Home > Plastic Blow Molding Material Selection Guide
Details
Details:
Model
Material
Brand
Origin
Application
Booling-Blow Mold-1
P20, 718, S136, 2738 etc
Booling
China
Home Appliance parts
Plastic blow molding technology can produce seamless hollow parts. This molding technology can be used with a variety of materials. It can also be combined with a reinforcing rib structure to effectively enhance the product’s load-bearing capacity and strength, reduce problems such as warping and deformation during molding, and quickly produce high-quality products.
Advantages of plastic blow molding:
- Save materials and reduce costs
- High production efficiency
- Can produce seamless hollow products
- Flexible product design
Related Hot Products
In plastic blow molding, it is necessary to carefully select the appropriate material based on the material’s mechanical properties, processing properties, shrinkage rate, and other parameters. Common materials suitable for blow molding include polyethylene, polypropylene, polyvinyl chloride, polystyrene, etc. HDPE blow molding and ABS blow molding are more commonly used in the automotive and packaging blow molding fields.
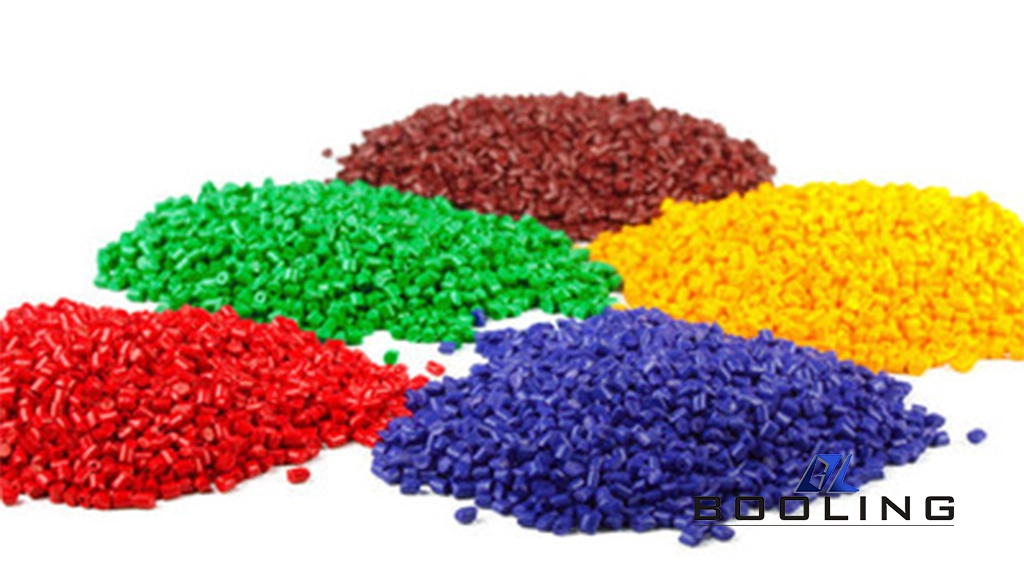
Classification of Plastic Blow Molding Raw Materials
Plastic raw materials used for plastic blow molding are classified according to different characteristics, and manufacturers choose according to application requirements and product characteristics.
-Classification by Use
- General plastics: General plastics have large output, easy molding, wide application, and good processing performance. Common general plastics include polyethylene, polypropylene, polystyrene, polyvinyl chloride, etc., which can be used to manufacture blow molding products in the fields of construction, packaging, agriculture, and daily consumer goods.
- Engineering Plastics: Engineering plastics have excellent physical and chemical properties, can remain stable during blow molding, and are resistant to high temperatures. Polycarbonate, polyamide, polyphenylene ether, polyoxymethylene, etc. are all engineering plastics, which play a great role in blow molding in precision fields such as electronics, industrial machinery, aerospace, and automobiles.
- Special Plastics: Fluoroplastics, polysulfones, silicones, etc. are special plastics used to process products with special performance requirements.
-Classification by Heating State
- Thermoplastics: Thermoplastics can be made into various products through the process of heating, softening, and cooling with the help of molds. After cooling and hardening, plastics can be heated again and processed, and the material utilization rate is high. When processing thermoplastics, only physical changes occur, which is both environmentally friendly and safe. Common thermoplastics include polystyrene, polyvinyl chloride, nylon, polyoxymethylene, ABS, plexiglass, polyamide and polycarbonate.
- Thermosetting Plastics: Thermosetting plastics will slowly soften after heating and have a certain plasticity. However, when the temperature reaches a certain critical value, it will solidify. After that, no matter how high the temperature is, it will not melt again. Instead, it will decompose and carbonize, and it is insoluble in various solvents. Chemical changes will occur during the processing of thermosetting plastics, and this change is irreversible. Common thermosetting plastics include silicone plastics, amino plastics, phenolic resins, epoxy plastics, etc.
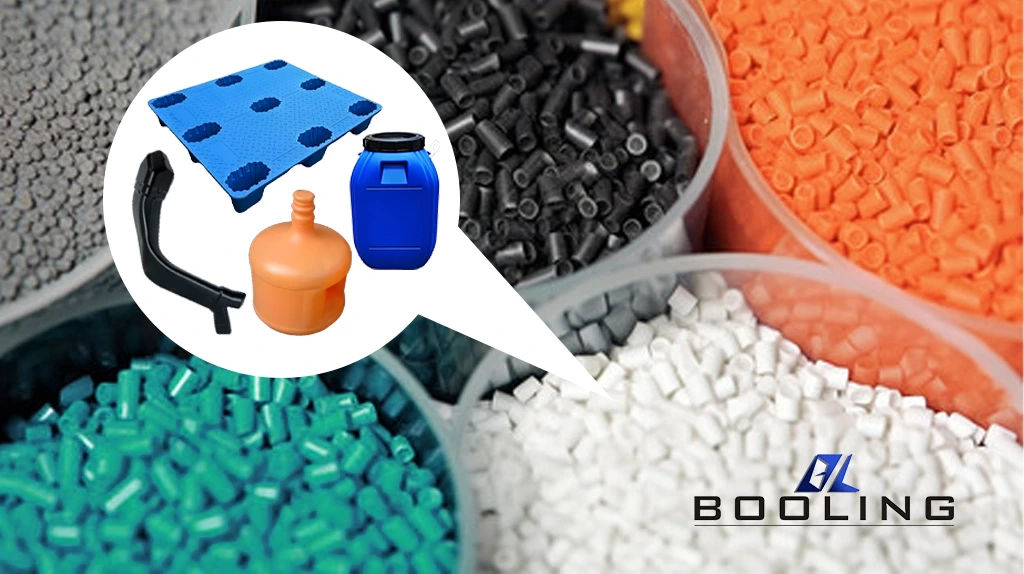
Selection of Plastic Blow Molding Materials
There are many raw materials available for plastic blow molding, and the processing methods are also flexible.
- Polypropylene (PP): Polypropylene has good surface transparency, good mechanical properties, waterproofness, and heat resistance, and can remain stable at high temperatures. It is mainly used for packaging blow molding of food, medicines, detergents, cosmetics and other products.
- Polyethylene (PE)
LDPE: LDPE has high transparency and good resistance to environmental stress cracking. It is mainly used for blow molding of small containers and folding bottom packaging containers.
HDPE: HDPE has good processing performance, rigidity, and toughness, and is often used for blow molding various plastic containers, such as pallets, air ducts, bus chairs, outdoor folding tables, refrigerators, etc.
- Polycarbonate (PC): Polycarbonate has high transparency, strong impact resistance, high strength, and surface hardness, and is hygienic, non-toxic, and heat-resistant. It is suitable for manufacturing products that require high-temperature disinfection, such as thermos, heat-resistant baby bottles, pure water turnover barrels, etc.
- Polyvinyl chloride (PVC): Manufacturers can change the properties of PVC materials by adding additives or adjusting the formula to make it less hazy, with better gas barrier properties, transparency, and impact resistance. Mineral water bottles, cooking oil bottles, detergent bottles, etc. are often made of PVC.
- Polyamide: Polyamide has high strength, high rigidity, good heat resistance, and oil resistance, and is often used to make automobile fuel tanks.
- Polystyrene (PS): Polystyrene has very good transparency, is easy to dye, and has a good appearance. It has good processing fluidity during injection molding, low molding shrinkage, good water resistance, chemical corrosion resistance and rigidity, and can be blown into various specifications of medicines and plastic food packaging bottles.
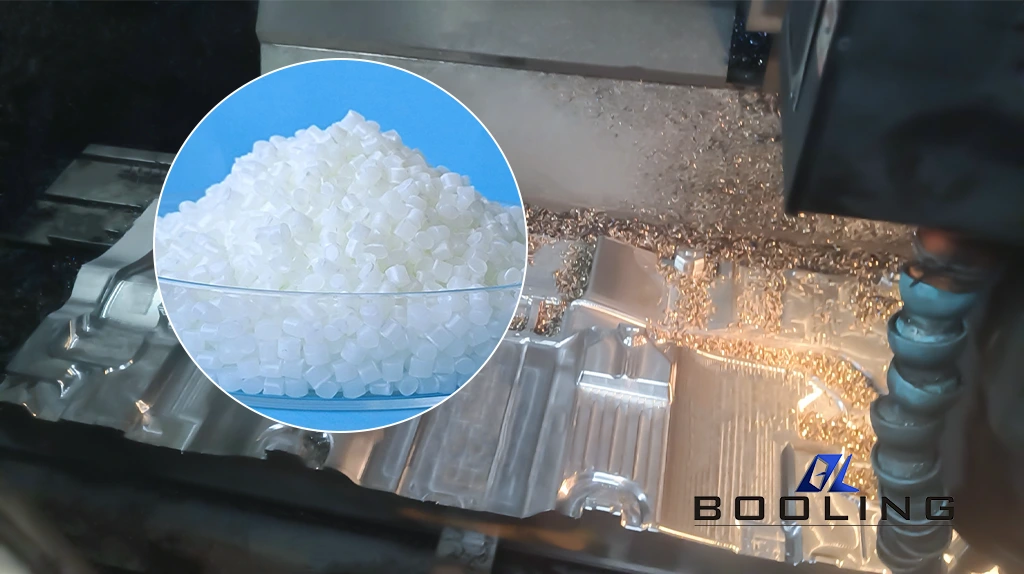
Raw Material Processing for Plastic Blow Molding
Before plastic blow molding, some plastic raw materials must be cleaned, dried and pre-processed before they can be used in production.
- Manufacturers must understand the performance and processing requirements of the materials, such as the water absorption rate, shrinkage rate, and other parameters of the materials, and also know whether the raw materials and additives are biocompatible, so as to achieve the best processing effect.
- Strictly inspect the purchased materials to check for color differences, impurities, and other problems. Many plastic raw materials are easy to absorb water during storage and transportation, which will have adverse effects.
- Before molding, the raw materials can be preheated to improve the plasticity and fluidity of the raw materials, making the plastic easier to shape during blow molding.
Automotive Mold Related Content
Applied’s expertise in modifying materials at atomic levels and on an ihdustrial scaleenables our customers to transform possibilities into reality.