Home > Automotive Injection Molding Companies
Custom Injection Molding
Custom injection molding has gradually become the mainstream production method in the plastic molding industry through its efficient production method, high-precision molded parts, and flexible technology and design, playing an important role.
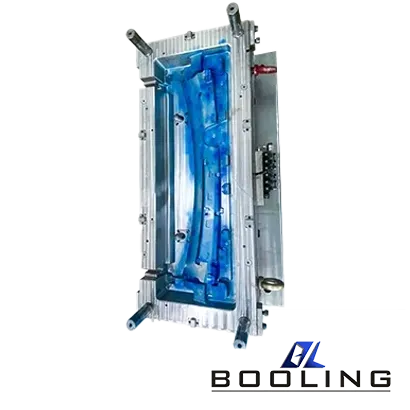
Automotive Injection Molding Companies
Some companies providing automotive injection molding services have an experienced design and operation team, as well as advanced custom injection molding production technology. At the same time, it can achieve a perfect combination of guaranteed product quality and comfortable customer service, producing high-precision products that meet customer satisfaction and excellent quality.
When the companies conducts automotive injection molding, the molten material (usually thermoplastic or thermosetting polymer) is first injected into a carefully crafted mold cavity. This cavity uses advanced CAD/CAM software and precision machining technology, which can serve as the blueprint for the final product. Thermoplastic injection molding ensures precision, repeatability, and versatility to create complex designs with complex details and strict tolerances.
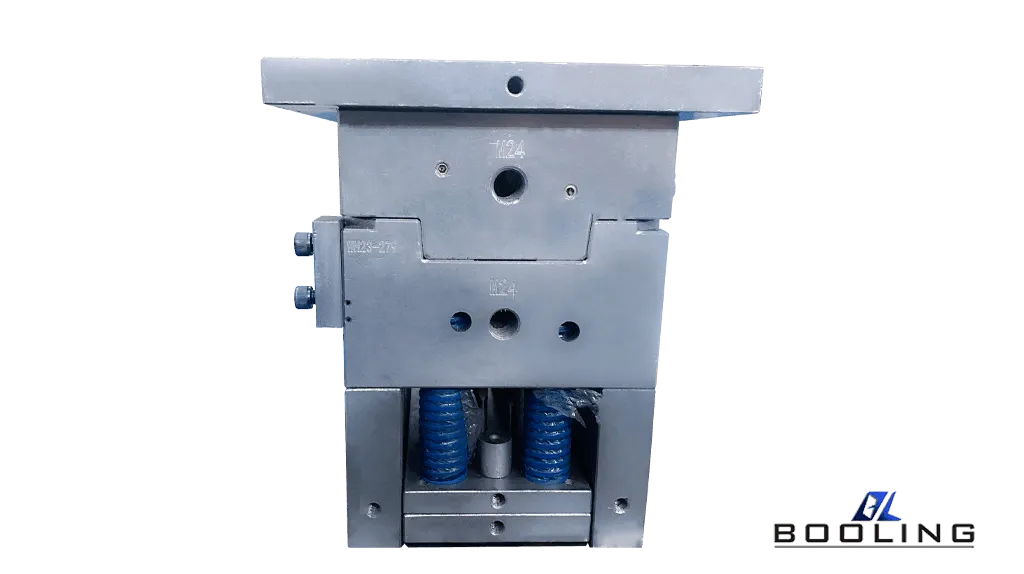
The Application of Injection Molding in the Automotive Industry
Injection molding is the most commonly used plastic molding method in automotive injection molding companies, used to process various types of automotive components. With the rapid development of the automotive industry, the demand for automotive components is also increasing. Injection molding, with its high precision and high safety characteristics, can efficiently and high-quality meet the processing needs of automotive components. Injection molding technology has become an indispensable key part of automotive manufacturing, and the following are the applications of injection molding technology in the automotive field:
Automotive Interior: Injection molding technology can effectively achieve the design of complex components such as the dashboard, center console, door panels, steering wheel, seat cushion, and interior trunk cover, meeting the aesthetic needs of both users and customers.
Exterior: Injection molding technology is well applied to the body shell, bumper, rearview mirror shell, door handles, and plastic frames outside the windows of automobiles, providing good durability, safety, and lightweight advantages.
Automotive brake components: The engine and brake components of an automobile are usually wrapped in a layer of plastic casing, which is usually manufactured through injection molding technology, such as the casing wrapped in automotive air conditioning and air purification systems.
Pipes and Connecting Parts: Automotive air conditioning pipes, refueling pipes, coolant pipes, etc. are usually manufactured using injection molding technology, providing good sealing and durability.
Automotive Lighting Fixtures: The transparent parts of the front and rear lighting fixtures of an automobile are usually manufactured using injection molding technology, but the selection of materials needs to meet lighting requirements and optical effects.
Brackets: Various plastic brackets and fasteners in automotive components benefit from injection molding technology.
Automotive Interior Vuttons: The various switches and knobs in the automotive interior need to be aesthetically pleasing and ergonomically pleasing, and the injection molding process meets these two requirements very well.
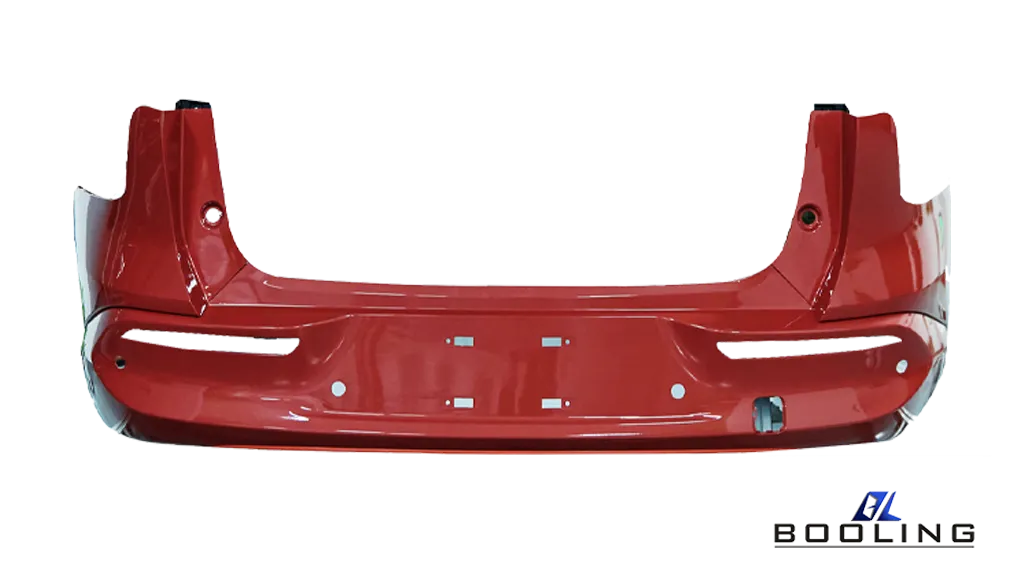
The Process of Automotive Injection Molding
Before conducting injection molding, automotive injection molding companies need to prepare and select the appropriate process before starting the injection molding process. Finally, they also need to carry out subsequent processing on the parts. The following is an introduction to the main process of automotive injection molding in the companies.
Preparation before Injection Molding
Before the formal start of the injection molding process, automotive injection molding companies need to first analyze and design injection molds that are consistent with the molded parts based on the size, structure, and materials of the automotive parts, with a focus on the parting surface, cavity, cooling, and drainage systems of the molds to ensure product quality during the injection molding process.
Secondly, material selection should be carried out based on the needs and application scenarios of automotive components, to achieve the best performance of the components; Check the color, particle size, water absorption, water absorption, and moisture content of the raw materials. For plastics with strong water absorption, drying treatment must be carried out before use, otherwise it will affect the quality of plastic molded parts. After drying, the raw materials must be put into use as soon as possible to avoid the possibility of moisture regain and increased drying costs.
Due to the difference in properties between metals and plastics, it is often necessary to preheat metal inserts before use to avoid defects such as cracks in plastic molded parts caused by different shrinkage rates.
Finally, it is crucial to clean the material barrel during the preparation stage, especially if the color or variety of the materials used earlier is different from this one, which can easily cause material mixing and lead to appearance problems of the final formed part for rework.
Injection Molding
The action program of plastic injection molding for different products may have certain differences, but the process content is consistent, mostly including mold closing, injection molding, pressure holding, cooling and curing, mold opening, removal, and trimming.
In the injection molding process of automotive parts, the parameter control of the injection molding process plays a decisive role in the quality of the finished product. The injection molding process needs to master the following aspects: first, control the temperature, pressure, speed, and other parameters of injection molding to ensure the stability and consistency of finished product quality. Secondly, it is necessary to master the opening and closing speed and processing flow of the mold, as well as the operating standards of the plastic injection molding machine, to ensure that the injection molding process can proceed normally. Finally, it is necessary to monitor the injection molding process to make timely adjustments, such as adjusting injection molding parameters based on changes in finished product quality.
Post Molding Treatment
After injection molding, automotive components need to be inspected to ensure that their quality meets the requirements, there are no defective waste materials, and there is no oil on the surface. Further trimming the edges of the product to improve its appearance and safety, as well as completing some product labeling steps at this time. If the final product requires packaging, it should also be packaged to prevent the influence of impurities and dirt, to meet the needs of customers and automotive injection molding companies. Finally, it is necessary to treat the generated waste. The waste from injection molding is generally crushed and can be reused, greatly improving cost-effectiveness and reducing the impact of environmental pollution.
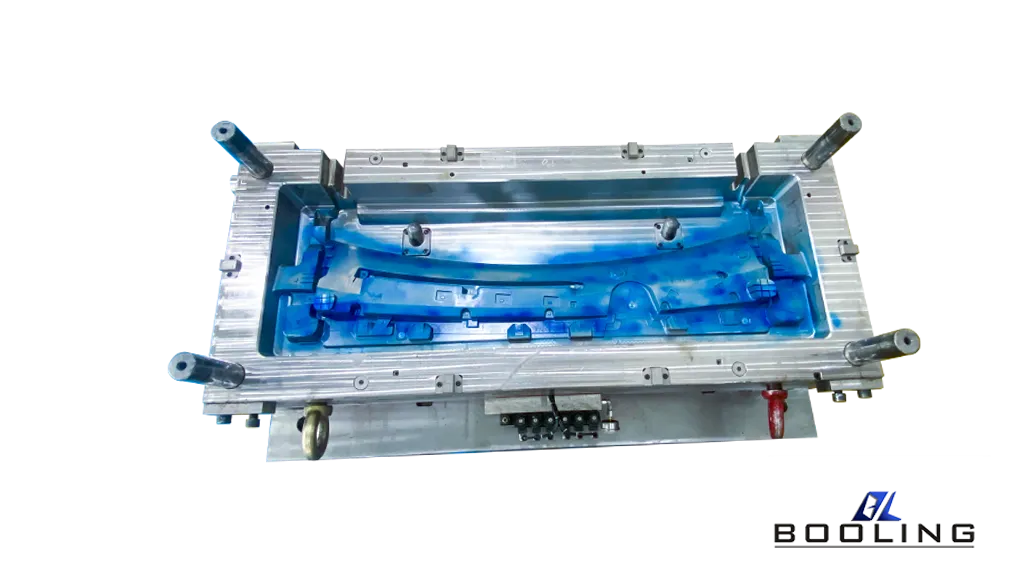
Mold Structure of Automotive Injection Molding Companies
- Mold Cavity: The mold cavity is the part of the mold where plastic parts are formed, which is an empty cavity. The shape of the mold cavity is completely consistent with the shape of the workpiece, and the mold cavity is generally composed of two parts: the mold cavity and the core.
- Forming Parts: The parts that make up the cavity of a plastic mold are collectively referred to as forming parts, usually composed of two parts: the core (internal shape of the formed plastic part) and the cavity (external shape of the formed part).
- Pouring System: The pouring system is a flow, channel that guides plastic from the injection molding machine nozzle to the mold cavity. The pouring system is divided into four parts: the main flow channel, the diversion channel, the gate, and the cold material hole. It is composed of a gate sleeve, a pulling rod, and a flow channel on the fixed template.
- Guiding Mechanism: It is a guiding component set up to ensure accurate alignment of the center position when the moving and fixed molds are combined, usually with guiding columns, guiding holes, or matching inner and outer conical surfaces set on the moving and fixed molds.
- Cooling and Heating Device: To better control the temperature of the mold, a cooling or heating system has been set up. The cooling system usually opens a cooling water channel inside the mold, while the heating system installs heating elements inside or around the mold.
- Exhaust System: In the injection molding process, to exhaust the gas inside the mold, an exhaust system needs to be set up. Generally, exhaust is carried out through fractal surface gaps, core gaps, cavity gaps, or exhaust grooves.
- Supporting Parts: Used to install and fix or support the forming parts and the aforementioned parts of the mechanism. Assembling supporting components can form the basic framework of injection molds.
- Side Parting and Core Pulling Mechanism: The entire mechanism that drives the movable core to move laterally (pull and reset) is called the side parting and core pulling mechanism.
- Ejection Mechanism: A device that ejects plastic parts from the mold during the mold opening process. Some injection molds have ejection devices that have guide parts to prevent the ejection plate from tilting during the ejection process, which maintains horizontal movement of the ejection plate. It is generally composed of the top rod, top plate, top plate guide pillar, top rod fixing plate, main flow material pulling rod, reset rod, support nail, and top plate guide sleeve.
Related News
Applied’s expertise in modifying materials at atomic levels and on an ihdustrial scaleenables our customers to transform possibilities into reality.