Home > 3D Printing Service > Custom 3D Printing
Custom 3D printing is a technology that uses digital technology material printers for manufacturing, and is often used in the manufacture of models in the mold manufacturing industry. Booling uses advanced high-precision 3D printing equipment to provide efficient 3D printing services for industries such as automobiles, home appliances, mechanical equipment, and aviation within shot delivery.
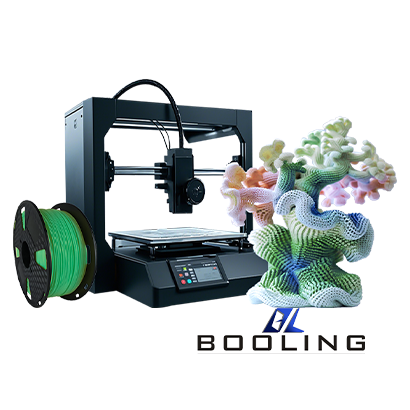
Custom 3D printing technology is a manufacturing process that produces products by adding materials layer by layer. Our engineers can provide customized services in product size and structure with flexibility.
- FDM
- SLA
SLS
Custom 3D Printing Capabilities
Custom 3D printing technology can provide faster response speed based on two-dimensional and multi-dimensional daily personalized needs.
·
US
Metric
FDM
47.2in. x 31.4 in. x 23.6 in.
1200mm x 800mm x600mm
SLA
47.2in. x 31.4 in. x 23.6 in.
1200mm x 800mm x600mm
SLS
47.2in. x 31.4 in. x 23.6 in.
1200mm x 800mm x600mm
*Custom 3D printing is generally suitable for the manufacturing of small batch or single-piece products.
Custom 3D Printing Material
Booling can provide custom 3D printing services, selecting and ordering suitable materials, such as plastic, metal, rubber, ceramic, etc., according to the product and your needs.
Material
- PLA
- ABS
- PETG
- CFRP
- Stainless Steel
- Alumina
- GFRP
The Advantages of Custom 3D Printing
Our 3D printing technology can realize the processing and production of complex shapes, which can directly turn your imagination into reality and create unique products and parts.
- Our 3D printing technology has a fast manufacturing speed, eliminating the steps of traditional mold design, mold opening, assembly, etc., shortening the manufacturing cycle
- Customized production can be provided
- Designers and customers have a higher degree of design freedom
- Provide lower costs
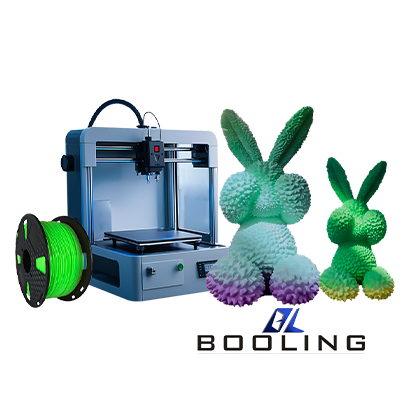
Application of Custom 3D Printing
Booling customized 3D printing technology applies to multiple ranges and fields, such as automobile, medical, construction, aerospace, etc. It has the ability of flexibility, customization, and rapid production, and has received good responses in many fields. Our designers will make unique designs according to the requirements of the application field and provide high-quality 3D-printed products.
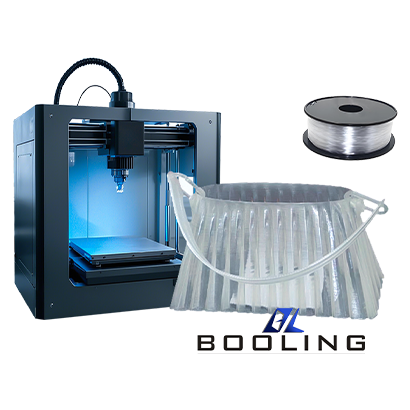
Guidelines for Custom 3D Printing
Custom 3D printing is fast and has a wide range of material options. It is suitable for manufacturing products with multiple varieties, low volume, and short molding time. Booling’s customized 3D printing technology is directly driven by digital models and has a fast response speed.
Custom 3D printing uses digital technology material printers for manufacturing and processing, and is often used for the processing of mold rapid models. Booling has directly used 3D printing for the direct manufacturing of products and some parts to improve production efficiency.
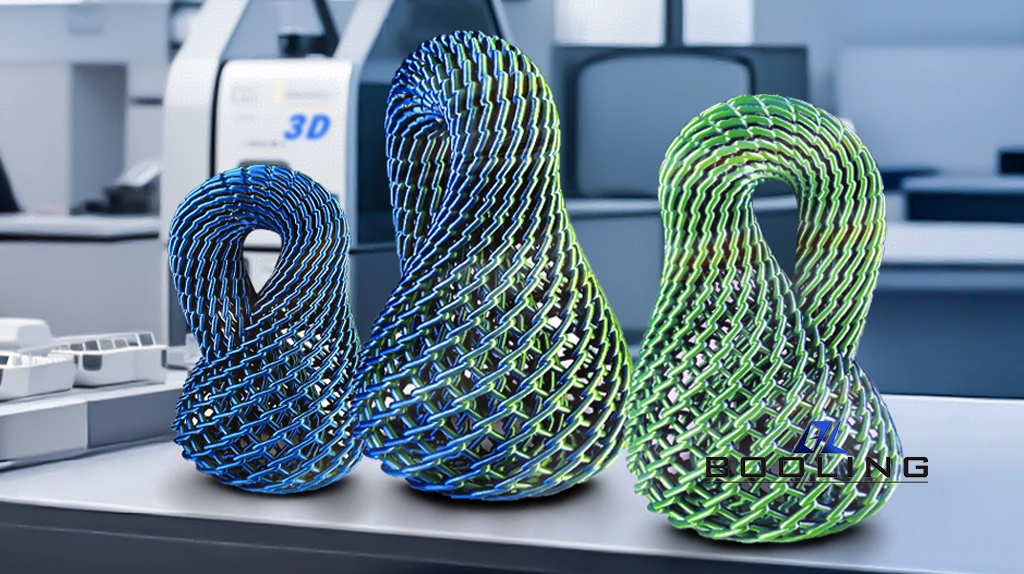
Advantages of Custom 3D Printing
Custom 3D printing technology, also known as additive manufacturing technology, has the outstanding advantages of high quality and low cost and is widely used in the fields of automobiles, aerospace, electronics, and electrical appliances.
- Our 3D printing technology has a high material utilization rate, especially for some large parts, which can reduce material waste
- The traditional processing method is to obtain the required products by cutting or grinding on the raw materials, using many machines and molds, which requires a large time cost. Our technicians can greatly reduce the processing time through 3D printing technology, directly print samples or sample molds of products, and shorten the processing time
- For the manufacture of some single pieces, low volume or complex products or samples, we will use 3D printing customization technology to achieve
- 3D printing technology has a low cost and is suitable for process evaluation and performance optimization before mold forming. It is widely used in high-precision fields such as automobiles, aerospace, construction, electronics, and electrical appliances
- Booling can use CAD technology to complete the rapid transition from model to single product
- Booling provides 3D printing remote manufacturing services, with relatively free design and high flexibility, which can meet customers’ design requirements in a short time
Custom 3D Printing Technology
There are many types of customized 3D printing technology processes. We provide a variety of printing technologies such as FDM, SLA, SLS, etc. to meet the needs of different products and users.
- FDM: This is the most common process in customized 3D printing. The material is heated to a semi-fluid state by a heating head and moves along the trajectory determined by CAD. The nozzle extrudes the material and solidifies instantly to form a thin layer with a contour shape. The 3D print head and base move vertically, and the material can be stacked layer by layer in a short time to print out a 3D product that meets the requirements. Booling provides dual nozzle processing technology with flexible support material selection
- SLA: Stereolithography is based on the photopolymerization reaction of photosensitive resin. The laser beam is used to irradiate the surface of the photosensitive resin according to the designed path, solidify each layer of resin, and cover and adhere layer by layer until the entire 3D part is manufactured. This technology has high precision and is suitable for processing models with more details and complex structures
- SLS: Selective laser sintering technology is a technology that uses a laser beam to sinter powder materials layer by layer to form solid products, with high precision and flexible material selectivity. Compared with other technologies, unsintered powder materials can be reused, reducing material waste. Booling’s SLS technology can achieve high-precision prototype processing and production, with an accuracy of about 0.1mm