Home > Refrigerator Mold: Injection Molding Solution
Details
Details:
Model
Material
Brand
Origin
Application
Booling-Home Appliance Mold-1
P20, 718, S136, 2738 etc
Booling
China
Home Appliance parts
Injection molding of refrigerator molds is an important process for manufacturing refrigerator components. Molten plastic is injected into a predesigned mold cavity, cooled, and solidified to form refrigerator components with specific shapes and sizes.
Advantages of Refrigerator Mold Forming
- Integrated molding
- High precision
- High efficiency
- Product consistency
- Realize the formation of complex structures
Related Hot Products
The injection molding of the refrigerator mold can form multiple components at once, with a short production cycle, and is suitable for large-scale mass production. It has high dimensional accuracy and surface quality, improving the overall performance and service life of refrigerators. During the injection molding process, the mold may encounter various operational difficulties, and manufacturers need professional solutions to solve the problems quickly.
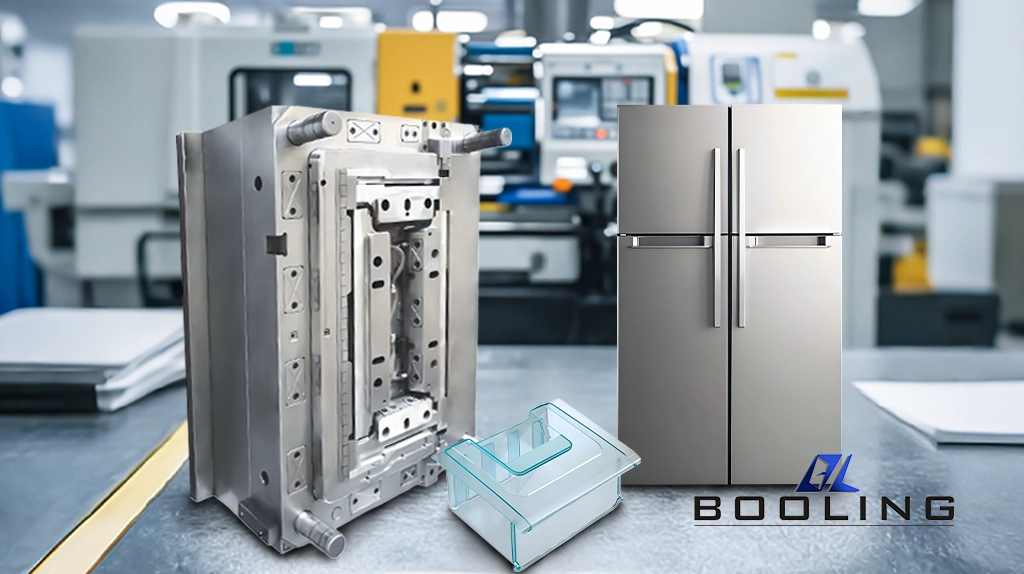
Injection Molding Process for Refrigerator Mold
The principle of injection molding mainly includes five stages: plasticization, injection, pressure holding, cooling and curing, and demolding.
-Plasticization: Granular or powdery plastic raw materials enter the material barrel of the injection molding machine from the hopper, are heated to a molten state, and the screw inside the barrel stirs the plastic to achieve a more uniform state.
-Injection: After the plastic is plasticized to the appropriate state, the screw of the injection molding machine pushes it forward and injects it into the mold cavity through the nozzle, filling every corner of the cavity. At this point, it is necessary to control the filling speed and pressure to ensure the quality of the formed product.
-Pressure holding: After the molten plastic fills the mold cavity, the injection molding machine needs to maintain a certain pressure and continue to replenish a certain amount of plastic raw materials to prevent defects caused by shrinkage rate.
-Cooling solidification: Usually, the heat in the mold and product is removed by circulating cooling water or other cooling media, and the final shape of the product is fixed.
-Demolding: After sufficient cooling and solidification, the product has a certain degree of hardness and strength, and can be smoothly ejected through the ejection device to complete demolding and obtain the final product.
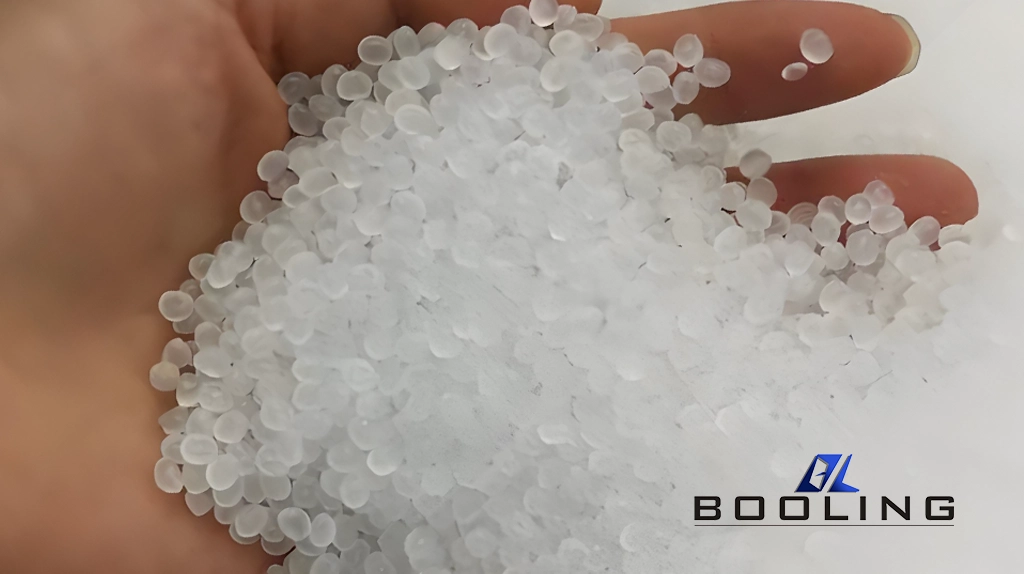
The solution to The Problem of Refrigerator Mold Cutting
During the injection molding process, the mold often has defects such as poor feeding, and the plastic raw materials in the barrel may not be fed, which affects the quality of the final product.
-Reason: Used recycled material, not fully crushed, uneven particle size; Insufficient drying, clumping, or bridging of raw materials; The drying temperature is too high and the time is too long; The vibration of the injection molding stage is significant during the injection molding process.
-Solution: Grind the larger recycled materials again or replace them with new materials for processing; Clearing the raw materials in the drying bucket; Reduce the temperature of the feeding section and barrel; Shorten drying time or lower drying temperature; Increase the diameter of the feeding port.
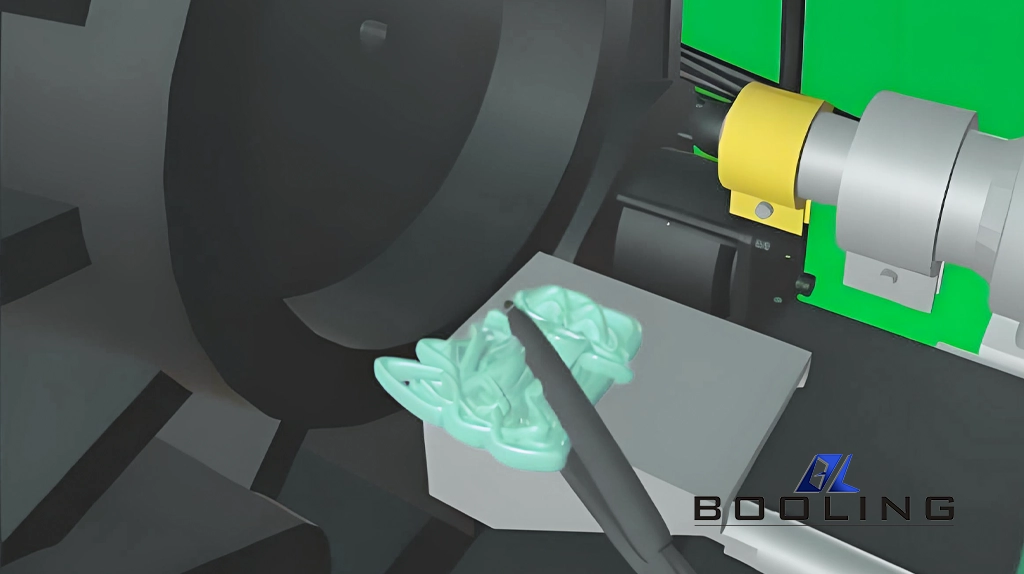
The Solution to the Problem of Refrigerator Mold Nozzle
During the injection molding process, the nozzle is prone to clogging defects, which prevent the melt from entering the mold flow channel. This defect can greatly slow down the progress of refrigerator mold molding.
-Reason: Metal or other nonmelting substances or materials mixed in the nozzle; No magnetic rack is placed in the drying bucket, and no magnetic tube is installed in the nozzle; For some crystalline resins, lower melting temperatures are set; The heating ring at the nozzle head is burnt out.
-Solution: Disassemble the nozzle and remove any foreign objects inside; Replace or re-screen the raw materials; Replace the nozzle head heating ring; Raise nozzle temperature
Automotive Mold Related Content
Applied’s expertise in modifying materials at atomic levels and on an ihdustrial scaleenables our customers to transform possibilities into reality.