Home > Injection Molding > Custom Injection Molding
Custom injection molding has been widely used by manufacturers in various industries such as healthcare, industry, and automotive, and exported to countries such as Germany, Japan, and Spain.
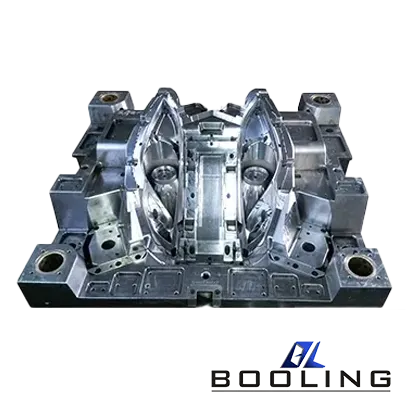
- Nozzle Temperature
- Mold Temperature
- Injection Pressure
- Injection Rate
Custom Injection Molding
The material selection for custom injection molding needs to meet product requirements while also having economic performance.
·
US
Metric
ABS
59 in. x 51.2 in. x 17.7 in.
1500mm x 1300mm x 450mm
PE
59 in. x 51.2 in. x 17.7 in.
1500mm x 1300mm x 450mm
PP
59 in. x 51.2 in. x 17.7 in.
1500mm x 1300mm x 450mm
PS
59 in. x 51.2 in. x 17.7 in.
1500mm x 1300mm x 450mm
*Custom injection molding provides a variety of material options, reducing tolerances and increasing precision.
Custom Injection Molding Material
The selection of custom injection molding materials requires many considerations, such as the physical and chemical properties of the materials.
Material
- ABS
- PE
- PP
- PS
- NYLON
- EVA
- Thermoplastic
- PMMA
- Silicone
- Rubber
- LSR
- TPU
- TPV
- TPE
The Advantage of Custom Injection Molding
Custom injection molding excels in high-volume production of precise, consistent parts from a wide range of materials at a low cost per unit.
Advantage:
- Higher Precision
- Lower Cost
- Fast Production Rate
- Wide Material Choice
- Environment Protection
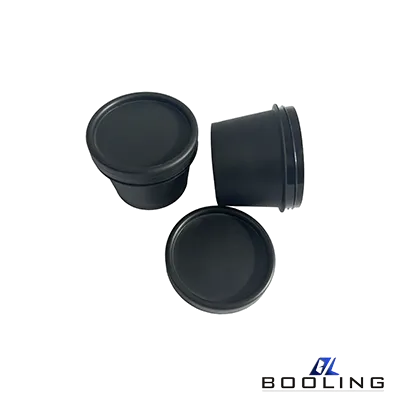
Application of Custom Injection Molding
Custom injection molding is widely used in various industries, even in industries with high precision requirements, such as the medical , automotive and aerospace industry, etc.
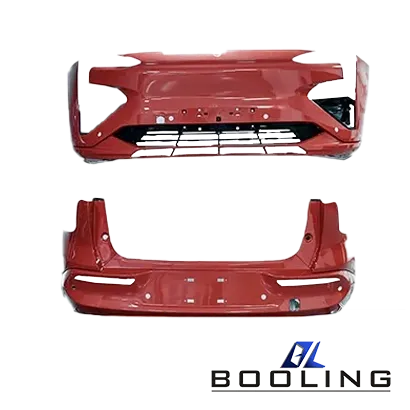
Guidelines for Custom Injection Molding
Custom injection molds are a crucial component in injection molding production.
Custom injection molding has been widely used by manufacturers in various industries such as healthcare, industry, and automotive, and exported to countries such as Germany, Japan, and Spain. The so-called customized injection molding is the process of melting selected plastic materials and injecting them into the mold cavity to produce various products. In this manufacturing process, quality control is crucial for manufacturers to ensure that the final product meets customer-customized requirements and standards.
Both custom and traditional injection molding processes require strict quality control measures to ensure consistent product quality. The first step is for the manufacturer to strictly inspect whether the raw materials used in the injection molding process meet the processing requirements, including their purity, fluidity, and other aspects.
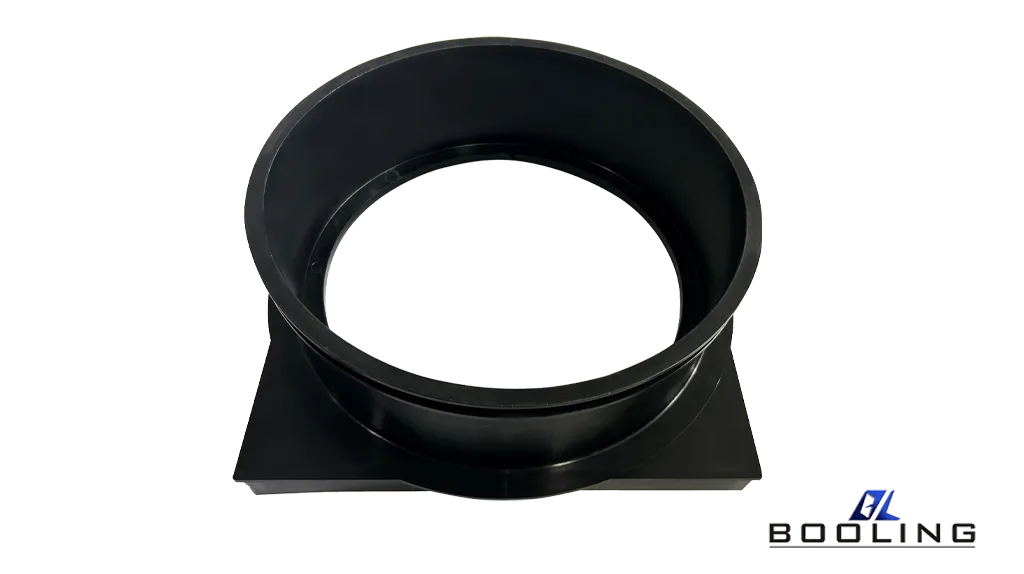
Designing the Plastic Part
The first step in custom injection molding is to design plastic parts. The customer will collaborate with the manufacturer’s engineers and designers to create a 3D model of the product to be designed based on factors such as size, shape, and function, to precisely design molds for injection molding.
In the process of custom injection molding, the selection of materials by manufacturers is crucial. The physical properties of different materials, such as strength, flexibility, and heat resistance, are different. Manufacturers and suppliers will customize raw materials according to different uses and usage environments.
When designing for custom injection molding, wall thickness is a key consideration. Thicker walls make parts stronger but also increase cooling time and material usage. Thinner walls are more cost-effective but may compromise strength. Finding the right balance is crucial.
Draft angles are important in custom injection molding designs. These slight tapers allow the part to release from the mold easily. Steeper draft angles are needed for textured surfaces compared to smooth ones. Proper draft angles prevent defects and stuck parts.
For custom injection molding, gate locations must be carefully planned. Gates are the entry points where molten plastic enters the mold cavity. Positioning gates in less visible areas helps minimize blemishes on the final part’s surface.
Undercuts and internal features require special considerations in custom injection molding designs. These areas may need movable mold components or alternative manufacturing methods to create the desired geometry. Careful planning avoids costly mold modifications later.
When designing for custom injection molding, tolerances, and shrinkage must be accounted for. As plastic cools and solidifies, it contracts slightly. Designs must accommodate this shrinkage to ensure the proper fit and function of the final part.
Rib and gusset features can reinforce custom injection molded parts without excessive material usage. These design elements increase stiffness and strength while minimizing weight and cost. Proper sizing and placement are key.
Custom injection molding allows for decorative textures and patterns on part surfaces. However, these aesthetic features require specific mold designs and may increase cycle times and costs. Balancing form and function is important.
The design of custom injection molding not only involves the shape of the parts but also needs to consider many other factors. Collaborating with experienced suppliers can not only optimize design but also achieve more efficient and high-quality manufacturing.
The Injection Molding Process
The custom injection molding process starts with clamping the mold shut. The mold is made of two halves that fit together precisely. Once clamped, the molten plastic is injected into the mold cavity through a small opening. The pressure ensures the plastic fills every corner of the cavity.
After injection, the plastic is allowed to cool and solidify inside the mold. This cooling stage is important for the part to retain its shape. The length of cooling depends on the plastic material and part thickness. Thicker parts require longer cooling times.
Once cooled, the mold opens, and the solidified part is ejected. Ejector pins push the part out of the mold cavity. The ejected part may have some excess plastic attached, which is trimmed away. This completes one cycle of the custom injection molding process.
The injection molding machine controls every stage automatically. It clamps the mold, injects the plastic, applies holding pressure during cooling, and ejects the finished part. This automation allows for high production rates of identical plastic parts.
The cost of designing and manufacturing custom injection molds in the early stages is very high. However after the mold is made, the cost of each component will be greatly reduced. Injection molding technology is an ideal choice for mass production, and the selection of plastics is also very extensive, such as polypropylene (PP), ABS, nylon, etc.
Choosing the Right Plastic Material
Polypropylene is a popular choice for custom injection molding projects. It is a lightweight, durable, and cost-effective material. Polypropylene offers excellent chemical resistance and is suitable for various applications, including food packaging, toys, and automotive components.
ABS (Acrylonitrile Butadiene Styrene) is another commonly used plastic in custom injection molding. It is known for its strength, impact resistance, and ability to maintain its shape under stress. ABS is often used in the production of electronic housings, automotive parts, and consumer goods.
Nylon, also known as polyamide, is a strong and flexible plastic material. It has excellent wear resistance and can withstand high temperatures. Nylon is commonly used in custom injection molding for mechanical parts, gears, and bearings, particularly in the automotive industry.
Polycarbonate is a transparent and durable plastic material. It offers excellent impact resistance and is often used in custom injection molding for applications that require clarity and strength, such as safety glasses, automotive headlights, and electronic components.
Manufacturer Booling has accumulated a lot of practical experience in injection molding. The leaders and operators of the company can clearly understand that selecting suitable plastic materials for custom injection molding projects poses certain challenges due to the performance differences between plastics.
In the eyes of Booling, the company needs to have a certain understanding of the uniqueness of the requirements before starting a custom injection molding project, such as the expected use, expected performance, and budget of the product. After understanding these, the company can recommend the most suitable plastic materials and guide customers throughout the entire injection molding process.
The Benefits of Custom Injection Molding
One of the main benefits of custom injection molding is the ability to quickly and efficiently produce large quantities of parts. The injection molding process can achieve a high degree of automation, requiring fewer manual steps, which greatly reduces manual errors and improves the accuracy of the parts. In custom injection molding, manufacturers can produce thousands or even millions of identical parts with consistent quality and accuracy.
Another advantage of custom injection molding is the ability to create complex part geometries and intricate designs. The molds can be designed to produce parts with various shapes, sizes, and features, including undercuts, threads, and textures. This versatility allows for the production of highly customized parts tailored to specific applications.
Custom injection molding also offers strength and durability. By selecting the appropriate plastic material and incorporating reinforcements or fillers, the molded parts can achieve exceptional strength and resistance to various environmental conditions, such as heat, chemicals, or impact.
The process is highly efficient, with cycle times ranging from a few seconds to a few minutes, depending on the part’s complexity and size. This rapid production rate contributes to the cost-effectiveness of custom injection molding, especially for high-volume orders.
Custom injection molding also offers the advantage of minimal waste generation. Any excess plastic or runner material can be easily recycled and reused in the next production cycle, reducing material waste and contributing to a more sustainable manufacturing process.
Applications of Injection Molded Plastic Parts
One of the primary applications of custom injection molding is in the consumer products industry. From toys and household items to electronics and appliances, injection molded parts offer a versatile solution for manufacturing intricate designs with precise tolerances. Custom injection molding allows for the creation of unique shapes, textures, and colors, enabling product differentiation and enhancing consumer appeal.
The automotive industry is another significant user of custom injection molded plastic parts. Automotive components such as dashboards, door handles, bumpers, and interior trims are commonly produced through injection molding. These custom parts not only provide aesthetic appeal but also offer lightweight and durable solutions, contributing to improved fuel efficiency and vehicle safety.
In the medical field, custom injection molding plays an important role in producing sterile and biocompatible components. From surgical instruments and prosthetics to drug delivery devices and diagnostic equipment, injection molded parts ensure precision, reliability, and adherence to stringent regulatory standards. Custom injection molding enables the creation of complex geometries and specialized materials for medical applications.
The construction industry also benefits from custom injection molded plastic parts. Building components such as window frames, door hardware, pipe fittings, and electrical enclosures are often injection molded. These custom parts offer excellent insulation properties, weather resistance, and long-lasting durability, making them ideal for construction projects.
Custom injection molding is also prevalent in the packaging industry, where plastic containers, bottles, caps, and closures are produced. These custom parts can be designed with specific shapes, colors, and branding elements, enhancing product recognition and shelf appeal. Injection molding ensures consistent quality and efficient mass production of packaging components.
Manufacturers can understand the different requirements of various industries and fields and can achieve an in-depth understanding of customer needs, designing and developing custom injection molded products that meet their unique specifications. The company’s professional design and operation team can utilize advanced injection molding technology and high-quality materials to provide precise and high-quality injection molding solutions.