Home > Injection Molding > HDPE Injection Molding
HDPE Injection Molding
Manufacturers widely apply HDPE injection molding technology to the plastic molding industry, such as healthcare, industry, electronics, and construction, and export it to many countries such as Germany and Spain.
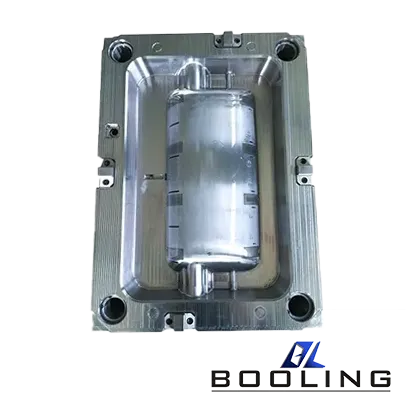
HDPE Injection Molding
- Phthalocyanine green plasticizer
- DOP
- DBP
- ATBC
HDPE Injection Molding Capabilities
The high crystallinity of HDPE determines its high density and high molding rate, making it an important injection molding material.
·
US
Metric
HDPE
59 in. x 51.2 in. x 17.7 in.
1500mm x 1300mm x 450mm
*The products produced by HDPE injection molding can provide strict tolerances and dimensional accuracy, making them very suitable for the customization and production of precision parts.
HDPE Injection Molding Material
HDPE is a type of PE material, and there are many common PE injection molding materials with different physical and chemical properties.
Material
- HDPE
The Advantage of HDPE Injection Molding
HDPE, as a commonly used thermoplastic, has many special advantages.
Advantage:
- Good chemical stability
- Recyclable
- Good wear resistance
- Good heat resistance
- Widely applicable
- Good electrical insulation performance
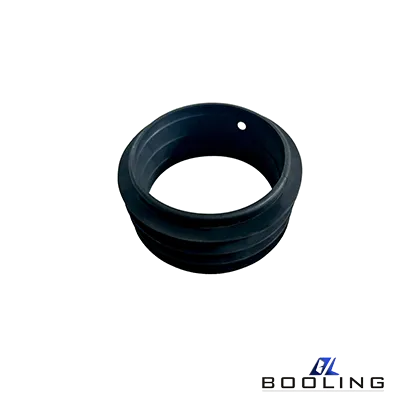
Application of HDPE Injection Molding
Due to the excellent performance of HDPE material, its injection molded products are also widely used, mainly including food packaging containers, daily necessities, pipelines, and wires and cables.
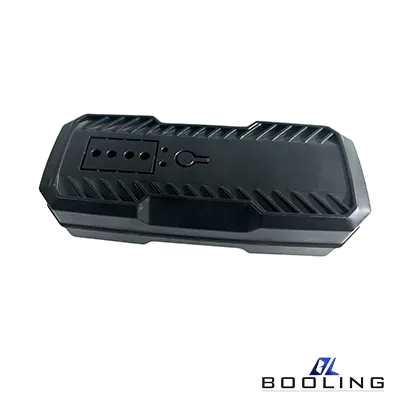
Guidelines for HDPE Injection Molding
HDPE material holds a very high position in injection molding.
HDPE Injection Molding Guide
HDPE Injection Molding
Manufacturers widely apply HDPE injection molding technology to the plastic molding industry, such as healthcare, industry, electronics, and construction, and export it to many countries such as Germany and Spain. The main principle is to inject melted thermoplastic particles or powders into the mold cavity under high pressure and solidify them into shape. HDPE has gradually become one of the most common and commonly used materials in injection molding processes. The advantages of HDPE injection molding make it a popular choice for various applications in various industries.
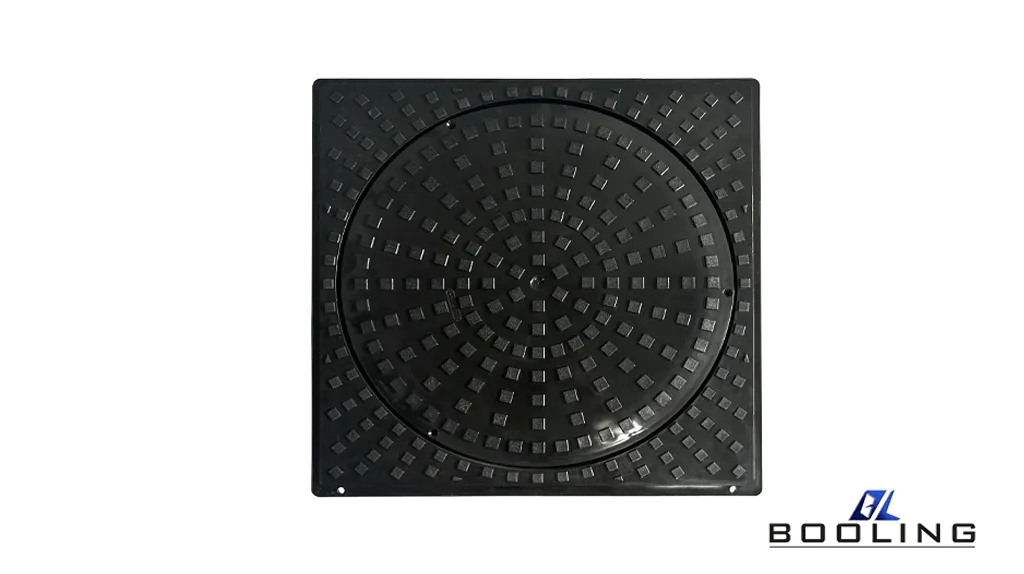
What is HDPE?
In the realm of thermoplastics, High-Density Polyethylene (HDPE) stands out as a versatile and highly sought-after material. Its unique properties and exceptional performance in injection molding processes have made it an indispensable choice across various industries. The significant characteristics of HDPE and its seamless integration analysis with injection molding technology are constantly being comprehensively developed.
HDPE is a linear polymer with a high degree of crystallinity, which contributes to its exceptional strength, rigidity, and resistance to chemicals and moisture. This thermoplastic material is widely used in the production of various products, including containers, bottles, toys, and automotive components. Manufacturers can utilize HDPE injection molding to produce various products with complex shapes and designs, meeting different product requirements.
The Injection Molding Process with HDPE
The main principle of injection molding is to melt thermoplastic materials and inject them into the mold cavity under high pressure. The high degree of automation makes it a preferred material choice for many manufacturers in plastic molding. Among various thermoplastic materials, high-density polyethylene (HDPE) has become a popular choice in the injection molding industry due to its excellent advantages and multifunctional properties.
HDPE is a linear polymer renowned for its strength, durability, and resistance to chemicals and moisture. Its high tensile strength and rigidity make it an ideal candidate for injection molding applications that require structural integrity and dimensional stability. HDPE’s low coefficient of friction and excellent impact resistance further contribute to its suitability for injection molding processes.
The injection molding process with HDPE typically involves several stages. First, HDPE pellets or granules are fed into the hopper of the injection molding machine. These pellets are then conveyed into the heated barrel, where they are melted and homogenized by the rotating screw.
Once the HDPE material reaches the desired temperature and viscosity, the molten plastic is injected into the mold cavity under high pressure. The mold cavity is carefully designed to impart the desired shape and features to the final product. HDPE’s excellent flow properties ensure that the molten material fills the intricate details of the mold cavity uniformly.
After the molten HDPE has filled the mold cavity, the cooling phase begins. During this stage, the mold is cooled, typically by circulating water or other coolants through channels within the mold. As the HDPE cools and solidifies, it takes on the shape of the mold cavity.
Once the HDPE part has solidified sufficiently, the mold opens, and the ejection system pushes the finished product out of the mold cavity. HDPE’s low shrinkage rate and excellent dimensional stability ensure that the molded parts maintain their intended shape and size after ejection.
Depending on the specific application, HDPE injection-molded parts may undergo various post-processing operations, such as trimming, drilling, or surface finishing. HDPE is compatible with various secondary processes, including printing, painting, and welding, greatly enhancing the versatility and flexibility of this material.
Benefits of HDPE Injection Molding
In the field of injection molding, high-density polyethylene (HDPE) is a widely used universal thermoplastic material. HDPE injection molding has many advantages, making it a preferred choice for materials in different industries.
- Durability and Strength
One of the most significant benefits of HDPE injection molding is the exceptional durability and strength of the resulting products. HDPE is known for its high tensile strength, impact resistance, and resistance to chemicals and moisture. These properties make HDPE injection-molded products ideal for applications that require long-lasting performance and resilience against harsh environments or heavy use.
- Cost-Effectiveness
HDPE injection molding is a cost-effective manufacturing process, particularly for high-volume production runs. The raw material, HDPE, is relatively inexpensive compared to other engineering plastics, and the injection molding process itself is efficient and streamlined. This cost-effectiveness translates into lower production costs, making HDPE injection-molded products accessible and economically viable for a wide range of applications.
- Design Flexibility
Injection molding with HDPE allows for a high degree of design flexibility. HDPE can be molded into intricate shapes and complex geometries, enabling the creation of products with unique and customized designs. This flexibility opens up opportunities for innovation and product differentiation, catering to specific market demands and consumer preferences.
- Lightweight and Portability
HDPE injection-molded products are lightweight yet sturdy, making them ideal for applications where weight is a critical factor. This characteristic is particularly advantageous in industries such as automotive, aerospace, and consumer goods, where reducing weight can lead to improved fuel efficiency, reduced transportation costs, and enhanced portability.
- Recyclability and Environmental Friendliness
HDPE is a highly recyclable material, contributing to a more sustainable and environmentally friendly manufacturing process. HDPE injection-molded products can be easily recycled and repurposed, reducing waste and minimizing the environmental impact associated with their production and disposal.
- Efficient Production Cycle
The injection molding process with HDPE is highly efficient, allowing for rapid production cycles and high output rates. This efficiency translates into shorter lead times, enabling manufacturers to respond quickly to market demands and meet tight delivery schedules.
- Consistent Quality
HDPE injection molding ensures consistent product quality and dimensional accuracy. The molding process is highly controlled, resulting in uniform and repeatable product characteristics. This consistency is essential for applications that require strict tolerances and reliable performance, such as in the automotive, medical, and consumer goods industries.
Applications of HDPE Injection Molded Products
High-density polyethylene (HDPE) is a general-purpose thermoplastic widely used by manufacturers in injection molding processes. High-density polyethylene injection molded products have been applied in various industries due to their high quality and precision.
- Packaging Industry
HDPE injection molding plays a pivotal role in the packaging industry. HDPE’s chemical resistance, durability, and lightweight nature make it an ideal choice for manufacturing containers, bottles, and closures. Injection-molded HDPE bottles are commonly used for packaging household chemicals, detergents, and personal care products. Additionally, HDPE injection molded containers are widely employed in the food and beverage industry for storing and transporting liquids, powders, and granular materials.
- Consumer Goods
HDPE injection molded products have a significant presence in the consumer goods market. From household items like storage containers, buckets, and crates to children’s toys and outdoor furniture, HDPE injection molding offers a cost-effective and durable solution. The material’s resistance to impact and weathering ensures that these products can withstand daily use and exposure to various environmental conditions.
- Automotive Industry
The automotive industry relies heavily on HDPE injection molded components for their lightweight and impact-resistant properties. HDPE injection molded parts are commonly used in interior trim components, air ducts, battery cases, and fuel tanks. These components contribute to weight reduction, improving fuel efficiency, and reducing emissions. Additionally, HDPE’s chemical resistance makes it suitable for manufacturing automotive fluid reservoirs and coolant tanks.
- Construction and Infrastructure
HDPE injection molding finds applications in the construction and infrastructure sectors. HDPE injection molded pipes and fittings are widely used for water distribution systems, sewage systems, and underground cable protection due to their durability, chemical resistance, and ease of installation. Furthermore, HDPE injection molded products are employed in the manufacturing of construction site equipment, such as traffic cones, safety barriers, and road markers.
- Agriculture and Horticulture
The agricultural and horticultural industries benefit from HDPE injection molded products. HDPE injection molded containers, trays, and pots are commonly used for seedling propagation, plant transportation, and nursery operations. These products are lightweight, durable, and resistant to moisture and chemicals, making them ideal for greenhouse and outdoor applications.
- Healthcare and Medical Devices
HDPE injection molding plays a crucial role in the healthcare and medical device industries. HDPE injection molded products, such as medical containers, vials, and caps, are widely used for storing and transporting pharmaceuticals, biological samples, and medical supplies. The material’s chemical resistance and ease of sterilization make it suitable for various medical applications.
The widespread use and uniqueness of high-density polyethylene (HDPE) injection molded products have been proven by most manufacturers. Its performance combination is unique, including its long lifespan, excellent corrosion resistance, and lightweight production, making it the preferred choice for manufacturers seeking reliable and high-performance solutions. The continuous development of injection molding technology may lead to the further expansion of the application of HDPE injection molding products, providing more innovative solutions to meet the constantly changing needs of various industries.
Maintaining HDPE Injection Molds: A Comprehensive Guide
In the field of plastic manufacturing, high-density polyethylene (HDPE) injection molding plays a crucial role in the production of various products, whether for daily necessities or industrial components. However, ensuring the lifespan and optimal performance of HDPE injection molds is only one key aspect that manufacturers need to carefully monitor and adhere to other best practices.
This comprehensive guide will delve into the complex maintenance and repair of HDPE injection molds, providing valuable insights and practical strategies to maximize the service life of the molds and improve production efficiency. By improving and researching these technologies, manufacturers can minimize downtime and downtime, lower operating costs, and continuously provide customers with higher-quality products.
- Preventive Maintenance Strategies
The key to maintaining HDPE injection molds for suppliers is to implement a comprehensive preventive maintenance plan. Before some potential problems become serious, they should be resolved promptly, so that manufacturers can maximize the service life of molds and reduce unplanned downtime. Some important preventive maintenance strategies mainly include:
- Regular Inspections: Conduct thorough visual inspections of the molds at regular intervals to identify any signs of wear, cracks, or damage. Early detection of these issues can prevent costly repairs or replacements down the line.
- Cleaning and Decontamination: HDPE injection molds are susceptible to contamination from residual plastic, moisture, and other impurities. Implementing a rigorous cleaning and decontamination protocol is essential to maintain the mold’s surface quality and prevent defects in the molded parts.
- Lubrication and Cooling Systems: Proper lubrication of moving parts and efficient cooling systems are vital for smooth operation and prolonged mold life. Regular maintenance and monitoring of these systems can prevent premature wear and ensure consistent performance.
- Mold Storage: When not in use, HDPE injection molds should be stored in a controlled environment to prevent corrosion, moisture buildup, and other environmental factors that can compromise their integrity.
- Corrective Maintenance Techniques
Wear beyond preventive measures is a problem with the usage time of HDPE injection molds. The molds will experience continuous friction over time. In this inevitable situation, manufacturers must adopt corrective maintenance techniques promptly to restore the molds to their optimal state. Some common corrective maintenance practices mainly include:
- Surface Refinishing: Techniques like polishing, grinding, and electropolishing can be employed to restore the surface finish of the mold cavities, ensuring consistent part quality and reducing the risk of defects.
- Mold Repair and Welding: In cases of cracks, damage, or excessive wear, mold repair and welding techniques can be utilized to extend the mold’s lifespan and restore its functionality.
- Mold Modification: As product designs evolve or new requirements arise, mold modifications may be necessary. Skilled technicians can modify existing molds to accommodate design changes, reducing the need for costly mold replacements.
- Mold Replacement: In some cases, when the mold has reached the end of its serviceable life or cannot be repaired cost-effectively, mold replacement becomes the most viable option. Investing in new, high-quality molds can ensure consistent production and product quality.
- Training and Skill Development
Manufacturer Booling has a skilled HDPE injection mold maintenance team, as a comprehensive training program and promoting the skill development of mold technicians and operators are crucial.
- Technical Training: Provide in-depth training on the principles of HDPE injection molding, mold design, and maintenance techniques to ensure a thorough understanding of the process and best practices.
- Hands-on Experience: Encourage hands-on experience and mentorship programs, allowing technicians to gain practical knowledge and develop their skills under the guidance of experienced professionals.
- Continuous Learning: Stay updated with the latest advancements in HDPE injection molding technology, materials, and maintenance techniques by attending industry seminars, workshops, and conferences.
- Documentation and Knowledge Sharing: Maintain comprehensive documentation of maintenance procedures, troubleshooting guides, and best practices, ensuring that knowledge is effectively shared and preserved within the organization.
By implementing these maintenance strategies, and corrective techniques, and training employees to continue learning, manufacturers can extend the service life of HDPE injection molds, enhance product performance and productivity, reduce operating costs, and continuously provide high-quality products to customers.