology.
-Cavity
- Structural form
When designing a 3D blow molding cavity, manufacturers can consider a two-flap or three-flap design that separates the bottom mold.
- Demolding form
To facilitate product demolding, the bottom is usually designed to be concave. For hard containers, a fixed bottom template is used, allowing the maximum depth of the bottom to be de-molded to be up to 0.8mm. When the depth of the recess is large, the manufacturer can install a sliding bottom module in the mold and configure a cylinder, tilting slider, or spring push mechanism to further improve the demolding quality. When the concavity of the bottom of the soft plastic container is less than 5mm, its elasticity can be used for demolding, thereby improving the demolding efficiency.
– Exhaust groove
In order to smoothly discharge the gas carried in the mold cavity, when designing a 3D blow mold, the manufacturer must consider and design the location and number of exhaust pipes. For non-large products, manufacturers usually design the width of the exhaust groove to be about 10mm and the depth to be 15-20mm, which will be designed according to the actual situation. In addition to using exhaust grooves, manufacturers can also use the mating surface between the collar block and the cavity for exhaust.
– Bottom module
- Material
Generally, the same material is used for blow molding molds.
- Bottom groove size design
The design of the bottom groove affects the demolding level of the blow molded product, and the size should match the overall size of the product. For large products, the bottom groove needs to be large enough to support the bottom of the product.
- Bottom shape
The shape of the bottom module is usually concave, which can increase the axial stretch molding area of the container and form a bottom with a relatively uniform wall thickness. To facilitate the manufacturer’s demolding, the bottom module can be made into a whole or two parts that are separately fixed in the two blow molding half-cavities.
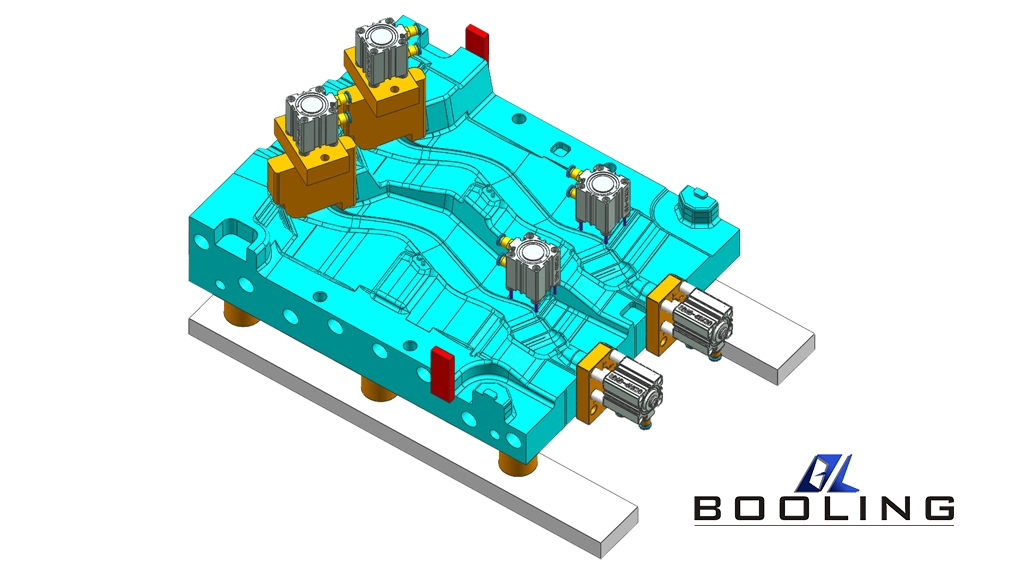
3D Blow Molding Parameter Setting
During the 3D blow molding process, the main parameters include billet temperature, mold temperature, inflation ratio, inflation speed and pressure. The setting of these parameters determines the production quality and precision of 3D blow molded parts.
- Setting of temperature and cooling time
During the 3D blow molding process, the temperature of the mold is usually designed to be in the range of 20~50℃. Too high or too low mold temperature will affect the quality of the final molded parts.
By installing a temperature regulation system, such as a temperature sensor, the processing temperature and cooling time of plastic parts can be controlled more accurately.
- Parison temperature setting
The setting of the billet temperature will directly affect the ability of blow molding. It is generally controlled between the glass transition temperature and softening temperature of the plastic and has the ability to blow molding while maintaining a certain fluidity.
- Blow molding speed
The speed in the blow molding process mainly designs the parison extrusion speed, inflation rate, etc. The parison extrusion speed is related to the properties of the material, the structure and shape of the product. The inflation speed is affected by the size, shape and wall thickness of the product.
- Blow molding pressure
Blow molding pressure is usually set between 0.2 and 0.7 MPa. For products with thinner walls and larger sizes, a higher pressure is usually required.
Automotive Mold Related Content
Applied’s expertise in modifying materials at atomic levels and on an ihdustrial scaleenables our customers to transform possibilities into reality.