Home > Blow Molding > HDPE Blow Molding
HDPE blow molding uses the appropriate air pressure of the blow molding machine’s blowing system to inflate the parison closed in the mold, and molds it close to the inner wall of the mold cavity to obtain HDPE products with high dimensional accuracy and uniform wall thickness, such as IP air ducts, oil drums, roadblocks, pallets, etc. Booling has rich experience in blow molding mold manufacturing solutions, using advanced EDM and CNC machine tools to provide users with high-precision HDPE blow molding mold processing and production.
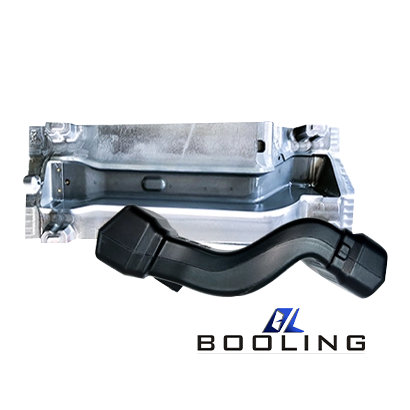
HDPE blow molding undergoes processes such as parison extrusion, blow molding, cooling, and curing to obtain hollow products with high dimensional accuracy and uniform bottle wall thickness.
- Extrusion: HDPE resin is melted and extruded into a hollow tube called a parison.
- Molding: The molten parison is clamped into a mold cavity and inflated with compressed air, taking the shape of the mold.
- Cooling: The inflated parison is cooled and solidified inside the mold to form the final product.
HDPE Blow Molding Capabilities
Booling combines HDPE materials with superior physical and chemical properties with 3D blow molding technology to produce products with special properties and cost-effectiveness.
·
US
Metric
HDPE
82.7 in. x 51.2 in. x 19.7 in.
2100mm x 1300mm x500mm
*HDPE is the most commonly used plastic for blow molding due to its durability, chemical resistance, and cost-effectiveness.
HDPE Blow Molding Material
There are several types of plastics commonly used in the blow molding process, each with its own unique properties and applications.
Material
- HDPE
The Advantage of HDPE Blow Molding
HDPE material is an ideal material for blow molding due to its durability, chemical resistance, and cost-effectiveness.
- It has excellent chemical resistance and can be used to mold chemical containers
- HDPE blow molding products have durability and impact strength
- It has high dimensional accuracy and surface quality and can be molded into products with high consistency
- HDPE material has low hygroscopicity and does not require drying before processing, which simplifies the production process
- HDPE blow molding products can be used in an environment of -40~50℃ and have good weather resistance
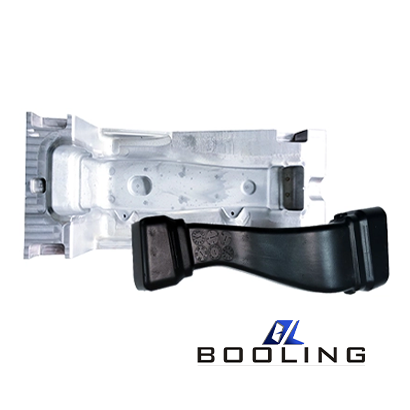
Application of HDPE Blow Molding
Booling provides HDPE blow molding in various fields, mainly including some bottles and containers, automobile fuel tanks, children’s products, industrial containers, various pipes, safety helmets, etc.
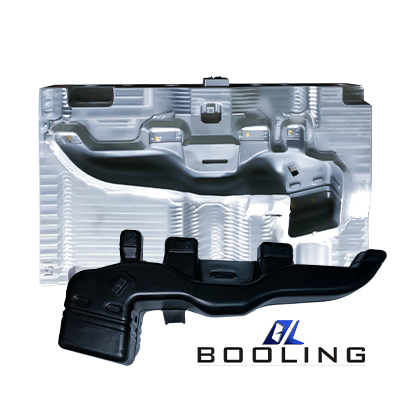
Guidelines for HDPE Blow Molding
HDPE blow molding technology has high efficiency and product quality advantages. Booling provides customized blow molding molds to meet the flexible processing needs of users and manufacturers in various industries.
The design and manufacture of HDPE blow molding molds determine the production efficiency, quality, and cost control of the product, and are the key process to realize the transformation of HDPE materials into high-quality hollow seamless containers.
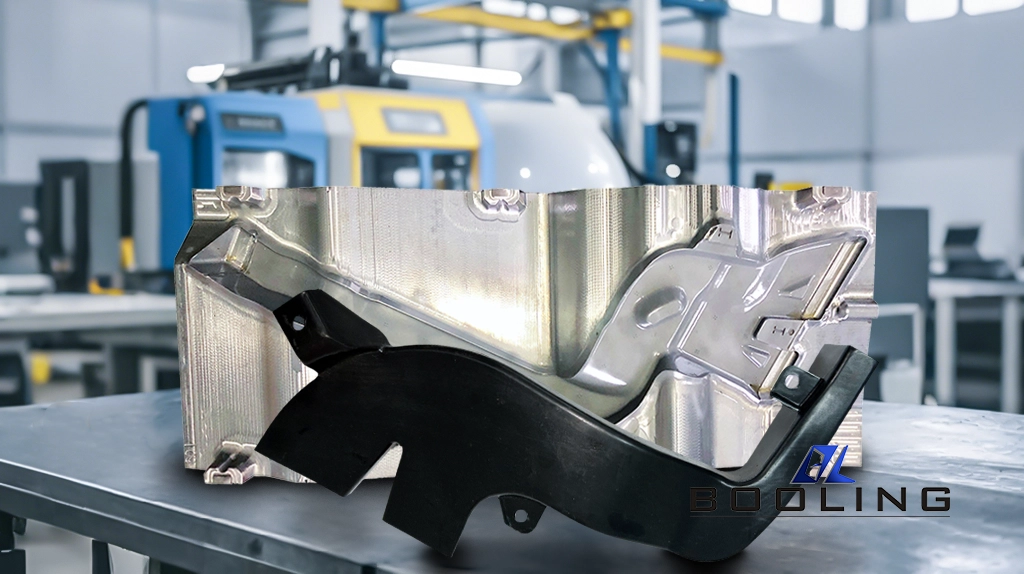
Characteristics of HDPE Blow Molding Materials
HDPE is an opaque white waxy material and a thermoplastic resin with a large usage. It is widely used in blow molding of food, chemicals, liquid, and other packaging. It can withstand large impact forces without breaking or deforming.
HDPE and high molecular polyethylene are suitable for the manufacture of various large oil tanks and oil drums. They are resistant to acids, alkalis, and organic solvents, and have excellent electrical insulation and good weather resistance. Booling uses its excellent surface hardness, tensile strength, and rigidity for processing, and combines the mold to obtain blow molding products that meet high requirements.
It has a low friction coefficient, and can effectively reduce the friction generated by the equipment during operation when blow molding. Booling uses this characteristic of HDPE material to process pallets in the logistics industry, which is wear-resistant and extends the service life of the pallets.
HDPE Blow Molding Process
HDPE blow molding is a hollow container manufacturing process with a complex molding process. Booling has a strict blow molding quality control program.
- Raw material processing: Select HDPE particles that meet the standards, and screen out impurities to improve the purity of raw materials
- Plasticization: Put the HDPE particles into the extruder for heating, and use the shearing effect of the screw to gradually melt into a uniform melt
- Parison manufacturing: The melt is extruded from the die to form a tubular parison. At this time, Booling will pre-blow into the parison to avoid defects such as uneven wall thickness and excessive burrs in the final container
- Blowing: After the parison reaches a certain length, the mold is closed, compressed air is introduced, and the blown parison is close to the inner wall of the mold
- Cooling and shaping: Booling uses water cooling or air cooling to ensure that the product can be cooled quickly and speed up the manufacturing cycle
- Demolding and post-processing: After the HDPE product is completely cooled, the mold is opened, and the operator takes out the molded HDPE product and trims the excess flash to ensure that the product has a smooth surface
- Quality inspection: Check the appearance and dimensional accuracy of the product. We will provide production videos with more than two complete cycles