Home > A Guide to the Basics of Plastic Blow Molding
Details
Details:
Model
Material
Brand
Origin
Application
Booling-Blow Mold-1
P20, 718, S136, 2738 etc
Booling
China
Home Appliance parts
Plastic blow molding technology is suitable for producing various hollow plastic products, such as automotive air ducts, chemical containers, household items, toy models, medical bottles and cans, etc. It has the characteristics of efficient molding. According to the long-term practice of our engineers, automated blow molding is particularly suitable for large-scale production of lightweight plastic parts. Through its precise mold control and air pressure molding, it can achieve high-quality products with uniform wall thickness and reliable strength. Blow molding products also have the advantages of no flash, fast molding, and material loss of less than 2%.
Advantages of plastic blow molding:
- It has high production efficiency
- The quality of the products produced is good
- The cost is relatively low
- The wall thickness of the product is uniform
Related Hot Products
Our engineering team has accumulated rich experience in applying materials such as HDPE and ABS. By optimizing the air compression system and screw extrusion process, we ensure that the parison is perfectly formed in the mold. Whether it is traditional plastic blow molding or the emerging 3D blow molding and stretch blow molding, they all have their unique processes and characteristics and are widely used by plastic product and mold manufacturers.
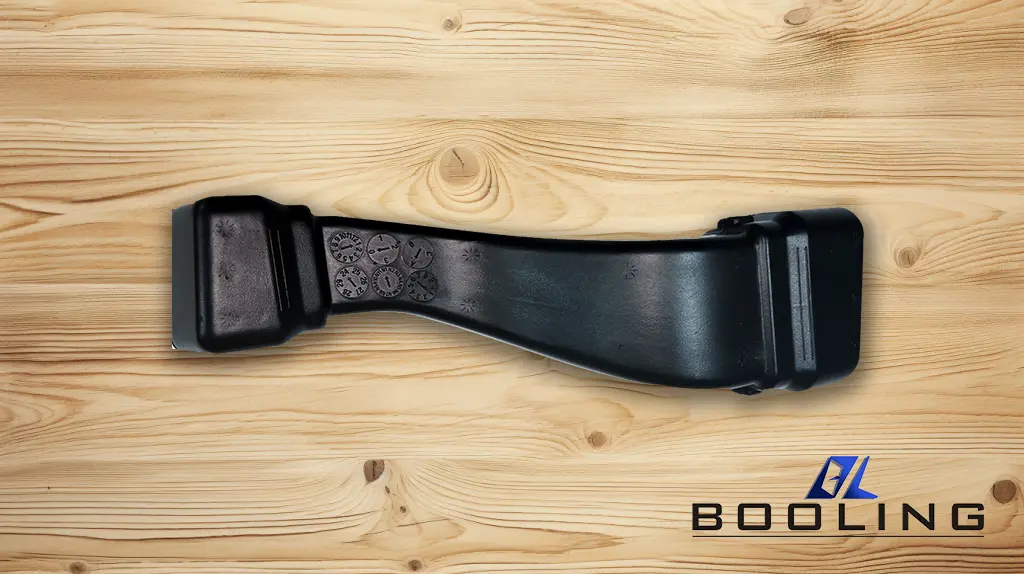
Booling Plastic Blow Molding System
Booling provides two processes, hollow blow molding, and film blow molding, to provide customers with a one-stop solution from process selection to intelligent processing.
-Hollow Blow Molding
Hollow blow molding relies on high-pressure gas to make products and realize the rapid processing of hollow products. Booling provides three major processes: injection blow molding, extrusion blow molding, and stretch blow molding, and uses precision molds to manufacture blow molded products.
- Injection Blow Molding
Our company is equipped with precision positioning equipment that can accurately mold the parison injected onto the core rod. After the parison cools, the core rod and the parison will be sent to the mold. After the mold is closed, compressed air is introduced through the core rod to blow the parison into shape. Products molded by injection blow molding do not require subsequent processing, and can directly process the bottle mouth thread, with excellent quality control.
- Extrusion Blow Molding
Extrusion blow molding first extrudes the molten plastic to make a preform, and when the preform reaches the predetermined length, it is clamped. Then compressed air is introduced to make the preform tightly attached to the mold cavity. After cooling, open the mold to take out the product, and then perform trimming and other subsequent processing. Our company is equipped with a professional twin-screw co-extrusion system, which can achieve rapid extrusion in a short time.
- Stretch Blow Molding
Stretch blow molding is also called biaxial orientation blow molding technology, which mainly includes one-step extrusion stretch blow molding, one-step injection stretch blow molding, two-step extrusion stretch blow molding, and two-step injection stretch blow molding. This process first uses the extrusion method to shape the blank and uses the biaxial stretch blow molding method to complete the stretching and blow molding of the blank in one machine. The physical properties of plastic products made by stretch blow molding will be significantly improved, such as stiffness, transparency, and gloss.
-Film Blow Molding
Film blow molding uses an extruder to make molten plastic into a thin-walled tubular blank, and then blows compressed air into the blank from the center of the head. Booling achieves precise film molding through precise control of pressure, temperature, and traction speed, and is widely used in the agricultural field.
“We believe that details determine quality”-Booling strictly controls every production link.
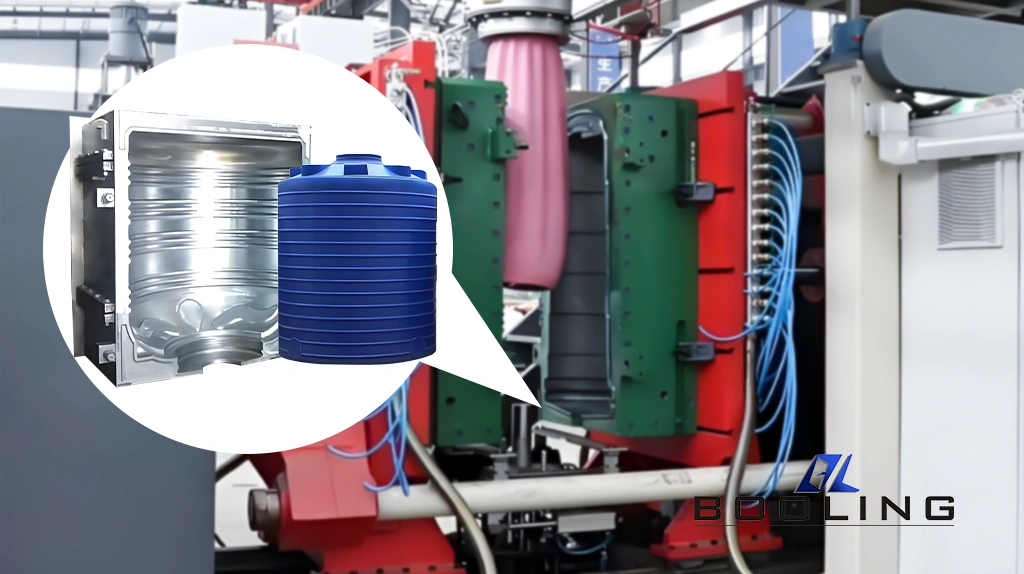
Booling Plastic Blow Molding Process
We strictly implement standardized operating procedures:
- According to the requirements of the product, our staff will select suitable raw materials to ensure that the raw materials have appropriate fluidity and stability.
- Put the prepared plastic raw materials into the extruder, heat them, and extrude them to form a tubular parison.
- When the parison reaches the set length, the clamping mechanism is closed, and the parison is clamped between the two halves of the mold. The clamping force of the mold must be uniform.
- Compressed air is introduced to allow the parison to expand and cling to the inner wall of the mold cavity. If there are patterns, text, or logos on the surface of the product, a higher pressure must be maintained.
- The mold is always kept closed, cooled, and shaped through the cooling channel, and an intelligent temperature control system is used to ensure the cooling effect and efficiency and shorten the molding cycle.
- We provide automated post-processing equipment and use manipulators and other equipment to ensure product removal efficiency.
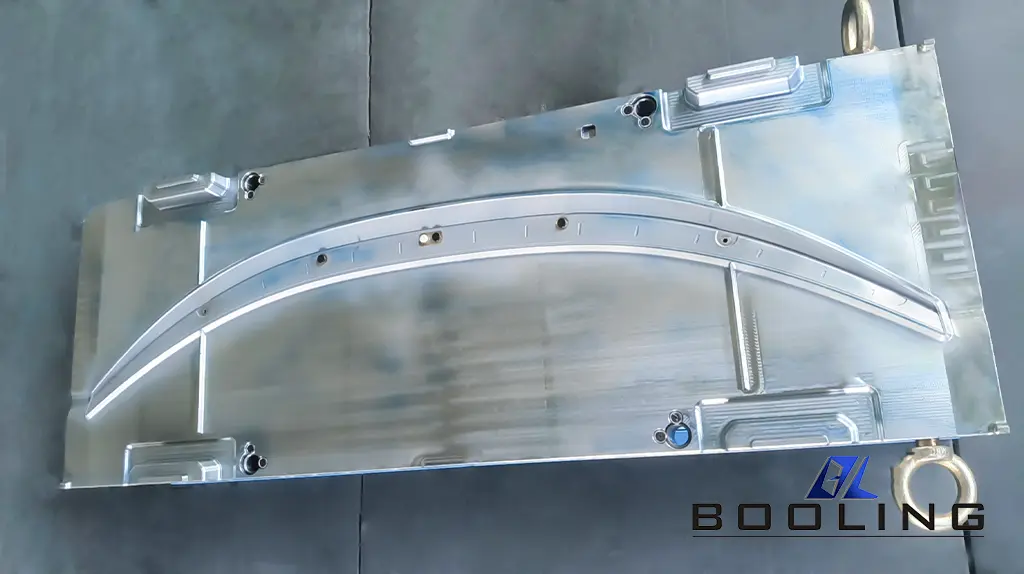
Booling Plastic Blow Molding Mold Maintenance System
Booling has established a complete mold maintenance system according to the requirements of the quality management system:
Improper mold storage will cause wear and tear, affecting performance. Our company is equipped with a special mold storage room, which is clean and ventilated to avoid excessive dust or humid environments, which may cause mold corrosion and reduced precision.
After the mold is removed from the machine or stored for a period of time, we will clean, lubricate, and rust-proof it, especially to clean the cooling water channel of the mold, add lubricating oil to all the transmission parts of the mold, to ensure that there is no abnormal sound when the equipment is running and the processing process will not be stuck. Anti-rust paint or anti-rust oil should also be sprayed on the surface of the mold to provide predictive maintenance.
There are many kinds of molds and equipment for plastic blow molding. We mainly classify and store them according to the variety, specification, and type of the product. Large and medium-sized molds can be classified and placed on the mold storage rack, and dust-proof film or cloth can be covered on the mold to prevent dust accumulation. Small molds can also be placed on the mold storage rack and numbered.
Three reasons to choose Booling:
- More than ten years of industry experience, professional and reliable technical team
- Complete quality control system, product qualification rate 99%+
- Quick response to customer needs, providing full technical support
Contact the Booling team now to get exclusive blow molding process solutions.
Automotive Mold Related Content
Applied’s expertise in modifying materials at atomic levels and on an ihdustrial scaleenables our customers to transform possibilities into reality.