Home > Automotive Checking Fixtures | Parts Inspection
Checking Fixture
The characteristics of automotive checking fixture are complex structure and high precision requirements. The main body of the automotive checking fixture is the main framework of the inspection tool, including the base (reference plane) of the checking fixture, the surface of the vehicle body, and the installation part.
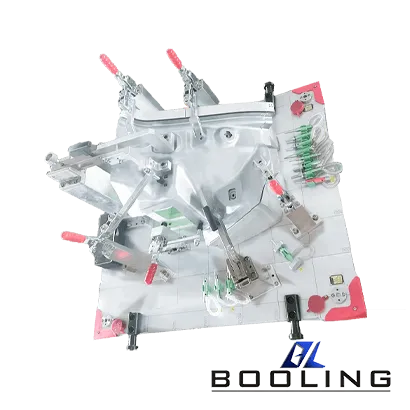
Automotive Checking Fixtures | Parts Inspection
Automotive checking fixtures are tools used for quality control and product testing on automotive production lines. Checking fixture can help ensure that the size, shape, and function of automotive parts meet design requirements, thereby improving the efficiency and quality of the entire production process.
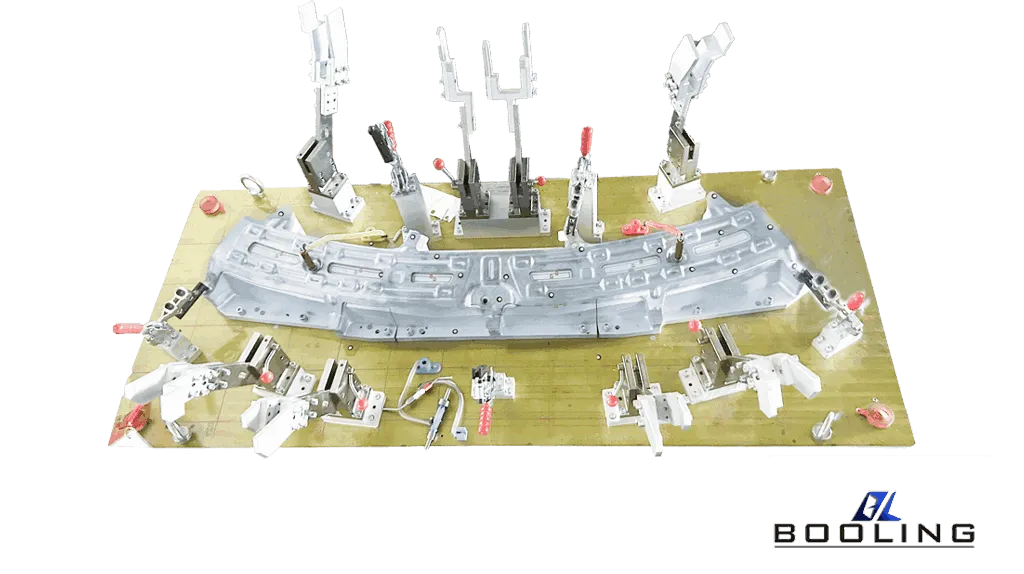
Role of Automotive Checking Fixtures
Realize online inspection of parts through fixture testing; inspect the surface and periphery of parts through visual inspection, measuring gauges, or calipers, and visually inspect the holes of different properties on parts and the connection positions between parts with the help of inspection pins or visual inspection, to ensure the rapid judgment of the quality status of parts during trial production and start-up production.
For some extremely important functional dimensions on parts, checking fixtures can also be used for numerical detection. Usually, it is not possible to directly obtain the precise coordinate values of parts based on the body coordinate system with the help of checking fixtures, but the parts are placed on the checking fixtures and measured by the three-coordinate measuring machine to obtain them. The structure of modern checking fixtures is designed to be used as a measuring bracket.
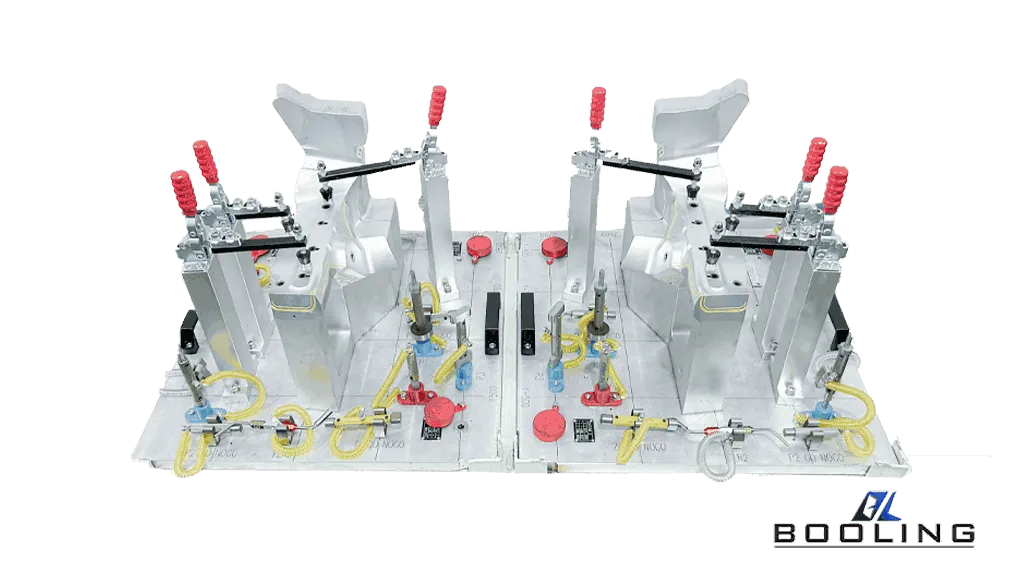
Application of Automotive Checking Fixtures
1.Engine Checking Fixtures
The engine checking fixture is a tool used to detect engine parts. It can simulate the position and posture of each part during the operation of the engine according to the engine design requirements, to detect and calibrate the size, position, assembly relationship, etc. of the parts. The characteristics of the engine checking fixture are complex structure, high precision requirements, and regular maintenance and servicing.
2.Chassis Checking Fixtures
The chassis checking fixture is a tool used to detect chassis parts. It can simulate the position and posture of each part during the operation of the chassis according to the chassis design requirements, to detect and calibrate the size, position, assembly relationship, etc. of the parts. The characteristics of the chassis checking fixture are simple structure and low precision requirements, but regular maintenance and servicing are required.
3.Classification of Checking Fixtures
According to the inspection object, it can be divided into stamping single products, parts assembly, and combined checking fixtures.
The stamping single product checking fixture and assembly checking fixture are mainly used to complete the measurement during the product processing process. It is often necessary to detect the profile surface and emphasize the continuity of the surface.
The combined checking fixture mainly detects the mutual coordination relationship of each sub-assembly and the coordination accuracy after assembly, and mainly plays the role of a measuring bracket.
The structural components of the automobile checking fixture:
1) Skeleton base part
2) Positioning device (positioning pin, positioning block)
3) Clamping device (clamp, magnet, etc.)
4) Profile or body (detection surface, non-detection surface)
5) Profile Template
6) Profile live block
7) Detection device (detection pin, feeler gauge, scoring line, dial indicator, etc.)
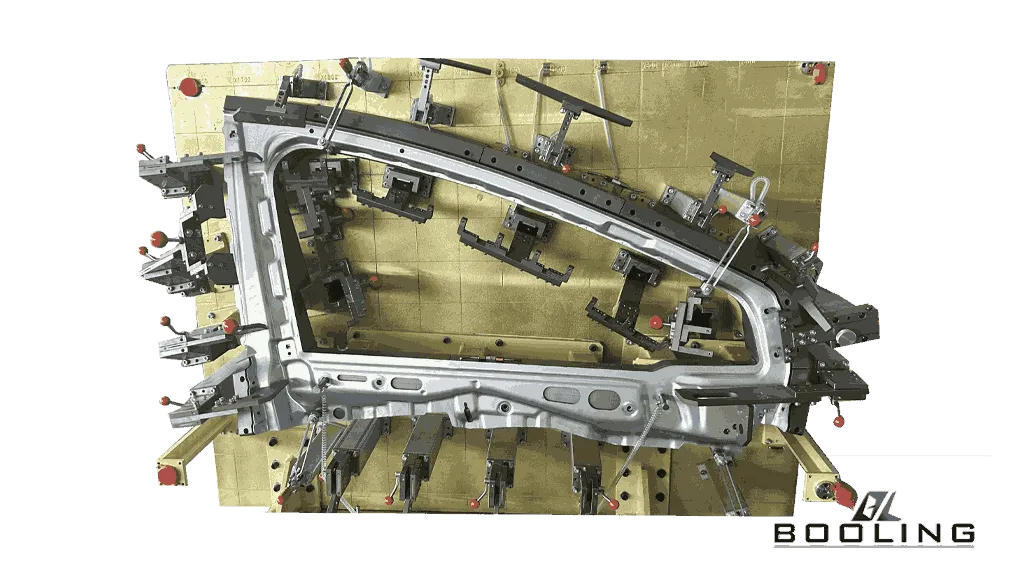
Automotive Checking Fixtures Types
- Angle Measurement Tool: a tool used to measure the angle between parts. They are usually composed of a rotating platform, an angle ruler, and a data acquisition system, which can help detect whether the installation position of automobile parts is correct.
- Dimension Measurement Tool: used to measure the length, width, height, and other dimensions of automobile parts. These tools usually include equipment such as calipers, vernier calipers, and projectors to ensure that the product meets the specifications.
- Functional Test Fixtures: used to test whether the functions of automotive parts are normal. For example, brake disc test benches can simulate braking conditions under driving conditions and determine the service life and effectiveness of brake discs.
When designing automotive checking fixtures, the following aspects need to be considered:
- Functionality: It can accurately complete the required test or measurement tasks and is easy to use and operate. They should be able to adapt to various specifications and models of parts and be able to work under different environmental conditions.
- Accuracy and Stability: To ensure the accuracy of the test results, high accuracy and stability are required. Its structure should be carefully designed to avoid error accumulation and provide reliable measurement results.
- Reliability and Durability: Due to frequent use on the production line, the checking fixture needs to withstand long-term and high-intensity work. Therefore, factors such as material selection and processing technology should be considered in the design to ensure its durability and reliability.
Automotive Checking Fixtures Design Process
- Demand Analysis: It is necessary to determine the parameters required for testing or measurement, and understand the relevant standards and specifications. Determine the type of checking fixture, accuracy requirements, etc. according to the needs.
- Structural Design: Structural design is carried out according to functional requirements and material characteristics, taking into account factors such as ease of operation, stability, and durability. At the same time, it is also necessary to select appropriate materials and carry out processing and manufacturing.
- Test Verification and Adjustment: Conduct actual test verification, and make necessary adjustments and improvements based on the results. This step is to ensure performance and reliability in actual use.
Automotive checking fixtures can provide automobile manufacturers with reliable and efficient quality control methods. They can not only ensure that the product size, shape, and function meet the requirements but also improve the work efficiency on the production line.
Related News
Applied’s expertise in modifying materials at atomic levels and on an ihdustrial scaleenables our customers to transform possibilities into reality.