Home > What is a chair mold?
Details
Details:
Model
Material
Brand
Origin
Application
Booling- Househlod Mold Mold-1
P20, 718, S136, 2738 etc
Booling
China
Household Mold parts
Chair molds are tools for manufacturing various chairs. They are made of mold steel with a certain hardness and wear resistance. They can produce chairs for different usage scenarios: restaurant chairs, kindergarten chairs, park chairs, gymnasium chairs, bus chairs, etc. The chairs produced by Booling are sturdy and durable, enabling manufacturers to achieve fast delivery of products.
Advantages of Chair Molds:
- High precision
- High processing efficiency
- Product consistency
- Strict quality control
Related Hot Products
Chair molds are mainly composed of cores and cavities, which can flexibly process various types of chairs. Manufacturers need to determine the size, shape, and details of the chair according to its intended use. Using CAD and other design software, mold drawings can be easily drawn, with various shapes and high processing feasibility.
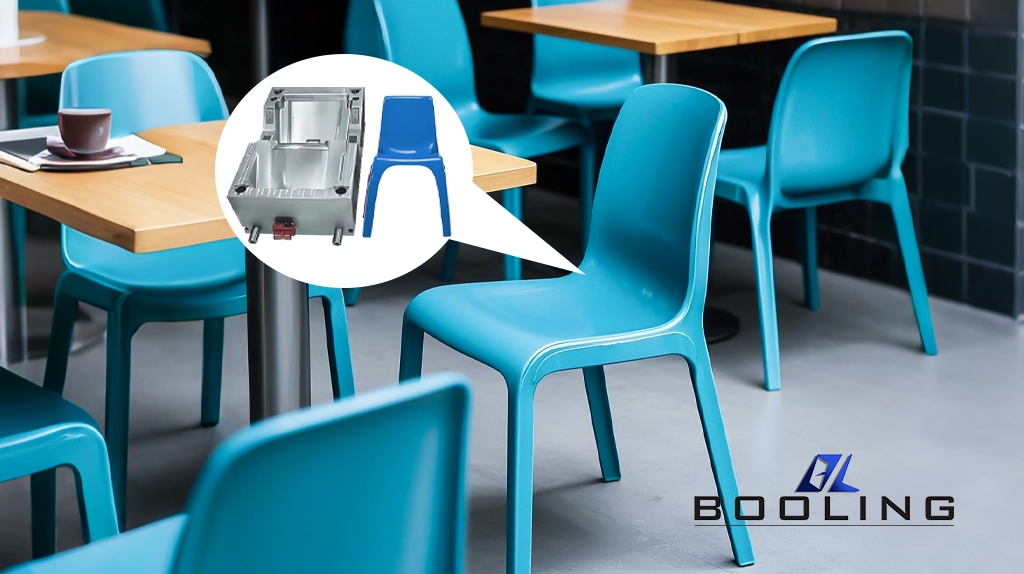
Uses of the Chair Mold
With the help of the chair mold of different designs, different models of products can be manufactured, which are widely used.
- Restaurant: The chairs used in the restaurant are of various shapes, matching the overall style of the restaurant and the dining table, considering the comfort and beauty of the seat surface. Some outdoor food stalls may use plastic chairs or stools with armrests. The design is relatively simple, but they need to be weather-resistant and stable and can be stacked when stored for easy transportation.
- Office: Plastic chairs pay more attention to practicality and comfort. They can adjust the height and have armrests. Sometimes they need to be matched with leather and fiber materials to improve the overall beauty and practicality.
- Outdoor: It needs to be waterproof, sun-proof, heat-resistant and corrosion-resistant. It is often used in places such as beaches, swimming pools, and terraces.
- Classroom: It is mostly used for children’s plastic chairs. It is small in size, cute in shape, and has a variety of color options. Cartoons and various patterns can be designed according to customer needs.
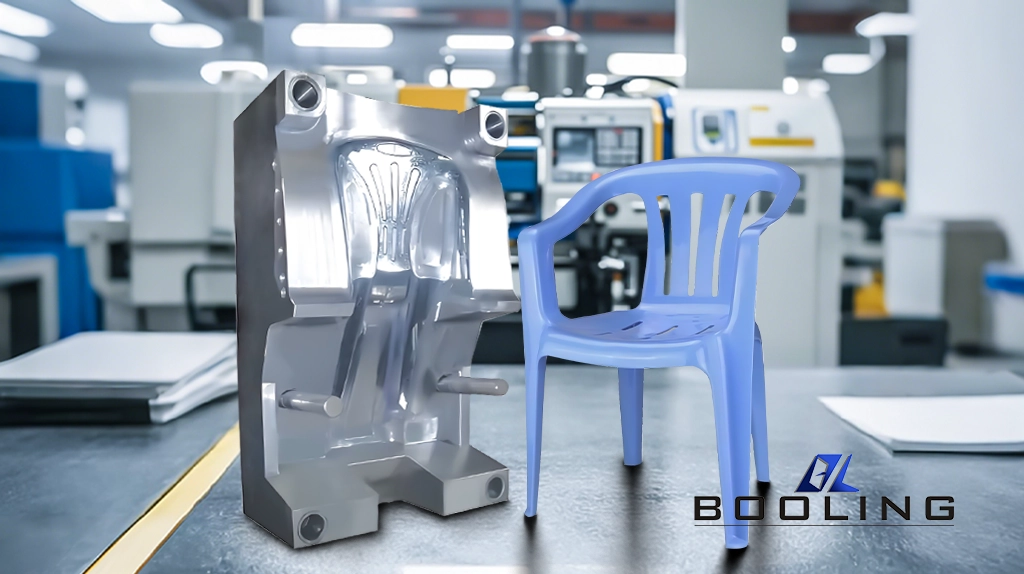
Chair Mold Design Process
Design according to the intended use, function, and appearance requirements of the chair, understand the production requirements and production cycle of related products, and determine the basic process of the mold.
If there is a mold model, import its 3D model into professional design software, and check the integrity and accuracy of the mold to avoid surface breakage problems. Analyze the shape, size, wall thickness, demoulding method, etc. of the product according to the model to clarify special design requirements.
Determine the number and layout of cavities, parting surface, and demoulding mechanism, consider the appearance requirements of the product, and select a suitable gate. For plastic chairs with high surface quality requirements, side gates and latent gates are generally used.
Use mold analysis software for simulation analysis to predict product molding and ensure the processing feasibility of the design scheme.
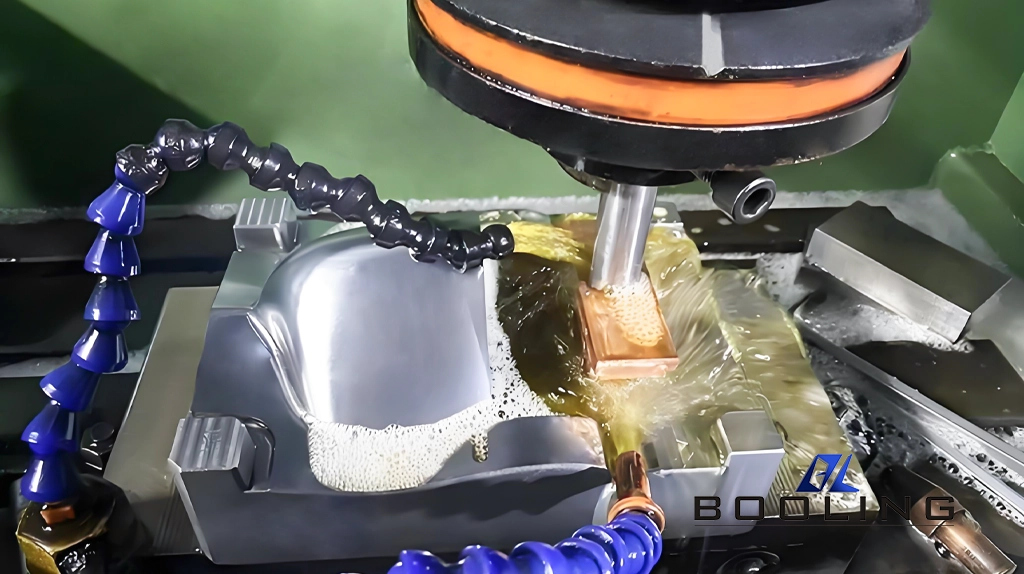
Manufacturing Process Of Chair Mold
According to the specific shape, size, structure, and functional requirements of the chair, it is processed and manufactured in combination with 3D modeling drawings.
Select suitable mold steel, such as P20, S136, 718, etc., to ensure that the mold will not be damaged by excessive friction when opening and closing the mold under high temperature and high pressure. After determining the mold steel, cut and blank the material, consider the processing allowance, and cut the steel into approximate size and shape.
Use CNC machine tools, EDM machines, drilling and tapping machines, and other equipment for fine processing, control the accuracy within ±0.01mm, improve the surface finish and hardness of the mold, and prepare for subsequent assembly.
Quench the mold to improve the hardness and strength of the mold. The quenching temperature and insulation time need to be determined according to the type of steel. Tempering treatment is carried out to eliminate the stress after quenching, stabilize the internal structure and size of the mold, and improve the toughness of the mold.
Automotive Mold Related Content
Applied’s expertise in modifying materials at atomic levels and on an ihdustrial scaleenables our customers to transform possibilities into reality.