Home Appliance Molds
BOOLING home appliance molds mainly use injection molding and blow molding processes to customize common home appliance molds in life, such as refrigerators, televisions, microwave ovens, and other plastic accessories.
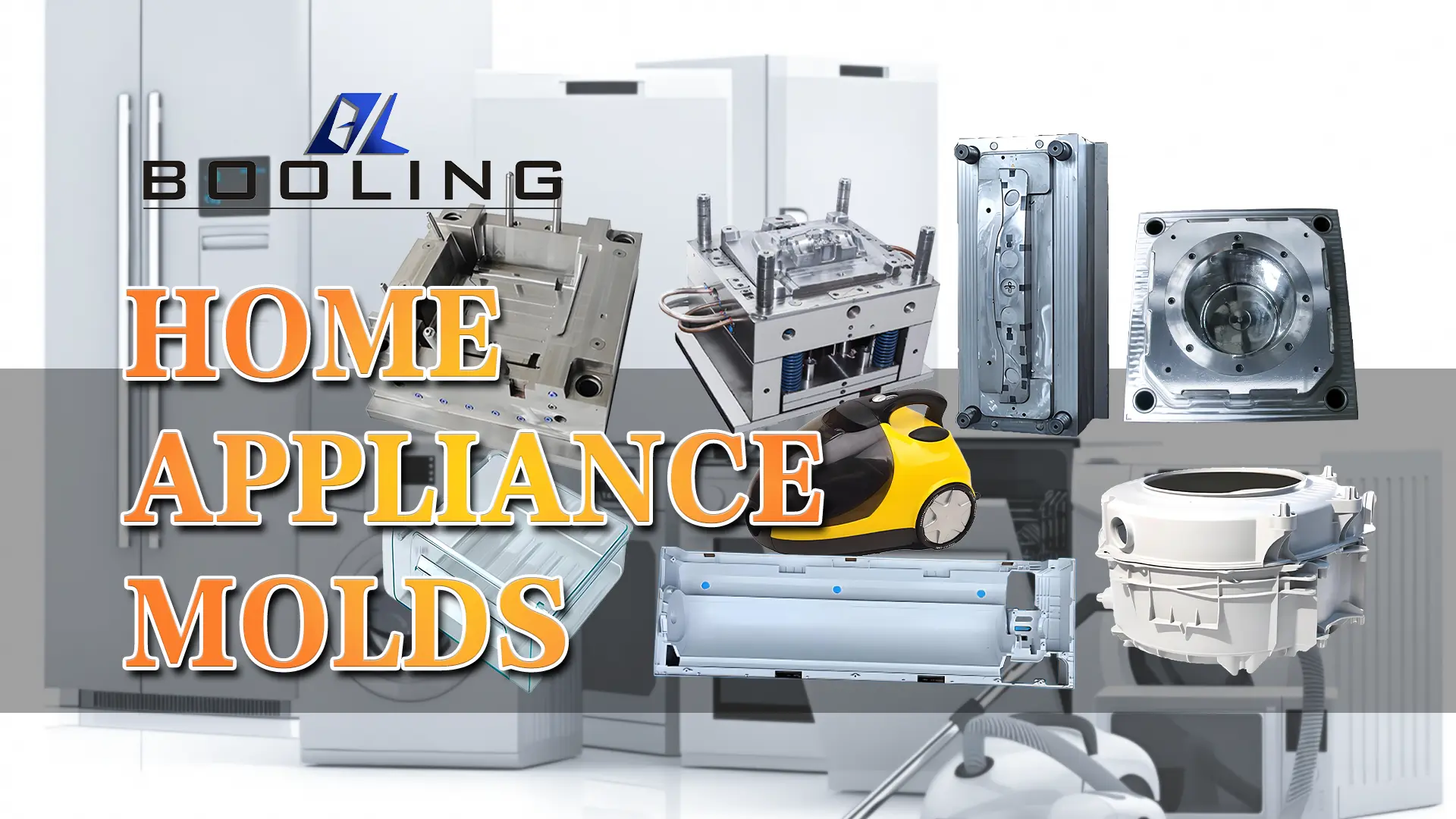
About Home Appliance Molds
BOOLING home appliance molds are mainly used to produce plastic shells and internal plastic parts of home appliance products, including the manufacture of molds for refrigerators, televisions, washing machines, air conditioners, etc. Based on the corresponding product design drawings provided by users, our company’s engineers will analyze the feasibility of product molding and provide you with professional product design optimization suggestions.
BOOLING air conditioner molds are assisted by CAD and other software to meet the appearance of various air conditioners, such as household, commercial, central air conditioning systems, and vehicle-mounted.
BOOLING refrigerator molds are made of food-grade materials that are resistant to high and low temperatures to ensure hygiene standards in refrigerator manufacturing.
The vacuum cleaner mold adopts 3D model design and CNC processing technology to meet the production of various types of products, such as household, car-mounted, commercial vacuum cleaners, etc.
The vacuum cleaner mold adopts 3D model design and CNC processing technology to meet the production of various types of products, such as household, car-mounted, commercial vacuum cleaners, etc.
The electric fan mold is processed by high-precision CNC and EDM technology. The mold steel selection is flexible, the production efficiency is high, and it can manufacture complex shapes.
Rice cooker mold can be set with multiple parting surfaces to achieve the production of complex shapes and parts. Booling provides mold design and manufacturing for rice cooker shells, liners, lids, control panels, and other parts.
Manufacturing Process of Home Appliance Molds
BOOLING has the most advanced molding technology in the manufacture of home appliance molds. Our engineers provide the best mold molding solutions based on the drawings or requirements provided by users, and strictly control each link of mold design, manufacturing, testing and debugging in the production process according to material and process requirements.
Injection molding is a cutting-edge manufacturing process that involves injecting molten material, typically thermoplastics or thermosetting polymers, into a carefully crafted mold cavity. This cavity, created using advanced CAD/CAM software and precision machining techniques, serves as a blueprint for the final product.
BOOLING 3D printing service mainly provides customized services for industries such as medical models, aerospace, and automotive parts design and manufacturing. The main types of 3D printing technology are FDM, SLA, SLS, DLP, binder spraying, material spraying, DMLS, SLM, electron beam melting, and LOM.
We conduct DMF technical analysis for customers based on product design, and with the professional technical support of our team, propose reasonable solutions before mold making. Booling blow molded products are more prone to shedding burrs, greatly improving production efficiency and facilitating workers to operate during stretching and blow molding processes in the workshop manufacture.
A checking fixture in the automotive industry is a precision tool used to inspect and verify the concentricity, runout, and other dimensional standards of components, ensuring they meet the required specifications through various types of inspection and testing methods.
Booling’s ABS injection molding parts have good rigidity, strength and processability, helping Manufacturers in consumer goods, home appliances, automotive parts, construction, and other industries to achieve high-strength and lightweight production solutions.
BOOLING Stamping Die specializes in the design and manufacture of precision progressive dies for automotive sheet metal punching and bending applications. Our expert team offers comprehensive services from prototype development to final press-ready tooling, ensuring high-quality cutting and forming solutions for even the most complex stamped parts.
FAQs about Home Appliance Molds
Application of home appliance molds in injection molding and blow molding processes
- Injection Mold
In-home appliance mold, the plastic shells of rice cookers, air conditioners, refrigerators, washing machines, dryers, hair dryers, kettles, vacuum cleaners, juicers, coffee machines, etc. are all made by injection molding. - Blow Molding Mold
The product is formed by blowing molten plastic into preforms with air. Common blow molding home appliance products include the plastic shell of water dispensers.
How are BOOLING's home appliance molds produced?
Home appliance mold generally requires high precision. Booling designs, manufactures, tests, and debugs molds in accordance with strict production processes.
1. Mold Design: Design is the beginning of home appliance mold production. According to customer requirements, Booling will use special industrial design software for customized design and convert customer concepts into 3D models.
2. Mold Production: After the design is completed, the manufacturer needs to repeatedly determine the design of the mold’s gate, runner, heating, cooling system, etc., and perform rough processing, semi-finishing or finishing of the mold. Booling’s CNC and EDM machine tool equipment accuracy is ±0.001-0.005mm, which can meet users’ high-precision quality requirements for products.
3. Surface Treatment of Molds
(1) Mirror Polishing: For home appliance injection molds made of materials such as P20 and 718, they have a certain hardness when they leave the factory and can be directly mirror-polished.
(2) Electroplating: Molds made of materials such as NAK80, S136, and S136H need to be electroplated to improve the overall quality, such as nickel plating, chrome plating, zinc plating, gold plating, silver plating, etc.
(3) Sandblasting: The hardness of NAK80 material can reach HRC37-43. Sandblasting of home appliance injection mold made of this material can effectively improve its corrosion resistance.
(4) Leather Grain: Mainly used in some injection molds processed with NAK80 and 738 materials.
4. Mold Trial and Quality Control: After the mold is made, it is necessary to trial-produce the product. According to the acceptance criteria, check whether the home appliance mold can meet the processing requirements and check whether the product has quality problems.
5. Debugging: According to the results of the previous mold trial, adjust the deficiencies of the parameters of each part of the home appliance mold to ensure the best solution.
6. After-sales Service and Solutions: Provide customers with corresponding accessories to maintain the continuity of subsequent production.
Outstanding Advantages of Home Appliance Mold
Booling’s home appliance mold has the outstanding advantages of high precision and high efficiency and can be quickly produced to meet market demand.
1. Booling can provide customized injection molding services for various home appliance plastic parts to meet the specific needs of users and provide customized home appliance injection mold solutions.
2. Use a variety of drawing formats, such as 2D (PDF/CAD), 3D (STL/STP/OBJ/IGES, etc.).
3. Home appliance injection molds support a variety of processing materials, such as ABS, PVC, PP, PE, and nylon, with a very wide molding range.
4. Booling’s home appliance mold hot runner uses processing materials imported from the United States, such as DuPont, USA, OMEGA, USA, and other brands, which are internationally recognized.
5. Home appliance injection molds have a long service life and can be processed in a long continuous cycle.
6. During the design process of home appliance injection molding mold, it is possible to achieve rapid conversion from 2D to 3D drawing formats, with a short time to market and efficient production.
7. Booling provides global injection molding export customization services and provides English and other language support.
Which countries are BOOLING's home appliance molds currently used in?
Booling’s home appliance mold has been exported to Canada, Australia, France, Germany, Ireland, South Korea, Italy, Japan and other countries due to our strict quality control.