Home > Stamping Die > Carbide Stamping Die
Carbide stamping die has good hardness and wear resistance, and have outstanding performance in corrosion resistance and high temperature resistance. Booling provides technical support and perfect after-sales service for the design and manufacturing of carbide stamping dies for sheet metal manufacturers in the automotive, electronics, home appliances, and other industries, and realizes the rapid delivery of high-precision sheet metal products. We have provided customized production solutions for carbide stamping dies for automotive parts companies in India, Mexico, Spain, Russia, and other countries.
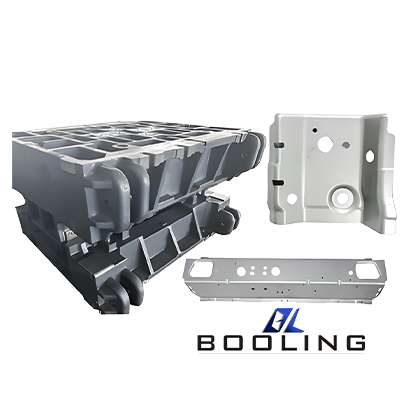
Carbide stamping dies are widely used in the processing of lightweight parts and metal materials. They can adapt to a variety of special working environments and maintain good strength and stability.
The Process of Carbide Stamping Die:
- Punching
- Drawing
- Forming
Carbide Stamping Die Capabilities
A carbide stamping die can realize the integrated design of complex structures, reduce the number of parts, improve processing efficiency, and reduce costs.
·
US
Metric
Alloy steel
68.9in.x 27.6 in.x17.7in.
1750mmx700mm x450mm
Carburized steel
68.9in.x 27.6 in.x17.7in.
1750mmx700mm x450mm
High speed steel
68.9in.x 27.6 in.x17.7in.
1750mmx700mm x450mm
*Carbide stamping die can better adapt to the diversity of processed materials, and have better adaptability and stability.
Carbide Stamping Die Material
Cemented carbide stamping dies are mainly made of carbide, which is different from traditional die steel in hardness, wear resistance, toughness, and processing performance. Cemented carbide is widely used in the processing and manufacturing of high-wear dies due to its high hardness and high wear resistance.
Material
- Alloy Steel
- Carburized Iron
- High-speed Steel
The Advantages of Carbide Stamping Die
A carbide stamping die is usually made of tungsten-cobalt carbide as the main material. The sintered material has high hardness, high strength, and excellent wear resistance, which is suitable for mass production of sheet metal parts.
- It has high surface hardness and wear resistance, can withstand strong impact and tens of thousands of frictions, and has a long service life
- It has good high-temperature stability
- It can achieve high-precision processing and maintain the consistency of parts
- It has good chemical resistance and can resist corrosion from acids, alkalis, organic solvents and other substances
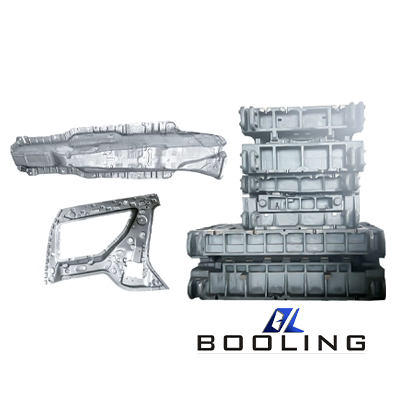
Application of Carbide Stamping Die
Carbide stamping die has been widely used in sheet metal processing in the fields of automobiles, construction, electronic equipment, etc., shortening the product delivery period of precision parts.
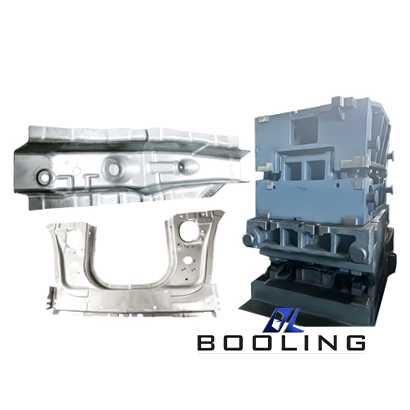
Guidelines for Carbide Stamping Die
Booling provides carbide stamping die customization services and a large number of stamping sheet metal parts. Users can select according to their needs to achieve a high degree of matching between products and needs.
Carbide stamping dies can be used in high temperature, high pressure, and high friction environments and maintain a long life. Compared with ordinary metal sheet processing, they are more cost-effective. Booling provides more cost-effective carbide stamping die solutions.
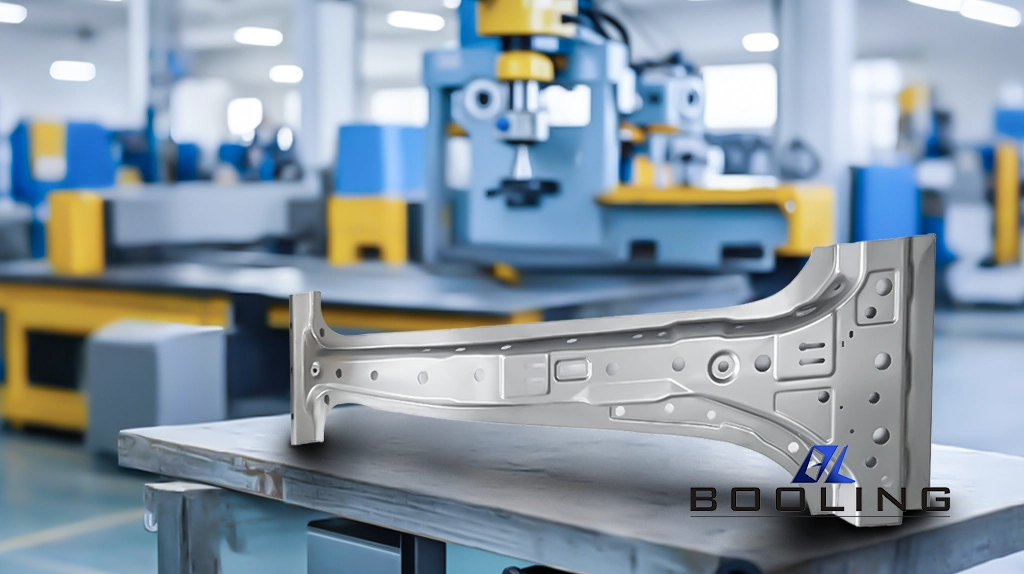
Carbide Stamping Die Process
Every step of carbide stamping die processing determines the quality of the final product. Booling provides one-stop services including die design, material selection, die manufacturing, inspection, and assembly.
- Die Design: According to the product structure, purpose, and size, use CAD and other software to design the 3D model of the die, including the punch, base, guide column, etc. of the die
- Material Selection: Order carbide materials to meet the shape and size requirements of the parts
- Die Manufacturing: Engineers process and manufacture stamping dies according to the 3D model, use electric sparks and precision grinders for fine processing, and cut metal materials into designed sizes and shapes. Perform heat treatment and processing on the die surface, polish, and grind as required to obtain high-quality die surface
- Inspection and Assembly: Assemble the prepared die according to the 3D drawings and assembly drawings to ensure that the opening and closing action of the die and the processing accuracy meet the requirements. Place the prepared material on the stamping machine and use the die for trial processing to ensure that the sheet metal parts can be formed smoothly
Carbide Stamping Die Process
The production of sheet metal parts in different application industries requires different dies. Booling provides the production of stamping dies such as punching, bending, stretching, and forming to meet the requirements of different industries.
- Punching die: The press applies pressure to the metal material to produce deformation or separation to obtain the required shape and size. The punching die is suitable for the manufacture of products such as automobile shells, brackets, and electronic product shells.
- Bending die: The bending die can be used to bend the metal blank into the required shape and angle, and is used in the production of various mechanical parts, such as gears and bearing sleeves of automobile engines.
- Stretching die: Through the action of the carbide stamping die, the metal sheet is formed into an open hollow piece under the action of tension, which is suitable for the processing of various connectors.