Home > Injection Molding > EVA Injection Molding
EVA Injection Molding
EVA injection molding technology has been widely used by manufacturers in various industries, including but not limited to medical, automotive, electronic, and household products, due to its high precision and smoothness.
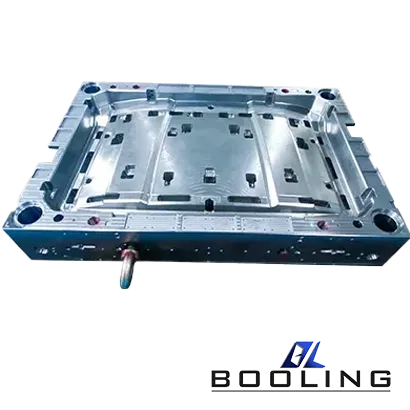
EVA Injection Molding
- Melt Index
- Acetic Acid Content
EVA Injection Molding Capabilities
EVA injection molding material is soft and elastic, with excellent injection molding ability.
·
US
Metric
EVA with Ethyl Acetate below 5%
59 in. x 51.2 in. x 17.7 in.
1500mm x 1300mm x 450mm
Ethyl Acetate in 5%~10% EVA
59 in. x 51.2 in. x 17.7 in.
1500mm x 1300mm x 450mm
Ethyl Acetate at 20%~28% EVA
59 in. x 51.2 in. x 17.7 in.
1500mm x 1300mm x 450mm
EVA with Ethyl Acetate Higher than 30%
59 in. x 51.2 in. x 17.7 in.
1500mm x 1300mm x 450mm
*EVA injection molding can also be precisely customized.
EVA Injection Molding Material
The performance of EVA injection molding materials depends on the content of ethyl acetate.
Material
- EVA
The Advantage of EVA Injection Molding
EVA injection molded products are soft and elastic, providing advantages that other materials do not have.
Advantage:
- Excellent chemical performance
- Having insulation properties
- Low temperature resistance
Ozone resistant
Antifungal
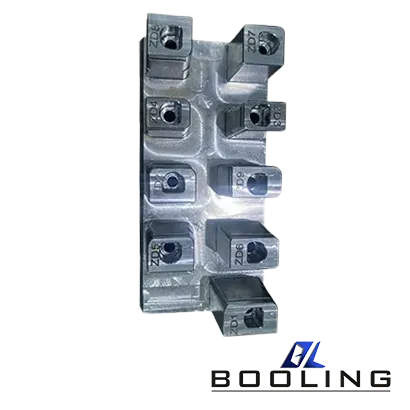
Application of EVA Injection Molding
EVA injection molding is used in the production of foamed shoe materials, films, wires and cables, toys, hot melt adhesives, and luggage due to its special performance.
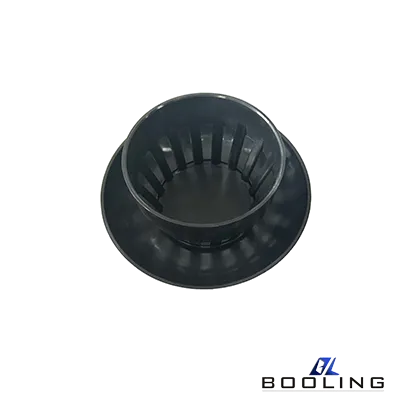
Guidelines for EVA Injection Molding
EVA injection molding is a special injection molding process.
EVA Injection Molding Guide
EVA Injection Molding
EVA injection molding technology has been widely used by manufacturers in various industries, including but not limited to medical, automotive, electronic, and household products, due to its high precision and smoothness. EVA injection molding is a professional thermoplastic polymer molding process, which is very suitable for products that require high dimensional accuracy and surface smoothness.
Eva injection molding is mainly aimed at processing thermoplastic polymers, usually including some polymer resins, which are injected into the mold cavity under certain pressure and temperature conditions. Melted plastic can fill the complex details of the mold, and finally cool and solidify to form a plastic part.
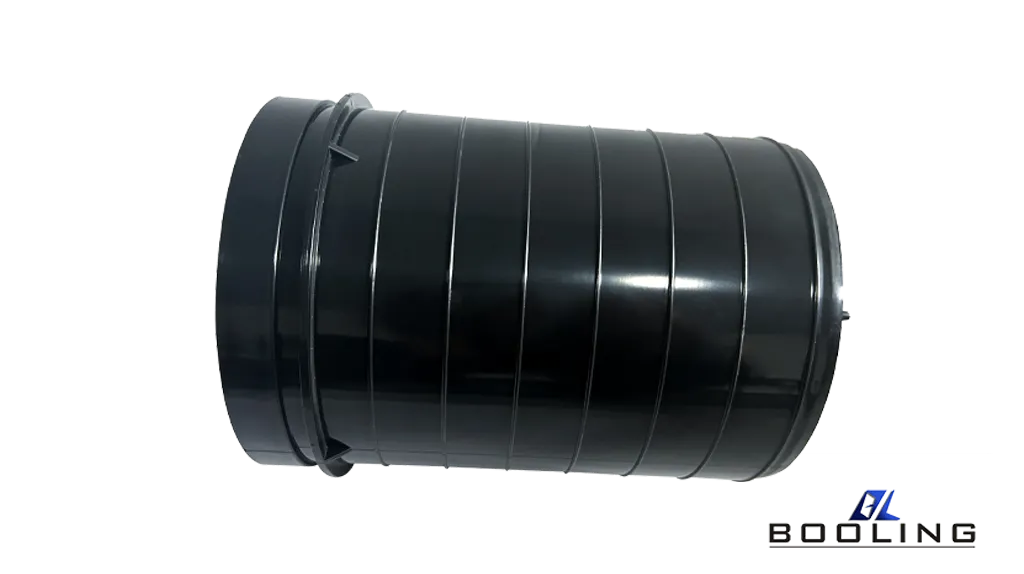
What is EVA?
Ethylene-vinyl acetate (EVA) polymers have outstanding and excellent properties and have been widely used in various industries. The multifunctional properties of this material are mainly derived from the monomers ethylene and vinyl acetate, and this uniqueness makes it an attractive choice for wide applications.
1.Flexibility and Impact Resistance
One of the standout features of EVA is its remarkable flexibility. The molecular structure of the copolymer allows it to bend and flex without compromising its integrity. This property makes EVA an ideal material for applications that require resistance to impact or deformation. Products such as shoe soles, gaskets, and protective gear benefit from the material’s ability to absorb shocks and withstand repeated stress without cracking or breaking.
2.Durability and Environmental Resistance
EVA exhibits exceptional durability, making it suitable for applications that demand long-lasting performance. The material is highly resistant to UV radiation, ozone, and weathering, ensuring that products made from EVA maintain their structural integrity and aesthetic appeal even when exposed to harsh environmental conditions. This characteristic makes EVA an excellent choice for outdoor applications, such as playground surfaces, roofing membranes, and automotive components.
3.Chemical Resistance
Another notable property of EVA is its remarkable resistance to a wide range of chemicals. This characteristic makes the material suitable for applications involving harsh chemical environments, such as in the automotive, construction, and industrial sectors. EVA’s ability to withstand exposure to acids, bases, and solvents ensures that products made from this material maintain their structural integrity and performance over an extended period.
4.Processability and Versatility
EVA’s processability is a significant advantage that contributes to its widespread adoption across various industries. The copolymer can be easily processed using various techniques, including injection molding, extrusion, and blow molding. This versatility allows manufacturers to produce a diverse range of products, from intricate components to large-scale structures, with relative ease and efficiency.
The EVA Injection Molding Process
EVA injection molding is a widely used plastic manufacturing technology, which mainly involves melting the polymer and injecting it into the mold cavity under certain pressure and temperature. After cooling and curing, the molded part will be ejected from the mold. The EVA injection molding process follows this principle, but its uniqueness lies in its need to adapt to the performance of EVA materials, so manufacturers also need to consider other factors.
Step 1: Material Preparation
EVA pellets or granules are carefully dried to remove any moisture content, as residual moisture can adversely affect the molding process and the quality of the final product.
Step 2: Melting and Plasticization
The dried EVA material is fed into the heated barrel of the injection molding machine, where it is melted and plasticized. The temperature and shear forces applied during this stage ensure that the material achieves the desired viscosity for injection.
Step 3: Mold Preparation
The mold, typically made of high-strength steel or aluminum, is prepared by applying a release agent to facilitate the easy removal of the molded part. The mold cavity is designed to match the desired shape and dimensions of the final product.
Step 4: Injection and Packing
The molten EVA is injected into the mold cavity under high pressure, filling every intricate detail of the mold. During this stage, additional material may be injected to compensate for the shrinkage that occurs as the polymer cools and solidifies, ensuring dimensional accuracy.
Step 5: Cooling and Ejection
Once the mold cavity is filled, the molten EVA is allowed to cool and solidify. Cooling channels within the mold facilitate efficient heat transfer, ensuring consistent and rapid cooling. After the part has solidified, the mold opens, and the ejector pins push the molded part out of the cavity.
Applications of EVA Injection Molded Products
1. Automotive Industry
The automotive industry has embraced EVA injection molded parts for their exceptional durability and resistance to UV radiation. These properties make EVA an ideal choice for interior components such as door panels, instrument panels, and trim components. The ability of EVA to withstand harsh environmental conditions and maintain its structural integrity ensures a long-lasting and visually appealing interior for vehicles.
2.Footwear Industry
EVA has become a staple in the footwear industry, revolutionizing the production of shoe soles, insoles, and midsoles. Its unique properties, including cushioning, shock absorption, and flexibility, contribute to enhanced comfort and support for the wearer. EVA injection molded components in footwear not only provide a comfortable experience but also offer durability and resilience, ensuring long-lasting performance.
3.Packaging Industry
The chemical resistance and flexibility of EVA make it an excellent choice for producing packaging materials such as bottle closures, gaskets, and seals. Injection-molded EVA components in packaging applications offer a high degree of precision and consistency, ensuring a secure and reliable seal for various products. This not only protects the contents but also extends their shelf life and maintains their integrity during transportation and storage.
4.Construction Industry
The construction industry has recognized the potential of EVA injection molded products for applications such as waterproofing membranes, flooring underlayments, and insulation materials. EVA’s resistance to moisture and its ability to withstand harsh environmental conditions make it an ideal choice for these applications. Waterproofing membranes made from EVA provide effective protection against water ingress, while flooring underlayments offer sound insulation and cushioning properties. Additionally, EVA insulation materials contribute to energy efficiency and thermal comfort in buildings.
5.Medical and Pharmaceutical Industries
The biocompatibility and chemical resistance of EVA have made it a preferred material for producing medical devices, pharmaceutical packaging, and disposable medical components. Injection-molded EVA products in these industries ensure safety, reliability, and precision. Medical devices such as tubing, connectors, and protective coverings benefit from EVA’s durability and resistance to chemicals and bodily fluids. Pharmaceutical packaging made from EVA provides a secure and sterile environment for medications, protecting them from external contaminants and ensuring their efficacy.
6.Sports and Recreational Equipment
The lightweight and impact-resistant nature of EVA has made it a popular choice for sports and recreational equipment. Injection-molded EVA components are used in protective gear such as helmets, knee pads, and elbow pads, providing superior cushioning and impact absorption. Additionally, EVA is utilized in the production of buoyant water sports equipment, ensuring safety and stability in aquatic environments.
7.Toys and Consumer Products
The versatility of EVA injection molding extends to the toy and consumer product industries, where it enables the creation of intricate and visually appealing designs. Injection-molded EVA toys offer durability, flexibility, and safety for children, while consumer products such as household items, gardening tools, and outdoor equipment benefit from EVA’s resistance to weather and wear.
The application of EVA injection molded products is indeed diverse and can be well applied to industries and departments that require high quality and performance. Modern technology is constantly developing, and the strong innovative application potential of EVA polymers is enormous, which can greatly increase the possibility of product and design innovation.
Quality Control and Optimization in EVA Injection Molding
Injection molding technology greatly tests the manufacturing accuracy and product consistency of manufacturers, so, during the manufacturing process, manufacturers must strictly control the quality. Especially for products made from ethylene vinyl acetate (EVA), this material has a wide range of uses. By carefully monitoring and optimizing each production stage, manufacturers can ensure that EVA injection molded products meet or even exceed quality and performance requirements.
1.Meticulous Material Evaluation
The journey towards excellence begins with a rigorous assessment of the raw materials. Incoming EVA materials undergo a series of stringent tests to verify their conformity with established specifications. These tests encompass a wide range of parameters, including chemical composition, physical properties, and thermal characteristics. By ensuring the consistent quality of the raw materials, manufacturers can mitigate the risk of defects and variations in the final product, thereby enhancing overall reliability and performance.
2.Process Monitoring
Throughout the EVA injection molding process, a multitude of critical parameters must be closely monitored and adjusted to maintain optimal processing conditions. These parameters include but are not limited to, temperature profiles, pressure levels, and cycle times. Highly trained technicians and advanced monitoring systems work in tandem to continuously track and fine-tune these variables, ensuring that the process remains within the prescribed operating parameters.
By maintaining precise control over these parameters, manufacturers can minimize the occurrence of defects, such as warping, shrinkage, or incomplete filling, which can compromise the integrity and functionality of the final product. This vigilant approach not only enhances product quality but also contributes to increased efficiency and reduced waste, ultimately leading to cost savings and improved sustainability.
3.Dimensional Inspection
Once EVA injection molding process is complete, the finished EVA products undergo a comprehensive dimensional inspection. This meticulous examination ensures that the products conform to the specified dimensions, tolerances, and surface finish requirements. Advanced measurement techniques, such as coordinate measuring machines (CMMs) and optical inspection systems, are employed to detect even the slightest deviations from the desired specifications.
By identifying and addressing any dimensional discrepancies early in the process, manufacturers can take corrective actions, minimizing the risk of non-conforming products reaching the market. This proactive approach not only safeguards the reputation of the manufacturer but also ensures customer satisfaction and confidence in the quality of the products.
Manufacturers can utilize advanced analytical tools and methods such as Experimental Design (DOE) and Statistical Process Control (SPC) to quickly identify and solve potential bottlenecks, truly simplifying operational processes and making improvements. These measures not only contribute to improving the product quality of EVA injection molding, but also have important driving forces for cultivating innovation within the organization.